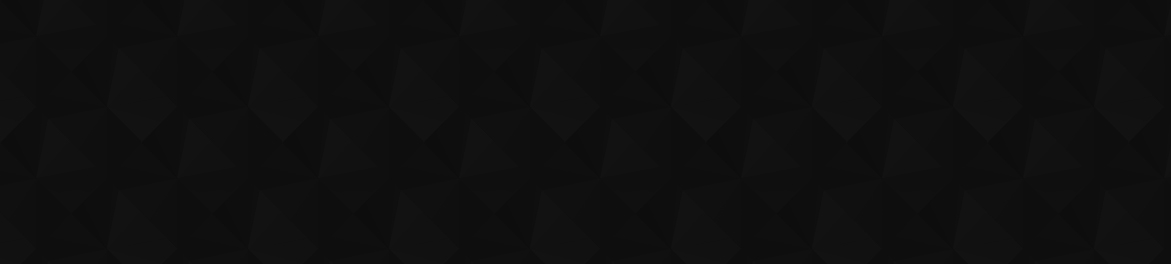
- 15
- 124 340
The Potting Shed Workshop
United Kingdom
Registrace 24. 10. 2014
Radius Dresser Build Part 3
This is the third and final part of the series on machining a radius dresser for my surface grinder. It features machining operations on the mill, lathe, shaper and surface grinder.
zhlédnutí: 1 203
Video
Radius Dresser Build Part 2
zhlédnutí 1KPřed dnem
This is the second video in the series on the build of a simple radius dresser for my surface grinder. This video contains a lot of machining with a shaper and a mill, but no bandsawing!
Radius Dresser Build Part 1
zhlédnutí 2,8KPřed 21 dnem
I need a radius dresser for an upcoming project. Rather than buy one, in this video I start the process of machining a simple one from scratch. I could have simply used the horizontal or vertical mill, but having started to machine the flame-cut plate on the shaper, I decided to try and do as much of the project as possible with it.
Machining an Anvil Clamp for a Uni-Mike
zhlédnutí 1,8KPřed 2 měsíci
I bought a Mitutoyo 117-107 Uni-Mike cheap - it had parts missing. In this video I machine some replacements using best guesses to determine dimensions to make this into a useful measuring tool.
Taylor Hobson Thread Chasing Lathe Part 1
zhlédnutí 3,5KPřed 2 měsíci
This is an introduction to the lathe that I've been restoring on and off for the last 4 years. It's the only example of this lathe I've been able to find anywhere so what's presented here is the result of a lot of trial, error and detective work. The lathe is very much work in progress but this video gives a glimpse of what it's capable of. It is pre-CNC automation at it's finest!
Sharpening the Lead on a Reamer
zhlédnutí 2,6KPřed 2 měsíci
In this video I show how to use the Union Tool and Cutter Grinder to put a lead on the end of a reamer
Mounting a Diamond Cup Wheel on the Union Tool and Cutter Grinder
zhlédnutí 1,5KPřed 2 měsíci
A low cost electro-coated diamond cup wheel is mounted onto my Union Tool and Cutter Grinder. The spindle on this machine is not completely straight and the wheel cannot be dressed, so in this video I attempt to get the wheel mounted and running true.
Endmill Sharpening Part 2
zhlédnutí 2,9KPřed 3 měsíci
In this second part on sharpening endmills on the Union Tool and Cutter Grinder I sharpen the end cutting faces of 2 and 4 flute endmills.
Elliott 10M Shaper Gear Cutting Fixture Part 5
zhlédnutí 29KPřed 3 měsíci
In this final part of the series on the gear cutting attachment I cut two helical gears, one in bronze and one in steel. The finished gears are then mounted in the mill to measure the ideal axis spacing for smooth engagement. The measurement technique was devised by Tom's Rabbit Hole: www.youtube.com/@thomasstover6272
Elliott 10M Shaper Gear Cutting Fixture Part 4
zhlédnutí 4,6KPřed 3 měsíci
Continuing the series on the gear cutting attachment for the Elliott 10M shaper, in this episode I go through the setup required and prepare to cut a gear
Elliott 10M Shaper Gear Cutting Fixture Part 3
zhlédnutí 13KPřed 4 měsíci
This is the third part in the series on the gear cutting attachment for the Elliott 10M shaper. In this part I configure the shaper to cut a 20 tooth, 12DP spur gear and cut the gear.
Elliott 10M Shaper Gear Cutting Fixture Part 2
zhlédnutí 6KPřed 4 měsíci
In this part I go through a little more detail on the overall system, machine a blank for the gear and modify the cutting tool that will be used to shape the gear. This is my first try at machining on camera in a proper video, so please let me know in the comments if there are things I could have done better.
