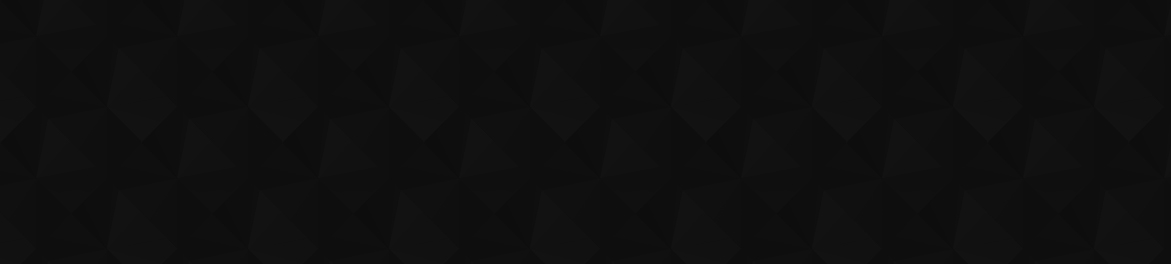
- 179
- 331 100
Maker | Geek
United Kingdom
Registrace 29. 08. 2015
I'm Dan and I love tools and learning how to use them. I also love to customise the world around me, so many of my projects are about making something exactly the way I want it, from turning my own pen, to installing my own kitchen, it's fun to personalise and shape the world you live in.
I'm not a professional woodworker/welder/turner or anything else you may see me do in my videos. I attempt to work these projects around an otherwise full time job in I.T.
if you're interested in the tools/components from my projects you can support me buy using my affiliate links here: www.makergeek.co.uk/linktree
if you really like what I'm doing, I also have a patreon: www.patreon.com/makergeek
I'm not a professional woodworker/welder/turner or anything else you may see me do in my videos. I attempt to work these projects around an otherwise full time job in I.T.
if you're interested in the tools/components from my projects you can support me buy using my affiliate links here: www.makergeek.co.uk/linktree
if you really like what I'm doing, I also have a patreon: www.patreon.com/makergeek
voice over version: GIANT! lazy susans for quick set changes
For those that prefer no music and just explanation about the project. this is the voice over version
for music chill vibs: czcams.com/video/NrxjHVxhs3g/video.html
for music chill vibs: czcams.com/video/NrxjHVxhs3g/video.html
zhlédnutí: 147
Video
GIANT! lazy susans for a quick set changes
zhlédnutí 198Před 14 dny
I was recently asked if I could come up with a reasonably inexpensive way to mount a door frame prop such that it could easily be rotated through 180 degrees for a set change. This is what I came up with. This video is music only, If you prefer no music and more description of what the thought process is then watch this one instead: czcams.com/video/ZHowIQz_34I/video.html
robot arm update. figuring out through bearing axle for better motor positioning.
zhlédnutí 129Před měsícem
robot arm update. figuring out through bearing axle for better motor positioning.
STL hacking: using fusion360 components to calculate a perfect fit.
zhlédnutí 265Před 2 měsíci
Sometimes most of the work is done,... but it's not quite right. Here I present some approaches to tweaking an existing STL in fusion 360 to make it suit your exact requirements
3d print: Convert STL with embossed text to multicolour with blender
zhlédnutí 568Před 2 měsíci
Have model with embossed text, but you want to make it multi-colour for your fancy multi-material 3d printer? I didn't find any obvious instructions on how to achieve this so figured I'd upload a quick instructional now I figured it out.
Robot cameraman mk.ii - pan and tilt
zhlédnutí 153Před 4 měsíci
A little while ago I broke my robot cameraman. I took it as a sign to start a long considered upgrade project.
Electronic Leadscrew v2 - for mini lathes
zhlédnutí 1,7KPřed 6 měsíci
Demonstration of all features of my updated electronic leadscrew project, suitable for essentially any lathe that could do with modernising. Supports Metric and imperial threading, various surfacing rates, pattern creation, psuedo-knurling. digital stop and resume.
