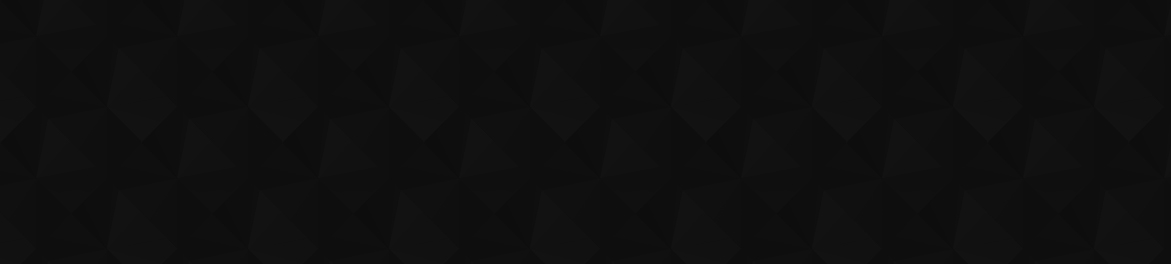
- 202
- 613 244
Klingberg Wing MkII
United States
Registrace 7. 05. 2017
On this channel I will display and discuss all of the development work related to the Klingberg Wing MkII. Subscribers will be able to follow all the engineering and construction work to complete the first full size prototype aircraft. There will be extensive discussions and demos of composite construction methods used to create very high to strength weight ratio structures. Videos will also include special aerodynamic discussions related to flying wings. All content of this channel is intended for entertainment purposes only. All of the information presented here is experimental in nature and there is no promise, express nor implied, that any of these methods or designs will result in successful aircraft or components. Anyone who becomes a Patron at www.patreon.com/klingbergwing will receive a free set of plans for the 1/4-scale R/C glider.
Flight Test Results and Glass Cockpit - Klingberg Wing MkII Development
This channel presents key activities related to my development of a new, 15m span, foot-launchable sailplane.
zhlédnutí: 274
Video
Slotted Control Surface Version 2 - Klingberg Wing MkII Development
zhlédnutí 460Před 2 měsíci
www.patreon.com/klingbergwing buymeacoffee.com/klingbergwing This channel presents key activities related to my development of a new, 15m span, foot-launchable sailplane.
Slotted Flap Test Results - Klingberg Wing MkII Development
zhlédnutí 251Před 2 měsíci
www.patreon.com/klingbergwing buymeacoffee.com/klingbergwing This channel presents key activities related to my development of a new, 15m span, foot-launchable sailplane.
Flow Separation Primer - Klingberg Wing MkII Development
zhlédnutí 1,6KPřed 2 měsíci
buymeacoffee.com/klingbergwing (Goes to gasoline) www.patreon.com/klingbergwing CFD Analysis Video: czcams.com/video/2mh8szvuD40/video.html Flap Plate Elevon Testing Video: czcams.com/video/cIrFkrkYI64/video.html This channel presents key activities related to my development of a new, 15m span, foot-launchable sailplane.
Slotted Flaps, a New Way - Klingberg Wing MkII Development
zhlédnutí 3,4KPřed 2 měsíci
Help support the test program: https: buymeacoffee.com/klingbergwing www.patreon.com/klingbergwing Note: Please post in English so the maximum number of people (including me) can benefit from your thoughts.
Making Compound Curved Composite Shapes - Klingberg Wing MkII Development
zhlédnutí 375Před 3 měsíci
This channel presents key activities related to my development of a new, 15m span, foot-launchable sailplane.
KW MkII Development - Composite Sandwich Panel Experiments
zhlédnutí 320Před 3 měsíci
This channel presents key activities related to my development of a new, 15m span, foot-launchable sailplane.
Side Quest - Original Klingberg Wing (KW MkI) Structural Design - KW MkII Development
zhlédnutí 716Před 7 měsíci
This channel presents key activities related to my development of a new, 15m span, foot-launchable sailplane.
Reynold's Number Issues? - an Analysis Part 1 - Klingberg Wing MkII Development
zhlédnutí 291Před 7 měsíci
This channel presents key activities related to my development of a new, 15m span, ultralight sailplane.
Dihedral Effect Side Quest - Klingberg Wing MkII Development
zhlédnutí 306Před 7 měsíci
This channel presents key activities related to my development of a new, 15m span, foot-launchable sailplane.