Elliott 10M Shaper Gear Cutting Fixture Part 1
zhlédnutí 35KPřed 4 měsíci
An in-depth description of the involute gear cutting attachment that I made for my Elliott 10M shaper
Cutting a helical gear on an Elliott 10M shaper
zhlédnutí 10KPřed rokem
First tests of a bolt on attachment for cutting helical gear teeth on a 10-inch shaper
This series of videos on gear cutting on a shaper is fantastic and very informative, great job Robert, the only thing that I don't understand yet is the spreadsheet of calculations. I have a 16 inch European shaper and a universal dividing head that mainly get used for keyway/ spline cutting so this will be something else to look at doing.
Robert, this video definitely was not too long for me. I also liked your use of milling cutters in your boring head -- I'll have to try that too.
@@bobvines00 Thanks for the feedback Bob. The editing took a lot of effort to keep the video moving at a good pace. As for the milling cutters in a boring head, it was because I couldn't be bothered to spend a couple of hours grinding some HSS, so it was a win-win situation!
Another fine example of tooling using a wide range of your machines. The set up on the Shaper is just great to watch.and the finished dresser will be a great addition to the Grinder. Nice work
@@Griffon37 Thanks Jon. In a couple of videos time I might get round to cutting a gear again😁
Very nice work as always Robert a great usefull project ! As an aside, I have had similar finish issues with that style of boring bar in the boring head. I found using an insert for aluminium works much better for the small depth of cut which is more common on the boring head. The style of inser I have used is a TCGT which is ground and honed to a sharp edge much like a hss tool. The moulded insert TCMT is good when you can give it a good depth of cut to get over the edge of the moulded insert. So I tend to rough with a moulded insert and finish with the ground insert. I also do this with the lathe tools if I need to take a very small depth of cut,it will prouce swarf almost down to dust size if needed. A good use of el cheepo import inserts for me ! Would be interested on your thoughts on this?
@@neilh2150 I like that suggestion! I use CCGT inserts for finishing on the lathe and this looks like the same way of working adapted for the boring head. Thank you! BTW, the moulded inserts always seem to rub on the bottom of the front edge, so I invariably grind a little more relief, avoiding modifying the cutting edge. I guess I'd end up doing the same with TCGT inserts, as most of the holes I bore out aren't that big a diameter. Or maybe I set the boring bar to the wrong angle in the boring head...
Lovely engineering at its best, certainly "Built not Bought", works brilliantly. During my apprenticeship I worked on a shaper for nearly a year on production jobs, 18" Churchill comes to mind?. One regular set of parts to machine were some hardenable stainless steel circular discs, and bevelled hubs that when assembled formed a pulley Vee with serataions to bite onto and drive a copper alloy seam welding wheel, circ 200 to 400 mm diameter. My job was to set up what I think was a purpose built dividing head, with a mounting spindle for the individual parts to be machined, and connecting the shaper ram directly to a ratchet and pawl arm to index the head. This 1978/79, so excuse me some of the details are wrong! Stainless steel was needed due to the strong magnetic flux developed by the very large AC welding currents required for resistance welding. Thanks again for sharing. Regards John from the Black Country.
really good viewing!!,, what a set up at the 30 minute mark!! awesome👍👍
Glad you liked it. I like a good setup too. It always seems to take longer than the actual machining.
Nice use of milling cutters in the boring head, I purchased a boxed boring head from a auction, it was full of the most weird grinds on all sorts of hardly recognisable milling cutters. 2 flute milling cutters work great in a lathe tool post for short bores, especially in brass or plastics. Excellent build and photography, thanks for sharing. Best regards from the Black Country. John
Thank you. Using the milling cutters was a result of laziness... I really didnt want to spend hours grinding up a cutting tool. I've never really got on with that carbide insert bar.
Nice Mate!
Thank you very much. I put much more effort into the editing, which takes me ages!
Very interesting video. I’ve never seen such fine curves. Lot of equipment in a shed. Very good stuff.
Thank you! That was a lot of work compacted into that video. As for the amount of equipment, it's squeezed into the little space I have. Using the bandsaw for example, I have to move a tool cabinet so the saw can be pulled out to use!
Olá amigo que maravilha de trabalho,perfeito!!! Lhe desejo saúde e cada vez mais sucesso!!!
Thank you very much!
That was a great series, very nicely done.
Thanks! Took me ages to edit that last part. Hours of filming got junked!
Really enjoyed this series Robert thank-you. I'm pleased to see the I'm not the only nutter that's made his own adjustable parallels! Did you cut the dovetails on the shaper?
