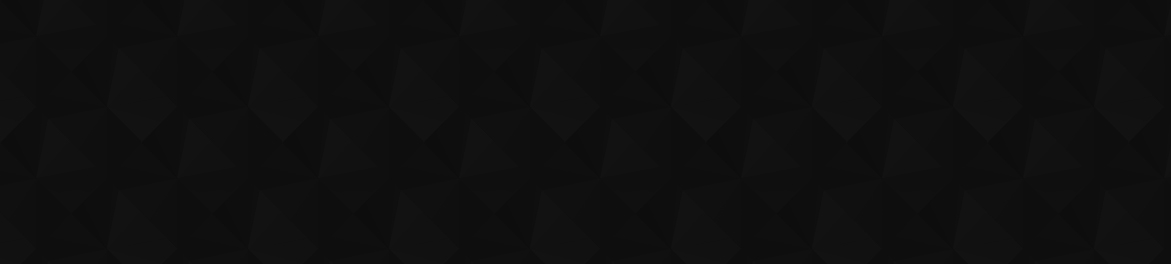
- 66
- 1 069 483
Kapman's Basement Workshop
United States
Registrace 27. 02. 2021
If you've got an interest in 3D Printing, Home Audio, Photography, Gardening & Hydroponics, Technology, Software or Computers, and just about anything interesting as a member of the Maker or Creator Community, expect to see some interesting projects chronicled in this channel. Focused and broad topics are the rule of this channel!
STL files are posted to Printables.com at:
www.printables.com/social/401093-kapmans-workshop/collections/401262
CFG files are posted here: github.com/Kapman1/Kapman1
STL files are posted to Printables.com at:
www.printables.com/social/401093-kapmans-workshop/collections/401262
CFG files are posted here: github.com/Kapman1/Kapman1
Building the ERCF v2, Enraged Rabbit Carrot Feeder by Siboor. Part 5 - Wiring & software
This video series shows how to build an Enraged Rabbit Carrot Feeder known as the ERCF v2 for your 3d printer. The ERCF is a filament changer that allows your 3d printer to switch colors during a print. In this video, I'm using a Siboor kit. You will need to 3d print your own parts with this kit. The kit is organized really well with a toolbox of very high quality parts. It even comes with a BTT BigTreeTech EBB MMB Mainboard and 2209 drivers.
This video is part 5 which shows how to wire and install software for the BTT BigTreeTech EBB Mainboard used to control both the Cotton Tail filament buffer known as the ERCT and the ERCF. Note that while the ERCF is closely associated with the Voron community, the ERCF & ERCT should work with any 3d printer.
Important links:
- Siboor Kits can be found here at a discount of $15: shareasale.com/r.cfm?b=2355443&u=3422519&m=142812&urllink=&afftrack=
- If you wish to purchase the BTT BigTreeTech EBB MMB Mainboard and 2209 drivers for your own build, please purchase from: shareasale.com/r.cfm?b=1890927&u=3422519&m=118144&urllink=&afftrack=
Important documentation:
- ERCT Github for documentation and STL files: github.com/Enraged-Rabbit-Community/ERCF_v2/tree/master/Recommended_Options/ERCT_Buffer
- ERCF V2 Github for documentation and stl files: github.com/Enraged-Rabbit-Community/ERCF_v2
- KlipperScreen Happy Hare Edition: github.com/moggieuk/KlipperScreen-Happy-Hare-Edition
Klipper LED effects: github.com/julianschill/klipper-led_effect
- Klipper LED Lighting:
github.com/julianschill/klipper-led_effect
- BTT BigTreeTech EBB MMB Mainboard documentation:
github.com/bigtreetech/MMB
This video is part 5 which shows how to wire and install software for the BTT BigTreeTech EBB Mainboard used to control both the Cotton Tail filament buffer known as the ERCT and the ERCF. Note that while the ERCF is closely associated with the Voron community, the ERCF & ERCT should work with any 3d printer.
Important links:
- Siboor Kits can be found here at a discount of $15: shareasale.com/r.cfm?b=2355443&u=3422519&m=142812&urllink=&afftrack=
- If you wish to purchase the BTT BigTreeTech EBB MMB Mainboard and 2209 drivers for your own build, please purchase from: shareasale.com/r.cfm?b=1890927&u=3422519&m=118144&urllink=&afftrack=
Important documentation:
- ERCT Github for documentation and STL files: github.com/Enraged-Rabbit-Community/ERCF_v2/tree/master/Recommended_Options/ERCT_Buffer
- ERCF V2 Github for documentation and stl files: github.com/Enraged-Rabbit-Community/ERCF_v2
- KlipperScreen Happy Hare Edition: github.com/moggieuk/KlipperScreen-Happy-Hare-Edition
Klipper LED effects: github.com/julianschill/klipper-led_effect
- Klipper LED Lighting:
github.com/julianschill/klipper-led_effect
- BTT BigTreeTech EBB MMB Mainboard documentation:
github.com/bigtreetech/MMB
zhlédnutí: 6 921
Video
Building the ERCF v2, Enraged Rabbit Carrot Feeder by Siboor. Part 4 - The Cotton Tail Buffer ERCT
zhlédnutí 7KPřed 2 měsíci
This video series shows how to build an Enraged Rabbit Carrot Feeder known as the ERCF v2 for your 3d printer. The ERCF is a filament changer that allows your 3d printer to switch colors during a print. In this video, I'm using a Siboor kit. You will need to 3d print your own parts with this kit. The kit is organized really well with a toolbox of very high quality parts. It even comes with a BT...
