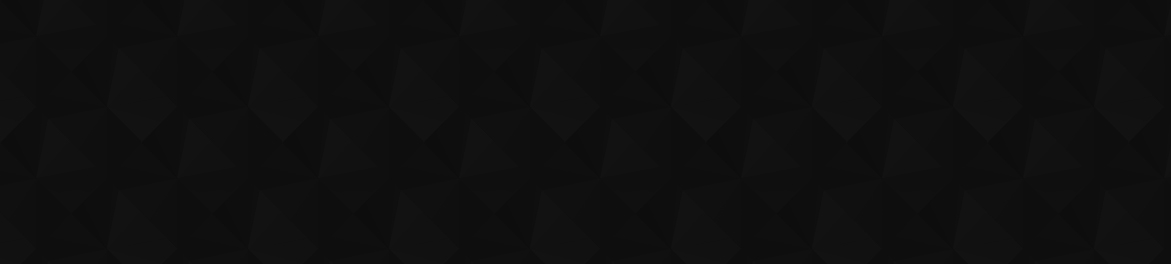
- 22
- 67 291
Cone Editions
United States
Registrace 5. 12. 2019
We explore everything from beginner inkjet skills to advanced digitally based intaglio and darkroom skills. Our mission with Cone Editions CZcams is to help you have more confidence in your printmaking. Cone Editions printmaking videos and tutorials are hosted by Jon Cone & Cathy Cone who established the world’s first digital printmaking studio in 1980. We’re joined by our in-house printing guru Walker Blackwell and studio magician Nathaneal Kooperkamp.
Here's a general list of things you can expect from this channel:
• An unfiltered look at what we do at Cone Editions Press
• Advanced printmaking skills tutorials
• Beginner printmaking skills tutorials
• Common inkjet printer problems
• Software tips
• Print Presentation tips
If you are interested in our printing services or our workshops - check us at cone-editions.com
Here's a general list of things you can expect from this channel:
• An unfiltered look at what we do at Cone Editions Press
• Advanced printmaking skills tutorials
• Beginner printmaking skills tutorials
• Common inkjet printer problems
• Software tips
• Print Presentation tips
If you are interested in our printing services or our workshops - check us at cone-editions.com
Cone Editions Direct to Plate PhotoGravure Workshops
In this workshop we will teach you how to produce photogravure plates with the Piezography three-gradated shades inkjet direct-to-plate process using highest-fidelity Green Mountain Plates and exposed with the unique verifiedUV system. These highest fidelity photogravure plates rival and can surpass copper plate photogravure and are much higher in fidelity than two exposure processes.
The workshop is totally hands-on. You will get inky so bring an apron with you or purchase one of our Cone Editions studio aprons. No experience in inkjet printing, Piezography printing, or gravure printing is necessary to take the workshop, but it always helps to have a bit of knowledge in one or more of these fields!
The concept behind this workshop is that the results you get at Cone Editions can be duplicated in your own studio. The same system that you will be using at Cone Editions is available as a package to bring back to your own studio if you choose. Or you can just come to the workshop to maximize your time making photogravures of your images - and have a blast! You can even choose if you want to have Cone Editions make your photogravure plates in the future and use the workshop to learn what you can do to get the best out of your images while learning new studio techniques to get the best out of the plates.
Sign up for our workshops here: www.cone-editions.com/event
The workshop is totally hands-on. You will get inky so bring an apron with you or purchase one of our Cone Editions studio aprons. No experience in inkjet printing, Piezography printing, or gravure printing is necessary to take the workshop, but it always helps to have a bit of knowledge in one or more of these fields!
The concept behind this workshop is that the results you get at Cone Editions can be duplicated in your own studio. The same system that you will be using at Cone Editions is available as a package to bring back to your own studio if you choose. Or you can just come to the workshop to maximize your time making photogravures of your images - and have a blast! You can even choose if you want to have Cone Editions make your photogravure plates in the future and use the workshop to learn what you can do to get the best out of your images while learning new studio techniques to get the best out of the plates.
Sign up for our workshops here: www.cone-editions.com/event
zhlédnutí: 844
Video
A comparison of LED lights in Cents per Microwatt for Platinum & Palladium alt process printing.
zhlédnutí 1,3KPřed 2 lety
In this video we break down different LED UV light sources using cost per microwatt using an Ian Leak measurement device filtered for alt-process Platinum/Palladium printing (aka 365nM sensitivity with a bit of 395 sensitivity as well). What we find is that the less expensive an LED strip is per meter, the MORE expensive it is when comparing the total cost vs actual UV irradiance.
