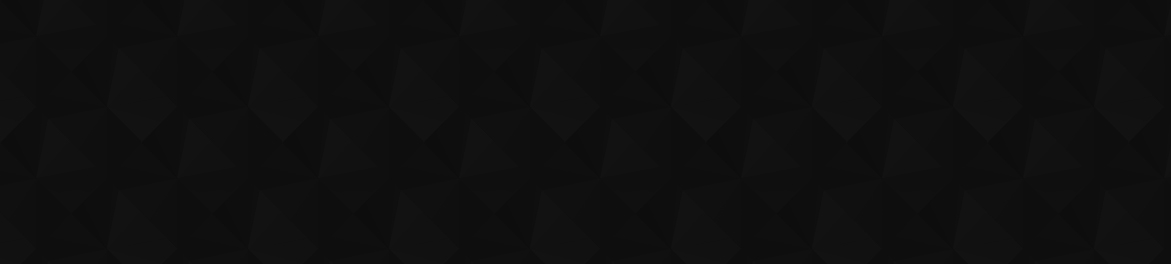
- 21
- 538 013
WildWillyRobots
Denmark
Registrace 13. 04. 2007
Wild Willy 2024 Robot Reveal
A short video about my new robot showing some of the internals.
Also a little about some of the considerations for the design of the gripper.
The competition is April 3rd and 4th 2024. Look at the website robocup.dtu.dk/ for more details.
Also a little about some of the considerations for the design of the gripper.
The competition is April 3rd and 4th 2024. Look at the website robocup.dtu.dk/ for more details.
zhlédnutí: 1 523
Video
Differential Swerve Drive Robot Assembly
zhlédnutí 6KPřed 9 měsíci
CAD drawing and parts list can be found at www.printables.com/model/599137-swerve-drive-robot
Meet Wild Willy: A Unique Robot in DTU RoboCup 2023
zhlédnutí 6KPřed rokem
My omnidirectional swerve drive robot, that can drive in any direction. Used in DTU Robocup 2023. Website of the Competition robocup.dtu.dk The Final of the Competition: czcams.com/video/rvt03q2qdPU/video.html
Differential Swerve Drive
zhlédnutí 376KPřed rokem
My take on a differential swerve drive. An omnidirectional wheel with stationary motors, that can drive in any direction. I plan to use 3 of these wheels in my next autonomous robot as an alternative to traditional omni or mecanum wheels. The model for the 3d printed parts and a list of other items can be found at www.printables.com/model/300105-differential-swerve-drive 00:00 Intro 01:10 Assem...
Stair Climbing Rover - Outdoor Test
zhlédnutí 20KPřed 2 lety
3d printed rocker-bogie rover driving around outdoors in various modes and terrains. The model files can be found here: www.printables.com/model/194299-stair-climbing-rover
Stair Climbing Rover Assembly
zhlédnutí 47KPřed 2 lety
Assembly instructions for 3d printed rocker-bogie rover. The model files can be found here: www.printables.com/model/194299-stair-climbing-rover
DTU RoboCup 2022 - Wild Willy - First run with onboard camera overlay
zhlédnutí 14KPřed 2 lety
Data from the robot onboard camera is shown as an overlay. The red bar at the bottom shows the detected line used for the line following. The camera operates at 10fps 320x240. The robot is built on a rocker-bogie design, making stair climbing quite easy. Unfortunately the robot didn't go up the stairs this year because the wooden floor was too slippery. All parts of the robot rover are 3d print...
Robot Driving on Stairs
zhlédnutí 46KPřed 2 lety
First robot in the DTU RoboCup competition to go up the stairs. The 3d printed rover is build on a rocker-bogie design, making this quite easy. It is using a Raspberry Pi camera to see the obstacles, and a Raspberry Pi for the calculations. All 6 wheels are actively driven and can turn independent on each other. All parts of the robot are 3d printed. The model can be found here: www.printables....
DTU RoboCup 2015 - Wild Willy - First run
zhlédnutí 702Před 9 lety
First run in the final - 19 points.
DTU RoboCup 2014 - Wild Willy - Second run
zhlédnutí 4,9KPřed 10 lety
Second run in the final - 17 points.