Building the ERCF v2, Enraged Rabbit Carrot Feeder by Siboor. Part 3 - Selector, Encoder & Axis
zhlédnutí 7KPřed 2 měsíci
This video series shows how to build an Enraged Rabbit Carrot Feeder known as the ERCF v2 for your 3d printer. The ERCF is a filament changer that allows your 3d printer to switch colors during a print. In this video, I'm using a Siboor kit. You will need to 3d print your own parts with this kit. The kit is organized really well with a toolbox of very high quality parts. It even comes with a BT...
Building the ERCF v2, Enraged Rabbit Carrot Feeder by Siboor. Part 2 - Filament block construction.
zhlédnutí 7KPřed 2 měsíci
This video series shows how to build an Enraged Rabbit Carrot Feeder known as the ERCF v2 for your 3d printer. In this video, I'm using a Siboor kit that comes with a CNC 80T gear. You will need to 3d print your own parts with this kit. The kit is organized really well with a toolbox of very high quality parts. It even comes with a BTT BigTreeTech EBB MMB Mainboard and 2209 drivers. This video ...
Building the ERCF v2, Enraged Rabbit Carrot Feeder by Siboor. Part 1 - Building the gearbox.
zhlédnutí 17KPřed 3 měsíci
This video series shows how to build an Enraged Rabbit Carrot Feeder known as the ERCF v2 for your 3d printer. In this video, I'm using a Siboor kit that comes with a CNC 80T gear. You will need to 3d print your own parts with this kit. The kit is organized really well with a toolbox of very high quality parts. It even comes with a BTT BigTreeTech EBB MMB Mainboard and 2209 drivers. This video ...
Recycle your BMG style extruder and build a Sherpa Micro extruder
zhlédnutí 24KPřed 10 měsíci
See how I recycled a BMG style extruder clone I was using for a bowden configuration to construct a Sherpa Micro extruder design by Annex Engineering for a direct drive configuration and saved about 150g in weight in the process. If you have a BMG extruder you plan on retiring, this might be a good option for you when you choose to upgrade your 3d printer extruder. Note that this is very simila...
Two Trees SP-5 3D Printer First Print!
zhlédnutí 2,9KPřed 11 měsíci
This video gives a quick overview of the Two Trees SP-5 3d printer. A quick review of assembly with a few tips and then gets into some thoughts about the experience with this Two Trees 3d Printer along with some sample 3d printing. Useful Links: Filament sensor mount and slicer configuration file: www.printables.com/model/523131-two-trees-sp-5-bl-touch-mount-runout-sensor-mount- If you are inte...
Build a Siboor Voron 0.2 - Electronics & 1st Print - Part 6
zhlédnutí 4KPřed 11 měsíci
This is a video series showing how to build a Voron 0.2 using a Siboor kit that comes with CNC and 3d printed parts to eliminate the need to print these parts yourself. This video is part 6 which covers the installation of electronics (MCU) and file configurations to create your first 3d print. The video concludes with thoughts on the quality and build of this kit and includes tips along the wa...
Weird PLA Filament Fix for your 3d printer #shorts
zhlédnutí 884Před rokem
Is your PLA filament breaking as it comes off the spool? Here is a super easy fix for that filament. I'm using the Kingroon filament storage bin and dehydrator in this video. It comes with everything you need to store and even repair your filament for your 3d printer. If you wish to get one yourself and improve the quality of your 3d printing, it can be found at this Amazon affiliate program: a...
Build a Siboor Voron V0.2 - The Print Head - Part 5
zhlédnutí 2,2KPřed rokem
This is a video series showing how to build a v0.2 using a Siboor kit that comes with CNC and 3d printed parts to eliminates the need to print these parts yourself. This video is part 5 which covers the print head. The series will conclude with thoughts on the quality and build of this kit and includes tips along the way. Important links: - Siboor Kits can be found here: shareasale.com/r.cfm?b=...
Build a Siboor Voron V0.2 - The Print Bed - Part 4
zhlédnutí 1,8KPřed rokem
This is a video series showing how to build a v0.2. This is a Siboor kit that comes with CNC and 3d printed parts to eliminates the need to print these parts yourself. This video is part 4 which covers the bed. The series will conclude with thoughts on the quality and build of this kit and includes tips along the way. Important links: - Siboor Kits can be found here: shareasale.com/r.cfm?b=2355...
Silica Gel Recycling #shorts
zhlédnutí 1,8KPřed rokem
Recycle and reuse Silica Gel Packets instead of throwing them out. In this short, I use a filament dryer from EIBOS to dehydrate Silica Gel as well as their filament vacuum pump, filament bags. I also 3d print special containers to consolodate Silica gel bags and for additional moisture absorption. #shorts Please note that the Silica Gel needs to dehydrate for 6 hours at 60c. Also, I have heard...
