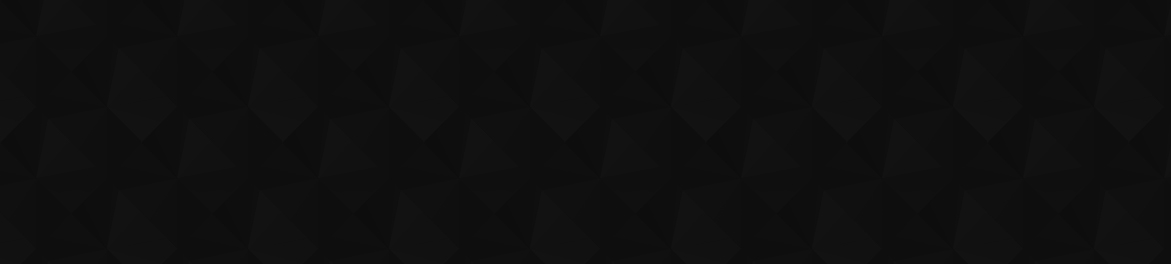
- 77
- 5 516 857
ROBRENZ
United States
Registrace 10. 06. 2008
Sharing my adventures in machining and engineering.
I am "robinrenzetti" on Instagram where i have lots of similar content.
I am "robinrenzetti" on Instagram where i have lots of similar content.
MAKING A BETTER ADJUSTABLE TIR LATHE CHUCK
Making an adjustable TIR lathe chuck from a standard 3 jaw chuck and backing plate. Showing a way to stiffen the chuck body and load the chuck body in compression using a needle thrust bearing arrangement. Callibrated adjustment screws allow precise adjustment moves.
#practitioner_of_the_mechanical_arts
Paypal donation www.paypal.com/cgi-bin/webscr?cmd=_s-xclick&hosted_button_id=W64WRAAGMA79J&source=url
Support through Patreon www.patreon.com/ROBRENZ
#practitioner_of_the_mechanical_arts
Paypal donation www.paypal.com/cgi-bin/webscr?cmd=_s-xclick&hosted_button_id=W64WRAAGMA79J&source=url
Support through Patreon www.patreon.com/ROBRENZ
zhlédnutí: 84 095
Video
LATHE CHUCK MAGIC TRT#5
zhlédnutí 80KPřed rokem
How to get optimum performance of a lathe chuck by properly loading the jaws before boring or grinding the gripping surfaces. #practitioner_of_the_mechanical_arts Paypal donation www.paypal.com/cgi-bin/webscr?cmd=_s-xclick&hosted_button_id=W64WRAAGMA79J&source=url Support through Patreon www.patreon.com/ROBRENZ
MAKING ULTRA PRECISION TOOLROOM SPINDLES #2
zhlédnutí 91KPřed 3 lety
Part 2 showing rotary grinding of the hardened parts. Discussion of many aspects of precision grinding in general. Showing my automated Harig grinder in action doing rotary grinding cycles. #practitioner_of_the_mechanical_arts Paypal donation www.paypal.com/cgi-bin/webscr?cmd=_s-xclick&hosted_button_id=W64WRAAGMA79J&source=url Support through Patreon www.patreon.com/ROBRENZ
MAKING PRECISION GAGE BALLS
zhlédnutí 403KPřed 3 lety
I show making high precision gage balls from ultra micrograin carbide with normal machine shop tools. Includes rough grinding, lapping, polishing and measuring to very high levels. Hertzian contact deformations are discussed including calculations. 0.000005" = 0.127µm (not nm) #practitioner_of_the_mechanical_arts Paypal donation www.paypal.com/cgi-bin/webscr?cmd=_s-xclick&hosted_button_id=W64WR...
DIY SURFACE PLATE LAPPING PART 2
zhlédnutí 85KPřed 3 lety
Final lapping of the surface plate to just get to the AAA tolerance. I show aluminum foil lapping and grooving and scraping in the lap used for final finishing. Measuring surface finish of Starrett AAA granite plate to determine the surface finish they thought appropriate. Lastly showing the construction of the lap I think will be ideal for future refinement of the plate to even tighter toleran...
MAKING ULTRA PRECISION TOOLROOM SPINDLES #1
zhlédnutí 104KPřed 3 lety
First of a series of videos on making ultra precision toolroom spindles. These are designed to have les than 0.000005" runout and very high stiffness. General design and machining before heat treatment is comvered in this video. (I said 75 divisions in the video, it is 72 divisions for 5 degree increments.) #practitioner_of_the_mechanical_arts Paypal donation www.paypal.com/cgi-bin/webscr?cmd=_...