The impossibly big verifiedUV™ 365nM UV Vacuum Exposure Machine Build (in progress)
zhlédnutí 1,4KPřed 3 lety
We are nearly finished with a giant 45" x 65" vacuum exposing machine we are building with the new verifiedUV™ super high output 365nM LED strips exclusively available from InkjetMall.com These strips have higher efficiency than any other 365nM LED strip being sold. They are newly developed and our machine is reaching an exposure that is as short as our 3K watt Nuarc. This is our dream system f...
1st Prototype of an Anthotype Print Exposing Head
zhlédnutí 903Před 3 lety
We are building a vacuum exposing unit for Anthotype printing. This particular prototype is designed around a total output of 800 watts of 460nM light. The deep blue is perfect for exposing plant derived photosensitive "emulsions". The aluminum plate is working perfectly as a giant heat sink radiating 90% of the heat out the back instead of at the print. The PAR we measured at 5" is over 1800! ...
Printing with Piezography® Pro inks on handmade Washi paper
zhlédnutí 8KPřed 4 lety
George Wiedenhofer challenged us to produce two portfolios of prints on Echizen Washi handmade by the living Master Ichibei Iwano IX. The paper is gorgeous. It is also slightly irregularly shaped making it impossible to feed directly into the printer. The paper making process created a surface that is also slightly fuzzy. There is no coating on the paper to help with density and dMax. We used t...
Direct to plate Photopolymer gravure from start to finish!
zhlédnutí 14KPřed 4 lety
This is a video that shows how we make direct to plate photopolymer gravure prints from start to finish. The video is mostly from my point of view which lets you check out the process as it's happening. The process takes place over a few days. Scroll down for time markers... 0:00 We start with a nozzle test on the 10 shaded Piezography monochromatic pigment ink set on an Epson Pro 9900 printer....
Cathy Cone photopolymer gravure project
zhlédnutí 2,7KPřed 4 lety
Six images; some with multiple plates and others with additions in drypoint, printed in different inks on Hahnemühle Copperplate Natural and hand bound into a folio. Printed by Nathanael Kooperkamp in collaboration with Cathy Cone at Cone Editions Press in February, 2020. A unique work with the potential of producing a limited edition. The photopolymer gravure plates were produced by direct to ...
Wet packing printmaking paper for photopolymer gravure
zhlédnutí 1,4KPřed 4 lety
Gravures are printed by impressing the inked plates under enormous pressure onto fine paper. Dampening the paper makes it more pliable letting the fibers find their ways into the tiniest of crevices to lift the ink out. But, the paper can not be too wet. It needs to be just damp. This is our process at Cone Editions Press for wetting printmaking paper prior to printing in our intaglio presses. ...
Photographs and the Handmade Book Workshop at Cone Editions Press
zhlédnutí 625Před 4 lety
Pam Heemskerk, an American photographer and poet living in rural Maryland, is the guest instructor for this workshop. The approach is to teach you from start to finish how to design and select materials, edit and sequence imagery, and to make a book that furthers the narrative content of your work. You will be introduced to a structure a day, learn how to make a mockup, and have plenty of studi...
Hand Tearing Deckles in Printmaking Paper
zhlédnutí 1,7KPřed 4 lety
This is the way we do it... Simple tools include a bone folder that is used to repair the torn deckle and smooth it down. The straight edge...which is actually difficult to find these days with a sharp edge. You can find straight edges in a lot of places. At one point we were ordering them by the droves and all really known Brands... but they were arriving "not straight" and not sharp. So we lo...
Calibrated "Simple Cyanotype" one bottle chemistry method
zhlédnutí 3,9KPřed 4 lety
We calibrated Mike Ware's "Simple Cyanotype" one bottle chemistry method at an exposure scale of 2.70. We printed several of Cathy Cone's images and got perfect screen to print matches on the first go. Simple Cyanotype lets the user choose a chemistry that can realize a range of exposure scales matched to the contrast range of their negatives. But, the holy grail of cyanotype would be a very lo...
Digital Negatives That Work - PiezoDN - Workshop at Cone Editions
zhlédnutí 3,2KPřed 4 lety
We teach you how to produce and calibrate screen-to-print-matching digital negatives for any darkroom or alternative process using the PiezoDN system. During the course of this workshop you will also be making and learning the Malde-Ware Platinum/Palladium print process. If your ultimate goal is to make silver prints, or salt prints, or cyanotypes or any process that requires a digital negative...