State of the workshop - 2024
zhlédnutí 263Před 7 měsíci
It's that time again for me to ramble on about what stuff I got up to in the previous year and reflect on how my workshop is setup, what plans I have for tools and projects etc.
3d printed end cap and switch for a 24v psu
zhlédnutí 68Před 7 měsíci
3d printed end cap and switch for a 24v psu
Kaiweets KOT936 Soldering Station - first impressions
zhlédnutí 117Před rokem
Kaiweets KOT936 Soldering Station - first impressions
Arduino based Electronic leadscrew - First threads
zhlédnutí 2,5KPřed rokem
Arduino based Electronic leadscrew - First threads
Fixing CHEAPEST amazon TIG pedal to work with ROHR WSME-200
zhlédnutí 3,3KPřed rokem
Fixing CHEAPEST amazon TIG pedal to work with ROHR WSME-200
Robot Cameraman Controlled by Garmin Venu 2+: The Future of Filmmaking!
zhlédnutí 103Před rokem
Robot Cameraman Controlled by Garmin Venu 2 : The Future of Filmmaking!
Eco-Friendly Garden Storage: Building a Cupboard from Recycled Pallet Wood
zhlédnutí 262Před 2 lety
Eco-Friendly Garden Storage: Building a Cupboard from Recycled Pallet Wood
Patio Furniture DIY: Building a Coffee Table with Steel and Tile
zhlédnutí 223Před 2 lety
Patio Furniture DIY: Building a Coffee Table with Steel and Tile
DIY CNC Machine Takes on 18mm Plywood: Can It Handle the Challenge?
zhlédnutí 576Před 2 lety
DIY CNC Machine Takes on 18mm Plywood: Can It Handle the Challenge?
CNC Rebuild : Y-axis ball screw mounts
zhlédnutí 1,9KPřed 2 lety
CNC Rebuild : Y-axis ball screw mounts
MX-5 Mod Series: How to Add a Remote Boot Release to Your Car
zhlédnutí 1,6KPřed 2 lety
MX-5 Mod Series: How to Add a Remote Boot Release to Your Car
What they don't tell you about replacing an mx-5 hood
zhlédnutí 217Před 2 lety
What they don't tell you about replacing an mx-5 hood
OX CNC refactor: x-axis carriage brackets
zhlédnutí 159Před 2 lety
OX CNC refactor: x-axis carriage brackets
3d Printing challenge - printing thin curved parts
zhlédnutí 502Před 2 lety
3d Printing challenge - printing thin curved parts
OX CNC refactor - part1: Y-axis gantry plates
zhlédnutí 420Před 2 lety
OX CNC refactor - part1: Y-axis gantry plates
I've just come from your V2 video - where I wondered why you did this project. For the fun of it seems like a good answer.
Pretty much for the fun, I was interested in the challenge and learning what was needed. I did also want to see if I could make a fairly cheap option, I thought the arduino could handle the processing load (and it can) but the memory is too limited. my latest version is now an esp32 which I'm messing with.
@@MakerGeek Excellent. Have you looked at the Raspberry Pi Pico (Pico 2 has just been released!). That has multiple state machines (running at over 100 MHz) and a lot more memory.
@@ChidleyEngineering I've not had a chance to check out the pi Pico. I've used the nano and fill sized in various places. These days the esp32 has been my go to for more power and electronics integrations. Though it's a bit of a pain with it's 3.3v logic, is the pico 5v?
@@MakerGeek 3.3V. It's all going 3.3V these days.
@@ChidleyEngineering yeah, and if makes sense. But all my stepper controllers need 5v signals so it means adding stuff to the circuit where with the trusty Arduino you could just pulse it direct.
What was the motivation for doing your version of an Electronic Lead Screw - what was missing from the other projects out there?
Fantastic idea Dan!! Well done xx
Hey! I'm a fan of voiceover videos more than music videos. But, I'm also one of those headphones listeners so clipping audio on the voiceover is a deal breaker. I've found that most video editors have a compression filter that will help but also checking audio levels before recording goes a long way. Cheers!
