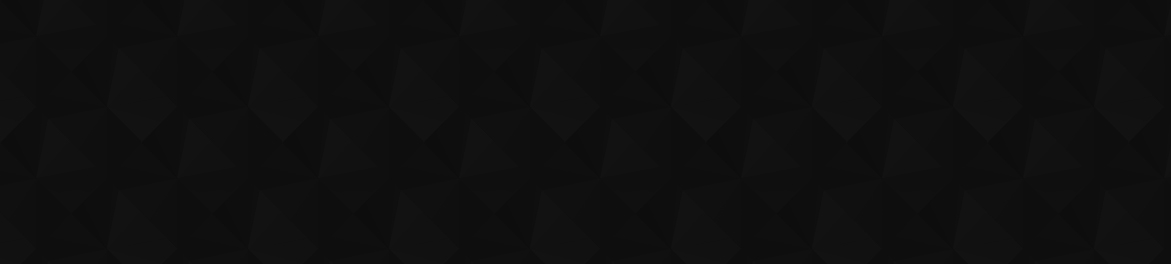
- 86
- 756 581
Paul's Garage Projects
United Kingdom
Registrace 21. 12. 2008
Decided to start keeping track of my projects - mainly machining with the odd smattering of electronics.
Making a Centring Microscope - Hemingway Kits
Here I have a go at making the Centring Microscope from Hemingway Kits.
Some of the tools I use and would recommend (affiliate links):
Starrett Edge Finder: amzn.to/3wLbqRp
Dykem Layout Fluid: amzn.to/3Tp2Xw1
Starrett Hacksaw Blades: amzn.to/3PdsbuW
CT-90 Cutting and Tapping Fluid: amzn.to/49TH4uo
Eclipse Scriber: amzn.to/4c6Ck6w
STA-BIL Rust and Corrosion Inhibitor: amzn.to/3wFSbIJ
Dremel 3000 Rotary Tool: amzn.to/3Pa3gIH
Trend Digital Level Box: amzn.to/49Z0dee
Sealey Imperial Hex Key Set: amzn.to/3wJFvRd
ElectroCookie Solderable Breadboard: amzn.to/4a1Dez5
Mitutoyo MIT103-129 Micrometer: amzn.to/3wDB9ei
Mitutoyo 103-130 Micrometer: amzn.to/3V4lEGr
Engineer Solder Sucker: amzn.to/438RFiT
3M Silicone Face Mask: amzn.to/3SYOLbu
Irwin Hacksaw Blades: amzn.to/3TpLOlK
Irwin Metal Hacksaw: amzn.to/3V6SvKI
Starrett 117D Centre Punch: amzn.to/3V6hRIG
Big Gator Tools V-Drill Guide: amzn.to/3Tq6hXP
Faithfull Engineers Square: amzn.to/48Jt05p
Milwaukee Set of Drill Bits: amzn.to/48O9uVo
Some of the tools I use and would recommend (affiliate links):
Starrett Edge Finder: amzn.to/3wLbqRp
Dykem Layout Fluid: amzn.to/3Tp2Xw1
Starrett Hacksaw Blades: amzn.to/3PdsbuW
CT-90 Cutting and Tapping Fluid: amzn.to/49TH4uo
Eclipse Scriber: amzn.to/4c6Ck6w
STA-BIL Rust and Corrosion Inhibitor: amzn.to/3wFSbIJ
Dremel 3000 Rotary Tool: amzn.to/3Pa3gIH
Trend Digital Level Box: amzn.to/49Z0dee
Sealey Imperial Hex Key Set: amzn.to/3wJFvRd
ElectroCookie Solderable Breadboard: amzn.to/4a1Dez5
Mitutoyo MIT103-129 Micrometer: amzn.to/3wDB9ei
Mitutoyo 103-130 Micrometer: amzn.to/3V4lEGr
Engineer Solder Sucker: amzn.to/438RFiT
3M Silicone Face Mask: amzn.to/3SYOLbu
Irwin Hacksaw Blades: amzn.to/3TpLOlK
Irwin Metal Hacksaw: amzn.to/3V6SvKI
Starrett 117D Centre Punch: amzn.to/3V6hRIG
Big Gator Tools V-Drill Guide: amzn.to/3Tq6hXP
Faithfull Engineers Square: amzn.to/48Jt05p
Milwaukee Set of Drill Bits: amzn.to/48O9uVo
zhlédnutí: 30 570
Video
Making a Spherical Turning Tool - Hemingway Kits
zhlédnutí 32KPřed měsícem
Here I have a go at making the spherical turning tool from Hemmingway Kits. Also, shoutout to @RustyInventions-wz6ir Some of the tools I use and would recommend (affiliate links): Starrett Edge Finder: amzn.to/3wLbqRp Dykem Layout Fluid: amzn.to/3Tp2Xw1 Starrett Hacksaw Blades: amzn.to/3PdsbuW CT-90 Cutting and Tapping Fluid: amzn.to/49TH4uo Eclipse Scriber: amzn.to/4c6Ck6w STA-BIL Rust and Cor...