Build a Siboor Voron V0.2 - Gantry and belts - Part 3
zhlédnutí 2,7KPřed rokem
This is a video series showing how to build a v0.2. This is a Siboor kit that comes with CNC and 3d printed parts to eliminates the need to print these parts yourself. This video is part 3 which covers the gantry (x-axis) and the belts. The series will conclude with thoughts on the quality and build of this kit and includes tips along the way. Important links: - Siboor Kits can be found here: s...
Build a Siboor Voron v0.2 - Part 2, Motors for motion Siboor Kit
zhlédnutí 3,8KPřed rokem
This is a video series showing how to build a v0.2. This is a Siboor kit that comes with CNC and 3d printed parts to eliminates the need to print these parts yourself. This video is part 2 which covers all mechanical parts that are needed to mount the stepper motors. The series will conclude with thoughts on the quality and build of this kit and includes tips along the way. Important links: - S...
Build a Siboor Voron 0.2 - Part 1, The Frame
zhlédnutí 8KPřed rokem
This is a video series showing how to build a v0.2. This is a Siboor kit that comes with CNC and 3d printed parts to eliminate the need to print these parts yourself. The series will conclude with thoughts on the quality and build of this kit and includes tips along the way. Important links: - Siboor Kits can be found here: shareasale.com/r.cfm?b=2355443&u=3422519&m=142812&urllink=&afftrack= - ...
DIY - Build this LED RGB Mood Lamp with your 3D Printer
zhlédnutí 2KPřed rokem
DIY - Build this LED RGB Mood Lamp with your 3D Printer
Sensorless Homing, eliminate microswitches with Voron, 3d printer, Klipper, stepper motors & more
zhlédnutí 45KPřed rokem
Sensorless Homing, eliminate microswitches with Voron, 3d printer, Klipper, stepper motors & more
QIDI X-Smart3. How fast can an FDM 3d Printer be? See this fully assembled corexy 3DPrinter run
zhlédnutí 4,2KPřed rokem
QIDI X-Smart3. How fast can an FDM 3d Printer be? See this fully assembled corexy 3DPrinter run
Canbus SB2240 and SB2209 3D printer Install, Thoughts & Tips from BigTreeTech (BTT)
zhlédnutí 64KPřed rokem
Canbus SB2240 and SB2209 3D printer Install, Thoughts & Tips from BigTreeTech (BTT)
Voron TAP build, install, configuration, tips & tricks, final thoughts.
zhlédnutí 39KPřed rokem
Voron TAP build, install, configuration, tips & tricks, final thoughts.
Upgrade to KlipperScreen with BTT Raspberry Pad Pi 5, CM4, emmc, Klipper, Fluidd / Mainsail
zhlédnutí 11KPřed rokem
Upgrade to KlipperScreen with BTT Raspberry Pad Pi 5, CM4, emmc, Klipper, Fluidd / Mainsail
GE5C bearing upgrade and it's impact on acceleration. Does it help?
zhlédnutí 10KPřed rokem
GE5C bearing upgrade and it's impact on acceleration. Does it help?
Upgrade and add new life to your old 3D Printer with the BIGTREETECH SKR 3 EZ and Klipper
zhlédnutí 15KPřed rokem
Upgrade and add new life to your old 3D Printer with the BIGTREETECH SKR 3 EZ and Klipper
Canbus (can bus) - EBB36 / EBB42 Install with Klipper on Core-XY Voron 2.4
zhlédnutí 81KPřed rokem
Canbus (can bus) - EBB36 / EBB42 Install with Klipper on Core-XY Voron 2.4
Install a Filament Runout Sensor on your 3D Printer and Klipper
zhlédnutí 31KPřed 2 lety
Install a Filament Runout Sensor on your 3D Printer and Klipper
Never brush your 3D printer nozzle again with this Nozzle Scrubber & Purge Bucket.
zhlédnutí 67KPřed 2 lety
Never brush your 3D printer nozzle again with this Nozzle Scrubber & Purge Bucket.
Eliminate 3D printer plastic odor by building and installing the Nevermore activated charcoal filter
zhlédnutí 22KPřed 2 lety
Eliminate 3D printer plastic odor by building and installing the Nevermore activated charcoal filter
Small Parts Organizer and Storage, DIY via 3D printing
zhlédnutí 6KPřed 2 lety
Small Parts Organizer and Storage, DIY via 3D printing
Thanks! I printed it, built it, and it works great!
I know this is an old video but a tip for crimping the tiny terminals. -Get some double sided tape and leave the terminals on the reel. -Have two sets of tweezers and a magnifying glass. -Place the wires and the terminals on the tape. -Using one set of tweezers, press and hold the wire insulation into the large set of wings and use the othe set of tweezers to fold the wings over the insulation. -Do the same for the second row of wings/tabs. -Then you can break or snip the terminals free from the reel and finish with your standard crimping tool.
