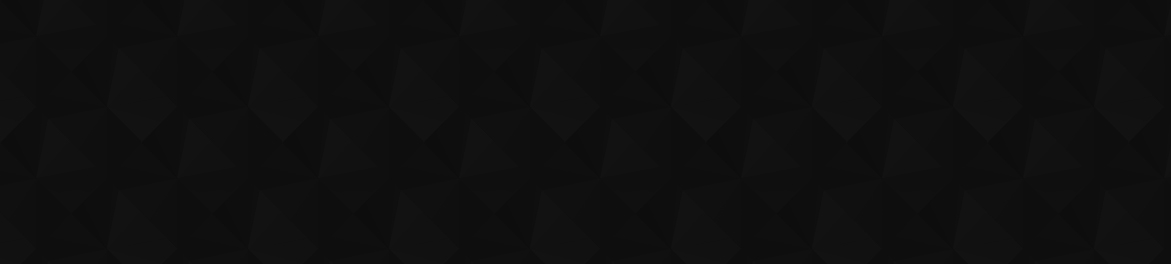
- 10
- 80 122
Backbeat Woodworks
United States
Registrace 16. 06. 2008
Hi, I'm Tony. I like to build things and make things out of wood, metal, plastic or whatever hits me in the moment. I'm horrible about "over engineering" projects and that can sometimes get frustrating.
I hope videos that I share can give someone some inspiration to tackle a project or build something. None will be perfect, but I do it for enjoyment. Hopefully we all can learn along the way.
Enjoy,
Tony
I hope videos that I share can give someone some inspiration to tackle a project or build something. None will be perfect, but I do it for enjoyment. Hopefully we all can learn along the way.
Enjoy,
Tony
How to rebuild a Dewalt 735 Type 1 Motor - Part II
Come along as I rebuild the motor in a Type 1 Dewalt DW735 thickness planer in this 3 part series.
It's easier than it sounds.
It's easier than it sounds.
zhlédnutí: 2 439
Video
How to rebuild a Dewalt 735 Type 1 motor - Part I
zhlédnutí 3,8KPřed rokem
Come along as I rebuild the burned up motor in a Type 1 Dewalt DW735 thickness planer in this 3 part series. It's easier than it sounds.
How I Made My Drill Press Table
zhlédnutí 179Před 3 lety
I wanted to revamp my original drill press table that I built several years ago and add some storage as well as solve the issue of the handle hitting the back of it. This project was quick and easy and gave me just what I needed.
My DIY Router Table Build Based Off Norm Abram's Plan
zhlédnutí 9KPřed 3 lety
I've wanted to build a cabinet for my router table since 2007 or so. I finally decided it was time to get it done. I based it off of the plans from Norm Abram and New Yankee Workshop.
How to replace a cooling fan in a CO2 laser with a Noctua NF-A9
zhlédnutí 202Před 3 lety
My cooling fan started making noise, so I replaced it with a Noctua 5 volt fan. The original fan is 110v, but I decided to replace it with a 5v fan and connect it to the power supply. I apologize for the bad video angles and some out of focus shots. I was hurrying an didn't take much time with the camera. Parts used on my laser: Replacement fan - amzn.to/3fX6PRz mA Meter - amzn.to/3wH1LXq Gear ...
Air Compressor Aftercooler for my Eaton Compressor
zhlédnutí 29KPřed 3 lety
I finally decided to tackle installing an aftercooler on my Eaton Compressor 5HP 60 Gallon air compressor. This is a video documenting how I went about it and I hope you find some of the information helpful. Parts used in this project: Derale Stacked Plate Cooler Kit amzn.to/3mcPPb5 Hayden Oil Cooler Mounting Kit amzn.to/3m74FQr Inline Water Trap with Auto Drain 3/4" amzn.to/2PbW0QP Pressure Re...
Sanding Disc Storage Box - Quick and Simple
zhlédnutí 7KPřed 3 lety
This is a quick box I put together for storing my sanding discs. It beats having everything stuffed in a drawer and not being able to see what you have at a glance.