Direct to Plate Gravure Workshop at Cone Editions Press
zhlédnutí 2,6KPřed 4 lety
Digital Direct to Plate Photopolymer (DTP) Gravure has the potential to allow a new user to make photogravures at the same standard as those practicing the traditional copper based methods but with 1/3 the cost and 1/10th the amount of labor. Our process matches your monitor. The process, as we teach it, is not difficult to master. If you have no experience in an etching studio you will gain a ...
Calibrating Platinum Print over Color Pigment Inkjet
zhlédnutí 2,5KPřed 4 lety
Calibrating Platinum Print over Color Pigment Inkjet
Calibrated Direct to Plate Photopolymer Gravure for the Curtis Legacy Foundation
zhlédnutí 2,7KPřed 4 lety
Calibrated Direct to Plate Photopolymer Gravure for the Curtis Legacy Foundation
Target Reading with the Piezography® Profiling System
zhlédnutí 1,2KPřed 4 lety
Target Reading with the Piezography® Profiling System
Part 1 - Single take video of CMYK direct to plate photopolymer gravure
zhlédnutí 4,5KPřed 4 lety
Part 1 - Single take video of CMYK direct to plate photopolymer gravure
Part 2 - Single take video of CMYK direct to plate photopolymer gravure
zhlédnutí 5KPřed 4 lety
Part 2 - Single take video of CMYK direct to plate photopolymer gravure
What is this beautiful press?
This press is a Ettan 36" x 72" which we've printed on since 1984! They are hard to find these days but they are fantastic presses...
question how does this method compare to using say a imagesetter and flim ? is this method better quality wise ?
Our method is dotless and continuous-tone producing more gray tone separations than can imagesetter. Because there is no film or exposure through glass it has higher levels of detail.
awesome
Many thanks.
I had no idea this was even possible
Bravo
I have been learning the photogravure process of printmaking and loved this video - thank you for sharing so much of the technical aspect of this gorgeous art! Could you share what cream you are using on your hands & gloves when putting on the gloves & why? Also, are you using deli paper for polishing the plate?
it's just a bit of corn starch. These plates have such a narrow bite that we can not use regular tarlatan to wipe as it would pull most the ink out of the crevices. So we use polyester wiping cloth by Akua (even though we use oil based inks) and we wipe the highlights with tissue as it does not take ink off the other areas. But no deli paper!!! It may be the tissue you are seeing.
@@ConeEditions Thank you so much for the clarification! I’ve signed up to be notified about classes/workshops for 2024 and hope to attend one of the photogravure workshops. Oh, can you tell me what the spray was you added to the leftover ink to be saved?
@@charalson3023 that is a typical anti-skin spray you should be able to source from any supply house that sells intaglio inks.
Interesting - thank you! You’ve been very kind to respond, much appreciated😊
What kind of plates are in use? Who is the producent?
These are the new Green Mountain Plates exclusive to InkjetMall.com. They turn yellow after exposure, have a very long tonal range as a result of their slow exposure speed. These we produce direct to plate using a proprietary 10 ink system which further increases tonality and resolution. Plates are here: shop.inkjetmall.com/Green-Mountain-Plates-SM-95.html If you would like us to produce them ready to print for you that service is here: www.cone-editions.com/gravure
What range regarding UV nm can be used? All within UVA? And are both the printing parts and the non-printing parts of the plate at the same height? In other words like an offset-print? Some kind of a litho-print? Can any type of ink via any inkjet-printer be used if the colours are defined (CMYK). Hopefully You will answer all of my questions! Thanks!@@ConeEditions
@@Jolleseileren the ideal would be 365nM, but up to 390nM although a bit more exposure time would be necessary. The plate could be used for relief where you expose what you want to remain high and roll up with ink, and what is not exposed goes into relief. But we exposed with a positive image so that there is a continuous-tone intaglio into the photopolymer... and where it goes below the surface is where it retains the ink. The surface would be where it does not or where it prints white or nearly white. BUT in our process this depth is very very shallow. How we do the inkjet direct to plate you can see here: czcams.com/video/7ZrV_y14Df4/video.html Some of the customers of our plates use their own workflows where they simply print a grayscale image onto the plate to act as the "positive". We use a special set of 10 gradated carbon inks and a calibration process to produce absolute continuous tone. If you have your own etching press - contact our studio and have us make you a plate. Making plates for other studios is part of our business. www.cone-editions.com/gravure
Where can I find this kind of washing pad you are using? Do you prefer this over a brush?