Making a Drill Bit Sharpener - Hemingway Kits
zhlédnutí 39KPřed 2 měsíci
Here I have a go at making the drill bit sharpening attachment for the Worden tool and cutter grinder. Some of the tools I use and would recommend (affiliate links): Starrett Edge Finder: amzn.to/3wLbqRp Dykem Layout Fluid: amzn.to/3Tp2Xw1 Starrett Hacksaw Blades: amzn.to/3PdsbuW CT-90 Cutting and Tapping Fluid: amzn.to/49TH4uo Eclipse Scriber: amzn.to/4c6Ck6w STA-BIL Rust and Corrosion Inhibit...
Making a Tool & Cutter Grinder - Hemingway Kits - Part 3
zhlédnutí 13KPřed 3 měsíci
Here I build a tool and cutter grinder using plans and materials from Hemingway Kits. The sheet metal parts were quite sharp and required a lot of deburring. They are all accurately to dimension and square, though. The plans are nicely printed on A3 paper, although the dimensions are in imperial - not great for my metric machines. Before starting each part, I converted all the measurements to m...
Making a Tool & Cutter Grinder - Hemingway Kits - Part 2
zhlédnutí 31KPřed 3 měsíci
Here I build a tool and cutter grinder using plans and materials from Hemingway Kits. The sheet metal parts were quite sharp and required a lot of deburring. They are all accurately to dimension and square, though. The plans are nicely printed on A3 paper, although the dimensions are in imperial - not great for my metric machines. Before starting each part, I converted all the measurements to m...
Making a Tool & Cutter Grinder - Hemingway Kits - Part 1
zhlédnutí 11KPřed 3 měsíci
Here I build a tool and cutter grinder using plans and materials from Hemingway Kits. The sheet metal parts were quite sharp and required a lot of deburring. They are all accurately to dimension and square, though. The plans are nicely printed on A3 paper, although the dimensions are in imperial - not great for my metric machines. Before starting each part, I converted all the measurements to m...
Making a Tiny Engine #Finale Last Parts, Assembly & Start!
zhlédnutí 1,3KPřed 4 měsíci
Here is the final part in a series of videos about making a model 2-stroke petrol engine. The specific model is an Atom Minor MK3, designed by Edgar T. Westbury in the 1940s. In this video, I make the remaining parts, get it assembled and attempt to start it for the first time. Some of the tools I use and would recommend (affiliate links): Starrett Edge Finder: amzn.to/3wLbqRp Dykem Layout Flui...
Making a Tiny Engine #6 Rotary Valve, Conrod and a Gudgeon Pin
zhlédnutí 2,2KPřed 5 měsíci
Here is the sixth in a series of videos about making a model 2-stroke petrol engine. The specific model is an Atom Minor MK3, designed by Edgar T. Westbury in the 1940s. In this video, I machine the rotary valve, conrod and the gudgeon pin. Some of the tools I use and would recommend (affiliate links): Starrett Edge Finder: amzn.to/3wLbqRp Dykem Layout Fluid: amzn.to/3Tp2Xw1 Starrett Hacksaw Bl...
