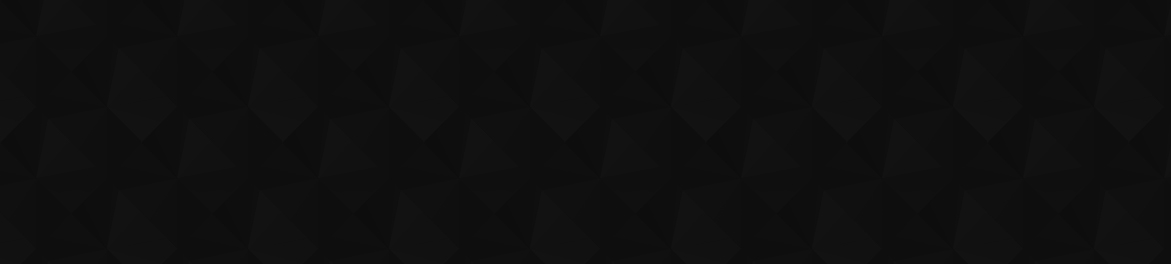
- 109
- 1 373 070
GD&T Basics - Engineer Essentials
United States
Registrace 20. 09. 2015
Our goal at GD&T Basics is to be your best source for GD&T information online! It is important to us that everyone involved with engineering and machining has the chance to learn and better understand GD&T and your prints. We offer custom training solutions for both individuals and companies to help increase and clarify your knowledge of GD&T.
We strongly believe that you can learn and apply GD&T if you break the concepts down and relate them to how they are actually used in the real world - not just what is written in the standards. GD&T can be a huge benefit to those companies that adopt it. In fact, GD&T allows companies to save time, money, and headache by only focusing on what is functionally necessary for their product.
Our passion is to make GD&T approachable and understandable. After using our course material, we promise a strong foundation in your GD&T knowledge that you can confidently apply in your work.
We strongly believe that you can learn and apply GD&T if you break the concepts down and relate them to how they are actually used in the real world - not just what is written in the standards. GD&T can be a huge benefit to those companies that adopt it. In fact, GD&T allows companies to save time, money, and headache by only focusing on what is functionally necessary for their product.
Our passion is to make GD&T approachable and understandable. After using our course material, we promise a strong foundation in your GD&T knowledge that you can confidently apply in your work.
Reporting Size Dimensions with a CMM
In this Question Line video, Jason answers questions about reporting size dimensions when using a CMM. He briefly explains Rule #1 of GD&T before diving into the criteria needed in order to accept or reject a feature of size. He also discusses manual vs CMM inspection and the reporting requirements of the ASME Y14.45 standard (Measurement Data Reporting standard).
Interested in learning more about Print Reading or GD&T? Check out more of our free GD&T resources here: download.gdandtbasics.com/youtube-free-gdt-resources
Interested in learning more about Print Reading or GD&T? Check out more of our free GD&T resources here: download.gdandtbasics.com/youtube-free-gdt-resources
zhlédnutí: 405
Video
When to Use DML Straightness
zhlédnutí 785Před 21 dnem
In this Question Line video, Brandon walks through examples for both surface straightness and derived median line straightness, explaining how to correctly apply them and discussing design and inspection considerations. Interested in learning more about Print Reading or GD&T? Check out more of our free GD&T resources here: download.gdandtbasics.com/youtube-free-gdt-resources #gdandt #straightne...
When to Use DMP Flatness
zhlédnutí 1KPřed 28 dny
In this Question Line video, Brandon explains the application of derived median plane (DMP) Flatness and discusses its frequent misuse and potential issues when used for stacking parts. He also provides an alternative for controlling flatness for stacking or symmetrical parts. Interested in learning more about Print Reading or GD&T? Check out more of our free GD&T resources here: download.gdand...