Thanks for the feedback. I should probably investigate the right settings in resolv. Audio levels/mix has always been a pain for me, I've had stuff that sounds totally fine/perfect for me that is unlistenable on other setups etc. I really wish youtube gave more/better tools to modify/fix audio after the fact ;-/
Thanks very much, really useful. As Tifi7160 says, on some (including mine) the green/black wire also continues through the plug.
What controll system you using? Here, via your comment on Toms vid. Check out my rig on the channel. -Ken
the underpinnings are GRBL, with a pretty custom python application on top to give me the various control inputs I wanted. Now that I'm rebuilding I'm considering moving away from GRBL and just doing something direct with accel stepper on an esp32.
@MakerGeek interesting.
Very informative, thanx!
2mm cut (80 thou). Hmm sounds aggressive. I tried too much and clogged up the cutter as al is soft and rewards patience. Now I use 10 to 20 thou passes to avoid ruining cutters. I also fix a shop vac near the cutter that cools it and removes most of the swarf making everything more visible.
Keep the red bits on as they stop the read heads from bouncing around and on the glass scale. Far too late now of course but they need to be pulled out after the entire scale and slide is bolted in. A bit like the old antistatic shorting wires on early FETS. Solder into place and then pull off the shorting wires. OK nothing like a mill but I suspect you will know what I mean.
Mounted my dro scale to the front of the apron like that (Chester DB7, very similar to your Warco I think) with the aid of a couple of custom 3D prints and bolted to those same follow rest holes. I've now crashed the scale into the chuck (thanks to my electronic lead screw and my stupidity) but have ended up putting the replacement in the exact same spot. Took the opportunity to open the danaged one and discovered lots of chips. Caution is a advised!!
I have just finished getting in a WM16B mill through a house doorway, a 90 turn and then another into a downstairs room and onto its stand on my own. What a slog. This was using a fork lift trolly with a wind up platform. All done, some filling work needed on the walls but not much luckily. I could not have coped with the weight of the WM18. The WM16 was already too wide to go through the 2'6" doorways. I had to angle it through as it slid around on the platform. Scary scary. I would recommend that you convert to belt drive or swap out for a new WM18B with DRO that is currently cheaper than a plain vanilla WM18. Much smoother and quieter.
oh interesting, is it a straight forward conversion? I feel like they had no stock of the B when I got mine. though the noise doesn't bother me overly. congrats on your 16B
On my side i use blender, you just select the face, extract, flat them and bam you got the dimension. Wish fusion could manipulate vertex, edge and face finger in the nose like that.
Amazing, the things you get up to!!!
Nice! I like the trick to get the circle. One thing fusion does quite well is rebuild a face, so you can take any flat surface, select one of the triangular faces, hit delete and it will remove all of the triangular faces on that surface, replacing them with a single face. A little tricky to explain so I recommend playing with deleting faces. It won't replace your technique for getting a perfect circle but it's really useful for cleaning up other flat surfaces on STLs. Once cleaned up it can make it much easier to work with other tools.
I should probably play more with the face manipulation. I feel like I sometimes struggle to get things back to a coherent solid. But you're right, in a lot of cases I'm sure deleting weird faces and having it just repatch is a fast way to fix things up.
Yes, this. ☝🏻 On any flat surface just deleting a single triangle will give you the same results with far less steps to do and saving your timeline.
You can also do the same thing directly in the slicer by Right Clicking on the model and choosing Add Part. Or in Fusion, I might have selected the faces of the text > Extrude > .2mm > New Body > Export. Always good to have options :)
the problem with fusion is that the imported stl will not have clean faces for the lettering, lots of little triangles once converted to a body. possibly there is a fast way to clean that up to get an easy extrude, but so far I've found blender to be faster for that sort of thing.
@@MakerGeek That is very true, and is a real pain in the butt. One trick that works most of the time is after converting a mesh to a solid in Fusion, split the body in half (or split it anywhere really). Flat faces will now be free of all those pesky triangles, and you just join the 2 parts together again. Shame it can't deal with curves too :( Apparently the paid version can do better, but I have no experience with that.
❤Great hack. Mahalo for sharing.