Re Number Issue Part 5, Final Segment - Extended Elevon - KW MkII Ultralight Sailplane Development
zhlédnutí 362Před 7 měsíci
Xflr Analysis of this control arrangement: czcams.com/video/sthW7RGetQk/video.html This channel presents key activities related to my development of a new, 15m span, foot-launchable sailplane.
Re Issues Part 4 Xflr Analysis - KW MkII Development
zhlédnutí 341Před 7 měsíci
0:00 Airfoil Analysis Basics and Problem Definition 10:44 Airfoil with Control Deflection and Related Pressure Wall 25:50 Flat Plate Control Surface Solution 31:13 Flat Plate Control Deflected 49:01 Swift Airfoil Analysis 59:46 Swift Airfoil Control Deflection 1:08:17 Potential Optimum Solution This channel presents key activities related to my development of a new, 15m span, ultra-light sailpl...
Reynold's Number Issues Part 3 - Re Plots -KW MkII Development
zhlédnutí 264Před 7 měsíci
en.wikipedia.org/wiki/Reynolds_number www.grc.nasa.gov/www/k-12/airplane/reynolds.html This channel presents key activities related to my development of a new, 15m span, ultralight sailplane.
Reynold's Number Issues Part 2- KW MkII Development
zhlédnutí 610Před 7 měsíci
Links to help in understanding: czcams.com/video/9A-uUG0WR0w/video.html This channel presents key activities related to my development of a new, 15m span, foot-launchable sailplane.
Airfoil Tools Walkthrough - Klingberg Wing MkII Development
zhlédnutí 605Před 7 měsíci
www.airfoiltools.com/ m-selig.ae.illinois.edu/ads/coord_database.html This channel presents key activities related to my development of a new, 15m span, foot-launchable sailplane.
Wing Skin Repair - KWMkII Ultralight Composite Glider Sailplane Development
zhlédnutí 457Před 11 měsíci
Wing Skin Repair - KWMkII Ultralight Composite Glider Sailplane Development
Composite Ultralight Glider - Klingberg Wing MkII Development
zhlédnutí 1,4KPřed rokem
Composite Ultralight Glider - Klingberg Wing MkII Development
Composite Tubing - Sandwich Panel Style
zhlédnutí 548Před rokem
Composite Tubing - Sandwich Panel Style
Klingberg Wing MkII Ultralight Glider - 2nd Flight
zhlédnutí 2,2KPřed rokem
Klingberg Wing MkII Ultralight Glider - 2nd Flight
Tufts of both wings on 2nd flight. Multiple local stall conditions.
zhlédnutí 360Před rokem
Tufts of both wings on 2nd flight. Multiple local stall conditions.
Klingberg Wing MkII Development - Harness adjustments
zhlédnutí 135Před rokem
Klingberg Wing MkII Development - Harness adjustments
Flight Testing Marina Bch 5-7-22 - Klingberg Wing MkII Development
zhlédnutí 778Před rokem
Flight Testing Marina Bch 5-7-22 - Klingberg Wing MkII Development
Klingberg Wing MkII El Mirage 2nd Flight Cockpit View
zhlédnutí 405Před rokem
Klingberg Wing MkII El Mirage 2nd Flight Cockpit View
Taxi Test - Klingberg Wing MkII Development
zhlédnutí 346Před rokem
Taxi Test - Klingberg Wing MkII Development
Klingberg Wing MkII Composite Hang Glider Aircraft Design - Elevon Upgrades
zhlédnutí 236Před rokem
Klingberg Wing MkII Composite Hang Glider Aircraft Design - Elevon Upgrades
Elevon Lumps - KW MkII Ultralight Composite Sailplane Development
zhlédnutí 463Před rokem
Elevon Lumps - KW MkII Ultralight Composite Sailplane Development
Elevon Upgrades - Klingberg Wing MkII Development
zhlédnutí 197Před rokem
Elevon Upgrades - Klingberg Wing MkII Development
Full Size Elevon Lumps - Klingberg Wing MkII Development
zhlédnutí 86Před rokem
Full Size Elevon Lumps - Klingberg Wing MkII Development
Thanks Sir for your share!!