MAKING AN AIR TOOL CHAMFER ATTACHMENT
zhlédnutí 42KPřed 4 lety
Design and construction of a chamfering attachment for a Dotco 60000 rpm air tool. #practitioner_of_the_mechanical_arts Paypal donation www.paypal.com/cgi-bin/webscr?cmd=_s-xclick&hosted_button_id=W64WRAAGMA79J&source=url Support through Patreon www.patreon.com/ROBRENZ
AUTOCOLLIMATOR MIRROR SYSTEM
zhlédnutí 69KPřed 4 lety
Brief description of how an autocollimator is used to measure straightness and flatness. Followed by my mirror system design and construction details. #practitioner_of_the_mechanical_arts Paypal donation www.paypal.com/cgi-bin/webscr?cmd=_s-xclick&hosted_button_id=W64WRAAGMA79J&source=url Support through Patreon www.patreon.com/ROBRENZ
BRUSH IN CAN MAGIC TRT#4
zhlédnutí 31KPřed 4 lety
My fix for the typical ugly brush in can scenario. #practitioner_of_the_mechanical_arts Paypal donation www.paypal.com/cgi-bin/webscr?cmd=_s-xclick&hosted_button_id=W64WRAAGMA79J&source=url Support through Patreon www.patreon.com/ROBRENZ
THE MAGIC SANDING PLATE TRT#3
zhlédnutí 49KPřed 4 lety
Details about my sanding plate and its uses. #practitioner_of_the_mechanical_arts Paypal donation www.paypal.com/cgi-bin/webscr?cmd=_s-xclick&hosted_button_id=W64WRAAGMA79J&source=url Support through Patreon www.patreon.com/ROBRENZ The 12" wide x 25 yard roll of 220 grit Silicon Carbide paper available from Abrasives South Inc. 1-800-255-8112 #18014 abrasives-south.com/product/roll-12x36-220-gr...
CNC PLUS OLD SCHOOL
zhlédnutí 50KPřed 4 lety
Using the CNC mill to do an old school metal removal technique. #practitioner_of_the_mechanical_arts Paypal donation www.paypal.com/cgi-bin/webscr?cmd=_s-xclick&hosted_button_id=W64WRAAGMA79J&source=url Support through Patreon www.patreon.com/ROBRENZ
MAKING GROOVING BORING BARS
zhlédnutí 190KPřed 4 lety
Making a group of carbide tipped grooving boring bars. CAD design is covered as is a method for repeatable location of the bars in making them and using them. Lots of grinding setups and non typical lapping techniques. The boring bar shanks are ground out of hardened dowel pins. #practitioner_of_the_mechanical_arts Paypal donation www.paypal.com/cgi-bin/webscr?cmd=_s-xclick&hosted_button_id=W64...
ROBRENZ TOOLROOM TIP #2
zhlédnutí 38KPřed 4 lety
#practitioner_of_the_mechanical_arts A modification to a standard grinding wheel hub to allow precise gripping of superabrasive wheels after indicating in the wheel OD. And a indicator protector to directly indicate on the abrasive surface of the wheel. A how to on dressing super abrasive wheels with Molybdenum rod. Paypal donation www.paypal.com/cgi-bin/webscr?cmd=_s-xclick&hosted_button_id=W6...
MAKING AN INSERT BORING BAR
zhlédnutí 371KPřed 4 lety
Making new insert heads for carbide shank boring bars. design and execution details are covered in detail. Method for repeatable quick change of multiple parts is shown. Custom D bit cutter creation for the insert pocket. #practitioner_of_the_mechanical_arts Paypal donation www.paypal.com/cgi-bin/webscr?cmd=_s-xclick&hosted_button_id=W64WRAAGMA79J&source=url Support through Patreon www.patreon....
TIPS ON PRECISION SPINDLE REBUILD
zhlédnutí 662KPřed 4 lety
Spindle rebuild of my Trak mill. I cover many details about spindle rebuilding and spindle design. #practitionerofthemechanicalarts I am "robinrenzetti" on Instagram link to Timken Fafnir catalog www.timken.com/wp-content/uploads/2016/12/5918_Machine-Tool-Catalog.pdf Paypal donation www.paypal.com/cgi-bin/webscr?cmd=_s-xclick&hosted_button_id=W64WRAAGMA79J&source=url Support through Patreon www...