DTU RoboCup 2013 - Wild Willy - First run
zhlédnutí 440Před 10 lety
First run in the final - 13 points.
DTU RoboCup 2012 - Wild Willy - Second run
zhlédnutí 319Před 12 lety
Second run in the final - 18 points.
DTU RoboCup 2010 - Wild Willy - Second run
zhlédnutí 143Před 13 lety
Second run in the final. 3 points
DTU RoboCup 2010 - Wild Willy - First run
zhlédnutí 162Před 13 lety
First run in the final. 13 points.
DTU RoboCup 2007 - Wild Willy SE - Second run
zhlédnutí 5KPřed 17 lety
DTU RoboCup 2007 - Wild Willy SE - Second run
DTU RoboCup 2007 - Wild Willy SE - First run
zhlédnutí 8KPřed 17 lety
DTU RoboCup 2007 - Wild Willy SE - First run
what kind of slotted bearings did you use for the ring gears
I have some question how you know the direction of the wheel when you only use 1 hall sensor
The encoders of the motors are used to calculate the angle of the drive wheel and the direction of the module. Because the direction of the module is random, when I power up the robot, I turn the direction until the hall sensor is trigged by the magnet. So the hall sensor is only used for zeroing the direction. After this only the encoders of the motors are used. Maybe I should create a video explaining this in detail.
If you look very closely at the wheel when I start the robot in this video, czcams.com/video/3W0p16vsgqA/video.html , you can see all the wheels changing direction, when they search for the zero position.
All that for a drop of blood ?
Where can i find your power screwdriver
It is the Wowstick 1F
Project without demo is waste of time
End of video should link to demonstrations. If not, then here are a video driving autonomously czcams.com/video/9Od0E53R8PE/video.html, and another driving remote controlled czcams.com/video/90HxqwZaWRA/video.html
I wish you good luck un the competition, and.more recognition for your swivel drive.
It didn't go exactly as planned in the competition, because I made a stupid mistake in the programming. But I did get to use the arm of the robot for solving obstacle with the qr code boxes. It can see it in action here: czcams.com/video/Al4ebXraGM8/video.html
Unrealistically long stairs tho
DID you use 3d printer to print the parts?
Yes, all the plastic parts are 3d-printet. There is a link to the design files in the description.
Great design and execution. Your robot is very sleek and the swerve drive is great! Very inspiring!
Thank you. I'm quite happy of the design myself, and the newest iteration with bigger motors works great.
Great video and robot! Really nice talking to you at the competition!
Nice to meet you there. I hope we will see more teams from Odense next year.
Hi this a beautiful design and as a college student it makes me feel like trying it out. So can you please explain or give us a circuit diagram of the electronics connection part sir. its a kind request please sir.
My electronics setup is a bit complicated, because I use it for autonomous driving. If you just want to remote control it, it can be done much simpler, but I don't have much experience with that. I would suggest, that you try to contact others, that have built it. Look at the comments section at Printables here: www.printables.com/model/194299-stair-climbing-rover/comments There is also a link to my custom PCB for the electronics, but again, that is most likely overkill for remote control.
You have been my inspiration for quite some time as I'm dead set on using the independent wheel steering like what you have. You continue to be my unofficial teacher. Thanks so much for sharing your designs and plans. Kudos to you!
I forgot to mention that I also love your implementation of the magnets for the covers. You rock!
Yeah, the magnets are quite nice. I will share the complete design at some point, but I need to clean it up a bit first.
Your Fanboy here. Absolutely stunning. Those colour combos and thoughtfulness of design is extravagant. Waiting to see it roll on the dtu competition floor.
I'm not fully satisfied with the colors, but had a bunch of the green filament, so ended up using that😀. Still a lot of work to make it actually run.
Have you tried ros2 on your robots?
No, it is just running my own software. I have looked at bit at ros, but it takes some time to understand how it works, and I'm not sure I have the time to invest in that.
The engineering on that looks amazing! The old one looked pretty cool when moving around, cant wait to see this one (hopefully) nail every obstacle.
Don't get your hopes too high. Currently I'm struggling just getting the cameras to work reliably.
I hope you will get it sorted out! On your old robot the camera seemed to work as intended, but maybe it only had the rgb camera?
