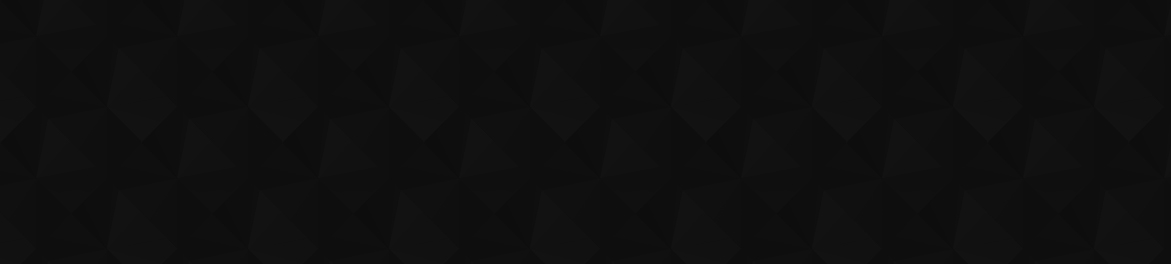
- 35
- 279 526
Bat Country Forge
Australia
Registrace 13. 05. 2015
G'Day I'm Dave and welcome to my channel.
www.batcountryforge.com
I am a Sydney based bladesmith and I aim to upload regular content for my customers of their knives being made. Feel free to request videos of different techniques or processes and I will do my best to capture them.
If you would like a blade or are curious to learn more check out my:
Website www.batcountryforge.com
Etsy store www.etsy.com/au/shop/BatCountryForge
www.batcountryforge.com
I am a Sydney based bladesmith and I aim to upload regular content for my customers of their knives being made. Feel free to request videos of different techniques or processes and I will do my best to capture them.
If you would like a blade or are curious to learn more check out my:
Website www.batcountryforge.com
Etsy store www.etsy.com/au/shop/BatCountryForge
Chef knife made from mining equipment
Core steel made from Caterpillar Universal joint bearing steel, soft jacket made from D11 ripper pin.
The core steel is forged out flat, ground clean then forge welded between two pieces of flattened ripper pin.
Usually I would use dedicated knife making steels but this was a bit of fun to raffle off at work for a good cause. Didn't have much time to film this one in between making the knife so there are a lot of steps that were not captured.
The core steel is forged out flat, ground clean then forge welded between two pieces of flattened ripper pin.
Usually I would use dedicated knife making steels but this was a bit of fun to raffle off at work for a good cause. Didn't have much time to film this one in between making the knife so there are a lot of steps that were not captured.
zhlédnutí: 456
Video
A simple Kitchen knife is made (2,000 subscriber give away!)
zhlédnutí 1,2KPřed 3 lety
Win this razor sharp hand crafted (from my workshop off cuts, think *recycling*) kitchen knife for yourself!!! Karl Truscott's message won the draw via excel random selection - 12/2/21 I have just got the new workshop up and running after nearly 12 months! To celebrate I made a quick little kitchen utility knife which will be given away on 12 Feb 2021. Hopefully I am at 2,000 subscribers by tha...
What to wear with a kilt? FREE SGIAN DUBH????
zhlédnutí 499Před 4 lety
This will be my first Instagram give away, that's right, you could win this knife!!!!! Watch as I make a Scottish Sgian Dubh ( also mispelt as a skean dew or miscalled a sock dirk) Head over to my instagram page to go in the running to win this knife or one of my the next monthly give away prizes. Sgian Dubhs are one of my specialties, I really enjoy making them. From time to time they are also...
Making a Damascus Steel Sgian Dubh
zhlédnutí 499Před 4 lety
Forging a damascus steel Sgian Dubh from 1075 and 15N20 steel.
How to forge a kitchen knife, forging W2 steel
zhlédnutí 810Před 4 lety
A complete video capture of forging a kitchen utility knife from W2 steel. This was 6mm stock which I normally forge under the power hammer but there are plenty of people who don't have those. So I did it the long way... I think one of the most important things I have come to learn is that to keep the proportions of the blade where you want them the whole blade has to arrive at the point of com...
Beginners Knife Sharpening
zhlédnutí 804Před 4 lety
A quick video I put together for anyone interested in finding a simple method to practice sharpening most symmetrical kitchen knives. I.E not specialty ground Japanese knives or knives with a zero grind. This technique should work for the average knife in most Australian kitchens. I have found while selling my knives people have plenty of questions about how to sharpen their new knife. When I b...