Working on building my ERCFv2 + Cotton Tail currently out of the TriangleLab kit. I will say that Siboor definitely did a better job with their kit - the flexible PCB to unify all the microswitches for the coupler blocks here, for one example, but also really organizing and labelling the kit. At certain points I had to bust out my calipers to make sure I had selected the right screws because TriangleLab just throws all the screws in a bag. I'm now hoping to find a video covering the entire process of soldering and setting up the LEDs for both the ERCF and the ERCT, because the manuals don't even mention how to wire up the LEDs for the ERCT or how you're supposed to chain them to the LEDs from the ERCF (as the BTT MMB only has one pin header for LEDs). Did you have any trouble with the support arms for the ERCT? I noticed in the CAD for them that there is barely any tolerance given to handle shrinkage, so I ended up having to shim the arms where the 3x M3x8 screws go in each in order to prevent the wheels from binding. The rabbit graphic also for some reason starts printing at Z0.4, and the bottom edges have a 45 degree chamfer, which caused me some problems. I ended up just modifying the provided STLs to be completely flat on the bottom to get rid of the chamfers and rabbit logo offset, and made the arms a bit wider to prevent issues with the wheels binding. Maybe my V2.4 isn't as tuned as I thought it was, but the support arm design definitely needs some work I think.
My support arms are a little rough when assembled. But they seem to work. My biggest complaint is the amount of space they take. And the flexible PCB, some people have received a standard not flexible version. I'm not sure which one I like better, but I ended up breaking mine by pulling out a microswitch by mistake. When I re-attached it, I never got a reliable reading again. When I get the followup video complete, I will show how I ended up soldering the microswitches with wires instead. FOr the LEDs. I used black filament and intend on mounting the ERCF to the back of the printer. All the extra leds did not make sense to me as I would not be able to see them. So I only mounted the front facing LEDs since those are the ones I would be able to see. I suppose if this was printed out of white or clear filament, the leds on the back side would be nice too. Thank you for posting and watching. I wish you a great build!
para configuracion en klipper varia?? si el motor de antes era un nema 17?
Sí, lo hace. Suponiendo que la cantidad de pasos sea la misma por revolución, deberá ajustar la corriente del motor paso a paso. Lo más probable es que ajuste la corriente a un valor mucho menor. Si usa el motor de 17 mm de grosor, probablemente entre 0,300 y 0,350. Si usa el motor de 20 mm de grosor de LDO, puede aumentar la corriente antes de que el motor se caliente demasiado.
Great video as usual. It's been a month since you posted on the ERCF. I hope it's not because your having issue with it working. I went ahead and bought an Anycubic Kobra 3 Combo which has support for 4 colors until the ERCF gets working without lots of fiddling. I was amazed at how much poop multicolor generates. The Anycubic generates way less poop than the ERCF and it's still too much. Plus it does not need those huge retract reel. Plus it has a built in dehumidifier. I am thinking the ERCF might be flawed by design/
The probalem I have been facing is the the ERCF, it's me! By mistake, I foolishly fried two canbus controllers on the tool head. One after another. Once I got it working again, I had to focus on some other print jobs I needed to complete. I also have a mounting/space problem. I hope to resolve that today and then I can get moving again on this project.
@@KapmansBasementWorkshop Yea that ERCF requires a lot of open space. Yours is 8 colors and that is a lot. Any interference could easily kill a print job. I am patiently awaiting your follow on video.
This is a "Fix" video for the Sovol SV06 linear bearings where the guy literally packs them with grease. I will find the creator and reply
czcams.com/video/lUvaA4fJWH0/video.html ---> He plugs the bearings with papertowels and then uses the rod to "pack" the grease in. 😎👍
Thank you for posting this!
3:13 whats the filament?
I used clear ABS for the shade. Black ABS for the base.
Thanks.
Thank you for watching!
Just finished your video series, thanks! I'm very visual so this helps fill in the confusion I may have when I hit a step and reading the Voron Manual.
Thank you. I wish you a great build!
Thanks a ton for these videos, I just got my V0 kit and waiting to finish printing parts before I finally install so I'm binging your videos in the meantime to get a feel for what I've got in store. Very detailed, nice tips, thanks! Man I am not looking forward to the Idler assembly lol
Thank you very much. Take your time and plan ahead for future mods since 1515 extrusion uses regular nuts. If you think you will attach an add on anywhere, look into how many are needed to mount the device and install the nuts now. Otherwise disassembly will be a future result. I wish you a fantastic build!
Hey, I highly recommend the filamentalist as a buffering system versus the ERCT. Makes loading, unloading etc much easier and the spools auto rewind!
I've been looking at it. I love the idea of the spool holder being the buffer vs having a spool holder and a buffer. I'm having considerable trouble with space and the current setup. Filamentalist would be a big improvement. I'm glad to hear it's working out well for you. Thank you!
I ran those for over a year. I saw no appreciable acceleration increase either. It did let the gantry sag more easily when the motors were turned off, leaving me to set the after-print park position at 350, 175 so the next QGL didn't take forever. What I did find was that, with the GE5C mod, I could support the gantry evenly high, loosen all the bolts to the gantry extrusions and let everything find it's relaxed position. Then tighten all the GE5C through bolts, and the rest of the gantry bolts. That made the gantry more rigid between the Z rails, and led to more accurate prints with better finish in the X and Y surfaces.
This is a good idea. I will need to give this a try. Thanks you!