I added an ELS to my warco WM180 czcams.com/video/PH6cTw_ml4M/video.html it was a pain to get the encoder set up but I ended up using a set of gears to transfer to the encoder. I use this baby every day now, rarely do I ever use the manual function.
yeah I saw the nano els build at some point. though only after I was some way into building my own. I guess I was trying to see how cheaply I could make the setup plus of course half the fun is doing it yourself ;-) glutton for punishment I guess. I can see the temptation to put a bunch of buttons on it, but I'm playing with how little I can get away with and make a functional setup. I can certainly agree that once you've used an ELS, it's hard to go back
@@MakerGeek Im personally not a fan of all the buttons. The chap that makes the controller also makes software called Lathecode which is super nice. It lets you describe the shape using parameters and from this it generates gcode which you can send to the controller. Ive made some really complex parts with it, and ive got a fork of the software where I have implemented support for tool changing by manually swapping a tool in the QCTP then selecting that tool on the controller and having it automatically apply the offsets. Its funny because initially I only wanted an ELS because i couldnt be arsed with changing gears but actually it shows how capable you can make these little machines with some electronics and some coding.
for sure, once you start to put a computer brain on it all sorts of interesting options open up. hard to know where 'improving a cheap manual lathe' turns into just a full CNC conversion ;-) very tempted to move onto sticking a motor on the cross slide also, did you upgrade the screws? or just doing backlash compensation?
Check out the Nano ELS H4. ive got one on my WM180 and it works really well. You can use it on the Z and X axis. In fact I can now run CNC jobs on it.
Great video. Mahalo for sharing! : )
Hi Dan, You're a star mate! Had exactly the same problem as you but no multi-meter. Did what you did and hey presto it now works. Now all I have to do is buy a jig to cut that kitchen worktop. Thank you! You've saved me a lot of money. Alistair
That's great to hear, always nice when you can fix a tool and keep on going. good luck with the kitchen
There never a failure it's a step to learning more for a better outcome.
Hi, very nice work and more information for when I try and create my own ELS sometime in the future. One thing to note is that your compound is at the wrong angle for threading, it should be 30 degrees off from perpendicular to the spindle axis whereas you have it 30 degrees off from parallel to the lathe axis. And I suspect you know for internal threads you should swing the compound to the opposite 30 degrees to ensure you are cutting on the correct flank of the threads.
This is some excellent work - I like the extra functionality of your ELS over most of them - being able to thread (or surface) for a known length, the limit switches, the patterns, etc etc. Those are very smart additions, and ones that I've wondered why other ELS projects don't have. You should put another servo on the cross slide, and you'd have a full CNC now :) Industrial servos have 2 tracks on their encoders, the regular X pulses / rev, as well as an "index" pulse that's once per revolution. That way you can get absolute orientation of the spindle as well, and you wouldn't have to calibrate your pulses/rev even if your 3d printed pulleys aren't 100% accurate. But given the repeatability of when you cut the patterns at the end, clearly your calibration is excellent even the way it is now!
Also, not a bot
Also, your "unidirectional patterns" are actually multi-start threads!
Thanks, they are all features that felt like things I would use. I have to say I've considered the cross slide also, but handling backlash in the leadscrews gets quite complicated, I suspect if I was going that far i'd want to replace them with ballscrews etc. Something I've played with recently that I might look at is magnetic orientation sensors that give absolute orientation in about 4000 increments. One thing though that I think I have to admit is that I reached the limit on the nano. it is certainly capable of doing the job, but the memory is not big enough to have the configuration/customisations I want without running into very inconsistent operation. When I next get time I'm going to switch out for an esp32, which is much more memory/cpu headroom. then rebuild around that. They're basically the same price, but I'm hoping much more reliable.