Hi Kees, it's a ceiling painting pad. You can get them at hardware or paint stores. Best regards, Jon
@@ConeEditions Thanks! How simpel can it be.
Do you guys have a shop playlist? The music is lovely...
That print is a piece of Art!!! What a fantastic and unique way of printing. My ink Jet procedures seem kindergarten in comparison 😅
When in the process would you normally trim the plate if you wanted a consistent border (imprint) around the final print?
We print our trim marks and do our trimming after we have final hardened the plate with the second exposure (4x the calibrated exposure). The trim marks give us consistency. You just increase the canvas size with a white margin around your area to the size of the borders you want, and then add 1 pixel all around of gray or black canvas size to form the trim edges.
I have tried making the "Simple Cyanotype" sensitiser solution and have come up against the same problem each time...When dissolving the Iron (III) nitrate nonahydrate in the citric acid solution, I am only able to add around 2g before it forms a brown precipitate and will not undergo the yellow -> green colour change upon addition of 10% ammonia. I can only get it to work as a sensitiser by adding considerably more ammonia, and even then can only dissolve ~4g of Iron nitrate. Following the recipe to the letter results in a very slow reaction to form insoluble Prussian blue in the bottle overnight. Any tips??
what is the fabric used for wiping?
You can not use traditional tarlatan with polymer because it aggressively removes ink. So we use Akua spun polyester wiping cloth by Speedball.
what inks do (brand, specific blacks) you use and modifies added?
We use oil based inks from Gamblin and Charbonnel. The blacks we like are Bone Black (which is very dark and produces open mid-tones and quarter tones...) and Carbon Black which is warmer, and occasionally Portland Black if we want to strengthen the mid-tones. Any of these blacks we can make warmer or cooler or more neutral by addition of color inks. Generally, our calibration process produces prints that match the display but often during proofing these decisions to strengthen or open come about seeing the work progress. The only modifiers we use are Hanco's Zea Mays transparent base (10-30%) and a little easy wipe.
So exciting
Love, love your vids... Im new and learning. Thank you.
Yes, I missed the most important part, making the plate, bummer
You can see how that's done here: czcams.com/video/7ZrV_y14Df4/video.html
Great waste basket shot at the end. Love the sound track too.
Printer settings, Curve? :)
This process uses several monochromatic inks from the Piezography black and white ink set. This is the same ink set that produces tens of thousands more gray levels than EPSON color inks... we do provide full library of free curves for all EPSON and popular 3rd party media for black & white prints, and also curves library for making digital negatives for alternative processes...but the curves for this multi-ink Direct to Plate are only available when you come take a workshop with us. You need a supported EPSON printer to install the Piezography ink set. The workshops are here: www.cone-editions.com/workshops and we have an online pre-recorded demonstration on it here: shop.inkjetmall.com/DTP-ZOOM.html
@@ConeEditions I sold my printer with the Piezography ink set, now using Epson P8000, I'm a printmaker, (learded from Dan weldon 2000) i'm just looking for more Information on direct to plate printing...
@@boxkam there are a lot of ways to do this process with direct to plate and the more popular method uses black ink only. That is how we started, then we moved to two inks, and now we offer three inks and are separating 256 gray levels on a photogravure plate. We use the Piezography Profiler to do that. We do offer Piezography ink set for the SureColor P6000, P7000, P8000 and P9000 printers. Those are our latest generation supported printers. If you wish to stick with your OEM inks you could install QuadTone RIP and print with the black ink only and generate a single curve on your own... It is not difficult at all to generate a single ink curve with QTR. You should be able to separate 100 gray levels or close to it. You can start with just 21 steps, and then comfortable with that move to 51 steps. Then go for the 100.
@@ConeEditions I have QTR and DN pro, I've been making DN for years, Just trying to get more info on Direct to plate :)
@@boxkam I'm Jon Cone, do you have my email? Easier to answer questions that way...
Beauty!
I would have like to have had some one talking about what they were doing not the JAZZ station thank you very much!
Wow! Who’s work were you printing? That dark desert scene blows me away
Amazing, you are always so far out front ❤
where is a good place for a straight edge like that with the burr on the edge?
Not an easy thing to buy online because you can not first feel the edge. All of the ones we bought online for tearing are dull. So we just use them for drafting. But, large architectural or art supply houses usually have quantities of stainless steel straight edge bars displayed and you choose the sharpest one.
incredible!
