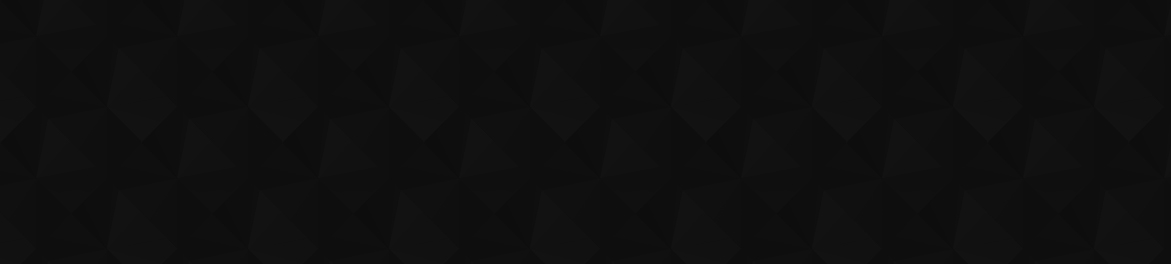
- 101
- 98 811
Daryl Smith
United States
Registrace 4. 10. 2013
My friends call me Daryl and I have been a machine builder, rebuilder and CNC service tech since the 1980's. I love what I do and love teaching others. That is what this channel's content will be about. Passing on what has been taught to me by others, and through my own experiences.
I have never had a job because this has always been my passion, building, rebuilding, or taking an old piece of scrap cast iron or machine and turning it into a useful tool again. The paycheck is just icing on the cake as the saying goes. My customers know that it's not about the money, it's about helping them out when they are in a bind. Honesty, hard work and kindness is what I am about.
I do scraping, spindle rebuilds, turret rebuilds, and add videos of doing all three. The smiley face water tower was taken when I was on a job in West Branch MI and the lightning was on a job in Muskegon MI.
I sell the things I fix on the link below.
I have never had a job because this has always been my passion, building, rebuilding, or taking an old piece of scrap cast iron or machine and turning it into a useful tool again. The paycheck is just icing on the cake as the saying goes. My customers know that it's not about the money, it's about helping them out when they are in a bind. Honesty, hard work and kindness is what I am about.
I do scraping, spindle rebuilds, turret rebuilds, and add videos of doing all three. The smiley face water tower was taken when I was on a job in West Branch MI and the lightning was on a job in Muskegon MI.
I sell the things I fix on the link below.
Okuma Genos L300 System Parameter 2
How to turn on hidden parameters and turn off parameters that you don't want operators to see.
zhlédnutí: 117
Video
CHANGE YOUR HYDRAULIC OIL!
zhlédnutí 991Před 8 měsíci
It's important to change your hydraulic oil at least once a year and use the oil that the manufacturer recommends.
Replacing o-rings on a Hardinge Collet Closer
zhlédnutí 279Před 8 měsíci
You don't have to disturb the bearings or bearing preload if you are just replacing the o-rings. I have replaced o-rings on Kitagawa, Samchully, Tomfu, and Hardinge collet closers or better known as rotary actuators. I have done them on Okuma, Hardinge, Haas, Mori Seiki, and Daewoo lathes. The o-rings wear out, and oil will start leaking out of the chuck end or the back end. It's usually a 4 ho...
How to turn on auto turret angle compensation on Okuma turning centers.
zhlédnutí 127Před 8 měsíci
How to turn on auto turret angle compensation on Okuma turning centers.
Okuma LB4000EX resetting x-axis zero position after a turret crash.
zhlédnutí 726Před 9 měsíci
Okuma LB4000EX resetting x-axis zero position after a turret crash.
LB4000EX turret tool plate alignment.
zhlédnutí 132Před 9 měsíci
LB4000EX turret tool plate alignment.
LB4000EXII turret and machine alignment tips after a bad crash.
zhlédnutí 374Před 9 měsíci
Where to start on a turret alignment after a bad crash. Warning! Do not move any axis with the gib screws loose. Example: if you loosen a z-axis gib screw on the spindle side, then jog the slide to the right (Tailstock side), you will probably wedge the gib and get a servo fault. It will be a bad day! Been there, done that! DO NOT MOVE ANY AXIS WITHOUT THE GIB SCREWS TIGHTENED UP. 1- Adjust all...
A day in the life of a field service tech. I should have stayed in bed.
zhlédnutí 180Před 11 měsíci
The date code on tires will be on one side only. It's a 4 digit number in an oval. The first two digits are the week, the second two are the year. So 2022 would be the 20th week of 2022. It's not worth the gamble to buy tires that are older than a few years, even if they look good or even new. The thumb nail is of the car after I climbed out of it.