Flatness with Datum Targets
zhlédnutí 708Před měsícem
In this Question Line video, Jason answers questions regarding datum targets and applying flatness and profile of a surface. Interested in learning more about Print Reading or GD&T? Check out more of our free GD&T resources here: download.gdandtbasics.com/youtube-free-gdt-resources #datumtargets #flatness #profileofasurface
When to Use MMC and MMB
zhlédnutí 1,1KPřed měsícem
In this Question Line video, Jason explains when the Maximum Material Condition and the Maximum Material Boundary modifiers may be used. Interested in learning more about Print Reading or GD&T? Check out more of our free GD&T resources here: download.gdandtbasics.com/youtube-free-gdt-resources #gdandt #maximummaterialcondition #maximummaterialboundary
Position on Bolt Hole Diameters
zhlédnutí 1,3KPřed měsícem
In this Question Line video, Jason explains what the position callout is controlling when the feature control frame is attached to a hole within a bolt hole pattern. Interested in learning more about Print Reading or GD&T? Check out more of our free GD&T resources here: download.gdandtbasics.com/youtube-free-gdt-resources #gdandt #trueposition #featurecontrolframe
Reference Dimensions on True Position
zhlédnutí 1,2KPřed 2 měsíci
In this Question Line video, Jason walks through an assembly drawing to explain the scenario where a feature being controlled by position must have a reference size dimension rather than a tolerance on the size of the feature. Interested in learning more about Print Reading or GD&T? Check out more of our free GD&T resources here: download.gdandtbasics.com/youtube-free-gdt-resources #gdandt #tru...
Composite Profile Control
zhlédnutí 1,3KPřed 2 měsíci
In this Question Line video, Jason discusses a composite feature control frame controlling profile tolerance. He walks through through the user submitted examples to explain the controls of each frame. Interested in learning more about Print Reading or GD&T? Check out more of our free GD&T resources here: download.gdandtbasics.com/youtube-free-gdt-resources #gdandt #compositetolerance #profilet...
Radial Hole Pattern as a Datum Feature
zhlédnutí 1,4KPřed 2 měsíci
In this Question Line video, Jason responds to a question regarding radial hole patterns as datum features. He discusses how to set up the datum reference frame, how the datum reference frame controls degrees of freedom, and how to apply the Maximum Material Boundary. Interested in learning more about Print Reading or GD&T? Check out more of our free GD&T resources here: download.gdandtbasics.c...
Cylindricity Measurements
zhlédnutí 1KPřed 2 měsíci
In this Question Line video, Jason answers the following question submitted by a user through our new GD&T Question submission page: “I have a question regarding cylindricity. If we’re measuring the ID of a bore (and let’s assume the entire length of the bore is straight) … And I measure .3750 ID at the top of the bore, and .3748 ID at the bottom of the bore… what would the cylindricity value b...
Checking Circularity with Digital Equipment
zhlédnutí 1KPřed 3 měsíci
In this Question Line video, Jason gives a high-level overview of how polar probes and TIR checkers are used to inspect circularity or cylindricity. Interested in learning more about Print Reading or GD&T? Check out more of our free GD&T resources here: download.gdandtbasics.com/youtube-free-gdt-resources #gdandtinspection #circularity #cylindricity
Radial True Position with Composite Tolerance
zhlédnutí 1,4KPřed 3 měsíci
Frequently, when composite position is called out on a pattern of holes, the holes are on a flat surface and the axes of the holes are parallel to each other. But what if the axes of the holes are not parallel, as in the case of a pattern of holes on a cylinder? In this video, Jason explains how to control radial position with composite tolerance. Interested in learning more about Print Reading...
How to Inspect True Position at an Angle
zhlédnutí 2,1KPřed 3 měsíci
Typically, when a hole is being controlled with position, the primary datum is often the surface that the hole originates from and the secondary and tertiary datums are perpendicular or parallel to the primary datum. However, this is not always the case. In this video, Jason walks through an example drawing to show us how to inspect a hole that is at an angle with respect to the primary datum. ...
True Position and Bidirectional Control
zhlédnutí 1,1KPřed 4 měsíci
The position symbol is one of the most useful symbols in GD&T because it creates a diametric tolerance zone that more closely aligns with the functional intent of a feature. But did you realize that you can use the position control to allow more tolerance in one direction and less in another? In this video, Jason explains how to achieve bidirectional position control through the use of a Multip...
Measuring Runout and Circularity with V-Blocks
zhlédnutí 2,1KPřed 4 měsíci
V-Blocks are popular tools used during many types of manual inspections. However, they come with a unique pitfall that can impact the accuracy of measurements. In this video, Jason walks through the potential issues associated with using V-Blocks and how they can affect measurements of circularity and runout. Interested in learning more about Print Reading or GD&T? Check out more of our free GD...