Nice to have found your channel. A aircraft design that always interested in me was the CFM Shadow, designed and built by Cook. I now see where his wing D spar design has inspired others, was well as he was inspired VJensen.
D-tube construction has been around since the '30's
I've been interested in designing and building my own hang glider for some time and have done nothing like this before. Being new to this, it would never have occurred to me to watch out for aerodynamic control effectiveness problems when the local Reynolds Number is around 400,000. Much less would I have thought that - until you came along - that there has never even been any research into this problem, posed by local Reynolds Numbers around 400,000. Anybody blundering into control effectiveness problems - without being aware of what you've found - would likely have found themselves in trouble and not be able to solve the problem. Thank you for drawing everyone's attention to this - valuable work, on your part!
Thanks, I'm glad to hear how you have found so much value in the work that I do. I look forward to seeing you as a new member on my Patreon site. Given all the value you have received, I'm sure your pledge will be most generous. Pledge at: www.patreon.com/klingbergwing
@@KlingbergWingMkII Not right now - simply because I can't see my way clear to getting any project of my own started, for financial reasons among others. If my financial situation in particular improves sufficiently, then I'll have no difficulty joining your Patreon site. Meanwhile, best wishes!
Beautiful idea. All the best engineering is, of course, beautiful. Elegant solution.
Thank you very much!
So you're increasing the AOA of roughly 100% of your MAC-aft chordline in order to .. lower the AOA? Doesn't that mean there's an inevitable bottom portion of the speed envelope where you're guaranteed to tip-stall and consequently experience an uncontrollable nose-up moment, as your center-of-lift moves forward?
Well those are terms I know, but what you are trying to say with me I haven't a clue.
I flew my hang glider at Dillon Beach around 1982.
It was a great spot! I wish it was up to us today, it would be the best spot for me to do my testing. But hey, we're still kickin; and flyin
Have you approached any composites manufacturers to be sponsors at least with material donations?
Nope, it's a tad difficult to get a sponsor for an aircraft whose flight qualities are still open to question.
Dear Mr. Klingberg, Iam a Glieder constructor from Germany and I love your ideas. Best greetings and much love and success I send you from germany. Gerd Greifenstein
Many thanks
Out of curiosity, what effect would small stall fences mounted to the control surfaces have?
Been there, done that: czcams.com/video/eH4HDLJVp4E/video.html Fences are for boundary layer problems. This is a Reynold's Number problem. You may wish to review: czcams.com/video/2mh8szvuD40/video.html
Thank you. I have a better idea of what you mean. I’ll be honest, I barely have a hobbyist understanding of aerodynamics. I’m a towboat captain on the Lower Mississippi River. I guess I could brag about practical experience in flow dynamics but honestly I have no formal training. After watching several of your videos I keep thinking about the morphing wing profiles that several universities are studying. The problem there is obviously weight. But in that vein, would a two piece control surface be feasible? Shipbuilders had a similar issue with low speed maneuverability and came up with a two piece rudder that increased handling capability and improved fuel efficiency while having a very simple mechanism. The Becker is interesting nonetheless. czcams.com/video/UDBeCqzYO5k/video.htmlsi=T2oV7V1xDziQWore
Morphing wing - really cool concept. However one would have to solve the weight/complexity issue to make them effective on a ultralight glider. What one might gain in aero efficiency would most likely be lost in weight gain, not to mention the big increase in build cost. I can't comment on the multi-part boat rudder concept as I've never seen one and I'd have to study it carefully. I can safely say that boats are not airplanes and water is not air - not all concepts transfer well between the two worlds. Overall, I'd say that designing aircraft is like making a fine wine - it is all about compromise across many, many factors and it takes about 50 years to learn how to make a good one....and then you die. (Old wine makers joke!)
Wonder what the challenges are to a flat component like that - making it stiff enough, flutter issues, etc.
Yes, flutter can be a big issue with flat plates and has to be studiously avoided. Spanwise flutter is not an issue because they are directly attached to the wing TE. However, torsion can be a big issue. Most of the "flat plate" controls I've used or seen are actually thin wedges so they form a torsion box to make them stiffer. One also has to be careful of what impact the placement of the control connection point might have. All that said, there are many powered ultralights that use flat, fabric covered, controls and I have not heard of any flutter problems. However, those controls are usually much shorter in terms of span.
