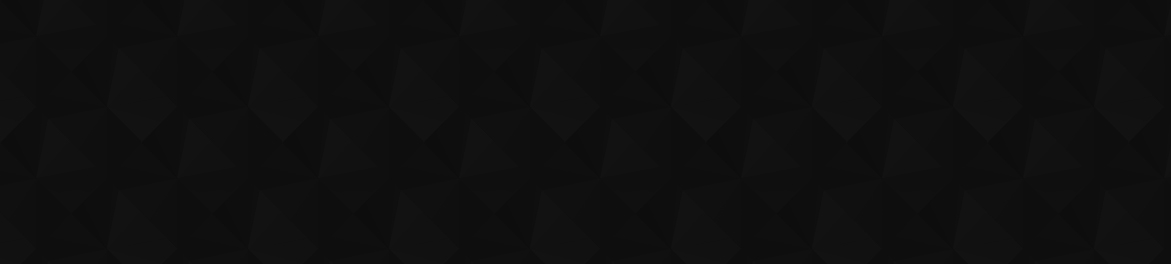
- 38
- 249 224
fkiQuality
United States
Registrace 16. 02. 2015
Here you will find the method to the madness and stop putting off fires for good.
My name is Francisco, and I work on improving the performance of all types of companies. My channel is all about learning a new way to look at your operations that will show you what really matters and take corrective or proactive steps. I integrate Lean, Six Sigma, and the Deming management methods.
So, if you want to make your operations more agile and sustainable, leaner and faster, subscribe to my channel right now.
If you are interested in Lean Six Sigma certification, email us at info@fkiquality.com
Don't miss this opportunity to join me and start your journey to operational excellence.
See you on the channel!
Francisco Pulgar-Vidal
My name is Francisco, and I work on improving the performance of all types of companies. My channel is all about learning a new way to look at your operations that will show you what really matters and take corrective or proactive steps. I integrate Lean, Six Sigma, and the Deming management methods.
So, if you want to make your operations more agile and sustainable, leaner and faster, subscribe to my channel right now.
If you are interested in Lean Six Sigma certification, email us at info@fkiquality.com
Don't miss this opportunity to join me and start your journey to operational excellence.
See you on the channel!
Francisco Pulgar-Vidal
Peru - Los Bancos de Oro
Francisco Pulgar-Vidal, proposes a human interpretation of the saying of the "gold bench" at the 130th anniversary celebrations of the Sociedad Geografica de Lima, February 22, 2018.
It is often said that Peru is like a blind man sitting on a gold bench who does not know and does not take advantage of the natural riches at hand.
Francisco suggests an alternative vision where the gold bench are the Peruvians themselves, who do not recognize, develop or take advantage of our own human wealth.
This is the main message of Dr. Javier Pulgar Vidal, Francisco's father, who dedicated his life to the study of natural resources and the development of Peruvians through the foundation of several universities and scientific institutes.
Francisco Pulgar-Vidal, propone una interpretación humana del "banco de oro" en las celebraciones del 130 aniversario de la Sociedad Geográfica de Lima, el 22 de febrero de 2018.
Se dice con frecuencia que el Perú es como un ciego sentado en un banco de oro que no sabe y no aprovecha las riquezas naturales a su alcance.
Francisco sugiere una visión alternativa donde el banco de oro somos los mismos peruanos, que no reconocemos, desarrollamos o aprovechamos nuestra propia riqueza humana.
Este es el mensaje principal del Dr. Javier Pulgar Vidal, padre de Francisco, quien dedicó su vida al estudio de los recursos naturales y al desarrollo de los peruanos a través de la fundación de varias universidades e institutos científicos.
#peru #lima #geografia #sostenibilidad #sustentabilidad #ochoregiones #education #universidad #recursos #recursosnaturales #riqueza #peruvian #peruano #perutravel #sociedad #geografica #pulgarvidal #javierpulgarvidal #amautadelperu #amauta
It is often said that Peru is like a blind man sitting on a gold bench who does not know and does not take advantage of the natural riches at hand.
Francisco suggests an alternative vision where the gold bench are the Peruvians themselves, who do not recognize, develop or take advantage of our own human wealth.
This is the main message of Dr. Javier Pulgar Vidal, Francisco's father, who dedicated his life to the study of natural resources and the development of Peruvians through the foundation of several universities and scientific institutes.