DIY SURFACE PLATE LAPPING ANSWERS TO PART 1 QUESTIONS
zhlédnutí 35KPřed 6 lety
DIY SURFACE PLATE LAPPING ANSWERS TO PART 1 QUESTIONS
DIY SURFACE PLATE LAPPING PART 1 (audio fixed)
zhlédnutí 144KPřed 6 lety
DIY SURFACE PLATE LAPPING PART 1 (audio fixed)
TORMACH SLANT PRO 34 SECOND PULLEY CHANGE
zhlédnutí 16KPřed 6 lety
TORMACH SLANT PRO 34 SECOND PULLEY CHANGE
I can tell you I would much rather sit through this than the movies coming out these days. About the same runtime, some really cool suspense followed by utter satisfaction with the bearings that just shloop on like that. Busy rebuilding my own spindle on a 1990s Pinnacle Mill that one of the previous owners tried to convert to cnc that didn't go too well. The information you just gave me saved me quite a few bucks, so, thanks.
I like to look at it as the 12 face method, not 3 plate method. 3 plates rotated 90 degrees in all combinations of of the 3 plates gives you 12 different faces to rub together. 4 directional faces each on 3 plates. Making a straight, flat edge is then quite more possible by rotating axially and longitudinally around the faces of rectangular stock. With the minimum requirement of at least 12 faces it can be done with one rectangular piece of stock and 2 squares of equal length. the squares can be rotated axially and flipped longitudinally for a total of 34 faces. you can obviously keep your "sacrificial" square stock to make more if you need to.
I so enjoy your channel. You even answer questions after 7 years of posting a video. Who does that? For no money either! Robin you are the man. God bless.
Glad to help
I like your consideration of details for precision. How accurate is your thermometer?
Fluke 8846A 6.5 digit.001 degree C resolution +/-0.08 deg C accuracy
Chuck, my pimp. I had to say it. Awesome video Rob. Thanks for sharing.
Creative and uber precise Robin. Thank you for sharing.
I'm not an expert on cars by any means. But I've built a thousand of them.
Such unique video content. Could you please share which wheels you used on the HARIG for this job pleas Robin. You mention 60 grit and it looks very open structure. Would that be a Radiac wheel , similar to those liked by Steve Barton ?
Yes
this is crazy
phenomenal. True mechanical engineer with practical experience.
Of course I watched it to the end. Ok so you’re not in a clean room. Clean rooms have tolerances also. “Everything is made of rubber”👌I love that saying! I greatly enjoy your attention to details that most don’t know, understand, consider or appreciate. It is impressive watching you measure things to sub micron levels in your garage. When someone brags to me how absolutely perfectly precise they made something I point them to your channel. And then I explain about how atoms have radiuses and so do neutrons. One of my pet peeves is how some routinely over use absolutes in everyday conversations. I appreciate your consciousness to such terms. Waiting for your next video.
It's crazy just your breath changed the shape of the level. I found your channel a few days ago and I can't stop watching. Please make more videos!!
I thought you were getting a little picky when using a counter weight on the level, I was surprised how much it made a difference. Great video and channel!
11 years, and I'm just learning this? Amazing sir, absolute fantastic information.
New subscriber here got put onto this channel via @StefanGotteswinter... Great content and Prost from Germany!
Thanks and welcome
Where has this CZcams channel been!? How have I not been here before ? New sub…. Lets go!! MACHINING FOR THE WIN!
It's like that carnival game where you have to shoot the red star out of the paper, also looks like you'll never quite get 100% here either.
Saying a prayer for part 3 🙏
The bearing with a taper outer race use to be called a WI bearing because the INNER was WHOLE = WI Great job. Might mention that the preload is set from the factory. Some mechanics believe you set the preload with the nut. Not if it is assembled correctly. The preload from the factory can determined by your RPM range.
Thank you!
thanks god, there are still people on this platform explaining some real stuff
OLÁ 14/08/24 Apenas uma sugestão: Descubra "o porque" não se lubrifica as roscas nem arruelas de parafusos. Roberto Udo Krapf
I like it. I have never done this but I am sure in the future I will. I can see all sorts of useful variants of this...
So awesome.
Stefan is still working on his, LOL Yall do good work!
Buck chucks are good tools to have. I have seen the distortion you have shown, my approach has always been to loosen all the adjusting screws and move only the one I need to move it in the direction I needed it. Then loosen it again and adjust the others as necessary until I get it running as needed. Always loosen them after adjusting them. Once the chuck is adjusted where it needs to be I snug up all the screws, one side then the other mindful to be deliberate to not skew the results.. Do this to secure the chuck in position being careful to avoid distorting the chuck while maintaining the concentric adjustment. Done it this way for the past four decades I machined and always teach others this method. This method works well and is quick. Nice chuck you have masterfully built thank you for the video.