Didn´t the Aeros Phanton use the flat plane?
From what I can see in the online photos, the answer to your question is, "Yes" It is nearly identical to what I used on my original Klingberg Wing back in the '80s. I should mention that the Phantom appears to have a much larger wing chord than my wing at the elevon. Maybe as much as 30% larger. This means they would not have had the same Re problems I'm dealing with.
Oh, BTW, have you flown a Phantom? I'd love to get first hand comments about its handling. If you don't do you know of someone who has flown one? Please let me know.
I found the original owners manual for the Phantom online! It states that the pilot must stay aware for spins. It says the glider will enter a full-blown spin in just a 1/4 turn! I'm not surprised to read this as the glider has strip ailerons which can really aggravate spanwise flow and promote spins. So, flat plate good, strip ailerons bad. In my early videos I explain why an elevon with "reverse" taper (smaller chord at the root and bigger at the tip) prevents this problem. In fact, I have a spreadsheet for calculating the planform of the elevon required to prevent spins. The results are based on the taper and washout parameters of the main wing.
@@KlingbergWingMkII Some of my glider-club-buddies flew the Phantom. Newer heared anything about spinning. Most of them went back to traditional gliders because the thing was mutch to heavy and quite difficult to land. In alpin CX-competions it is a big disadvantage, if you have to care too much about finding a siutable landing field with the perfect wind. After rought landings the pilots were traped under the havy glider some times in a position that did not allow them to free themselfes from glider or harness.
Rather than the reverse duct sticking up, why not reprofile so the duct follows the same profile as the wing and make the leading edge of the flap dive inside the duct?
Of course as that would be lower drag. However, this is an initial experiment and before I spend a lot of time do a bunch of fancy building, let's see if it even works.
On an aircraft design I worked on we gave the ailerons a small increase in thickness. This, combined with hinge placement, kept the top surface of the aileron protruding into the boundary layer as it sips off the wing surface.
Yep, that would be standard design procedure. You can see me test that option in my earlier videos. It proved ineffective, probably because of the low Re. Near stall speed my wing operates at an Re range that is largely unexplored. See this vid for my CFD analysis of the issue: czcams.com/video/2mh8szvuD40/video.html
Looks like you are creating a slotted panel surface with the intent of keeping the flow from separating. The ME-163 has a similar slot detail near the leading edge of each wing to minimize flow separation. The Cessna 177 uses a short reverse (upside down) slot on the stabilator for better control response. You could also try VGs as a quick way to energize airflow over the flap. I would curve the internal channel for a smooth transition from bottom to top and eliminate the big flat piece. Interesting concept.
All good pts. There are many aircraft that have employed leading edge slats. I think the most interesting is the Tiger Moth (or was it the Gypsy?) which had LE slats that deployed automatically when it hit a predetermined AoA. If you check out my earlier videos you will see I've tried dozens of different VG options. Problem is, at 20 mph and a very low Re (under 500K) it is very difficult to energize the flow. VGs bring high energy flow from the freestream into the boundary layer but if there isn't much energy in the freestream, then they are useless. What I'm doing here is a simple first rough cut (my common approach to problem solving). Optimizing the solution comes later if the method proves to be effective.
To differentiate the effect of trip strip, you could also just close the air intake with a tape.
No, the cover on the upper surface could still act as a trip strip even if the bottom slot is closed. Good engineering dictates that the configuration for the upper cover be as close to identical as possible.
I have a prediction, the flow will be interrupted by the deflector and act as a spoiler in the flap up position. Flap down it will act as a choke point and cause undesirable characteristics. better design may be to design a slotted flap that has a smooth airfoil leading edge and eliminate the excess hardware. Notice on the illustrations you've used from the laminar air flow style wing that very much attention was paid to SMOOTH airflow.
Interesting thoughts. Given the format we are working in, I'm not sure I'm correctly visualizing what you describe. That said, the best I can do is to note that I'm not doing this test to use on my flaps. I use the word "flap" as a generic term for a control surface. The elevons for my wing are flaps that must travel up and down, so I'm not sure what you are describing would work. The test I'm going to do is set up for down only to represent what happens on my wing. On my wing I'm having problems with the flow over the elevons only when they are deflected down. Does this make sense?