Forging Deba Knife
zhlédnutí 7KPřed 5 lety
In this video you can see the many things I put under my Anyang power hammer to compensate for not having cutlers dies fitted :) I make a second two layer deba using 80CrV2 and mild steel, this time I started out with 12mm mild steel and 6mm carbon steel to try and prevent warping by having a thicker body of non distorting steel... well you will see how that goes. This knife is currently availa...
Forging Japanese Deba: Part 2
zhlédnutí 920Před 5 lety
Part 2 of my Japanese deba knife build, made with mild steel and 80CrV2 High carbon steel forge welded together. I am quite fascinated with the 2 layer forge weld method at the moment as it presents some unique challenges. Firstly using mild steel and carbon steel to make up half of the blade each ensures that the blade will warp. I found that after tempering and grinding a hollow into the back...
Forging Japanese Deba: Part 1
zhlédnutí 905Před 5 lety
A short video of some of the work I did in the shop this afternoon. I haven't made a video for a long time. Ni Mai blade made of 80CrV2 and mild steel. If anyone knows the correct designation for a blade of 2 main layers please let me know. Forged to a deba shape I plan to asymmetrically grind the blade for left handed use with a hollow grind in the back. One of the unique challenges to this ty...
Vallorbe hardness test files
zhlédnutí 12KPřed 6 lety
A video for knife making tool geeks. I think these Rockwell hardness test files are an essential part of your shop when you start heat treating tools and knife steel. They can easily tell you if your steel has hardened and roughly how hard the steel has gotten. While no match for a bench mounted indentation tester these will get you confident in your heat treating ability. Get a set yourself at...
Forging a HUGE pattern Welded bar at Eveleigh Works Redfern (better Audio)
zhlédnutí 18KPřed 6 lety
For this video we go and visit Matt Mewburn at Eveleight Works 1880's Locomotive workshop turned School of Blacksmithing. Flaming hot mischief abounds. This is actually a collaboration I was invited to join by Sam Fowler and Irish Mike. Matt and I forge a HUGE billet of pattern welded steel that will be forwarded onto Sam for shaping and machining. Then onto Michael Cthulhu for some of his slic...
Klingspor Wonder Discs
zhlédnutí 2,1KPřed 6 lety
Klingspor NCD 200 I bring to you the klingspor cleaning disc? I am not sure what they are supposed to be called. The cleaning disc, perfect for forged axes, swords and sculpture. Do not use on Hot steel!! Great for rust and scale removal, and begins the surface finishing process for you. This disc not only grinds but begins polishing the steel so as not to leave gouges. Get them here: www.artis...
Heat treating O1 Steel and grain growth
zhlédnutí 11KPřed 6 lety
I get asked quite often about heat treating O1 tool steel. While it is relatively simple in annealed flat section forging brings with it some challenges. If stock removing from flat bar (or round bar if you hate yourself) heat the O1 after machining to 815 Degrees Celsius and hold for around 10 minutes. Quench into medium speed oil and then consult a tempering diagram. If forging try to keep th...
Electro Etching Blades Again...
zhlédnutí 2KPřed 6 lety
Re shot a quick overview of the Metal Marker MK3 as the last video had no sound... Electro etching is a very versatile way to mark your blades as you can easily change designs or etch large areas. The flash toner stencil system is as easy a printing your design on white paper with toner based ink and hitting it with a zenon flash bulb. I used the below bits and pieces: www.artisansupplies.com.a...
Making a custom logo etch on a blade
zhlédnutí 1,1KPřed 6 lety
Ever wondered how to make a repeatable impression of your makers mark on a blade. Electro etching can be a really great method for sigining your work. If using flash toner stencils you can easily change the design and size of your mark as simply as printing the image with a TONER printer. Inkjet will not work. Using the Gelandangan Metal Marker MK3 I demonstrate how to simply etch your makers m...
Heat treating Simple carbon steel in a forge
zhlédnutí 4,8KPřed 6 lety
Heat treating Simple carbon steel in a forge
3M Trizact Gator Belts for knife making
zhlédnutí 18KPřed 6 lety
3M Trizact Gator Belts for knife making
Beginners Heat treating SUP9 / 5160 steel
zhlédnutí 25KPřed 6 lety
Beginners Heat treating SUP9 / 5160 steel
Steel for making knives Australia: The best steel for beginners!!
zhlédnutí 32KPřed 7 lety
Steel for making knives Australia: The best steel for beginners!!