Hi, I am also trying to figure out all this, and I still do not understand why people are so busy with 7000 accelerations if plastics such as PETG rarely support printing speeds greater than 90mm. and the flow limitation is almost reached. Well, you can get 150 there. But what is the point of such huge accelerations, it gives almost nothing in real time printing... what I don't understand? You can leave the acceleration at 4000 without all these complications and lose nothing. Is it because I print PETG, is the situation different with other plastics?
While the situation is different with different plastics, and flow rate can be limiting, each of these are seperate problems on their own. Flow rate can be increased with temperature and with high flow nozzles and hot ends. However, due to the tiny space available on a bed to reach the top speed on a print, the print head needs to accelerate to actually hit those speeds in that tiny space. There are calculators available online that can show you what acceleration you need to even hit those print speeds. So taking your case as an example, lets assume your hotend and extruder can actually hit 150mm/s. With your current acceleration, will it every actually hit that speed? And for how long? As acceleration increases, your hotend can hit that speed sooner and for a longer distance which greatly increases the overall print speed. Acceleration in many cases is the biggest factor in print times. Have a look at the acceleration calculator at the bottom of this web page (blog.prusa3d.com/calculator_3416/) and try some values. On a 200mm bed, if your acceleration is 300, printing a 200mm line with a sped of 150mm/s means you can never hit that speed for more than about 125mm. That also means that many of the smaller moves on that print will never hit that speed. Bump acceleration to 3000 and the printer can hit that speed for almost the entire move. And moves that are 5mm or larger will hit those speeds as well. Thank you for commenting and watching.
@@KapmansBasementWorkshop Thank you so much for that insightful response. I understand. The point is that the printer does not have time to gain speed on short movements. and in printing very often there are areas where even 150 mm will not be achieved. I see. Although the difference between 4000 and 10000 is not that much, but yes, the effect is there and it can be a goal. Thank you.
This may be a dumb question but it looks like it might be possible to scale this down to just two colors?
I think you can easily scale it down to 2 colors. I would probably add a few extra than you might need just for convenience. It can give you color choice without needing to swap filaments manually or also give you a choice of filament type. Being able to switch between ABS and PLA between different prints (for example).
I won't have sensorless homing anytime soon. How are the switches failing? You connect them in NC mode right, so if the switch has failed, it must register instantly triggered and prevent further movement, i would think? A little bit of a dumb idea but like... i guess i can just run a ground pad to the moving part and the stationary part can be a pulled up pad. Just a steel-nickel strip. Not ideal because that would have to be in NO mode.
This is an enclosed 3d printer. The internal temps get between 60c and 70c. I think that approaches the switch's operating limit of 80c. I also think soldering wires to the switch, if you are not quick enough about it causes some damage to the switch as well. The combination of the two means the switch doesn't last as long as I would suspect.
@@KapmansBasementWorkshop So here's a not-so-hot tip, you don't have to solder wires to switches. You can use fitting spade plugs. People less inclined to crimp can order endstop spade wire premade from various Reprap and Ramps suppliers. When using spade plugs, switches must be connected in NC (normally closed) mode. This way, if the connector degrades or the wires get tugged and fall off, the endstop is interpreted as triggered without actuation and should stop hazardous movement. But i say the hole in the switch terminal actually locks the spades pretty nicely! Also see Alex Kenis video Failing Switch Problem: Omron vs the Modern Mouse Circuit. This dude is excellent at building 3D printers, but this time he is talking about something else but it still applies. Thing is our endstop switches while different in size, they have the same type of internal construction and guaranteed also the same problem. In short, if you run a 32bit board with 3V3 IO logic voltage, the switch is operated outside spec on the current-voltage curve with either or both being too low. Normally, the switched power electrically causes an impact to oxide that forces it to flake off. If the current and voltage are too low, the switch experiences continued oxide growth. At elevated temperature, even within switch's operating range, the oxide growth is much accelerated. I also think switches should ideally be coated with a layer of deoxit d5 inside. See Applied Science: How Corrosion Inhibitor Protects Metal. Alex concurs, when i talked to him about it. There is a way to run switches harder, you can run them from 12 or 24V high rail. One side of the switch gets connected to this rail via a pullup resistor corresponding to a suitable current according to switch spec, and in parallel this same side of the switch gets connected to the microcontroller input via an 1n4148 standard small-signal diode, with the diode pointing away from microcontroller and towards the switch. The other side of the switch is tied to ground. Engage weak software pullup. This way when the switch is open, the microcontroller input is driven by internal pullup. The 24V rail would love to pull up the microcontroller beyond absolute maximum rating, but for that to happen the current would have to be flowing in the opposite direction of diode, which the diode prevents. However, when the switch is closed, the switch will successfully pull down the microcontroller through the diode, while the high rail and its resistor provides switch cleaning action. You can use this same high rail to logic voltage conversion trick with inductive probe as well, if you were to use one. Since you have failed to describe the failure mode, i mean whether switch fails open, fails closed, or fails no-contact, i don't know whether these approaches are applicable. I thought i wasn't too ambiguous but i guess i was.
How does it sound? Is there a material recommendation? Or a tpu gasket for the driver?