Thank you for sharing. Interesting concept and I'm looking forward to seeing the results.
Be sure to sign up at my Patreon site to get the results
Hi Rol, Tehachapi, Labor Day Weekend?
Will they let me test my wing there?
@@KlingbergWingMkII I'll check. in the past we demoed the Carbon Dragon on auto tow after the sailplanes were down. We'll call it demo flights not test flights due to fatal at airport with powered homebuilt. There are hang glider sites near by. Airport runway is about 5000'.
I had one more question, that I hope you won't mind answering; Won't the slotted elevons add drag? how do you plan to handle the additional drag?
Yes, the slots will add drag but probably a small amount compared to a low Re airfoil. The low Re airfoils have their high drag at AoAs of 1 degree or less. At those low AoAs the slots will be parallel to the flow so the added drag should be minimal because the pressure differential between the lower and upper surfaces is close to zero. There will be added drag only when the flap is deflected downward when turning. Most high speed runs involving minimal turning, so a limited negative impact. However, I still think the best answer will be the flat plate elevons attached to the TE of the wing. That currently looks like the lowest drag option. This upcoming test is an interesting side quest while I wait for good flying weather to test the flat plate elevons. Plus, it could be a good option for the flaps on my wing to make them more effective for pitch trim and landings.
@@KlingbergWingMkII Thank you
Thanks for the informative video. I hope this works out. I had one question though; in of your videos from not too long ago, you hypothesized that the Reynolds numbers out at the tip are too low and that's what's causing all these problems. So why not make a custom airfoil that performs well at those low Re? It seems to me that if the designers of the swift and the carbon dragon could do that in the 70s and 80s, with your level of knowledge, skill and experience and the software tools available today, that should be possible. Thanks again for sharing your work
Yes, that would be quite easy. However, there is a price to pay. Low Re airfoils are inherently low speed. When taken to higher speeds (low AoA) the drag goes way up. In one of my vids I describe the drag polar for the low Re airfoils and why they get draggy. Gliders such as the Swift were not designed to go fast. I think they had a Vne of about 70 mph. I want a Vne around 100 mph, so this requires a different airfoil. This is all a very sticky problem because we have never really strived for an aircraft that has high performance over such a wide speed range - a vexing problem that requires airfoils that can change shape for different speed ranges (doable but very heavy) or a unique solution the will appear to be "like magic" if I ever find it.
@@KlingbergWingMkII Oh! I hadn't realized that. I'll go watch that video now. Thanks
Best of luck on you impending test flight.
Good luck Rol.
Thanks!
Fantastic
Thank you so much 😀
It is really lucky to have a top notch engineer expert offer an insight into how known materials can work together to form such a light and strong wing structure. By the way, maybe Mr. Calhoun might want to trade places.
And who is Mr. Calhoun?
Calhoun is not an engineer, but somehow he leads Boeing. It did not work that well.
I was an engineer on the 757 and 767 development programs. It was a great company back in the day. Never let finance lead an aerospace company.
Such a awesome video like seriously sir thankyou for making this🙏🙏
Glad you liked it. I hope you watch the entire series about stalls and spins. Enjoy!
Thoughts on end-grain balsa?
The honeycomb core is 2 lbs/cu Ft, the best one would do with balsa is around 6 lbs/cu ft and it would take a lot of work to find enough blocks of that density to do just one aircraft. However, end gran balsa does have very good compressive strength and I suppose that is why it is used in some boats and windmill blade. But, too heavy for my purposes.
It seems to me that if you have foam on the outside and honeycomb in the center that the shear stiffness (or compressive stiffness) near the skin is lower, equal to a normal foam sandwich. This decreases the local buckling stress. Do you than have any advantage of the honeycomb in the middle of the panel? Let alone that you now have 2 additional bonding interfaces in the sandwich which consume resin as well. Looking forward to your findings.
Sorry I was not clear in the video. My goal is to get the outer skin of foam at the same level of the honeycomb so that both the foam and the honeycomb are bonded to the composite skin. In that way one could gain the advantage of high compression strength of the honeycomb and the added bonding area of the foam. Recent tests have show that it is nearly impossible to press the honeycomb into the PVC foam, so, nothing gained so far. However, my experiments continue. BTW, compressive strength and shear strength are not the same. The are generally 90 degrees out of phase to each other. It is the compressive strength of the core material that prevents local buckling when the sandwich panel is undergoing compressive and/or bending loads. I am making this clear so that my viewers do not get confused.