Common Errors in GD&T Drawings: Incorrect Usage of the MMC Modifier
zhlédnutí 1,3KPřed 5 měsíci
Common Errors in GD&T Drawings: Incorrect Usage of the MMC Modifier
Common Errors in GD&T Drawings: Misuse of the Symmetry Symbol
zhlédnutí 1,1KPřed 5 měsíci
Common Errors in GD&T Drawings: Misuse of the Symmetry Symbol
Common Errors in GD&T Drawings: Mistakes in Defining Features
zhlédnutí 2,2KPřed 6 měsíci
Common Errors in GD&T Drawings: Mistakes in Defining Features
Common Errors in GD&T Drawings: Neglecting to Reference the GD&T Standard
zhlédnutí 1,7KPřed 6 měsíci
Common Errors in GD&T Drawings: Neglecting to Reference the GD&T Standard
GD&T Position vs. Coordinate Dimensions
zhlédnutí 10KPřed 9 měsíci
GD&T Position vs. Coordinate Dimensions
Inner and Outer Diameter Datum Features
zhlédnutí 1,7KPřed 10 měsíci
Inner and Outer Diameter Datum Features
Metric vs Inch Dimensions and Tolerances
zhlédnutí 1,1KPřed 10 měsíci
Metric vs Inch Dimensions and Tolerances
Datums, Datum Features, and Datum Simulators - Oh My!
zhlédnutí 6KPřed rokem
Datums, Datum Features, and Datum Simulators - Oh My!
I'd like to throw in my two cents in the hope that someone reads it and offers a counter opinion. I asked this same question in the GD&T Basics Inspection course and I agree that in an ideal world, anytime the UAME or local size reports out of tolerance, then the part should be rejected. But in my (limited) CMM experience, the UAME and local size rarely report within tolerance on a CMM when dealing with a tolerance that tight unless you have an analog scanning probe or take an extremely dense number of hits. And I'm talking like a point every couple of millimeters (who has time for that?). And even then, it can sometimes report slightly out of tolerance. I'm sure it has something to do with the math involved, which is beyond my knowledge. I've come across this more times than I can count when measuring drill holes for example where the UAME reports too small, yet the plug gauge always fits. But we don't have functional gauges for every single feature that we machine. Sure we have bore gauges and micrometers, but those just give a two point dimension. So I have no other choice but to rely on the average size (or least squares in CMM terms). It's also a lot more repeatable. Do I like it? No, I hate it. But realistically, if I were to fail every part where the UAME or the local size reports out of tolerance on the CMM, then I'd be rejecting about 80% of the parts that we make. And that doesn't help me, the company, or the customer. Again, I want to stress that I get much better results with an analog scanning probe vs taking hit points, but even that has its limits and not everyone has one of those. That also comes with other things that need to be taken into consideration, like using the correct filter for instance. But that's another topic entirely. So in my view, when dealing with tolerances as tight as the one in the video, the average size is often a necessary evil when the UAME or the local size reports out of tolerance. If anyone else experiences the same thing or has a different view entirely, please chime in because I'm still relatively new myself.
I put GD&T on my drawings to better define my parts and give the machinists more tolerance. But the parts are always quoted more expensive because they have to have more experienced technicians interpret my drawing and they say it requires a CMM inspection now. How would you respond to this?
Thanks, How to define tolerances for different surfaces on part? For example we have Bumper and we want to define tolerances on this part on different points (X,Y,Z) How we calculate? ❤❤❤❤❤❤❤❤
I'm designing components for high volume manufacturing (>100,000 pcs/y), so we have to rely on process capability for quality assurance. What are your thoughts on the use of MMC/MMB or envelope, in combination with process capability? Is it feasible or not?
its larger the hole smaller the material condition .
Excellent explanation
I've learned more from these videos than what I learned from college. Thank you!
(1:52) Can you use the MMC modifier and still ensure a minimum wall thickness? Yes, you can by reducing the Position Tolerance = $$!!.
So it means, I will add bonus tolerance to position tolerance(0.05 mm) , after datum B and and C size measuring. For example if datum B size is 25 mm I will add 0.05 mm. If datum C size is 30 mm, I will add 0.1 mm. I measure feature itself as 10 mm, I will add 0.1 mm. In final condition it has 0.05 + 0.05 + 0.1 + 0.1 = 0.3 mm position tolerance. Is it correct?