Making a Tiny Engine #5 Piston
zhlédnutí 2,7KPřed 6 měsíci
Here is the fifth in a series of videos about making a model 2-stroke petrol engine. The specific model is an Atom Minor MK3, designed by Edgar T. Westbury in the 1940s. In this video, I machine the piston, which required an outer diameter lap. Some of the tools I use and would recommend (affiliate links): Starrett Edge Finder: amzn.to/3wLbqRp Dykem Layout Fluid: amzn.to/3Tp2Xw1 Starrett Hacksa...
Making a Tiny Engine #4 Jet Tube & Cylinder Head
zhlédnutí 1,5KPřed 6 měsíci
Here is the forth in a series of videos about making a model 2-stroke petrol engine. The specific model is an Atom Minor MK3, designed by Edgar T. Westbury in the 1940s. In this video, I machine the jet tube and cylinder head. Some of the tools I use and would recommend (affiliate links): Starrett Edge Finder: amzn.to/3wLbqRp Dykem Layout Fluid: amzn.to/3Tp2Xw1 Starrett Hacksaw Blades: amzn.to/...
Making a Tiny Engine #3 Crankshaft & Cylinder Barrel
zhlédnutí 2,7KPřed 7 měsíci
Here is the third in a series of videos about making a model 2-stroke petrol engine. The specific model is an Atom Minor MK3, designed by Edgar T. Westbury in the 1940s. In this video, I machine the crankshaft and the cylinder barrel. Special thanks go to @Blondihacks for her excellent guide on ID lapping of bores. Some of the tools I use and would recommend (affiliate links): Starrett Edge Fin...
Making a Tiny Engine #2 Main Bearing & Backplate
zhlédnutí 1,4KPřed 7 měsíci
Here is the second in a series of videos about making a model 2-stroke petrol engine. The specific model is an Atom Minor MK3, designed by Edgar T. Westbury in the 1940s. In this video, I machine the main bearing and the backplate. Some of the tools I use and would recommend (affiliate links): Starrett Edge Finder: amzn.to/3wLbqRp Dykem Layout Fluid: amzn.to/3Tp2Xw1 Starrett Hacksaw Blades: amz...
Making a Tiny Engine #1 Crankcase
zhlédnutí 2,1KPřed 8 měsíci
Here is the first in a series of videos about making a model 2-stroke petrol engine. The specific model is an Atom Minor MK3, designed by Edgar T. Westbury in the 1940s. I bought the kit, plans and the original construction book from Hemingway Kits. The plans appear to be enlarged versions of the book drawings, with all the measurements in imperial. I've also been using the Jan Huning guide on ...
Making a Graduating Tool - Hemingway Kits
zhlédnutí 246KPřed 9 měsíci
Here I build a graduating tool using plans and materials from Hemingway Kits. All of the measurements on the plans are in imperial units, which provided quite a challenge, as all my tools and machines are metric. This wasn't obvious when I bought the kit, but I guess it's standard in the model engineering world. The plans themselves were nicely printed out on A3 paper with well-written instruct...
Whitworth Drawbar for the Mini Mill - Project
zhlédnutí 1,3KPřed 11 měsíci
Whitworth Drawbar for the Mini Mill - Project
Making a 3D Printer Nozzle From Scratch
zhlédnutí 2,3KPřed rokem
Making a 3D Printer Nozzle From Scratch
Custom Fine Pitch Thread Cutting Tap Project
zhlédnutí 2,5KPřed rokem
Custom Fine Pitch Thread Cutting Tap Project
DIY Precision Lapping Plates from Scrap
zhlédnutí 11KPřed rokem
DIY Precision Lapping Plates from Scrap
Mini Mill Bearing Upgrade: An Attempt to Fix Spindle Runout
zhlédnutí 12KPřed rokem
Mini Mill Bearing Upgrade: An Attempt to Fix Spindle Runout
Transforming Scrap Metal: Mini Mill Slotting Head Build
zhlédnutí 7KPřed rokem
Transforming Scrap Metal: Mini Mill Slotting Head Build
Hi! Do you know if G02 and G03 can be used in GRBL?