Chicken Coop Watering System
zhlédnutí 13KPřed 3 lety
Follow along as I put together this barrel for my mom's chicken coop. My goal is to minimize the amount of time she has to spend maintaining their water. I'm sure some if it will be trial and error along the way. Eagle 30 Gal Drum amzn.to/2PnutvJ Bulkhead fitting for Barrel amzn.to/3dmTRcL 1 inch PVC Shut off amzn.to/3docmhd Fountain Pump amzn.to/2PjxME9 Thermostatically Controlled Outlet amzn....
Converting My Delta Dust Collector into a 2 Stage Cyclone Separator
zhlédnutí 14KPřed 3 lety
I decided to convert my Delta 50-760 dust collector into a 2 stage unit using the Oneida Super Dust Deputy. I also topped it off with a Wynn Environmental pleated filter. So far this conversion has been well worth the time and effort. I'm glad I finally did it. And both the Super Dust Deputy and Wynn pleated filter are awesome and I would recommend using them. If you have any questions about wh...
Kreg Accu-Cut Unboxing
zhlédnutí 1,7KPřed 3 lety
This is my first impression of the Kreg Accu-Cut system. I have several Kreg tools and find they have a major place in my shop. I use my K3 and K5 Pocket Hole jig on lots of projects. Tools Kreg Accu-Cut amzn.to/3wbjrKD Dewalt DCS570 Cordless Circular Saw amzn.to/2PLW5dB Wyze Band Activity Tracker amzn.to/3fsUxQA
Did the same on my Ingersoll rand two stage my tubeing was 5/8 had to get the inverted tubeing nuts to come from head and tank iam also using the 3/4 pvc pipe up n down with drains and motor guard and a whole house descent filter on the end for painting i can't have a drop of water at the end of my hose sounds like over kill but it definitely works
Video is waaaaay too long, get in get to the point and get out, this video should be 4 minutes tops
@cecorri Thanks. I appreciate your pointers.
Nice looking piping, smart routing
So I made essentially this same setup, except I have an IR compressor(175psi). But instead of running a single filter after the Derale radiator I ran a 3 stage Nanpu set from Amazon. Filter, coalescing then desiccant dryer then into the tank. Within 3 seconds of turning it out the 1st filter stage of the Nanpu blew apart. Looks like three of the metal lugs holding the bowl cannister on had just sheared off. The cannister flew down and smashed into the floor with all the plastic parts busting everywhere. Dented the metal cannister also and a small piece of something had flown by my head. I think it was one of the lugs. My first thought was that the nanpu, which I'm sure is cheap chinese pot metal, had a stress fracture in it. My second thought was that having all three stages inline created to much back pressure and the 1st stage gave way. I am using 1/2" NPT so the lines are big enough. It was probably a combo of those two items. My goal was to have the air as dry as possible going into the tank. But when I replumb it I think I'll go with just a 1st stage filter/regulator and put the coalescing and desiccant filters after the tank. Also, posted this as a warning to anyone else trying it. Take precautions when starting it up the first time with any modifications, like turning it on from the break far away from the compressor! ha.
Yeah, there was definitely a moment of stress when turning it on for the first time. Thanks for giving your experience. Hopefully it gives others more information to work with.
I have one of those style air compressors. It has a Campbell 7 horsepower compressor head that looks like yours. I am in Pennsylvania and my 300 gallon compressor is in the damp barn . It gets super wet and water gets into everything. I am upgrading my HF sandblaster to the metering valve , lights and new glass with t-bolt thumbscrews that will hold the glass in and and screw into the outserts that I used for 1/4-20 threads. You are an inspiration . I should have the 17 centimeter light strips for inside. If everything works well then I am going to convert to vapor honing for glass bead's
Aww man I watched both videos and would have been able to do it without. Wish there was a reassembly video l. It’s going to be hard watching the first one in reverse. Thanks for the videos they were so helpful
Thanks mate, my motor has burnt out again, first time under warranty, and I only plane softwoods, happened again, watching your video has shown me a major design fault in my opinion as an old electrician, the motor spinning at such speeds generated a large amount of heat and needs cooling, encasing the stator in a plastic housing that insulates and holds in the heat along with a fan that is only for exhausting shavings, this machine should have a short duty cycle, once I replace the rotor, stator and brushed I think I will do just that, thanks for a great video well done.