Problem was a bad connection in the cable on the RGB camera. I fixed it by soldering the usb cable directly to the camera board. I had the TOF sensor on the blue robot, but never used it because of a driver issue. The sensor was quite new at that time. This year I got the sensor working on a Pi4, but in the end decided to use Pi5 on the robot. And then I had the same problem with missing driver support for Pi5. Arducam released support for Pi5 a few days go, but I didn't have the time to implement it.
Great news! Did you manage to get a run in too? I only do dumb industrial robots which just performs the same actions over and over. At some point I would like to add some kind of vision to them too, but so far I haven't found anything (at a not too crazy price) which can handle what I need.
Yeah, I did run today in the competition, but the result was not great. I made stupid mistake of merging to programs for different parts of the track into one, but never actually tested that it was working. But I did solve the qr code box challenge, so the gripper in the video worked decently. I work with industrial robots and vision in my day time job, so I know that part very well😀
amazing ingenuity and evolution from last years already amazing robot! Thank you for sharing
Thank you. It is mostly an evolution of the hardware, but so far it has not run that much, so I'm not sure it is better.
That's freaking awesome.... Wish I was there to beat you :) (Because I would bring great software and some random slapped together hardware)
Yeah, it has been a long time since we have seen anyone do a Crazy Ivan
@@wildwillyrobots Maybe next year!
We definitely need someone who can write decent software in the competition😀
So glad it turned around and went back up. I was prepared for disappointment, but I was not disappointed. My friends would love a vacuum robot that could handle stairs, lol.
These 100mm steps are not a problem, but I don't think it will be vacuuming normal stairs anytime soon.
why not just use the original design with slip rings?
Slip rings are a bit expensive when you need 6 of them. And also, I'm not sure they can transfer the encoder signals from the motors without adding noise.
@@wildwillyrobots guess you have a point there on cost, idk about the communication, it's been a minute since I seen this.
I was wondering, how did you design the reverse bevel gear? Or if there is a better name for it?
The bevel gear was modeled in Onshape using a feature script called "Bevel Gear Pair". It was then combined with a normal gear made using the "Spur Gear" feature script.
@@wildwillyrobots Could you possibly make a CAD tutorial on making one? Also if you know is there a way to do this in fusion360?
@@bio.s2903In Onshape, once you have selected the feature script, you get a dialog, where you put in the dimensions and the gear ratio, and then the gear is automatically generated. I have never used Fusion360, but assume it can run custom scripts to generate complex parts, just like Onshape.
@wildwillyrobots Great work! and Thanks for sharing. May I ask what control strategy and components you are using to control the motor wheels?
In this video it is remote controlled. I have a Raspberry Pi that receives commands from the remote. It then calculates the required speed and angular direction for each of the 6 wheels, and send those values to a custom build motor driver, that turn does the low level control loop for controlling the motors. This is a somewhat complicated setup, but that is because my primary use of the rover is to drive as an autonomous robot. For someone who just want to drive around with a remote, it can be done much simpler.
Such Amazing work!!! Love it!!!
Very nice design but no information
What kind of information do you need? There are more details in the link in the description.
Very small and shallow stairs.
Yeah, but still most small robots in the size of a robot vacuum cleaner will not be able to go up.
Brilliant design. However I think a simpler answer to your problem would have been to use a slip ring to pass the drive motor wires through the steering axis.
😊🎮🏎️
No 🎮 Fully autonomous🤖
its really great project can possible to provide part list, circuit diagram and coding stuff?
You can find most parts at www.printables.com/model/194299-stair-climbing-rover In the comments at Printables you can also find a link to the motor driver board schematic. I have not shared any code.
Thanks for sharing, how much does it cost to build one?
I am currently doing a group project about a gripper remote robot thst can climb stairs and turn, and cost of building the whole thing should be lesser than $120(AUD), size is 250 (mm) x 250(mm) . Can anyone provide any suggestions for this one?
Most expensive parts are 6x motors, 6x servos, motor driver board, Raspberry PI, battery, camera. Haven't calculated the exact price, but as it is shown in the video, I think somewhere in the range €250-350.
@@wildwillyrobots wow, that is crazy. Thanks for sharing, despite the price is a little bit out of budget to me, it looks pretty good.
Yeah, it is a bit expensive as you need 6 of everything.