The driver came with a gasket. I simply used it. I used PETG for the filament. I was worried the driver might get a little hot during times of heavy use. I also like the PETG toughness. I think it sounds/feels great to accompany a desktop speaker system. It made a huge difference in bass response. I would describe the sound as very quick and tight. The driver I used might not be considered a strong candidate for a subwoofer driver by many, but I foound the cost/performance tradeoff amazing. I have 2 of these in use in 2 different rooms. They sound great.
I guess perfect is an enemy of good. I use (the) Ender 3 and had some issues with curvy print bed. And had to flatten it with bare hands, and later with aluminum sticky tape a metal ruler and a flashlight. I do not have probe, so my head ain't aching 'bout it. = ) I recently printed with no trouble, when I noticed, that actually the left side was lower for some reason, and the right side was quite near the nozzle. Wanted to check this after printed a couple of items and some had smaller holes than others. I saw slight imperfections on the first layer but it stuck alright, so I ignored this. So I corrected bed knobs after I noticed bed nonalignment. So my guess if it sticks it is flat = )
I've never been that lucky. But, If the bed isn't level, you run the risk of part of the 1st layer not sticking to the bed. Thank you for watching and the commentts!
Hey, at first I did not understand. But then... This is a clever idea, to touch some button with nozzle and then touch exactly same button with probe to get height difference.
It's very clever. It's so simple. I didn't really get it at first as well. But after I did not understand why this wasn't used by all printers. Thank you for watching and commenting!
This is usefull if you change nozzles alot. The main problem i see is making sure the nozzle is clean without user intervention. I replaced my Induction Sensor to a Clicky because changing between beds would mess up the readings, clicky works all the time
I used the similar Euclid probe. It worked great. Thank you for watching and the comments.
Hello, what do you use as a nozzle hight probe?
I use one of these: mods.vorondesign.com/details/t1DBVlcUBbdEK6habEsVzg you can get a kit if you like for about 5 or 6 dollars. It mounts right next to the bed. In the description I have links to the probe that mounts to the print head.
Hi, I am setting up a new Voron 2.4 r2 type printer, I am using a BTT M8P with a CB2, when everything is ok I would like to get started on the ERCF too but I already have the extruder in CanBus to connect to my M8P and I can't yet find a video that shows what to do in this case... I must directly put it in parallel with it, remove a 120ohm resistor, move it?
If you are using a U2C or the existing mcu with canbus capabilities, you need to one terminator on that device. In addition, you need a terminator on the oppposite end of the canbus. Most people will attach the terminator on the very last canbus device.
Also, if you are using the U2C, it's actually a small canbus all on it's own. Meaning each socket sits next to the other on the bus. So you can have a terminator on the last device connected to the green wire terminals and then run cables from each of the sockets to individual canbus controllers, all without terminators. It's pretty cool.
I’ve ran into some issues after noticing you are communicating with can. my printer does not have a can interface. I flashed katapult using usb instead can. I can see it listed as a katapult device when i search for it, but obviously nothing comes up on can0. Am i still able to set everything up and is e this board with usb only or will i need to get a can add on to use with my printer to be able to use the ERCF?
You can just install Klipper on the controller and not use canbus. The controller will appear as a second mcu that you will declare in the printer. Cfg file.
@@KapmansBasementWorkshop Thanks for the fast reply, I got it talking with klipper hat a few minutes ago. The selector is working, but for whatever reason my drive stepper is not working. Have checked the stepper it’s self if good. I’d like to check that is set as the right pins. in hawrdware it’s just mmu:MMU_GEAR_STEP. Where do i find what those actual pins relate to? I might try changing it to the 3rd drive to see if that solves it
UPDATE- found the code in mmu and changed it to drive 3 and now it works fine
@@JacobBlocker Cool. I’m glad you got it working.
is this for a specific printer or any printer running klipper?
It should work for any printer running Klipper.
You can also add 2 x 80 mm fans at the bottom of the case to help with cooling. There is a lot of options now to optimize cooling with this case.
I agree. I did have fans in those positions at one time. But with later upgrades removed them. I've been slowly eliminating fans over time...
Now you have an option to use - A Thermal Grizzly - Carbonaut - Carbon Thermal Pad inplace of thermal grease / paste. The thermal pad won't " Dry - out " and can be reused many times.
Has it been working well for you?
@@KapmansBasementWorkshop Using the Carbonaut - Carbon Thernal Pad has been working well so far. I am considering getting a couple more for my GPU. Not sure how beneficial it wold be though
Nice video. You can remove the dual 3 and 1/2" drive bay that supports the quick insert and release to allow more space for the PSU and cables. I have done this myself and using my Seasonic PRIME TX-1600 ATX 3.0 psu has been nice.
I also installed a hotswap bay which added an additional drive bay as well.
@@KapmansBasementWorkshop I took that drive bay out - to make more room for the cables from the PSU. Sorry for any confusion.
No problem. This is what's so great about this case!
Did you encounter any issues fitting the Board into the PCB Holder? Mine seems to be to tight on the left/right and the screw holes are also not fully aligned. Up to now i did not encounter serious issues with accuracy on other parts
I did have a problem in that part warped during the print as ABS loves to do. It doesn't fit perfectly, but it does fit. In my case, due to the warp, the cover for the PCB won't snap on nicely. I will try to reprint that part later.