Thanks! Well, other than rough Chinese offerings, adjustable parallels aren't that cheap! Didn't use the shaper for those, I sharpened a face & side cutter at an angle, tilted the work by the dovetail angle and horizontally milled them. They were then surface ground to make everything line up perfectly and to make them look pretty.
I don't think I ever had an "oops" moment like that... well... not more than a few times a week :)
Only a few times a week! Very proficient😁
Its very enjoyable watching you work.
Thanks! All edited to speed things up of course😁
Beautiful work,Robert and good to see how you do use your macinenes.Thank you.
Thanks!
A very clever way to use the micrometer
Thank you!
Very interesting. Nice work sir
Thanks very much!
Good video. What do you call the fixture that holds the ER32 Collet and mounts to the table? I would like to buy one. I think with one of those I can use my surface grinder to sharpen end mill flutes.
I think a universal head is one of the names for the fixture that carries the bore. I agree that a surface grinder should be capable of doing the grinding. I often use mine in preference to the TC grinder for several grinding operations when its more convenient, or when the increased rigidity of the SG makes a better job of it. There isnt to my mind much difference between the two machines. The SG usually has a mag chuck on the table, ground flat in situ, which makes it unattractive to remove to fit alternative fixtures.
@@ThePottingShedWorkshop I had a design for one years ago, but never got around to making one. In fact the plans may have been from a book by a guy last name Hall. Thanks for your reply.
I wish my shaper had an auto vertical feed. But... I really miss that. And indeed, a sheertool gives the best results at 15° à 25°.
Can you not modify it to have vertical feed? As for the shear tool, I've been using the wrong angle for too long!
@@ThePottingShedWorkshop I think it's possible, but I need to drill and tap holes in the machine. I don't want to do that.
@@Rustinox Yes, I don't like making permanent mods to my machines if I can avoid it. The Elliott 10M already has the stub shaft hole drilled and a locking screw hole drilled and tapped.
I don’t think anyone can complain about bandsaw footage when you are entertaining us for free. Your videos are well put together and the subject matter is right up my street. Thank you.
Thanks for that. Yes, you're not paying to watch it and I'm not getting paid to make the videos! I can see the bandsaw becoming a bit of an ongoing joke!
Nice video, Robert! I just bought an older 12 in. shaper, and I’m looking forward to getting to know it…
@@thomasstover6272 Nice one! I hope it's in good condition. Mine's had a lot of TLC to get it cutting accurately, including scraping the cross slide ways. I look forward to it appearing in a video!
That's good. Shapers are fun.
WOW, that is great. Do you know if it is possible to make helical bevel gears on a shaper?
@@kioliex Thanks. I think I can see a way to make bevel gears on a shaper, but helical bevel gears, I think not. The fundamental principle behind cutting gears on a shaper is that the cutting tool resembles a rack tooth. As a helical bevel gear will not engage with a straight tooth rack, I don't see a way of cutting one with the shaper.
@@ThePottingShedWorkshop Okay, that makes sense. Thanks.
Good to see the progress,Robert.See you part 3.Thank you.
Thanks. Part 3 is a bit long but I wanted to squeeze everything into one video. It should be out next week.
The relationship between shaper tools and surface finish is extremely complex and subtle.
Hmm, so I've found!
Nice to see you using the vertical feed, I never got a "round toit", despite buying the gears some twenty years ago when I first had my 10M shaper!. The joys of high angle shear tool! I'm glad your persevering! Cheers, Matthew
Thanks. I knew the vertical feed would come in handy one day!
Recently found your channel and loving the content. Do have a question, though. I understand why you didn't angle the 40 deg relief cut. I agree it would retreat and eventually be none center cutting. However is it truly center cutting now with what looks like 1/2 of each flute being a 90 deg plowing into the work?
This is a very interesting video and I'm eagerly awaiting "Part 3"! Does your part/vise/shaper knee "dip" down during cuts or is that an optical illusion?
@@bobvines00 I'll try not to disappoint with part 3! No, its not an illusion. The whole shaper rocks as the ram slides forward. The support bar under the table minimises sag on the table alone. I guess I need to jack up the front a tad to minimise it, but as it doesn't seem to affect the accuracy much (1 to 2 thou parallelism on a part), messing with the machine feet hasn't risen to the top of the project queue!
Hi Robert. I enjoyed the video thank you. This project is becoming very interesting. Look forward to the next update. 👍🇳🇱
@@alungiggs Thanks. Still have to edit part 3 but I'm hoping you'll find a couple of things in it a bit different and interesting!