@@MasterHomebrew Hello, can you please explain/show how you converted the motor to 230V? I would like to do that for all the reasons you point out but can't find anything on how to do it or the parts? Thanks so much!!
It would be nice to see a parts list.
This is for type 1 motor only. Type 12 is a newer version with different part numbers and specs and the parts are not compatible or at least the armature and field. Parts can be ordered online by a number of different websites including ebay may have some. I will say this. The motor has too much current running through it which is what causes the motor windings to burn up. It is running close to 15 amps and maybe more. Helical cutters draw more current and compound the problem. Best solution is to upgrade to a 230v armature and field cutting the current in half thereby reducing the heat created by excessive current. All this current also runs through the main power switch and micro safety switch which can also cause them to fail. I converted my motor to 230 and never worry about it again as current drops to 7 or 8 amps. The parts listed are for the 120v version because that what you asked for. Armature 5140011-80 Field 5140011-78 Brush 5140011-85
@@MasterHomebrew Can you please show the parts list/directions on converting to 230V? Thank you!!
Parts list
Good job on the copper bending from the cooler to the water separator. You just have to wonder why the makers do not use these coolers from the get go. Or, at lease offer them vs. the expensive methods.
Can you post a picture of the wiring of the lead wire, switch, safety switch, and breaker
Hello Tony - what is the best way to remove the front and rear bearings from the Armature and front plate? Thank you - Scott
Hi Tony - you mentioned a need to "calibrate" the planner - what is that and how is it done? Sounds like maybe another video or maybe an instruction sheet...? Thank you Scott
Hi Tony - I for one would enjoy seeing a reassembly video as well...! Would you be able to include a parts list of the items you replaced as well...? You have shown me that i can do this as well - Many, many THANKS! Scott
You mention in the Title of your planner videos that there is a Part III... I'm not finding a video or link to Part III ---- Can you let me know where I can find it? Thank You - Scott
Thanks for sharing; well done.
Motor on my DW735 is dead, too. I have power to the motor, it self. Checked all, wires switches, reset, etc, all good. If he'd reply where we can order same parts as he did, would surely help.
Where did you order the parts? And how much did it cost?
😀 Nice and neatly done. Great job.
Can you tell us which parts you ordered and from where? Sure could ise good links as I am going to have to do the same thing. Thanks
Can you add a parts list and purchase location for all the parts you ordered? I am going to need to do the same. Thanks
Guess I will go ask the guy who did the Type 12 if the parts are interchangeable.
I’m curious if they are interchangeable as well? Any info ?
He has never answered the question. Maybe he doesn't know.
@@clayedwards987 I’m guessing so. I may just order a new field, armature, and housing In type 12 although mine is type 1.
Let us know how it works. Questions I had were 1) would either armature and field fit in either case, and 2) were the two cases with their screw and pin holes be the same?
First one I've seen using the stacked plate style cooler, good on you for not just following the "conventional wisdom" of buying a derale 15300 because that's what everyone does. And your temperatures speak for themselves. Nice job, nice bends as well.
Hey question, my motor burned up and started smoking and wouldn’t work anymore. I ordered and replaced all motor components. Ran a few boards thru and I could hear the motor going slower and slower. Lots of sparks coming from back of motor area. Can you point me in the right direction as to what might be going on? I would think a completely rebuilt motor would run like a champ.
I've read that people see sparks. I've never watched the motor while running mine. Honestly, I don't know why your motor would be slowing down. Maybe taking too large of a cut? I baby the thing when using it and run very conservative cuts. The motor I rebuilt came from someone who admitted to taking big bites in poplar. I'm sorry I don't have better answers for you.
At 11:25 do you see those caps he took off that is the brush port cover remove and pull out the little square things with a spring on it that is the brush. Clean or replace and see if that works.
Hello, thanks for the video. has the pump prevented the freezing or did you have to use a heater? Thanks again
Thanks so much for putting these videos together. I'm about to go through all this myself and you are the only one I can find who has filmed this process. I was a lot more nervous before I watched you videos. Appreciate it.
So the hot air that radiates from the cooler is now being pushed over your (already) hot compressor head?