First off, great series! I was just wondering if you plan on posting a video of calibrating and testing the system? Also i have followed one of your older videos on sensorless homing, and was wondering does the filametrix work with sensorless homing?
Please note when you release the final part that not all SIBOOR kits are created equally. Myself and several others had a rigid PCB pre-gate board which has been known to cause problems (false gate reporting) and while some kits have WRGB LED's others use RGB only. I would make sure people understand what version of the kit your configs are for, if you still plan to release! I have the WRGB rigid pre-gate board version and I am having a ton of issues.
I do plan on releasing another video to conclude this. However, I fried my SB2209 by mistake. Waiting for it's replacement. About the PCB, I ripped out a microswitch by mistake. It just pressed back in since it wasn't soldered. But that microswitch and each surrounding it became unreliable. I pulled off the circuit board and soldered wires instead. Rock solid. I recommend following the manual on cutting the wire lengths and soldering. In the long run, it saved alot of time! In the last video, I plan on covering this as well.
You could probably use the GND and 5V from the reserved STP sockets (STP1 & STP2) for the extra LEDs and, as you said, solder the signal wire in series at the end of the LED strip. Unfortunately, the RGB socket pin (PA2) looks like the only one capable of PWM (apart from the motor PWM pin, PA0), which LEDs need. Siboor missed a trick here to make this a bit easier by putting another connector block at the end of the strip. I'll probably not bother with the coupler block LEDs but the selector one may help troubleshooting in operation.
Actually, the selector LED cable passes through the cable chain since it needs to accommodate the entire length of the ERCF so the connections have to be made at the MMB end, which means the selector LED needs to be the first in the chain but in series with the LED strip otherwise it will be the same colour as LED0. This isn't straightforward at all unless Klipper can do a software PWM on pins PA3 & PA4 to keep the LED chains independent. Klipper can do software PWM on the MCU so it depends on whether the MMB is capable. It should be.
I ended up just using the led pcb. Looking at where I was going to indtall this and because I used black fillament, I decided to not use the other LEDs. Thank you for this tip!
If you try to use "CTRL + V" to paste in a terminal on Linux, you will get that wrapper around whatever you are trying to paste. You can use "CTRL + Shift + V" to paste correctly.
I did not knnow this. Great tip. Thank you!
Guten Morgen, haben sie das mmb 1.0 Bord oder das mmb 1.1 Bord verbaut??
Guten Morgen! I believe I have the 1.1. But I need to remove it to see the back side to be completely sure....
Don't screw the microswitch board in until it's assembled. Assemble the support arms, buffer wheels and spacers and screw the support arms together one at a time. Once that's done there's enough flexibility between them to fit the coupler blocks if you start at the MMU end. Then add the ball bearings and microswitch board.
Thank you for the tip!
Hi, I probably sound dumb, but I want to be sure I know what I'm buying. Does Siboor ERCF V2 kit include 3D printed parts? From my understanding it doesn't which isn't really an issue, I just couldn't find it written anywhere.
It does not. You will need to print those parts by yourself. Thanks for posting!
Did you get this 8 neopixel PCB to work correctly? I have also built the siboor kit. After the installation it was reversed with the basic configuration in my case. A simple change from 1-8 to 8-1 made the whole thing even more confused. Now I've been playing around with the mmu_hardware.cfg for days but nothing useful comes out of it and I'm beginning to think it's a hardware defect. Basically there shouldn't be much to it, I only use the 8 neopixel PCB like you in the video. mmu_num_leds -> 8 mmu_num_gates -> 8 exit_range: 1-8 / 8-1 No status_index I also played around with the color_order, also without success
I did get it working. It took a few tries: [mmu_leds] num_gates: 8 led_strip: neopixel:mmu_leds exit_range: 8-1 #entry_range: 9-{mmu_num_leds} status_index: 9 frame_rate: 24 also: [neopixel mmu_leds] pin: mmu:MMU_NEOPIXEL chain_count: 9 # Number gates x1 or x2 + 1 (if you want status) color_order: GRBW I believe that was it. If not, I can dig a little more.
@@KapmansBasementWorkshop Unfortunately, the config does not work for me. I have also tested the 8 Neopixel cable, but this does not work at all. What I find strange with the Neopixel PCB is that when I deactivate it or switch from status to filament color, the number, position and color of the LEDs change with each switching. There is no consistency. But maybe there are kits with different hardware in circulation, my Microswitch PCB for the Coupler Blocks is also solid and not flexible like yours.
@@Heyde84 Seems the kit might have changed. But I've always had these led strips work the same way, except if when 3 or 4 colors. Hmmm.
bonjour , très bien expliquer merci pour les informations
Merci beaucoup!
I love watching this. Thanks!
Thank you for watching!