Blacksmith forges Mighty Scottish Weapon
zhlédnutí 1,1KPřed 7 lety
Blacksmith forges Mighty Scottish Weapon
Tips for new knife makers: How to get clean curves on handles
zhlédnutí 3,2KPřed 7 lety
Tips for new knife makers: How to get clean curves on handles
Why does every Damascus beginner video have a damn power hammer
Hi are you still teaching locally?
i have no power hammer,how can it works for me?
I bought one kitchen chef knife for around 50 euros and it had nice symbols on it, but damn a knife 50 euros thats crazy... 3d printing should make it cheaper to make those knifes though, specially in the future..
Five years old, but I have a question please (if you're still active). Do you just test this on the very edge? Is that because that area will be removed during sharpening anyway?
No you can test all over as long as you have ground the scale back and are checking steel itself rather than oxide. Its often interesting to see how the thickness will impact hardness. A slightly softer spine might be preferrable but you need to know that the "working" part of the blade has hardened as you intended.
Thanks mate
@@batcountryforge5945Hello again! A quick question please. Should you run the file across the edge or the flats of the bevel? I have a piece of steel that skates on the edge up to about 60, but scratches the flats. Also, how much pressure should I apply? I know that's hard to describe...
Thanks for this helpfull and detailed tutorial. I crack a can for you, cheers from Germany
Great video. I plan on using 01 steel for all of my knives. I think thats how i found your video. Very helpful for me thank you
Nice 👍
Great work
Thats strange, I didn't know Sam worked on horses hooves 🤔 and was an author 🤔🤔 and has been to six countries 🤔🤔🤔 and that his name is SIMON instead of SAM 🤔🤔🧐🧐
Love the recycling idea. Good work
Thanks mate, u'll have to come for a hit one weekend
Nice work Dave
Thanks mate, video was a bit of a rush to fit with making the knife. That steel got 65 on medium oil quenched from 805 degrees and passed a few flex tests, hoping it was similar to 52100 or SUJ2. The joy of unknown steel ay
Are you around Victoria? Do you do custom made sword? How much for one but I do it in your shop but I pay full price.
What are you add that whit powder please replay ????
Borax to act as a flux
Borax powder or boric acid
How can i bay that
Sodium borate, usually sold with laundry supplies which you might be able to find at a hardware store. Anhydrous borax is the best. Anhydrous borax is sold at a few blacksmithing supply companies.
Are there gator belts for the 1 by 30?
Would love to give you a " Thumbs-Up " sadly your Audio tecording fell short..however keep up the good tutorial work..!!
Rockwell c indicates the shape of diamond used. C being a rounded one.
Copy, I have a big electronic one now, Ill have a look but I'm pretty sure it does have a round indenter.
I had a quick google, rockwell b apparently means ball, and rockwell C means it has a cone indenter. Load force is also different between the 2 tests. Good comment, I never would have come back to think about that.
@@batcountryforge5945 sorry, I remembered it wrong.
Grate build
Thanks Dave, just found your channel and subbed!
Thanks Paul, I work big days in mine rehab now but I am hoping to free up some time and do some more videos!
Could you heat treat 5160 in a charcoal forge like 1084, say minimal soak time and let it go just past non magnetic, quench in canola oil afterwards. I have used 1084 with success for blades and tools, but would like to use a tough big chopper type steel for large blades, but backyard heat treat set up.
The soak time would be key to getting the most out of spring steel. You really want to get that cromium and silicon disolved properly to get any of the benefits of using the spring steel. Otherwise stick to your 1084. I mean you could do it and you will harden the steel some but you could get a better result if you get temperature a d time right.
@@batcountryforge5945 Thanks for the info.
truck springs are usually 5160, which is a very good steel for beginners..You can of course get new 5160 from spring makers.. heat treat temps are not real critical. Non-magnetic is hot enough, although 825 or 835 might be better. you *can* use a MAPP torch shooting into a small firebrick enclosure for a forge but you'll go broke buying those 400-gram bottles.far better to build a real forge.
Very nice training.
What is oil name ???
In the description it reads canola oil
Thank you for sharing this. It's still impressive what you can do with a MAP gas torch. 👍
I've always used my homemade propane forge to heat treat never tried to use a map torch until today. Well last night, I was using unknown steel so I tested a piece and it hardened great, but when I went to heat treat the blade I couldn't get a uniform heat. I ended up doing it in two parts. Bottom half closest to the tang then top half. It hardened enough to slice my finger open and then cut paper after I ground the forge scale off on the belt but I wasn't satisfied with it so I annealed it and I'm just gonna wait til I can get my propane tank refilled. Money's tight these days is the only reason I even tried with the map torch. I just happened to have a tank sitting around unused. Not sure why I couldn't get a good uniform heat, the blades only about 5-6" inches long. Idk 🤷🏼♂️
Beautiful mate.👍
How about talking
Is there something else you need to know?