"A bit marmite" is my new favorite expression!
🤣
You can do the video in half the time. Then you get more like and....
Great stuff, It's good to see the shaper being used! I don't know why there are so many complaints about the bandsaw footage, I find it works great to send me to sleep. Better than counting sheep. More bandsaw footage!!!
🤣
Sorry for your loss Robert. That’s a great idea to use the spindexer, I’ve been looking to buy a radius dresser for some time, I won’t need to now - thanks.
Thanks. Glad you like the spindexer idea!
Sorry for the loss of your father.
Thanks.
My condolences
Thank you.
Hi Robert, condolences on the loss of your father, lost mine 2 months ago, last picture was of him in hospital intently watching your gear cutting on the shaper! He was most impressed! Another great how too on the shaper, Dads Amcco 7” is coming to my shop. Cheers Kerrin
Hi Kerrin, Condolences to you too. I'm going to miss being able to ask my Dad about gardening matters, about which he knew more than I do. It still surprises me who and how many people watch the videos I produce. You'll enjoy having his shaper in your shop. I don't use mine on every project, but there are some things that are so much easier with a shaper, like internal keyways, and its fun running it.
Ohhh god; the bandsaw. That brought back painful memories from only 2 months ago. I wanted 40mm riser feet for my lathe, mill and surface grinder. I have a 4.1/2 bandsaw and a 90mm dia section of scrap hydraulic cylinder chrome bar and need 13 feet. It took over a week on and off, 3 blades and 2 tins of cutting fluid. Each cut took well over an hour, with a new blade. Far, far longer without. Shuddering just thinking of the horror of it all. I'm looking forward to seeing the rest of the job though.
My condolences Robert.Excellent work.Thank you.
Thank you! I might have overdone the footage of bandsawing though😳
Having lost a father, I feel for you. Thank you for machining this with the shaper. I've long wondered about running a shaper bit into a sharp corner, as you demonstrated here. I'm glad that you've chosen the shaper for this, instead of the milling machine!
Hi Marc, Thanks. Its much worse for my mother though. When I started machining this, I used the shaper in case the tool got blunted by the flame cut edge, as sharpening is easy. However, it was more interesting for me to attempt to do most of it with the shaper. There are bits I resorted to the mill though, as you'll see in part 2.
Condolences on the Loss of your father Robert. I lost mine in 1985 39 years ago and I still miss him and his influence. But it does get better with time. The first bandsaw cut was a bit long winded lol but yes I know what you were trying to convey........ 'god I want to get on with my project!'
Thanks. Funnily enough, editing it felt like it dragged on but I was pressed for time. Normally I watch through what I've done before posting but I ran out of time as we had to travel for the funeral.
Did I just fast forward through the entire, real time bandsaw cut of a 4x1.5" hunk of metal? LOL, that's a no from me.
Sorry, it was edited in a rush. The alternative was not to post this week as I'll not get the chance to edit any more till Sunday. I will take your comments on board and try to make part 2 move quicker.
Suggestion, 'm not sure I really need to see every chip coming of the band saw!
I can't disagree with you. Sorry, I had limited time to edit the video, so I didn't get chance to review it before posting. If you stick around for part 2, I promise to do better!
I'll be there for round 2! You're work interests me !
Condolences at this difficult time. I appreciated your video and look forward to seeing this project progress.
Thanks. This is just a project to make another project possible, which is for another project... 😁
Condolences Robert, Thoughts are with you
Thanks.
Hi Robert. Condolences for the loss of your father. I recently lost my mother. So, my thoughts are with you 🙂. I enjoyed the video and look forward to seeing the next instalment. Greetings from Amsterdam, Al. 👍🇳🇱
Hi Al, Thanks. It's not nice but inevitable, especially as he'd reached 89. Next part has been filmed but not edited yet. Takes me ages to edit,, something like about 5 hours for this one. I'm sure I'll get quicker one day😁
I have never seen this technique before! Thank you for sharing.
You're welcome!
Very nice work sir. I like it when a tool can be saved and get used again.
Nice job on a rare tool build. We shared this video on our homemade tool forum last week 😎
Have you considered instead of using a serpentine belt, using a coged belt with the driving pulley wide enough to allow the belt to walk back and forth with the headstock?
Fascinating.
Thank you. It seems to be a bit of a unique beast now.
That's a nice machine. Thanks for the lesson.
Thanks. The grinder is just the right size for my workshop. It's one of the machines I wouldn't be without now.
@@ThePottingShedWorkshop I don't have a T&C grinder but so I've no practical experience but that one looks nicer (more refined) than the Clarkson. Cheers