Does this paper need to be pre- coated like commercial papers are for inkjet/pigment printing?
No, not at all. Most of the gampi and traditional washi take inkjet ink beautifully. But, you do often need to better control the amount of ink being printed on it. ICC profiling can help. But, we use a printer driver that we can more easier control how the ink is printed, the total amount of ink from all the channels, and then on top of that we profile with the Piezography Professional Edition toolkit. But, you can also get really beautiful results by on these paper with traditional printer driver that comes with the printer. You would probably need play around with the different paper settings in the printer driver to get an idea of what setting produces the best ink output on the paper. Coating it removes a lot of the more intrinsic and lovely qualities that the gampi has (like sheen...) The inks then sheen... They are definitely worth the work.....
@@ConeEditions Thanks! I just started learning Richard Boutwell's Quick Curve-QCDN to go with my epson p800. I love the rice papers and will defiitely look in to it. Is there a front and back side to this paper? I'm so sorry I missed George's Show at the Crary Gallery. We're only an hour away, but we were in Maine at the time.
@@dorothykloss5303 both sides are printable but also usually different from one another. We print on the smoother side.
Great work .........................................fantastic video
Nice Vid - what is the purpose of adding the transparent base to the ink?
Our process uses the Piezography Pro ink set and the Piezography software - and we are able to separate 256 gray levels in the plate. That's considerably more than copperplate photogravure. Adding transparent base is critical to that - and we lose nothing. We can get a very dark black even with 30% transparency - so what the transparent base does is open up a lot of the mid and dark tones. Without doing this, those tones would not be as smooth - although some people prefer chunky shadows... we prefer open shadows with lots of transitions between the shades...
@@Inkjetmall thank you, good insight
wonderful video - just ran across it. Just learning to make cyanotype prints based on digital negatives and would love to know what paper you are using for this video. It looks very sharp and grain free, and clearly works well with this chemistry. Could you comment on what type of paper you are using for this process.
we use Revere platinum paper!
@@ConeEditions Thanks so much, I will try some. I use your inks on my 3880, and love the results.
I appreciate the effort that went into this experiment, but I don't think it yields valid or useful results. Firstly, the sensitivity of the emultion of the platinum or cyanotype process is not equal for 365nm and 395nm. At the same power output 395nm LEDs will likely yield longer exposures because the emulsion is less sensitive to this wavelength. Secondly, a UV sensor typically has a spectral sensitivity curve that isn't flat. Your measurement for the cheap 395nm LEDs is likely far too low as the UV sensor is most sensitive to 365nm (and therefore less sensitive to 395nm). Lastly, the density of LEDs within the field of view of the sensor isn't controlled for. So, wouldn't it make more sense to do a real world comparison? I'd like to see a measurement of the exposure time needed for a particular print with all three kinds of LED strips, keeping all other variables the same.
1. We are specifically testing for 365 Iron processes (PtPd as in the title). 2. I stated that the 395 are what a lot of people are purchasing in order to do iron processes, but they are actually needing 365. So yeah, it's part of the point. We have narrow band 365 filter on the sensor similar to 365 process. As stated in the video, it does pick up some 395. 3. Re: density of LEDs: In this video and test we are attempting the "most-dense possible" amount of LEDs for each strip profile. Essentially we are doing cost of uW based on the largest amount of 365 UV we can pump out per CM per LED type. That is the test. These are all clearly defined parameters. 4. Yes, we can do a real-world comparison. Sure, that's in the plans. It will be PtPd to start with, along with other 365nM processes. And we can do real-world cost-per-uW based on those printing methods sure. 5. Why does time matter? Well the longer the exposure the less prints you can do (a lot of LED units out there are doing 20min exposures for PtPd and Cyanotype etc) while we are doing 62sec exposures on our strips (90sec for cyanotype). This is significant if you are wanting to get 15 prints out or 20 prints out in a day. The longer the exposure the more dry the paper becomes for print-out methods. The longer the exposure the more wear on the LEDs (heat over long periods of time) and the lower UV output you get the hotter the chips get. The longer the exposure the more electricity is used and the more all the other parts wear out (vacuum pump, power controllers, etc). So there is value in figuring out the shortest exposure and there is value in finding the real cost of the shortest exposure possible with different LED types. In this case we are testing it in a 365nM defined space.