Francisco Pulgar-Vidal, propone una interpretación humana del "banco de oro" en las celebraciones del 130 aniversario de la Sociedad Geográfica de Lima, el 22 de febrero de 2018.
Se dice con frecuencia que el Perú es como un ciego sentado en un banco de oro que no sabe y no aprovecha las riquezas naturales a su alcance.
Francisco sugiere una visión alternativa donde el banco de oro somos los mismos peruanos, que no reconocemos, desarrollamos o aprovechamos nuestra propia riqueza humana.
Este es el mensaje principal del Dr. Javier Pulgar Vidal, padre de Francisco, quien dedicó su vida al estudio de los recursos naturales y al desarrollo de los peruanos a través de la fundación de varias universidades e institutos científicos.
#peru #lima #geografia #sostenibilidad #sustentabilidad #ochoregiones #education #universidad #recursos #recursosnaturales #riqueza #peruvian #peruano #perutravel #sociedad #geografica #pulgarvidal #javierpulgarvidal #amautadelperu #amauta
zhlédnutí: 469
Video
DPMO Method for Process Capability | Green Belt 2.0® Lean Six Sigma | fkiQuality HD
zhlédnutí 10KPřed 4 lety
The DPMO method to calculate the capability of a process is useful when there is more than one aspect of quality being measured. With two or more quality aspects, the Sigma method (czcams.com/video/vtnNz3cckQs/video.html) does not work. Measure only quality characteristics that matter, don't go overboard, this is why they are called "critical to quality" or CTQs. The table used in this video is...
Sigma Method for Process Capability | Green Belt 2.0® Lean Six Sigma | fkiQuality HD
zhlédnutí 3,5KPřed 4 lety
The Sigma method is used to measure how capable or "satisfying" a process is. Sigma tables display sigma values and their associated yield (in percentage) and defective proportion (in defects per million opportunities - DPMO). The table used in this video is derived from the standard Normal distribution N(0,1) and is free of the arbitrary 1.5 sigma adjustment featured in many books. The 1.5 sig...
Six Sigma | Real-world Effects of Low Quality | Green Belt 2.0® Lean Six Sigma | fkiQuality HD
zhlédnutí 441Před 4 lety
The quality of an entire process can be measured by its yield, which is calculated as the ratio of good results to the totality of results. That is, yield = number of good results / total number of results. The concept and calculation are the same for each individual process step. For this reason, it is easy to think that the quality of the entire process would be the same as that of the indivi...
LEAN work is fast work | Green Belt 2.0® Lean Six Sigma | fkiQuality HD
zhlédnutí 728Před 5 lety
One key Lean outcome is that the flow of work accelerates. Watch this healthcare example which takes less time to deliver better care. Lean achieves this by focusing more on the flow of work and its speed than on maximizing the use of equipment and personnel. Another key result is a higher sense of accomplishment for the employees, who feel that they are actually having an impact, which is a ke...
Six Sigma | The x-bar R Control Chart | Green Belt 2.0® Lean Six Sigma | fkiQuality HD
zhlédnutí 2,1KPřed 5 lety
Use the x-bar R control chart to monitor and improve processes where data can be collected at about the same time and/or under similar conditions. The chart will display the variation between the sets of data, called subgroups, in the x-bar section and between the individual observations in the R section. This way, the x-bar section shows how the process being measure changes day after day, whi...
Six Sigma | Mis-managing with Numbers | Green Belt 2.0® Lean Six Sigma | fkiQuality HD
zhlédnutí 869Před 5 lety
We always compare pairs of numbers! This month's results to last month's, this year's to last year's, ... how much does this tell you? Then, how do you try to explain every change up or down ... or even that there was no change? There's a big difference between describing numbers and understanding the operations that produced them. Discover the control chart to see results in time sequence and ...
LEAN | The Kaizen Staircase | Green Belt 2.0® Lean Six Sigma | fkiQuality HD
zhlédnutí 1,1KPřed 5 lety
Masaaki Imai, the man who popularized the concept of "kaizen" describes how real progress is achieved not only by implementing large-scale, disruptive change, but also small, daily changes throughout the entire company.
LEAN | 3 Nevers for a Perfect Process | Green Belt 2.0® Lean Six Sigma | fkiQuality HD
zhlédnutí 696Před 5 lety
A perfect process is one that is continually improving itself, so it's not a destination but a journey worth starting. (Timestamps below) 3 key behaviors are key to achieve a process that produces near-perfect outcomes based on continual process improvement: 1) Never make a defect 2) Never pass a defect 3) Never accept a defect These behaviors help avoid the risk of unawareness of poor quality ...