This is such a helpful video. I refer to it regularly! Thank you for posting it.
Can we use one of the axis of the hole as priamry datum, and apply parallelism to the other axis of the hole respect to the primary datum? If yes, only primary datum wouldn't be enough to control all six freedom, how should we pick the secondary datum or even a tertiary datum needed?
Yes you absolutely could use one hole as a primary datum feature and control the other hole with parallelism with respect to datum A. In this case since we are using parallelism, we have controlled 2 Translations and 2 Rotations. So you are indeed correct that we have not controlled all 6 DOF however, for parallelism we are only concerned with orientation of the axis to the other axis, and NOT translation and NOT rotation about the datum axis. So that would be perfectly fine to only reference datum A in this scenario if youre ONLY concerned with orientation.
@@Gdandtbasics Thanks for the feedback. What if we still concern with all the three rotational movements between the two axis, and wanted to use the parallelism to control, is that legal based on ASME? I take your picture for example but the two holes become threaded holes in my case. Both two holes will be assembled with a hollowed clylindrical shaft valving , imagine we have a clylindrical filling gun to fill these two shaft valving one by one, during the filling we must keep the parts stay flat (means not clockwise or counterclockwise movement allowed) and also need enough room for the filling gun so it will not interfere with the shaft valvings. Is it legal to use parallelism to control with, use one of axis as primary datum A(have controled 2 Translations and 2 Rotations) , the bottom surface as datum B to control the third rotation? Or any disadvantages for indroducing the datum B?
Very Good video on explaining Profile Tolerance. I enjoyed the clear and informative content; nothing extra; straight to the point.
1) I‘m afraid, there is no reale feature function according to „flatness 0.005 M“ at datum A. 2) If this plate is srewed or stacked, a complete differend specification is required (please see: The plate can be screwed from two different sides). 2) If someone wants to use „flatness 0.005 M“ for whatever reason, then it is easier to write 1.000 -0.02 +0.025 without additional flatness. Kepp it simple! If a fit is required, it‘s a very good idea to keep in mind the gauge, which explanes the simulation of the missing contact partner. If you work with 3D-CAD it’s very helpful to work with assembly constrains to explane contacts. If you create a nominal design where all features with fit function are at MMS, all parts in your assembly are representing the go gauge against each other! A specification is only necessary to control maximum of fit clearance. Unfortunately with the modell of GD&T (or IS0 GPS) a specification uncertainty against nature function appears. Should we start to speak about this issue?
I’ll save some people time. This is not a software tutorial for programming a CMM. It’s only using a CMM for measurements.
According to our records, the BTC transaction has been successfully received.
Yes, it is obvious that when a datum plane is define by 3 datum target points, flatness is meaningless because they will always form a perfect plane. however, when the datum targets are surfaces instead, with meaningful areas, or you have more than 3 datum target points, you will have a flatness mismatch between a simulator and the real part. Is there a way to impose a restriction to the deviation of those multiple points or surfaces from a perfect plane, without qualifying the entire surface? (for example, you have four contact points, and you want to make sure that with any 3 points in contact, the fourth point will never have a larger gap than a certain value)
That's a great question, Datum target points, regardless of how many or where they are, will not ever "control" any aspect of size, location, orientation, or form. You can however still apply a form control to the entire surface, or portions of that surface as you mentioned and we show in this example. THat would be the only way to control specific form deviations in this scenario.
If datum targets are applied, how to simulate datums during inspection via CMM. Should fixture must be used? Is there any option by CMM software or programing?
Usually a jig. Most CMMs I've seen do not have datum target simulators. Maybe more high end ones do ... Or 3D scan measurement software, like GOM Inspect, do have ways to simulate datum targets.
Thanks
Very well explained!
a Vivid video presentation👍
Thanks a lot. very useful training. god bless you.
May be datums B and C are equal: A | (B-C) MMC
The 8 holes would need to be a simultaneous requirement output per ASME 14.5 right? Would software treat them more as a single pattern instead of separate features if output as a SIM. REQT.? Would the results really be any different?
The 8 holes would definitely meet the simultaneous requirements applied by default via ASME Y14.5. Ideally the software treats anything with the same datum structure as SIM REQ by default but this is not always the case for all software.