@@ConeEditions I'm just making a point about the science. Using a narrow band 365nm filter is the reason your 395nm power measurement is erroneously low. The implicit assumption here seems to be that the spectral sensitivity of the emulsion is equal to what the narrow band filter transmits. I don't think that is the case. Regardless, I think we agree that it makes sense to buy better LEDs to save time.
@@ConeEditions You are not really testing the 'most-dense possible' amount of LEDs for each strip profile, as you are using the plastic connectors for these strips. In my UV exposure rig, I soldered the ends to the UV strips, which enables them to be stacked without any gap and with a more secure connection. Maybe the argument is that soldering is an 'advanced' skill, but if a person does not have knowledge of soldering/electronics, I don't think he/she should work with either AC mains or high-power DC power.
@@anders077 that's correct we are not, because most of the exposure plates made with these are in the 30x48 inch range and some up to 44x64 inches and therefore the easiest method of replacing strips should they be injured is not by soldering in tight places and upside down. A completed exposure system looks like this: shop.inkjetmall.com/VerifiedUV-Exposure-Systems.html So, it is not the lack of skill, but the practical application of when someone inadvertently closes the cover on an ill-placed lunch box they can muster their own repair by reaching in to unclip and re-clip new strips rather than to try and solder while upside down or using a mirror. There is no voltage drop to using the clips and our current highest density (at 3mm between strips) produces greater than 7000uW/cm2 at 4-6 inches. And this is more than 7 times the amount of irradiance produced by a 3000w NuArc platemaker. At 11mm between strips the systems produce 4000 uW/cm2, and we also offer lower powered systems with even greater gaps to about 2000uW/cm2. As is the 3mm spacing will expose a platinum print in 60 seconds compared to the 18 minutes of a NuArc system.
where can I find the LEDs with the highest performance?
shop.inkjetmall.com/VerifiedUV-v2-365nM-UV-Led-5-Meter-Strip.html#attr=64286,64285. Warm regards -CEP
Thank you so much
wow... Just wow. Amazing outcome, guys. Where are you based?
We are located in Vermont.
Just great to see how professionals work. Thanks
Nice video, thank you. Is there no need for a screen exposure using this method, or are you introducing a dot pattern in your image?
No need for a screen. With direct to print the actual dots from the inkjet printer provide the "screening". It can be done at 2880dpi with the UltraHD Matte Black ink that Inkjetmall.com sells for Epson printers. Or it can be done at 1440 dpi with Epson black ink. We also have a three ink method which prints at such fine resolution, that it looks photographic without any dot textures whatsoever.
Why'd yeah stop at 65"?
it's all we had room for in our studio!
👁️🖤
Great work, and a pleasure to witness.
Boards of Canada was a very lovely, unexpected touch
WOW
Systems now for sale at Vermont PhotoInkjet from 11x15 with vacuum up to 30x40, shop.inkjetmall.com/VerifiedUV-Exposure-System.html
What software are you using on the MacBookPro to be able to use the DTP70
We use an old mac pro running 10.6 connected to ColorPort (the screen you see if most likely just ScreenShare open). But if you wanted to use a MacBook pro, you can run Windows 10 with Parallels and run ColorPort that way.
@@ConeEditions Thank you. I have a older Mac that can do the job 😊 Just wondered if it was possible on a new one.
So Colorport can't be run w/Monterey
Your videos really do need narration.
Bonjour ! Je peux avoir le numéro de téléphone. J'ai besoin de plaques polymères.
Nous ne vendons que des plaques que nous produisons et qui sont prêtes à imprimer. www.cone-editions.com/gravure
Great video, beautiful looking prints! Thanks Jon! Since the paper is so thin did you use the same backing sheet when you made the uncoated paper profile (.quads) and .icc profile?
Hi Michael, we did. We kept the target mounted on a thin white receiver paper in order to bring the luminance up on the 700 gray patch target. The print to screen match was really good! :)
If you ever break an old Epson printer they have some decent fans in them.
Please explain the purpose and use of this creation! I'm impressed.
The 365nM UV strips are a new generation we developed to be super strong. For LEDs, it is unusually strong and the unit is designed for super short exposures when we use it to expose a negative onto a platinum print. The shorter exposing time benefits the process by not driving all the moisture out of the sensitized paper and promotes higher dMax and less noise. It has an exposure calculator to measure the amount of UV the platinum print is receiving so that we can perfectly calibrate the process so that a digital negative makes a platinum print that matches the image on a display. That’s it in a nutshell!
"Dear Santa Claus . . . " ☺
That's a dream machine no doubt about it ! Fantastic job ! I'll be attempting something similar in the autumn !