Six Sigma | Project Management & Lean Six Sigma Go Together | Green Belt 2.0® | fkiQuality HD
zhlédnutí 8KPřed 5 lety
2 similarities and 2 differences between PM and LSS show us what to learn from these complementary methods. Timestamps: 0:39 - First Similarity Between PM & LSS - Complementary 1:04 - PM & LSS are Complementary Slide 1:38 - Second Similarity Between PM & LSS - More Effective Together 1:48 - First PM Concept - LSS Projects Structured in Stages 3:26 - Second PM Concept - LSS Projects launched by ...
Green Belt workshop - Lean Six Sigma
zhlédnutí 148Před 5 lety
Our Green Belt course is the best - here is why you need it: * To quit fire-fighting and solve your operational challenges. * To find and fix the changes that really hurt your operations. * To go beyond quick fixes and apply “a method to the madness”. * To learn to attack the non-value-added tasks accepted “as part of the job”. * To make your teams’ best effort really effective. * To stop damag...
Six Sigma | Never build a control chart this way! | Green Belt 2.0® Lean Six Sigma | fkiQuality HD
zhlédnutí 2,9KPřed 6 lety
Avoid this common mistake: placing control limits at 3 standard deviations from the average. Instead, control limits are calculated correctly from the variation within the sample or from one observation to the next. (x-mR and x-bar-R charts) Based on a paper by Jean-Marie Gogue, French Deming Association.
A Course Fit for All Organizations | Green Belt 2.0® Lean Six Sigma | fkiQuality HD
zhlédnutí 50Před 6 lety
Process improvement with emphasis on cultural change. Solve problems once. Sustain excellence every day. Become Lean and efficient. Education by fkiQuality Contact us at info@fkiquality.com
See and Solve Problems Differently | Green Belt 2.0® Lean Six Sigma | fkiQuality HD
zhlédnutí 74Před 6 lety
fkiQuality courses will let you see problems differently and solve them better. Turn your teams into problem-solvers. Become Lean and efficient. Education by fkiQuality Contact us at info@fkiquality.com
Six Sigma | ZERO Defects 1: You don't want this | Green Belt 2.0® Lean Six Sigma | fkiQuality HD
zhlédnutí 2,5KPřed 6 lety
Fat-free. No-lead. Free-range. Zero defects is a negotiated value dependent on how "zero" is defined, a compromise. Instead of a compromise, know what you want - your target value - and continually seek to achieve it.
Six Sigma | Overview of the Control Chart | Green Belt 2.0® Lean Six Sigma | fkiQuality HD
zhlédnutí 9KPřed 6 lety
Six Sigma | Overview of the Control Chart | Green Belt 2.0® Lean Six Sigma | fkiQuality HD
Six Sigma | Histograms can't show behavior | Green Belt 2.0® Lean Six Sigma | fkiQuality HD
zhlédnutí 888Před 6 lety
Six Sigma | Histograms can't show behavior | Green Belt 2.0® Lean Six Sigma | fkiQuality HD
Six Sigma | The Price of Acting without Knowledge | Green Belt 2.0® Lean Six Sigma | fkiQuality HD
zhlédnutí 942Před 6 lety
Six Sigma | The Price of Acting without Knowledge | Green Belt 2.0® Lean Six Sigma | fkiQuality HD
ONE THING you are doing WRONG when Improving a Process | fkiQuality Lean Six Sigma Green Belt 2.0®
zhlédnutí 2,8KPřed 6 lety
ONE THING you are doing WRONG when Improving a Process | fkiQuality Lean Six Sigma Green Belt 2.0®
Today is not Tomorrow | Green Belt 2.0® Lean Six Sigma | fkiQuality HD
zhlédnutí 99Před 6 lety
Today is not Tomorrow | Green Belt 2.0® Lean Six Sigma | fkiQuality HD
Six Sigma Overview | Fishbone Diagram | Green Belt 2.0® Lean Six Sigma | fkiQuality HD
zhlédnutí 48KPřed 6 lety
Six Sigma Overview | Fishbone Diagram | Green Belt 2.0® Lean Six Sigma | fkiQuality HD
LEAN | 116 Innovators Discussion | Green Belt 2.0® Lean Six Sigma | fkiQuality HD
zhlédnutí 918Před 6 lety
LEAN | 116 Innovators Discussion | Green Belt 2.0® Lean Six Sigma | fkiQuality HD
5 Steps DMAIC Overview | Green Belt 2.0® Lean Six Sigma | fkiQuality HD
zhlédnutí 75KPřed 6 lety
5 Steps DMAIC Overview | Green Belt 2.0® Lean Six Sigma | fkiQuality HD
1 Secret Nobody Knew | The Red Beads Experiment 3 of 3 | fkiQuality Green Belt 2.0®
zhlédnutí 1,6KPřed 6 lety