@@MakerGeek There's a really cool (and open source) one I saw recently on Rotary SMP's channel - video title 'Roll you own DRO / ELS'. He's using a little custom board with an STM32 for the real time stuff, and a raspberry pi and the 7" touchscreen with a GUI written in Kivi (running on the bare metal - no linux underneath, or at least not a full x/wayland display manager underneath) for the UI. He can take in 3 axes of sensors (scales or rotary encoders), and he took it even a step further, where you can drive one axis based on the position of another (all configurable / changeable in real time), so that you can cut helical gears without needing physical gears between an axis and a rotary table on the mill. I'm really torn as to build that one, and implement some of the features you have in yours, and add in 2 axis control (one based on the spindle for ELS, and the other configurable as it is now for all kinds of other crazy stuff like an electronic taper attachment) or just go full out and go to LinuxCNC. I've wanted to do a LinuxCNC project for a long time... decisions decisions...
Music levels compared to your voice are totally obnoxiously loud. Consider using sound level balancer or do it manually.
Something I've learned through CZcams is that different systems/setups can render audio quite differently. So what should fine on my system is rubbish for other people. One day I'll get it figured out
I have been coding industrial firmware for about 25 years, including a lot of pulse reading, pulse generating encoder type stuff. I think your issue with getting incorrect number of pulses at low spindle RPM would be completely fixed by using quadrature encoding, ie 2 inputs from the encoder and not just 1. Simple quadrature decoding should still be very quick in firmware, and you dont even need full quad you can do a half quad decoding where if input A goes hi or low you just add or subtract a count (when input B is lo), and you subtract or add a count on the A edge (opposite) when input B is hi. With a full quad or half quad system you will always get a perfect count of 800 per rev (or whatever). Great video! Thanks for sharing. 🙂👍
Thank you. I actually started using the second pulse to give me direction detection, but it's a good point that I could use that to improve pulse counting generally. however i believe I have finally run up against the limits of the arduino nano which seems to start becoming quite erratic as you consume more of it's limited memory with program code. when i get time I'm going to experiment with identical code setup but switch out for an esp32 to see how it compares.
@@MakerGeek thanks for the reply! ESP32 has quite a bit of difference in processing power compared to the nano 😎
Maybe control chuck acceleration to avoid missing counts on chuck position.
you mean hook into the pot that controls rpm speed and control that electronically for smoother accel? certainly something I've thought about. though most of the time I can somewhat achieve that manually. it doesn't really matter if I miss pulses before I begin an operation though. and once I start I tend to leave the chuck running at a constant rate throughout.
Very nice. I am not a robot and I'm looking forward to your finished product. I hope you offer it for sale.
Cheers. Slight delay on the els front as I hit some unreliability in testing and I don't want to offer something I'm not 100% on. But I've a few ideas to work though it
Really useful, thanks (and the previous video). I'll be trying to replicate this in the next few days.
Just for reference, it worked a treat. It's ridiculously satisfying to be able to 'plip' the boot open! 😁
Great, I'm glad the video helped. I agree, it's a very satisfying upgrade to the car ;-) plus the weather is starting to give us proper top-down days to enjoy.
Super interesting. What a huge project. Mahalo for sharing!
Awesome!! Thank you for sharing an update
Looking forward to it
Just posted a video update to catch up with where I'm at.
What camera do you use? Will you ever rebuild into a new version, I'd be interested to see an updated make video on it if possible
The dslr is a canon80D that I've had for years now. I did consider whetherlife would be easier if I started with a newer/lighter camera. but for now I'm sticking with what I have. I'll see how it goes on the video front, I might film some bits and pieces of it in the next few weeks
Fun fact. ER collets have a 1mm clamping range. A set of metric ER32 collets will do everything you need. Even imperial.
interesting. obviously, I knew there was some range to the clamping size, but I hadn't really though about the fact that you'd essentially have continuous coverage. that's a great point
Nice cribbage board. If you come to Hawaii here, then I can see your cribbage board in person and we can play on Waikiki Beach.
I'd love to come to Hawaii one day. cribbage on the beach sounds exactly my speed ;-) I will however have to make another one of these, since this one was a gift.
Stepper motors expect a smooth acceleration profile. I have a supply of Oriental Motors steppers with 1000 steps per revolation and a mini lathe with a lowest speed of 240 RPM. The issue is that sending a burst of stepper pulses for every encoder pulse asks the stepper to accelerate faster than it is capable of doing. I have been trying to code an algorirhm that encludes acceleration/deceleration at an evenly spaced pulse output. I am using an ESP-32 which should be totally capable of making the nessary calculations per interrupt, but, including an acceleration and deceleration profile I have yet to be successful.