So you test the forge weld by hitting it diagonally, but you've tack welded the pieces together. How would you know, just caught my attention.
Because it is soft the layers will separate dispite the tac welds. Also ideally, you lay the welds in so poorly that the weld metal falls away after a few heats ;) dont want them ending up in the knife.
All those old tools, love it
Most beginners have a hydraulic hammer. Lol
Thanks for sharing. I am learning to make a Damascus knife and need to know what needed to join the metal
Thanks for the advice. Just starting out and I've been looking for a while for a good steel to start with. A lot of people get to in depth with all the different kinds of steel. Ima go with 1085 thanks to the advice!
1084 sorry
hey mate, thanks for the video, but what type of gas does the burner require as i may purchase one for myself?
Hi Daniel, LPG (liquefied Petroleum Gas) which is mainly Propane and Butane. The burners I use here run well on an 8.5 kg BBQ cylinder. In colder climates (Eastern NSW winter) they do tend to drop their vapourisation rate and it can be hard to sustain forge welding unless it is a full cylinder.
@@batcountryforge5945 thanks man
Hi...i try to make my first damascus but does not become
Does sup9 holds an edge like 5160?
Hey mate, do you still make deba knives? Could you make one using a dyed maple burl?
Banyak bacot anying..
So you are quenching as soon as you hit non-magnetic? You're not going slightly past non-magnetic?
With this method by aiming for non magnetic you will probably overshoot the 815 degree mark a bit. If you aim for "slightly past" I reckon you are likely to overshoot by 100 degrees. There are a lot of variables with this method but if a little torch is all you have it can get you started in the hobby. If you enjoy it, long term aim to build something that provides good insulation and bettler heat control for heat treatment. Have you had a go yourself yet?
@@batcountryforge5945 I see. I've made about a dozen knives. I hollowed out some fire brick and use a mapp gas torch for a mini forge. I still have a lot to learn about heat treating.
Q: "The best steel for knife making?" A: "That steel that you can't find anywhere."
Where abouts are you?
@@batcountryforge5945 Arizona. I have been looking for 1080/1084 steel for months. I can't even find it online. It's sold out everywhere. All I can find is very limited 1075 and plenty of 1095, O1, etc.
@@KurNorock If you grab that 1075 and treat it like 1084 to begin with you will be off to a great start.
I’m new to this and just starting out. Made a few single metal blades and I want to try Damascus. Is it a bad idea to only use a few layers, like 3-6?
Bruda..😗😘
DON'T KNOW WHAT YOU SAID OR HOW TO DO WHAT U ARE DOING...............
Would the same process apply if using a coal forge or would I need to get a gas forge?
It does, however it is a little harder to see the borax temp with solid fuel. I began by forge welding in a coke forge. Just be careful about overheating the steel which is much easier to do accidentally in a solid fuel forge. Start setting your welds with light hammer blows when you see the steel just beginning to throw off sparks. The sparks show that the steel is burning so too many sparks is also a bad thing.
Where can I buy a torch like your?
I got mine from Bunnings, also sold at gasweld and total tools in Australia.
How bout the sup9 steel is that exact 5160, is sup9 a good steel?
Nice video, I just started working with 01 this year, I got some practice in soaking for around 8+ mins using 1095, but I have to do it by hand and eye control, as my forge isn't temp controlled, that's the tricky part, soaking by eye took me about 2 years to get down without over heating it. I had to make a very specific open back forge, which lets a lot of the heat out, so it doesn't get too hot in there.
Thank you I really enjoyed the Video I'm just starting with my first Knife, making it from an old Farriers Rasp. Cheers
What is the resin you used to glue the Handle can it be got from Bunnings if not where can I get it I'm on the Mid Nth Coast NSW
Hey mate I used Blade bond Epoxy from Artisan Supplies in Sydney
@@batcountryforge5945 Thank You very Much.