Hi there! I believe they are supported, I never used them though. Always used fusion 360 to generate the gCode 👍
Recently bought a used VM32L machine, and experienced the very same issue. Got hold of a replacement spindle from Amadeal (UK), and some quality SKF bearings. Managed to reduce the runout from 0.08mm to 0.02mm. Still not ideal but it will certainly help with the work that I use it for.
just earlier I was sketching out a sphere cutting attachment for hair clippers, to get a perfectly orbular hairdo
Best video that I have seen you make. Didn't realize that you can do such excellent work. Impressive build.
Many thanks! I'm always trying to improve 👍
Merci !!!
I am a machinist for 40 years now and I don't understand why you're blueing your part and wreck your calipers for marking distances on your part. All my lathes came with an Y-axis nonius or, better DRO indicator. Touch of, zero the Y and Bob's your uncle. It looks fancy maybe... But the only thing here which get's blue sometimes is me ;-) I own a Swiss centering microscope for years now and I discovered that you have to tune it every time when you mount it; tip. I also discovered, watching this video, mine has a much better image and therefore much easier to set and use. It's a nice project to build but is doesn't approach the quality of a bought Swiss or German optical centering microscope. I know price is an issue here. But first when do you need a centering microscope? This question should be involved in this video I think. For me the only reason is to find the center of a hole in a rotated part in the X-Z or Y-Z plane. What you see through the microscope then is an ellipse. And you're able to find the center with this tool. Start of with looking at a straight edge and tune the position of the center of the microscope by moving the x or the Y axis on your machine (depending on the orientation of the edge you're looking at). When spot on turn the microscope 90 degrees. Adjust the lens so it centers on the same edge. Rinse and repeat. If both 90 degrees apart movements show the same edge at the center of the microscope you're tuned in for measuring the part and find edges and centers. And pretty accurate within 0.01 mm. TRhank you and all the best, Job
Many thanks for sharing your insights, Job! The calipers I use for scribing are an inexpensive pair, so I don't mind them getting a bit worn. I do plan on adding a DRO to my lathe in the future, but I still find visual aids helpful to avoid making mistakes. The video doesn't quite capture the quality of the microscope - it looks much better in person. Getting usable footage with my mobile camera was challenging. I wouldn't be surprised if a professional microscope offers better image quality though. As for why I built it, it looked like a fun and interesting project for a hobbyist like myself.
them calipers must worn to the nub, ouch😂
Don't worry, it's just a cheap set I use for scribing!
I have been machining stuff for over 40 years and is one of the coolest things I have seen
New to the channel. I appreciate you showing the use of the tool as well as the machining.
Neat.
Very well done, the part and the video.
Many thanks!
Nice 👍
Thanks!
👍
Great editing! I enjoy watching machining hate watching ever hole drilled,tapped etc. Nice job showing the finished part in use also. subscribed and thumbs up!
Thanks Bob, I try to keep it entertaining!
This is like therapy. Amazing levels of craftsmanship and excellent production quality/values. Very impressive, to say the least.
Many thanks for the kind words!
i didnt know i needed one till now... thanks.. jerk.
🤣🤣
i always think....could i make that....probably not. nice work
Well know I know how to tell if something is square. Gotta have something flat first, agree?
Think you'd struggle without a flat surface. You can make an incredibly flat surface from scratch, just by rubbing three plates together: czcams.com/video/R8XEqo4YC5Y/video.html
These were used on jig borers and they were in all the catalogs 20yrs ago, then faded away because they only work on jig borers. The reason is conventional milling machine collets or tool holders are not accurate enough to remove and install the device without losing its calibration.
There level artistry that goes into mill work like this, also we used these for measuring the depth of scratches and gouges when I was a helicopter mechanic. Now I know how they’re made.
Top Job, Sir 👌
Thank you! Cheers!
Very interesting. Nice work sir
Many thanks Rusty!
where do you get the reticle?
The reticle came with the kit, but I believe it was sourced from a UK company called Graticules Optics. Think this is the item www.graticulesoptics.com/products/microscope-eyepiece-reticles/circle-gauges-and-protractors/ne48-concentric-circles-1mm-10mm-crossline-scales A very nice piece of kit!