I have not found this to be an issue. my stepper seems to handle quite happily going from a standing start to getting pulses for most thread pitches. obviously in some conditions you get an acceleration profile for free because the spindle also has to accelerate up to speed. It almost certainly helps that I'm using a servo type stepper which works to catch up with the positions you''ve requested so even if it's an aggressive start it catches up anyway.
That's why a "motion controller" is more complicated than you think. You might need to send motor pulses at non-integer ratios of encoder pulses, and you certainly can't send a "burst" of motor pulses at each encoder pulse. You need to use timers to space out your pulses equally over time in the right ratio to encoder pulses over time coming in. And you can't really work in an acceleration on the motor - it has to line up with the encoder, or else you'll get improper threads if you're using the ELS for threading.
Hello! Not a bot! Very interesting indeed, been toying with the idea of doing this to my lathe. Would be very interested in the electronics side of things for this.
I'm working on making the software side a bit more robust and configurable etc. if only the day job didn't take up so much time :-)
Hi Dan. I've been catching up on some of your recent stuff, and this one is particularly interesting to me. Having just had a purpose built workship/hobbyspace completed I can now at long last acquire a lathe and get started on some "tinkering" in earnest. I'm actually looking at getting a small lathe (either the Warco Super Mini, or the WM-180, which can both be bought now with DRO fitted). I'm also learning electronics myself as I like the idea of "messing around" with CNC stuff too. I've been watching a couple of other implementations of electronic lead screws (Clough42 and routercnc), and I like your approach using the Arduino. Very helpful, and very inspiring! I wonder how complex it would be to modify cross slide movement and the compound movement to an electronic solution, integrated with the lead screw. I guess that would make it a full blown CNC machine! Probably VERY complex! Thanks. Terry
there is certainly a fine line between augmenting a manual lathe and just building a CNC machine! I'm handling the backlash in the carriage/leadscrew digitally but if you were going much further I suspect most people would replace the leadscrews with ballscrews or something. certainly in theory you could mount steppers on the cross slide. a bit more fiddly since they'd need to move/carry cables with them etc. the more you augment the more options you need to be able to manage via the control box etc. not sure it adds enough additional utility on a small lathe.
@@MakerGeek Thanks Dan. Understand your rationale. You've clearly done a great job integrating an electronic leadscrew solution with that WM-180. I'm pretty convinced that's the machine I should purchase. Thanks again for your inspiring videos!
@@terryhowlett1434 it's a great little machine. Can highly recommend.
Not a bot!
On the back of the chuck...router pockets for magnets (say every 30 degrees)...mount a hall effect sensor on the case behind the chuck..wire into the arduino...this way it can count the rotations...and be even more accurate, (even better..INSIDE the mounting bolt heads) This way the magnets are out of the way, solidly mounted to the chuck, and the hall effect sensor is out of the way. Will take some work...but will be permanent and not be in the way, might need a wiper or something to remove chips from the magnets though
His leadscrew uses a rotary encoder with a resolution of 600 pulses per revolution, I don't believe a hall effect sensor with a resolution of 12 pulses per rotation would offer any benefit.
I did consider hall effect sensor. I actually started with that as my prototype for the rotary encoder in general. I'm not sure how consistently it would trigger at the same moment. But you're right it would be more convenient as a permanent fix setup.
indeed. for calibration to be useful I just need 1 pulse that is garunteed to be an exact rotation. I have less exeprience with hall effect. I know the optical sensors on the end stops of my cnc are very repeatably accurate.
Hey Dan, hope you’re doing well! Enjoy your videos a lot. I like the tinkering and projects the most but I’m also thinking about whether to get into metal (normally just wood for me) and lathing in particular so great to see this stuff in action! Not sure I get what the compound slide was doing here as I was thinking by moving that you’re effectively changing the “phase” on the threading so I need to get my head round that better. Love the ELS though, not seen one in action before. Cheers!