1 Secret Nobody Knew | The Red Beads Experiment 3 of 3 | fkiQuality Green Belt 2.0®
For Finance decision-making | Green Belt 2.0® Lean Six Sigma | fkiQuality HD
zhlédnutí 302Před 6 lety
For Finance decision-making | Green Belt 2.0® Lean Six Sigma | fkiQuality HD
Valuable for all careers | Green Belt 2.0® Lean Six Sigma | fkiQuality HD
zhlédnutí 1,1KPřed 6 lety
Valuable for all careers | Green Belt 2.0® Lean Six Sigma | fkiQuality HD
7 Ways you're Managing People Wrong | The Red Beads Experiment 2 of 3 | fkiQuality Green Belt 2.0 ®
zhlédnutí 2,6KPřed 6 lety
7 Ways you're Managing People Wrong | The Red Beads Experiment 2 of 3 | fkiQuality Green Belt 2.0 ®
You Think You/re Managing with Facts? | The Red Beads Experiment 1 of 3 | Green Belt 2.0® fkiQuality
zhlédnutí 6KPřed 6 lety
You Think You/re Managing with Facts? | The Red Beads Experiment 1 of 3 | Green Belt 2.0® fkiQuality
LEAN | 8 Wastes - Why Do We Over-produce | Green Belt 2.0® Lean Six Sigma | fkiQuality HD
zhlédnutí 3,1KPřed 6 lety
LEAN | 8 Wastes - Why Do We Over-produce | Green Belt 2.0® Lean Six Sigma | fkiQuality HD
Six Sigma | ZERO Defects 2: How to get there matters | Green Belt 2.0® Lean Six Sigma
zhlédnutí 7KPřed 6 lety
Six Sigma | ZERO Defects 2: How to get there matters | Green Belt 2.0® Lean Six Sigma
great video that illustrates if a process is stable or not. It also highlights how moral from employee can suffer.
nice illustration of the importance of identifying root cause
interesting take on interpretating disparate data
Control Charts can be a manager's great "friend". It aids a manager to make an informed decision, instead of just looking at numbers and trying to impulsively make a decision based on the numbers.
This video/Lessons highlights the importance of using Control Charts. More importantly, it explains how production system put in place by management is crucial to the success of an employee and hence some management practices can be harmful to employees.
We can use statistics to create a Control Chart, look for problem areas, and predict future performance. In the Red Bead Experiment we can see that the Control Chart shows that all variation is common cause variation and has nothing to do with the workers performance.
The Red Bead Experiment reinforces that 94% of production problems come from the system. Since management owns the system and quality is the outcome of the system, quality must start with Managment. Rewarding or punishing workers has no effect.
The Red Bead Experiment is a good representation on how numerical goals can be meaningless if the system is flawed.
It really interesting to see how businesses can easily misinterpret data in making crucial operational decisions.
excellent example of how to back into a problem and address either yield or sigma to include in the charter respective of what is important to your audience.
great visual representation of how much satisfaction a customer will get from an improved process.
Informative video on the DPMO method and how it can be used to calculate Sigma, DPMO, and Yield when there are more than one CTQs.
Good explanation on the Sigma Method for process capability. Useful tool to see your progress when running Lean Six Sigma projects to increase process capabilities, which results in a higher yield and reduced DPMO.
I liked how the formula ca be used to show how to different targets can be met.
Having the graphical depiction of the different sigma values was very helpful in seeing how changes in the the average and/or the standard deviation affect the shape/position of the curve.
Another very informative video. The fishbone diagram visually helps to uncover the problems and their root causes. It can help in brainstorming to find the causes of problems; the ones that are not usually visible or likely obvious.
A great and "easy to understand" explanation of the uses of Control Chart. They help one to identify regular causes of variations or special causes of variations, calculate UCL and LCL, thereby investigate changes in data and make the right decision.