I have one, it certainly will shorten sone setups And help in adjustment of not only tools but also fixtures and machines (re center tailstock to name one)
I haven't had the chance to use it a great deal, but I think with the DRO on my mill, I might be able to measure things like thread pitches and angles. Also, I might be able to work out radii using multiple x/y coordinates.
@@PaulsGarageProjects yes, it is useful and with that DRO you can reverse engineer things surprisingly well
Can I get details of this
@@PandiyaRajanbpkyou use it like jeasuring microscope to measure between holes and edgs of things like gear or screw teeth... getting accurate coordinate map in two planes, then you can get third axis by using a dial indicator, those can then be put into CAD software and values possibly with luck minutely tweaked to fit a standard (rare), or you can just put time in trying to match them to standard threads/gear in machinists handbook or similar. this was a whole class when I went through training, not always easy to do when repairing old precision equipment (instrument maker/micro mechanic training decades ago) standards could be used in parts or not at all, even weird mixes, like metric pitch but diameter in inches or reverse, some had just invented a thread to fit specifically that thing, often weird things with random sizes, not always fun to replicate.
How to ruin a caliper. Well demonstrated.
Don't worry, it's just a cheap set I use for scribing!
@@PaulsGarageProjects there's alwas one
Looks great, does the kit include the graticules/prism/objective or are they separate purchases?
Thanks! You get all of the required items with the kit 👍
@@PaulsGarageProjectsthat’s awesome :-) I’ve used the Isoma and another type before, but this looks ideal for an upcoming project!
My ears! Choke up on that boring bar! You'll get a lot less squealing and chatter. Looks like you've got about a 6:1 stickout. Anything over 4:1 with a steel bar is questionable, especially in a #2 universal tool holder.The #41 is more rigid.
Many thanks for the tip!
Happy days, thanks for sharing Paul, that turned out nice buddy
Thank you very much!
How long did it spin?
Think it span for about a minute and a half on the bench. I imagine it would spin for a lot longer on a hard surface such as glass 👍
I started one of those kits a decade ago, must be getting round to the time to start again. I only stopped because there wasn't a local anodising company to do the necessary, i think I'll just paint it on the inside.
Just painted the inside of mine with dark layout blue, which seems to have done the trick 👍
@@PaulsGarageProjects I would still love to anodise it for the protection but if it is a case of being protected or not used, paint wins everyday.😉😉
@@chrisstephens6673 anodising is easy. dilute h2so4, a battery and resistor or variable supply... the dye is boiled in afterwards. except black DYE can be the challenge. buy the commercial stuff ;) most colours can be done using cheapo fabric stain and food dye, but blacks tend to be a mixture and only one takes... leaving you with dark blue etc... like ink on wet paper bleeds different colours. once you get the hang of it its sort of hard to stop... ;) some colours are a challenge. theres also "hard anodising" thats a bit harder to get right, requires a freezer....
I’m in the same boat, completed the machining but haven’t sorted out the anodising
@@paradiselost9946 thanks for that, I know the principle but rather thought that the hard variety would be a good idea.
awesome work! clickspring is starting to have some competition :)
beautiful work!
Many thanks!
nice ..... you will be up there with Dan Gelbart soon chap .... peace
Ha, Hemingway also has _centering microscope_ misspelled at the top of their webpage, but done properly in the text.
Damn! Where did I write centering? Thought I'd used the British Centring all the way through!
Hemingway’s web site spell it correctly in the title, but get it wrong in the text.
Please how to make a cnc with grbl full video 😊
👍👍👍
Hi Paul, as a fellow-builder of useful projects & tooling / fixtures, I appreciate your contribution to the community. You inspire me & keep me motivated- thank you. Could you share some feedback on how that O1 is performing? How is durability/ edge retention? I appreciate the level of care in your turning and drilling of your 0-flute C/C, In practical application would you reckon your heat treat is on par with the same quality of workmanship? My HSS 0-flutes work very nice in 5086 & 6061 when crisp and sharp, but they don’t do as well in A36. I’m optimistic that o1 might be a beautiful material choice to build my own countersink from. Thanks for sharing. I’m my small circle I’m the twist drill rehab guy! I have a crude jig and can at times subsidize it with enough attention to make a real respectable & symmetric 4-facet grind, but always chasing “better” I would love to rebuild it. I mentioned my reaction of inspiration. Specifically, your tool & die cutter has inspired my vision of its next iteration. Thank you.