Question for you that will help me orient to this video. I've noticed that people use two strategies getting the CanBus signal sent. Strategy 1) "Raspberry pi" connects via USB to "Printer MCU board" (ie, Octopus 1.1), then use the canbus out plugs on that MCU board to send CanBus to your ERCF. Strategy 2) "Raspberry pi" connects via usb to "Printer MCU board" to control printer generally. But the pi also connects with a second USB cable to a "USB to CanBus Bridge board" (ie, BigTreeTech U2C adapter board). Then you connect you CanBus cable from that bridge board to your ERCF. I know both of these strategies work - which is this video using? (my hunch is it's strategy 1, but I'm unclear) Thank you!
I'm actually using Strategy 2. My U2C is pre-exisitng since my 2.4 alrady has canbus installed for the printer tool head that is using an SB2209. There is a 3rd way too.... Strategy 3) Just use USB and a power cable and don't use canbus at all. I have never tried that before, so I can't give good guidance here. I believe the Esoterical website covers that if you want to try that. Thanks for watching!
Is this using a canbus board like a btt u2c or is it using the canbus on something like an btt octopus?
I'm using a U2C. My MCU is a Spider 1.0. I also use a SB2209 over canbus in the tool head (installed previously).
Where did you get the stl for the led pcb? I cant seem to find it...
It's right here: github.com/Lzhikai/ERCF-V2-Accessories Thanks for watching!
@@KapmansBasementWorkshop Great! thanks
Use zippo lighter fluid (naptha) to remove the glue residue
Thats a great tip. Thanks!
Hi man. Thx for all nice videos. Im also building an Siboor ERCF V2. One question that popped up for me was how do they think about the bypss channel. I have the filament coming in right from the electeonics box area. Not clear how they think here!!??
I have not used that yet. But Siboor didn't design that part. Ask the ERCF discord channel. I'll bet someone knows the answer there. Thanks for the kind words and watching!
I got to 4:50, and got a error. I think it's something about an updated version or something. For anybody else who had the error, please help. I have no idea what I'm doing.
Please copy the message you get and post it here.
I don't have the uuid from katapult though. I don't know if that's important.
@@alexlikesallthegamez Please paste the error message you are getting here in the comments.
ERROR:root:Can Read Error Traceback (most recent call last): File "flash_can.py", line 137, in send_command ret = await self.node.readuntil() File "flash_can.py", line 287, in readuntil return await asyncio.wait_for(self._reader.readuntil(sep), timeout) File "/usr/lib/python3.7/asyncio/tasks.py", line 423, in wait_for raise futures.TimeoutError() concurrent.futures._base.TimeoutError
@@alexlikesallthegamez Are you using a U2C?
If you run into the issue where all the pre gate sensors come up as triggered when running the mmu_sensors command in the console, the issue I found was all the holes where the bearings dropped in had a little bit of an overhang issue causing the bearings not to fully seat which then in turn caused all of the switches to be pressed. Also easiest way to install the pcb is when the buffer is put together.
Thats a good tip. I ended up ripping one of the microswitches off the PCB by mistake. I pressed it back in, but once hooked up, both it and the switches aroound it were unreliable. I ended up pulling the PCB off and soldered wires across the microswitches. I will show it off in the next video. Thank you for posting!
@KapmansBasementWorkshop I just ordered a pcb set from siboor so I didn't have to solder my wire management needs some work
Which STL did you download to use this BMG clone? They have a "micro standard r2" and "micro fixed alpha 1".
I don't remember both those being there. I believe I went with "micro standard".
Thank you for putting this together ❤
Thank you for the nice comment and watching!
@@KapmansBasementWorkshop I have been meaning to understand how ercf and similar mmu systems work. I recently completed my first voron and a trident and looking to expand more on its functionality so trying to understand mmu and toolchangers
@@sanketss84 Well, I'm actually doing the same thing as you!
@@KapmansBasementWorkshop what I wanted to do was automate filament change with just two spools. for that I needed a way to synchronize another motor with extruder motor which will pull/push the filament from the bowden on filament change macro. this motor will disengage during normal print with the help of a stepper mechanism. hence I was trying to understand the mechanism of 3d chameleon , ercf v2 and trad rack and spin my own simplistic version which would work just for two spools.
@@KapmansBasementWorkshop this system will be cheaper than an idex or dueling dragons or tool changers as they have other headaches of managing the kinematics and taking apart the belts and also programming the usage of multiple toolheads. and add to that nozzle alignment.
Does happy hare have some discord or community for discussions , this is quite neat and very well put together.
I could not find one. The only thing I can see is his Github. I agree with you. The software is an amazing package. A lot of work went into it. I will send some funds his way via the link on Github.
So weird that this solution is hard to find. Even where it is discussed on reddit, no one bothers to post the actual 3 lines of text.
Thats the issue I ran into. I figured it can't just be me. I hope it's helpful to you!
Thanks a lot for the video. Do you have any tips on how to manage the sherpa motor wires? The ones that came with mine seem really fragile, and the fact they're not bond together makes me think they'll snap or tangle somewhere with time.
I only have one piece of advice. I built a secoomd one and I needed to trim and strip the ends of the motor wires. It ripped the wire right out of the motor and there really is no way to service the motor. I had to purchase a new one. So be careful with stripping the wires! Other than that, once trimmed, terminated and connected to the controller, no trouble at all. These have been very reliable motors. And I really like the extruder!