Asking "why" multiple times is a terrific way to get to the get to the cause and effect. I've used this method with customers, and never knew it originated from the fishbone diagram.
excellent explanation of how these control charts can improve a process by identifying signals at a granular level.
Very informative video showing how using three-standard-deviation limits rather than three-sigma limits in control charts is incorrect. Using three-standard-deviation limits widens the control limits and may not show abnormal process behavior.
Excellent explanation of how to create X-Bar and R control charts, and why we must monitor both of these charts to detect special cause variations (signals to action), as opposed to common cause variation (random noise). If special cause variations (signals to action) are found, we must do an investigation to find the root cause and eliminate.
Great visual on how confusing +/- sigma with sigma can be and the effect on control limits differ between the two.
Very informative video on the Fishbone Diagram. The Fishbone Diagram is a useful tool to break down complex problems or processes. Using the Fishbone Diagram, we can brainstorm and identify what changes to test, to improve a problem or process.
Great explanation of the difference between the Sigma lines and the standard deviation. The control chart gives you a visual representation of data over time. It shows whether a process is displaying abnormal behavior .
Very interesting concept to look at different categories of causes. I'm familiar with the "5 Whys" but didn't know that this was the origin.
This explanation shows the importance of looking into the special causes of variation.
Very good explanation of the difference in meanings between the 1,2 & 3 sigma lines and the sigma used to show the standard deviation
This video really covers the difference between the Control Chart and the Histogram. The Control Chart gives a more accurate picture of the natural variations in a process unlike the Histogram. The UCL and LCL guides the reaction of an individual to changes in values in a process.
excellent illustration of how a control chart is more accurate than a histogram.
excellent illustration on how managing with numbers requires that we give correct meaning to each value.
Control charts are very valuable in helping manage, for instance, operation in a "levelheaded" way. It gives a better picture unlike a histogram.
Informative, the three different examples of the same data help clarify how the variables of behavior over time aren't expressed when using a histogram.
Thanks for explaining the difference between a Histogram and a Run Chart. It was easy to follow your explanation.
This video brings to attention the importance of due diligence. Acting without the right knowledge and facts can be really costly.
The 3 Nevers for a Perfect Process really explains the saying " a stich in time saves nine".
This video further shows how reducing the number of steps (LEAN) and increasing the quality of each process (SIGMA) can sustain quality end-to-end performance.
The chart and your explanation really made it easy to understand this concept. This video greatly explains flow/process and resource efficiency. Thank you.
This video really makes me question why QC & QA are SEPERATED from production. The cost of inspection and rework from an internal view is one thing to consider. However, the cost of an upset customer that no longer wants to do business with you because of the continuous cycle of rework should be the external view to be considered first. Yet, the vicious cycle continues.
When you air for a target the goal is to hit the center "a bullseye", are you continually aiming for the center and hitting with minimal variation, or are you simply happy to hit the target?
You’re never going to hit the target always, because of multiple reasons called causes of common variation. The best that anybody can do is to aim for the target with minimal variation.
Change is difficult, but when the change is coming from the voice of the employee then ownership is realized at a rapid rate of acceptance.
Good video on building a value control chart, and how values increasing gradually, values changing randomly, and values change abruptly affect the UCL and LCL.
Video showing how Control Charts can be a great management tool, to filter out the noise, and be able to see more clearly when action is needed.
Excellent video showing the difference between histograms and run charts, and how run charts can show behavior/trends, whereas histograms cannot.
Thanks again for another enlightening video. It is really important to have great communication between the different departments of a company as well as their customers, among other things, to prevent over-production and therefore waste.
Thanks for such a detail explanation of 8 LEAN Wastes. The diagram you drew really helped me to visualize the inter-connectivity of the 8 LEAN wastes.
Good explanation of the control limits and the comparison to the histogram
It is expedient to build in quality measures into our processed and try to get higher yields and avoid costly reworks.
Knowing that the company is a system with a series of interrelated functions with one common aim, there should be constant and clear communication between them and also continuous process improvement to achieve the best outcome.
Easy to see the difference between the histogram and the run chart in a side-by-side comparison. The behavior of the variables is easy to see.
It is very interesting to learn the similarities and differences between Lean Six Sigman and Project Management and very striking how the two complement each other and play a very vital role in an institution. Maintaining a well skilled and well-informed Lean Six Sigma and Project Management teams will sure be a lifeline for a company that wants to thrive and/grow for a really long time.