@@wildwillyrobotsyeah... I can get that, I think we may need another plan for this haha
Impressive design!
A slip ring might help with the wires limiting rotation
Others have made the same suggestion, but they are a bit expensive. Also, I'm unsure if they can deliver a noise-free signal for the encoders. Regardless, I simply wanted to try something different.
This is insanely beautiful
Very Interesting 👍👍👍
Amazing - Thank You
I LOVE you
This is one of the best stair climber. Did the stairs are 17 cm ?
I think it can do about 15 cm without tipping over. If I remember correctly the the ones in the video is 10-12 cm
Do you have any plan to add Mic and speakers? Maybe a screen as well 😶🌫️😶🌫️
There is a Raspberry Pi inside, so it is possible. But not that useful for my application.
What brand wireless screwdriver are you using?
It is a Wowstick 1F+. It is struggling a bit the first time the bolt cuts the thread in the pastic.
I would like to know what size wheels you use.
Check out the description at Printables: www.printables.com/model/300105-differential-swerve-drive
Hey I want parts not whole modle can you share the link
You can download the individual parts on Printables. www.printables.com/model/194299-stair-climbing-rover/files
Hello can u tell me from where brought the remote and how you connected that
I have mostly used it for autonomous driving and not remote controlled. You can check the comments on Printables. There are some details about the electronics I used.
@@wildwillyrobots hey I have some query can you share your whatsapp number or insta id
😮😮😮😮😮😮😮😮
So great. I love this style of robot. Could you share the design of the swerve wheel.
It is mostly the design from this video czcams.com/video/TP8wQRZUuk4/video.html (link to model in description). Main difference is that the motors of the robot are horizontal and not vertical as in the video of the swerve module.
@@wildwillyrobots Thank you so much
The only thing cooler than mecanum wheels is: this thing
Did you publish the code?
No, but there is not much to it. Some speed controllers for the wheels and a little trigonometric calculations to find the angles or the servos.
Can this be developed for mobility units for people with disabilities who are looking for lightweight stair climbing, all terrain units.
You will need larger wheels to climb normal stairs. This means that you will only have one wheel on each step at a time, which I think will be a problem.
Hi, im a big fan of your robot designs and the algorithms. Is your code publicly available? I really would like to read it and understand the control mechanisms.
The code is currently a mess, so I haven't shared it. Also it has various dependencies, so it is a bit hard to get it running. But overall I have low level control on a Raspberry Pico, that controls the speed of the wheels and the servos. Then I have a higher level program, running on a Raspberry Pi 4. This makes the image analysis for detecting obstacles, and calculates the required speed and position of the wheels, which is then sent to the Pico.
@@wildwillyrobots is it just a simple feedback from vision that controls the motor velocities or you calculate the position data to drive the robot to the position
@@barknvar3902 Image analysis finds the line in the bottom of the image. Then a P-controller is used to calculate the steering direction. Is is just the error (deviation from center of image) times a constant. This gives a steering direction, and from this the speed and orientation of all wheels are calculated. So it is just a controller trying to keep the line in the center of the image.
Impressive evolution from the prototype differential swerve drive to Wildwilly… where the drive motors don't have to be spaced 180° apart.
Yes, the motors can be positioned freely around the large gear. In this version, I'm also using a bevel gear for the motors, so that they can be horizontal and not vertical as in the prototype.
@@wildwillyrobots Interesting - Thank you - I look forwards to the follow-up video.
Excellent work my friends!)🤩💥💯👍
I have been looking forward to your swerve drive ever since I first saw it, and this is a great run! Even more so that even with the mishap about the rear motor, it still moves very well. Amazed with how you designed your feedback loop so it will not make bizarre movements due to that different gear ratio. Hope to see your swerve drive in more things in the future!
Thank you. Actually the control is not that difficult, but more on that in the next video :-)
I neeeeed that video!@@wildwillyrobots
in 2023?
Not sure what you are asking?
@@wildwillyrobots i was there in dtu last month. i did not hear anything about it.
It was in the Library April 12 and 13.
@@wildwillyrobots are you working in DTU?
@@xinglinjiang4952 I'm a former student at DTU
Fantastic! Thanks for sharing your robot with us. I'd love to compete at the RoboCup some day.