Hey, many thanks for the kind words! I'm just a hobbiest, but from my experience, hardened O1 is good for cutting aluminium and free machining steel, but would expect to be sharpening it pretty frequently for more challenging materials. For a small home shop, I've been really impressed with the tool and cutter grinder I built. Can see myself building further addons for it in the future.
Well done, nice editing, stop biting your nails.
Many thanks! Like to keep them short - more of a nail clipper than a biter!
@@PaulsGarageProjects Good man.
This is interesting. Why is it shiny? Normally, you should get a dull grey color no matter the grit size of the diamond. The cast iron must be of weird quality (mythical chinesium) that it enables the diamond particles to "scratch" instead of "tumble".
Good question! I was surprised to see it come up to a mirror finish myself. At a guess I'd say it's just your common, cheap gray cast iron.
@@PaulsGarageProjects i'm quite certain that all the plates have diamond strongly imbedded in them.. the cast iron was so freakishly soft, that it got embedded. To try if the diamond is embedded get a piece of hardened steel (parallel, old gauge block etc) and rub it on the plate.. if you see alterations you know what you've got :)
There are definitely diamond particles embedded in the plates - I've been keeping them separate for the different grades of lapping compounds. I'm not convinced that it's the diamond that's making the cast iron shiny though, have a look at the finish people get in cast iron frying pans - they look like mirrors!
@@PaulsGarageProjects I have never made that claim. I have made the claim, that embedded diamonds create microscraches that look make the surface shiny (it's the scratches). I lapped cast iron (with cast iron) many times with various diamond sizes and it always came out matte. Please look at Stahli's (german lapping machine producer) and it's there explained with great footage and animations. czcams.com/video/fnoVV-RWIWY/video.html
1:38 bless you!
🦾🦾🦾
Thanks for putting out this great video Paul. I will use it as a guide during my build. I bought a handful of their kits a couple months ago and have been enjoying working my way through them. As I was sitting down to start this build, I fired up your video and immediately discovered that my order was missing that bag of parts with the Oilite bushings and other assorted hardware. :( I reached out to them (on Friday evening (after closing hours) - and hope to hear from them tomorrow AM. If their reputation is accurate, I am sure they will take care of me. I really wish they would use decimal units in their diagrams. I don't have them memorized, so I have to break out the calculator for every measurement. I hate to mark up these beautiful schematics with my terrible handwriting. - But, that's my Only complaint!
Many thanks! I usually take pictures of the plans, replace all of the measurements with metric, then print them out. Fair bit of work, but helps to avoid mistakes 👍
Gostei muito valeu muito obrigado!
Thank you very much!
Does it chatter more than normal?
I've used it a fair bit since I made it and haven't had any trouble with chatter. Although I do run the lathe at a slow speed when cutting threads.
good
Genio totaaaal...!!!!♥♥♥🙌
Hi, is that a german lathe? Cus I saw that 0 compound degree is when the compound is parallel to the way, and with american lathes it is 90 degree that way. Nice Video!
Thanks! It's a Boxford lathe made in 1970 ish in England. I got caught out by the way the compound works the first time I cut a thread - ended up with a sawtooth profile!
@@PaulsGarageProjects thanks for your answer. It happend to me the same cus I have also the same compound Angel. I made many bad threads and broke many tooling until I got it right. So you put your compound at 61 degree to cut 60 degree thread and not 29 right?
@@svenmj4973 Yep, 61 degrees. Although I tend to only bother for larger threads 👍
Are any plans available for this ?
There are plans available, but I think you have to buy the kit to get them. If you got in touch with Hemingway Kits, they may sell them separately.
@@PaulsGarageProjects Thank you
Found it. Thank you
Is there a reason you decided on using a deburring tool on that first part after reaming that first hole? I mean, you were already set up in the lathe, why not just turn a light chamfer instead?
Good point. Didn't really put much thought into it, just wanted to break the edge 👍
Excellent video, thanks.
Many thanks!