I'll be honest, my understanding of the compound usage is limited. Essentially you're moving in at the same angle as the thread cutting tip so after the first pass your cutting on the leading edge and not both. If that makes sense. Not sure it makes much difference but it is much easier to track the ins and outs of the total depth cut. I started out with a wood lathe, it's a slippery slope :-)
@@MakerGeek Ok nice - I'll look into the thing about the compound. Without having tried this myself, it's all a bit theoretical at this stage! Yeah, I'm not sure I "need" a lathe (and I need more hobbies like a hole in my head!) - I can justify woodwork tools as I use them round the house regularly, but I need to find more excuses for metal working before I convince myself - either that or just say "it's a hobby" and ignore it's usefulness :)). All the best, Pete
some time ago I accepted that my workshop is essentially a closed eco-system in which i use tools to make/improve other tools ;-) on rare occasion something comes up that also benefits from having the tools. but mostly it just keeps me happy and occupied.
@@MakerGeek - lol, love it!
Why change direction at an endstop rather than, er, stopping? Surely reversing is more likely to scrap the part / tooling?
Mostly a question of options. Most of the time I'm not actually doing a finishing pass, it's just one of many passes that need to be done to dimension down. At which point I'm less concerned about messing up the previous cut. But it's fair to say it would probably be worth being able to toggle between reversing and stopping
Did you use quadrature encoder signal or an interrupt service routine?
It's using an ISR. This does mean i can't tell which way the spindle is rotating. But that's mostly not a problem.
@@MakerGeek Cool, May I ask how you changed pulse width, I've been trying to get my prototype working without accelstepper (it seems too slow but it's probably my code).
@@aaronveale6402 that's just a question of how long you wait between setting the port high and setting it low again. You just need to make sure you're in the tolerance of your stepper driver's ability to detect it. I have been using 5microseconds.
@@MakerGeek so you're using delayMicroseconds? That's what I've been attempting.
@@aaronveale6402 yes. Is it not working for you? What behaviour are you getting?
I have the same lathe and would be interested in your ELS box as it is something that I have been considering as I already have the stepper motor powering the leadscrew.
so at the moment are you just manually controlling speed/direction but without reference to the spindle rpm?
@@MakerGeek Yes that's right, I do have a rotary encoder but not fitted it yet as I haven't had anything to make as I have been busy doing other stuff on my Rose Engine lathe. However, I want to update my RE so will need to get back to some machining shortly.
I am fairly certain that I'm not a robot, at least that's what my programming says.
Yes watching and very interested in one of these.
What actual steps do you get rather than 800, I just wonder
It's about 820 for me. Which seems like a higher deviation than I'd expect from the theory. But this is why we calibrate
Wow, that is a lot of noise. Worth putting a ‘scope on the signal line? Try to track down the source of you extra ‘pulses’ rather than just compensating for aggregate error?
Would you consider sharing the code for this? I'm interested in different approaches to programmign the ELS on arduinos
I've been working on refining it, making it more general purpose and configurable etc. my intention is to make the control box available to buy at a reasonable price. I have considered sharing the code but have decided against it at this time. in my experience open sourcing code leads to a lot of requests for support and changes and not a lot of contribution.
Were you disengaging the half nut between passes? I didn't see you do it but the carriage was stopped and I thought I heard you say you could rejoin at any mark on the dial. I'm guessing you have a metric pitch lead screw. At any rate, nice job.
in this video I was just like a normal threading operation with a gearbox. Since this I've made quite a few improvements and now I can digitally stop/move/restart never disengaging the leadscrew. just pulling together a video on the updates now
@@MakerGeek great, thanks.
I really appreciate that you made this video. Really you deserve all good things. Thank you very much.
I have same pedal, using it with VEVOR TIG. Measured the voltage coming from the machine - it is just 5v. It probably comes from the controller board. One problem I found is that in some positions of the main regulator, pressing the pedal reduces current. I guess the solution is to install an opamp between the main regulator potentiometer and the foot activated potentiometer.