You use VaRTM to produce your panels? Do you worry about degassing your resin before you start the infusion or do you do a hand layup first then pull vac?
Resin infusion is way, way too heavy for this type of aircraft. I spread epoxy in the fabric by hand and vacuum bag to the core. You can see this process in many of my early videos. One exception is DOW XPS styrofoam as it is too weak in compression for vacuum bagging. See the spar layup videos for a demo of that material.
@@KlingbergWingMkII Can you provide the video name? I didn't see XPS mentioned in the "Spar Cap Layup" one and I've watched all your videos, so can't remember either 😄
I use xps as the core foam for the spar: czcams.com/video/5mAtcGb2NUs/video.html
I wonder if CNC routing a cavity pattern for the honeycomb would save you a layer of foam. Like foaming thehoneycomb, minus the mess... Thanks for sharing.
routing which material?
@@KlingbergWingMkIIThe foam, carving thin channels for the honeycomb pattern to embed fully while keeping it low tech enough to be feasible at home.
Based on my recent experiments it looks like routing the foam might be essential. I have found that the honeycomb cannot cut into the foam using pressures available to a home builder. The routing would have to leave a very small layer of foam so the various pieces stay together.
if you are not using prepreg, you can use a paint roller to apply some resin on the nomex just enough to wet one side of it. then stick it to the carbon part which is already soaked with minimal amount of resin. this way you can avoid using unnecessary resin within the cells.
You have "special powers". I ordered rubber rollers earlier this evening for just what you suggest, except using urethane glue. I'm also going to try pouring a thin layer of glue in a tray and dipping the honeycomb core in it. I'll be doing videos on the results. Foaming epoxy could also be an interesting experiment.
@KlingbergWingMkII nice! I tried dipping but for the small pitch of the cells I had and the viscosity of the resin used, it didn't work out due to resin membranes bridging the cell gaps. Maybe less viscous infusion resin would have worked though.
I wonder if a Nomex core material filled with 'dry' micro balloons remove the need for the two 1mm sheets of foam either side if the Nomex. 'Dry micro' uses just enough epoxy to bind it. It's quite stiff and light. I haven't looked at the numbers / weights yet. I have a small sample of 3mm hex-cell Nomex and a bucket of micro balloons in my workshop, so I may make up a test sample to weigh and test. Keep it coming Rol - I learn every time I watch you!
Yep, that's a common method for "potting" the core where bolts and other fasteners will pass through. Too heavy for large areas. I experimented with it in the very early stages of my project for the LE of my D-tubes - they were bulletproof but too heavy.
Composites have so many applications beyond aviation, so every video you share is full of fascinating possibilities!!
I'm so loving your teaching still over my head. I'll pick something up out of this. Thank you
Your welcome!
Wow, you are so over my head, but I love learning all this new stuff. Thank you for taking the time to teach your ideas.
You are so welcome!
Come see my latest design at: czcams.com/channels/Xhs5u7kC5pYoqNUQU9SdWw.html
Come see my latest design at: czcams.com/channels/Xhs5u7kC5pYoqNUQU9SdWw.html
Hi, look slike that local stalls are reason for that authority problems you have, right?
Yes and no. The local stalls are being caused by flow conditions over the elevons that are the result of the low Reynolds number. To fully understand, you need to watch the following two videos: czcams.com/video/3PqZurAydNw/video.html and czcams.com/video/2mh8szvuD40/video.html
Untill landing it looks good :-)
Yep, and we thought all was OK, just a few adjustments to more flare authority. However, 3 years later I'm still working the problem of having enough control authority for this type of wing. Recent analysis has provided some insight and I have mods I believe will work. If you look at my most recent videos, you'll see what I think is the root cause of problems. Hopefully I will have it fixed soon!
For which aircraft did you build this spar please? Can you give me the name of the airplane?
Klingberg Wing MkII
I’m actually really curious about the micro scale red rigid glider at the beginning of the video. I would like to build one about 10’ long any blue prints on that?