Oh my goodness! I'm an engineer and heat treater. I make knives too. As far as O1 heat treat is concerned you do not hold it at hardening temp for 30 minutes nor 5 minutes. If you buy spheroid O1 with 0.10 to 0.20% vanadium like I do there is no need for for grain refinement with this steel, it is not 1080. I started heat treating O1 in a charcoal forge in 1992 and then I bought a nice Paragon oven and made perfectly heat treated knives thanks to Kevin Cashen. Firstly O1 doesn't decarburize nearly as much as 1080-75 or L6 or simple alloys. If you're going to forge it that's a different story. But it isn't necessary to do three cycles if you just buy the O1 with Vanadium and stay away from Latrobe's formulation. Some folks are under the impression that that small amount of vanadium would make vanadium carbides. Not at all, it restricts grain growth quite a bit. It is why I'd buy 80CrV2 instead of plain 1080. If you want the edge holding of a high vanadium steel and only have a forge there is a steel for you called CruForgeV that is essentially 80CrV2, but with 0.75% vanadium. Oh and FYI, vanadium carbides are harder than tungsten carbides. Alpha Knife Supply sells it in .250 thick flat bar. Do not forge below 980c to 1065c and normalize at 870 C and slow cool to room temp. To anneal heat to 760 C and slow cool at no more than 22c per hour until after it drops below 640c then it isn't as critical on the temp drop, but nothing quick, just a slow air cool after it hits 1000 F. This is Bohler's formulation. Latrobe doesn't have the vanadium. O1's analysis. Carbon, 0.95 Chromium, 0.55% Manganese, 1.10% this is very, very high for a knife steel, but has its uses. Silicon, 0.30% Tungsten, 0.55% Vanadium, 0.20% To austenitize with an oven, heat to 1200 (650c) and equalize then ramp up to O1's sweet spot at 1475 (801c) for 15-25 minutes (according to thickness) then quench in 120 to 130F oil, Canola oil or peanut oil both work, but they break down after a while. Within two to three minutes after quench if there is any warp have a vise and heavy pliers handy to straighten, but after four minutes it loses its flexibility and you must straighten during temper. This is that high manganese content, O1 is the only steel I know that will do this. Note the 15+ minute time is for O1 with vanadium only, otherwise only hold 7-15 minutes depending on thickness. The 15 minute time will put the chrome and tungsten into solution and you will get chromium and tungsten carbides. If HT in a forge for 5 min you will get mostly ferrite or iron carbides. If Liquid Nitrogen is available then use it as it will work on O1 and improve the toughness, although it isn't worth paying for the improvement you'll get. If HT in an oven for max hardness then the As Quenched hardness will be HRC 64-65. Temper at HRC 400f/204c for 2 hrs. 2x for 63-62 450f/232c for 2 hrs. 2x for 61/60. 500f/260c for 2 hrs. 2x for 59/60.
Cheers man good info!
Would I be able to forge a piece of CPM 10v without messing anything up? I faintly remember the forging window being 1700f - 2000f. Could this be done safely without a temp controlled oven? What should I look out for? 17%~ carbide will be hard to move, so I may eventually try forging other lower carbide tool steel. Also, are high speed steels unable to be forged, or are they just harder? Thanks.
@@lindboknifeandtool I would stick to 52100 and not try to forge high alloy steels. I know an experienced forger and he tried forging D2 with all its Chromium and 1.5% carbon and he said it was a disaster. He made some knives, but threw them away when one just popped off the table all cracked.
Wow, some amazing info right here. Sounds like Mountain Fisher knows his/her stuff. Been struggling all week with heat treating several hundred small, quarter sized parts made from O1 and arrived at similar conclusions....
Hey mate great video, I want to buy some steel to make some larger survival/chopper style knives, will I get the most out of 5160/SUP9 by heating past non magnetic and quenching in canola like you would with 1075/84?
I read on creativeman.com that it can be heat treated the same as the other basic carbon steel but I've read conflicting information elsewhere so I'm not sure.
Hi Wilson, the short answer is no. To properly dissolve and even out the carbides and things like chromium/silicon you will need to soak the steel. I.e. heat it to its autinisation temp and hold it there. I would think depending on the alloy/ thickness it will be between 5-20 minutes. So if you are looking for "the most" out of any steel you need to know its austinitisation temp and soak time to start.
Hi Wilson, the short answer is no. To properly dissolve and even out the carbides and things like chromium/silicon you will need to soak the steel. I.e. heat it to its autinisation temp and hold it there. I would think depending on the alloy/ thickness it will be between 5-20 minutes. So if you are looking for "the most" out of any steel you need to know its austinitisation temp and soak time to start.
It will definatley harden but you will be leaving some performance on the table. Ill look up the specifics and get back to you.
@@batcountryforge5945 Thanks mate I thought that would be the case