You didn’t talk about the modifier. How can you have a MMC without a tolerance of size?
The size has already been insepected during the machinging process, so don't need to recheck it for the wellding assembly , just use the data recorded from the machinging.
@@user-nh7gk1bw7d Which would mean that the MMC modifier should not be included in the feature control frame.
@@EricIrwin A tolerance of size for the hole already included during the machining process, and considering the size of the hole will not change after welding process.For simplicity and save money (double check will cost extra money), use a reference size is a good choice for this purpose, that doesn't mean the size have no tolerance though. On the other hand, when MMC modifier is applied for the welding asselmbly, we can use a clylinder pin gauge to check the position tolerance.
@@user-nh7gk1bw7d I think the error in your logic is that the datum reference frame has changed from the part to the weldment. I still don’t believe it would be good practice to apply the material condition from the part to the weldment. I agree that you could get an answer as you have described but I don’t believe the answer is the correct interpretation of the applied tolerances.
@@EricIrwin The tolerance is determined by the ability of manufactruing process, it dosen't matter if it changed from one process to anoter process unless the size of the feature will be affected by the subsequent process
Thanks a lot!
Hey thanks for this explanation! Question 8:23: Is there a difference for the manufactured part to inspect if you: 1) Have Datum A on the surface (like in the video), or if you put: 2) Datum A onto the flatness callout itself, and not on the surface? Does it matter or is it actually the same? Thanks :)
Great question, we get that one alot! The interpretation is the same regardless if you attach the datum feature symbol directly to the FCF or the surface.
So professional! not only about the GD&T, but also about the thread measurement
What is repeatable measurement
Is there a way to determine the direction of the probe such that the surface is normal to the direction of the probe at point of contact?
Perfect, thank you.
I finally have a reason to use my salad bowl.
Wondering as you the delete datum "C", at 3:20, can we delete datum "B" from the 2nd line of control frame of Example 2 (for tol. 0.1)? To allow rotation but with in the area for tol. 0.5 ?
Yes you are correct you can get rid of B from the lower frames to allow more rotational freedom within the larger tolerance zone from the upper frame.
As far as I know, the material conditions might be applied only on feature of size. What should be the MMC value of a point, which is an intersectoin of five axes? Are you going to add the MMC of every cylinder? I think - no. Are you going to find the MAX MMC of some cylinder an use it? Or is it the MIN value? Think it is not correct either. Also, cannot think of any real world problem, that will require such dimensioning schema. Of course, if it is going to be a check gauge - then, yes, it might work. But, don't think the CMM will be able to evaluate this.
Thank you so much.
Thank you for answering my questions. This video is clear. Now I am more confident to discuss with my colleagues. Super appreciated.👍👍👍
Very interesting video. 2 questions here, which I think were not clear: 1. While in the nominal case, those 5 cylinders converge to a point, in reality they will not. The axes will kind of miss each other in 3D space so how could a single point be determined? 2. Regarding the orientation in plane (that fixes the rotation of the pattern of 4 holes), you mentioned that you can choose whatever you want. But again, since on the actual part, those 5 cylinders will not have the nominal angles, is the reference orientation considered as an average between the orientation of those 5 cylinders? Otherwise, choosing just one would imply that it is a difference to which one you choose, since the will have different deviations to the orientation. Thank you very much!
I would think the CMM can do the mathematical calculations for the 5 cylinders converge to a point. Every two axis will converge to a point, if we can find a a circle that just big enough to accommodate all the points converged from those 5 cylinders, that center of the circle I would believe be the determined zero point
That’s what tolerances and bonus material are for. Nothing is ever perfect, so the same rules apply here.
@@kw2519 No sure this is it. The only "approximation", if you will, is with regards to the point cloud filtration/association, which is the way to approximate the real geometry in the best way. Moving forward from there, all elements are perfect geometrical elements that have a precise mathematical description. There needs to be a precise way to calculate all of these median points, axis intersections etc.
@@AlexLapugean ya and that’s usually defined by the way your point cloud is setup. You can take two measurements of 3 points and get a very rough approximation. Or you could sweep the bore at 10 depths and get a much better result. I’m just saying it all comes down to how the parts dimensioned. As he said, we are the interpreters.