A rough set of plans are available for the 1/4 scale version R/C model - it flies great! You get a copy of the plans (and lots of other goodies) in the Welcome Package when you become a Patron at: www.patreon.com/klingbergwing
2 AIREX Foam Questions for your novel Composite Tubing: You mention the AIREX foam is .7 mm thickness in this video (0:44 sec) I have scoured the web for .7mm AIREX foam. 2mm is the thinnest I can find. Could you have misspoken? Also, could you please post the type of AIREX (C70, MO80, etc.) you use I am building a prototype tool, and I am binging on all your videos. You are a superb educator and engineer!
www.r-g.de/en/list/Sandwich-material--Honeycombs--Foam-/PVC-foam--Airex-Mycell-
I liked the MK I better ❤
I'm curious, why?
probably foolish idea but couldnt you just reverse the steering on rudder to compensate for the opposed roll?
Yes, because the rudders are not active controls, just stablizers.
In the old Low'n'Slow newsletter Steve Morse published a design for a forward swept Batwing tailless glider, haven't heard the name since. Had you seen the drawing you would remember the name!
Man, you are dating yourself with that one! You must be at least as old as I am - that pub goes way, way back~
Have you considered the effect of with controlling the elevon pitch with trim tabs alone? Good luck in any case!
Too complex and heavy, mechanically.
I admire your tenacity Rol. Good luck with your mods.
Thanks, we should find out in a couple of weeks, weather permitting.
What about "springloaded" turbulators, that retract automatically at high speed?
Always an option and I speak to them in an upcoming video. Spoiler Alert! - VGs only added about 2 degrees of available elevon travel - not enough to solve the problem. You all will be surprised to see the final solution so stay tuned!
Very informative video. It's hard to appreciate all the time and effort put in to solving a problem that so few would encounter, and even fewer would understand completely. Your methods of finding out how you identified the problem are a gold mine of information. So, my sincere "thanks" for your video. On the design side, perhaps you could look at installing a wing cuff at the outboard wing to extend the leading edge of the wing without any major modifications to the trailing edge. Installation and adaptation may be easier since you have the D tube to anchor off of. Many aircraft are starting to adopt the Cirrus like wing for spin resistance. You can then perhaps play around with a slightly different airfoil by virtue of modifying the outboard leading edge geometry (i.e. make it a low Reynolds number airfoil) to get a more favorable Reynolds number without necessarily increasing the chord of the wing to 32".
Thank you very much for all the kind words. I love all the support. Funny thing, the LE cuff was the preferred solution (Peter's idea) for several days. Then I realized that I had some data that showed there was more at play here than Reynold's number. I think I will be able to stay away from the low Re airfoil choices and thus retain the high speed end performance. Please stay tuned for the entire series, I'm sure you'll be surprised at the final solution!
Great to see another video on what is a fascinating project. It seems so counter intutive to start wing design at the tips, but when you think about it, thats where the really serious problems occur. I am looking forward to seeing the new elevons and if you go to a simple constant chord wing planform. Thumbs up and respect is due for all your efforts to sort out the issues with the project so far. Was it Einstein who said that " Genius is 1% inspiration and 99% perspiration".
Thanks for the words of support and encouragement. I won't be going to a constant chord wing because that would require designing and building and entirely new aircraft and I probably don't have enough "healthy" years left in me for that long-term project. However, I will be making progress with the current design until it is fully flyable (I hope). Others can "pick up the stick" and go forward with what we learn from my current efforts.
That really is a fascinating and extraordinary contribution to the field.
Thanks! Everyone on this end has been quite surprised about the results. My wife and I had a little celebration because I've been beating on the problem for nearly 2 years now. Hopefully, next time out with the Wing will be much more satisfying and I thank you and all my Patrons for your continued support!
I use this tool with Open VSP, which is the NASA design software. It's open source, so it's free. Between these two tools, I have designed all kinds of airplanes.
Yep, it's an excellent tool. Great value for the price!
So, a more Reynolds-number-friendly airfoil section at the tip?
Yes and no. Future video will explain.
How about retractable VGs? 🙃 yeah I’m a lot of help lol
Yep, that has been discussed at length, but the impact to the D-tube would be extensive and would need a series of load rings. However, there is another potential solution, which I will post in a week or so after the next round of tests tomorrow. Stay tuned!