Found lots of good information here. I'm making my own version of this tool grinder, and I got a good idea of how to design mine using what I got, except I bought the main arm/tool holder and a 25mm polished rod everything else is going to be made or salvaged stuff and raw metal. deciding what are good features to include in my design since its final shape is still very flexible. also, I have parts off a small bench drill press I will use. Is it useful to have a height adjustment on the grinding wheel? and a feed in and out on the wheel spindle? and is it useful to have angle adjustment in both x and y axis for the wheel?
As you can see from my profile picture I managed to buy a Hilger & watts TA1-5 DIV 0.2 arcseconds here in the UK but finding the precision mirrors for it can be very challenging so making one is the only option I have. When mounting the first surface mirror to the sled with adjustable nylon screws is it necessary to align the mirror perpendicularly to it’s base feet? if so how can you do that with the highest level of precision? Would you need to pitch lap a thick piece of glass to λ/20 to then have a dead flat surface so you can reference from to then get the mirror perpendicular? Any help would be greatly appreciated 😁
Hello Robin, my comment is not specific to this video. I just wanted to thank you for sharing your knowledge and especially your thought process during your projects. When I first found your channel (Stefan Gotteswinter recommended you) I basically did not understand anything you explained or did ... it just was way to advanced for me. Well the virus caught me and I bought a lathe, mill, surface grinder, d-bit grinder, and lots and lots of tooling. Basically watched all the videos from Stefan, Tom Lipton, Joe Pie, This Old Tony and so on (sure I forgot some channels) and then again stumbled upon your videos and finally managed to understand most of what you said. Its a real pleasure to watch your videos and I learnt a lot by doing so multiple times ... even if machining is just a hobby to me it has become an important part of my life for me and thats mainly because of you and Stefan. I think you are improving the life of a lot of people. Keep on turning :-), ATB Stefan
Robin, this is the second time that I've watched this video -- after Stefan mentioned it in his "Toolgrinding: Radius Groove Inserts" video (July 2024). I think that I'll need to manufacture a similar mount for my shop, even though I'm not a content creator. You're either a degreed Engineer or easily put many to shame with your knowledge and skills! I hope that you are well and haven't posted recently because you are simply too busy with your business to film & edit videos. I miss your videos though! ;)
Very cool positioning system you've come up with Robin! The forethoughts in your design process is amazing. Thanks for sharing
Buy nice or buy twice
this is the equivalent to a therapy session for a recently graduated precision mechanic apprentice. Thank you for your video
we made a dozen sets at work. they work great. it was a great upgrade from standard stones.
With respect to your surface preparation at 15:15, what do you think about Dan Gelbart’s favored surface prep of using Ajax to clean surfaces before finishing (covered in his powder coating video I believe)?
Please post more !
I never cared for the moore pattern scraping. I think it addresses problems that are best handled otherwise. Form(flatness usually)is usually the paramount goal and moore scraping does achieve that but at a cost. Bearing texture is also required in may sliding parts and again Moore scraping achieves that after a fashion but again, at a cost. Whitworth's scraping method achieves flatness as well or better and is faster. The Whitworth method can also achieve a good bearing surface if desired. We are 200 years past Whitworth's work and still have not evolved the process , in fact it has devolved into a search for "points". Whitworth was not trying to get "points" he was trying to get as flat as possible, points were just a by product of his method but they happened to provide a great bearing surface at the same time. The ideal surface for a bearing is to be dead flat, dead smooth and scientifically textured for lubrication and debris removal. We are not doing a good job of that with current scraping methods.
On what basis are you making these statements? Moore pattern scraping is widely accepted as best practice by people who would know
@@JohnMaxGriffin It is explained in my comment. The Moore mystique is based on the performance of the excellent machines they made and some associate that scraping method as the reason, it is not. Equal or superior results can be had by using the original Whitworth methods. Especially if you apply modern tribological knowledge to the surface texture. The Moore pattern requires a lot of practice and gives results only equal to other common methods. The only real benefit is that you can claim it is "Moore pattern" scraping. Its main benefit is leaving minimal burrs but mainly is merely ornamental. The accuracy is no better than other methods.
@@billshiff2060 Again, I'm asking for actual empirical evidence for what you're saying. You've said a bunch of stuff and given your personal opinions, but without providing the basis for those opinions. Where's your evidence that the "original Whitworth methods" are superior?
@@JohnMaxGriffin I have nothing to prove to a knowsitall/knowsnothing bystander. My comments are only for those with ears to hear and eyes to see. I've given you enough bread crumbs that you could follow it up and make up your own mind with all the facts but you have allowed your mind to be made up for you.