These are great questions. You are absolutely correct in saying that the axis of the holes will never converge on a single point. In order to get the center point of the pattern of holes as a datum we need to simulate the datum. And for a pattern of holes, that simulator (physical or digital with a cmm) is 5 cylinders located at true positions (ie converging on a single point) and those theoretical cylinders will expand simultaneously until the pattern of tangible holes "settle" out on the radial high points of all 5 holes simultaneously. This is simulation at RMB. However, a much more practical real world gage would be if datum B were called out at MMB, this would allow us to have stationary pins that dont need to expand. And the part is allowed to "shift" on these perfectly located pins, resulting in datum shift.
I started at SDSU 8 years ago now as an ME and never heard about this until now. Gd&T was just briefly mentioned in my cad class and that was it.
Air gage, what is that? Not ever heard about that.
Using the hole positions as Datum B does bother me. It feels to me that this part will ride on a shaft, and it's most important to ensure the parts features are centered on the shaft. Therefore I'd prefer to see the ID 1.000 +/- .001 to be Datum B. Subsequently the bolt circle diameter and hole positions would be slaved to the bore. Trying to measure the position of the 1.500" boss based on the position of holes that themselves may have up to .0025" deviation seems ambiguous.
That's a great analysis of the decision making process that a designer must understand when selecting their datums for feature control frames. The functional intent of the part should dictate the select of datum features. With out seeing the rest of the assembly in this example we are only operating on assumptions of the final assembly criteria. If the center bore was a clearance bore then it would likely make more sense to use the pattern of holes as a secondary.
Why do people ask these obvious questions? You want to know the cylintricity, you MEASURE CYLINDRICITY. You can't just measure something else and then just assume things. That is the first step to bad engineering, where components end up being functional by chance or overengineering, not by virtue of good design and control.
Thanks!
This is very informative thank you. 👏
A point can't be a secondari datum I don't see it over restir same F.D. more Tham ones it error
Hi as a teacher of Mechanical Engineering, I find your videos a great resource and encourage my students to watch them. Thanks
At 9:58, shouldn't the original point(Zero) be the intersection point between datum A and datumC. What you want to express is that we can add X value depends on the Pin the inspector will be choose, is that correct?
abseloutly amazing
Your video mentions a polar probe or a TIR checker. It'd be cool if you included slightly more details on those types of tests to educate people. Searching either of those didn't come up with a ton of useful links. I assume we're talking about a system that checks with multiple sensors to monitor for the lift of the center axis such as czcams.com/video/fIbt7lBTL2s/video.html or a CMM setup that can plot the polar graph (either cause the part can lay flat normal to it's rotation axis or you have the part between centers or some other method.
Thanks for the comment, I love this idea! ill put it on the short list of ideas to make for a video. Stay tuned!
I ask this question to geotol pro if I can use runout as datum and the answer is no. Runout should be reference to axis. And runout callout cannot be attach to dimension. Conclusion. They should overhaul gd&t.
The key difference here in this example is the fact that the runouts for datum features A and B are in reference to datum axis "A-B" which is a completely different axis then datum axis A or datum axis B, which is completely legal to see/inspect and in fact a very common design.
The inclusion of runout callout for datum A and B, with a diameter tolerance of 1.5 +.000 -.002, is unnecessary since the size tolerance is smaller than the runout tolerance. This incorrect example contributes to confusion among beginners and diminishes the widespread use of GD&T.
Thanks for the repy! This is actually a very common dimensioning scheme, but i can understand the confusion. Runout is controlling location of the axis of the feature, in addition to its form. And since the the datum axis is created from both datum feature A and B, it is NOT in reference to the same axis as the feature we are controlling. Thus the size tolerance can hold a tighter form of the feature, while the runout will allow a slightly looser coaxiality error. I hope this helps clarify things for you!
What would be the difference if you used a composite position tolerance, instead of a multiple single segment? And is there an equivalent to composite tolerance in GPS? Thanks!
This is a tricky concept to explain quickly however from a high level, composite lower frames ONLY control orientations of the pattern and not locations with respect to the datums. Where MSS will control locations. There are some configurations of upper and lower frames where both the interpretation of MSS vs composite would be the same. And to the best of my knowledge there is nothing in the GPS that is similar to the Composite control. Thanks for the question!
@@Gdandtbasics thank you for the explanation.