I can't believe you have never bent tubing before! Nice, tidy, symetrical bending job! Smart choice to purchase a better, larger quality bender, which makes non- crushed, smooth radius bends. Cheap "ain't" good, & good ain't cheap. I used to bend & install stainless steel (SS) tubing from 1/16" to 3/4" for LPG & CNG. That 1/2" & larger was so tough that we used gear reduction benders from Swagelok, if I recall correctly. Anyways nice install. Oh, I think you will get cooler outlet temps. closer to ambient with the addition of an electric fan ducted to force all fan air thru the cooler (for greater water condensation), & get more air over the pump fins to boot! *Two YT comp. air related channels for you or your viewers: #1) THE Compressor Guru (Bud Stiner), tech. videos for DIY's, #2) Doug Kronemeyer, engineering level knowledge on max. efficiency passive moisture removal in 3 parts (DIY #9.) Best complete logical info. I have found yet for small shop & hobby air systems! Paul from S. Central Tx.
exactly which aftercooler did you use with the 10an inlet and outlets
Here is the one I used. The price has went up about $25 since I did this project. Derale 51910 19 Row Core Stacked Plate Cooler Kit a.co/d/4DCTurb
You did a great job with bending that copper tubing but I have one concern, how are you going to get to the back of that compressor to change a belt or what ever needs to be done, I would build a small enclosure outside of the shop and put that compressor out there and not have to listen to that noise,
I have been in that shop!
excellent mod to that compressor, it is the best way to have a shop pneumatic network that is free of condensation .
Great job, your tubing bending skills are far better than mine! 👍
So your copper hookups to the 10AN cooler.....did you step that down to 8AN and flare the copper ends ?? ....or did you go 8AN to 1/2 NPT and used a compression fitting?? Nice setup !
This fella did a similar drying scheme using a remote t5ransmission cooler czcams.com/video/yDOna_Yy69I/video.html
How much ceiling height do you think you need, for what you have. Thanks
My ceiling is about 9 feet. You could probably get by with a touch lower. It would just really depend on the size of your collection bin.
What size are your main runs, 5"?
I did 4 inch. I don't have a very large space and I'm usually only running 1 tool at a time. Once in a while I might be running the CNC and another tool.
Wow the focus motor on your lens is loud. What are you shooting with so i know to never buy one?
Next try getting a cone air filter like the ones for cars or better yet get a full air intake housing off of a car and use it as your compressors air filter. Makes it much quieter..
You talk and act almost exactly like the ksr dude kevin…. Like could be his brother almost.. lol. Check him out on youtube if you dont know who im talking about.. search ksr and pick a video.. see if you cant tell who im talking about..,
Great video thanks 👍 I have same Delta extractor and I’m going to follow your example.
?
Did you list all the pvc parts and materials ? It looks like you used more pieces than I see listed
What size PVC pipe? How many inches from the bottom did you drill? What size bit did you use to drill in the barrel?
a bigger tank cools the air
Hi and thanks for the video but I’m confused where the pump comes into play. Can you elaborate?
Backbeat Woodworks, what did you use to bend your copper tubing with? I'm currently working on adding a cooler to my compressor. I was able to bend most of my tubing by hand. I made it all the way to my water trap with out a problem. Coming out the other end of the water trap, I will have to make quite a bit of 90 degree angles to make it back into the tank. I tried bending that by hand with no luck. I'm using 1/2 in od 3/8 id copper. I found out it's hard to find compression fitting elbows for 1/2 in. My compressor is set up like yours
I used a tubing bender. It's really the only way to bend it without kinking. You can see me using it in the video. I'm not very good at it, but it worked out.
@@backbeatwoodworks I borrowed a pipe bender and a tube bender from some buddies. They kinked it. My local hardware store had the correct kind, but they didn't have one for 1/2 tubing. Looks like I can only find that online. I've learned that's it's hard to find a lot of fittings for 1/2 in copper tubing
When free-hand bending the cooper pipe, especially sharp bends, you can fill the tubing full of dry sand and tape or cap off the ends. The sand will support the tubing and keep it from collapsing.
nice work
Nice job 👍
Check out my air comprsoir after cooler at my u tube channel Stephen eggert..its a Saylor-beall.