@@billshiff2060 Ok, so just another case of a CZcams comments guy with big claims and nothing to back it up.
Re-watching I am getting more and more ideas. I don't really need a set-tru chuck but stiffening the system with two bolt patterns is a game changer IMO. In fact a thing I have been irritated by is the fact that on the chucks I currently use, chips get caught in the annular space between the backing plate and the chuck. It gets worse because the type I have has a keyway. I was thinking about somehow filling up the space with a sealant or something but that would be so permanent it would be a huge hassle when the chuck would need disassembly. Right now I am always taking the chuck off the backing plate when swapping them. Now, I think there is a great opportunity to kill two birds with one stone. First, make a thicker chuck end/ stiffener plate that lines up with the outer mounting surface of the chuck, so there is no shoulder anymore. Then, post-machine the two in assembled condition and add bolt holes as required (for front mounting if that is not already the case). Then, machine the backing plate adding the threaded holes and get rid of the stepped shoulder. Next, mount the to together and indicate on the lathe to run dead center. Take the assembly to the drill and add to conical dowel pin holes. Add dowel pins for future alignment. For disassembly, dowel pins with internal threads may be used for a slide hammer or threaded holes may be added for pressing the pieces apart with screws. When all is done bore the (hard) jaws as is now well known. Notes: - The chuck end/ stiffener plate does not need to be an interference fit per se when the set-tru feature is not added, however I feel that it will only add to the stiffness. The plate may also be fitted with screw holes for push-off disassembly. - Making the end face of the chuck flat will make it very easy. After all making two parts with the same axial dimension on two shoulders is over-constrained by definition, with the set-tru feature it is necessary but pretty advanced skills and equipment are required to do it right.
Dear Sir Robrenz, I am Abay from Ethiopia. First of all, I thank you in advance for taking your precious time to consider my request. Could you please assist me in order to rectify 'ZANROSSO 1500Y Cylinder Block and Head Resurfacer Machine, which is giving a hyperbola surface finish. Deviation ranging 0.15/.1 mm. I couldn't even find the manual. Previously, four times other Technicians have tried to solve the problem but nothing pays off yet. Now it's my responsibility to bring the machine to life and before I attempt to start working on the Resurfacer , I humbly seek assistance. Thank you so much. I am also addressing this to anyone who come across to this comment of mine.
is it possible to generate pulse with the help of this one in pA (cuurent as source)
Hey Robin! @ 49:53 you spoke of the twisting and flex forces on your stick-out piece. We-all have this problem. Where are your HD extended jaws for the Kurt vice? Half-ass Ross uses his often in his 2 car machine garage.
2nd time I've watched this. I always learn something new with you. Thank you for your time and sharing your knowledge!
Glad it was helpful!
just watching this as i bought a u3 version yesterday for 500euros with all the accessory's and a full 5c collet set from 1.5,2,3,up to 30mm as it was the last one and they now only have the u5 which is as far as i could see the same machine.but cost 899.
What type of hardened linear shafting did you replace the original one with? Did you get it from McMaster also?
Metric linear motion shafting from McMaster
@@ROBRENZ Thank you for the reply. I meant which type of steel would be the best for this - for a 25mm linear shaft McMaster has 1055, 1566 Carbon Steels, 52100 Alloy Steel, and 420 Stainless Steel. I'd guess that the 1566 would be the best because it seems to have the highest hardness and also the best straightness tolerance and surface smoothness ratings. Probably I am just splitting hairs here and they are all better than the original though.
The quality of parts/work that gets cranked out on this channel is top fkn class!! Gives us a real insight into how engineering actually practically playes out when high tolerances are required! Even tho i have done some highly accurate work myself ik constantly suprised and learning new things with ROBRENZ!! LOVE IT!!
I have a 1/2" CBN wheel I wonder if it will work?
Yes but not a good as diamond
Incredible again Robin. Thank you👍👌🇦🇺
Glad you enjoyed it
Love the math at the end.
Should doing this cause rust to develop faster? Lathe is 6 months old and I keep getting surface rust showing up. After using coolant I will blow all the ground surfaces down and then wipe clean off using wd40. A day later with no use I will notice rust that stains into the surface
I have had wd 40 make things rust. I use light machine oil or even olive oil
Sir, As an engineer, I can say that you are a spindle expert, just one of the various types!
HA - a couple of minutes in and you said, correctly, 'orienting' not the far more usual incorrect, and very irritating 'orientating'. Well done you!