Unloading a Clausing Colchester lathe the easy way.
zhlédnutí 347Před rokem
Unloading a Clausing Colchester lathe the easy way.
Checking flatness on a new Challenge surface plate with a Rahn Repeat-O-Meter.
zhlédnutí 1,3KPřed rokem
Checking flatness on a new Challenge surface plate with a Rahn Repeat-O-Meter.
Scraping or picking? What works for you?
zhlédnutí 1,5KPřed rokem
Scraping or picking? What works for you?
Solid Rock Indicating Transfer Stand and Squareness Checking Fixture
zhlédnutí 326Před rokem
Solid Rock Indicating Transfer Stand and Squareness Checking Fixture
Removing the tool plate from a Conquest T-42 turret.
zhlédnutí 157Před rokem
Removing the tool plate from a Conquest T-42 turret.
Hardinge Conquest T-42 Live Tool Drive.
zhlédnutí 721Před rokem
Hardinge Conquest T-42 Live Tool Drive.
Learn to read your bluing after printing a surface.
zhlédnutí 1,1KPřed rokem
Learn to read your bluing after printing a surface.
Daewoo Puma 2500 LSY Live Tool Alignment / Spindle Orient
zhlédnutí 426Před rokem
Daewoo Puma 2500 LSY Live Tool Alignment / Spindle Orient
Scraping is physical and mental therapy for me. 😀
zhlédnutí 3,1KPřed rokem
Scraping is physical and mental therapy for me. 😀
JC Busch straightedge scraping projects
zhlédnutí 501Před rokem
JC Busch straightedge scraping projects
Repairing a Daewoo Puma 2500LSY turret after crash.
zhlédnutí 294Před rokem
Repairing a Daewoo Puma 2500LSY turret after crash.
Does the shim pack act as a slip surface in event of the spindle crash or locking up?
I believe it sets the backlash between the live tool drive gears, John. The live tool housing would rotate with the tool plate when crashed, so it isn't like most other live tool turrets where the drive system is mounted to the main body, and then is misaligned after the tool plate gets hit. Thanks for the question!
@@OtherBrotherDarylSmith I just saw your other video of the disassembly of the gear and saw the key way on the shaft so i figured my I was wrong. Thanks for replying! I’m trying to figure why live tool spindle on an Okuma losing power. Like it’d slow down if I squeeze on the spindle. I thought there may be a clutch built in.
@@johnngo9690 What model of Okuma do you have? I have been inside most of the Okuma live tool turrets. On most Okuma turrets the tool plate alignment is critical, as the tool plate/live tooling mount becomes mis-aligned to the drive unit.
@@OtherBrotherDarylSmith LB4000exII is the model
@@johnngo9690 Hi John. The tool plate alignment is critical on the LB4000 Okuma lathes because the live tool drive uses a shaft with a slot in the center to drive the live tools. The alignment will be good left to right, but up and down will be off if the tool plate is not aligned correctly. This will cause a camming action when the tool drive slot turns to the horizontal position. If you were able to engage the live tool to the drive and spin it by hand you would feel a bind as the slots goes horizontal and then snaps to the vertical position. The live tool will be noisy if this is happening and will get louder as the speed increases. It will also start wearing the flat ends of the live tool drive shafts and the slot in the live tool drive.
Superb again
Bhai tool jal jayega RPM kam karo..?
Any chance you could make one of these showing us the proper method for aligning the sub spindle to the main?
I am currently turning down most of my jobs due to health issues, but I did do a tailstock and turret alignment on a Genos L300M last week. The first thing to do is make sure a spindle is straight. To do that you cut a diameter about 8 inches long, then check for taper with a micrometer. They diameters on both ends should be the same. Do that on the main and sub-spindles. If they are both straight you can chuck up a gage pin in the sub-spindle making sure there is zero run-out. Then tram that gage pin using a co-axial indicator in the main spindle. Another test would be to use the same tool and cut the same diameter on a part in both spindles and check the diameters with a micrometer. They will be the same if the spindles are aligned correctly. Those are two different different ways to check the alignment without using test bars. It is always easiest to install a test bar with the same diameter in both spindles and check both with a mag base and indicator mounted on the turret while moving z-axis. This will check spindle straightness and alignment, but you need to make sure the test bars have zero run-out. You can split the run-out in half at the indicating point if there is run-out. There are always two planes that will be straight on a test bar or cylinder square if there is run-out. Email me if you do not understand that and I will call you. It's hard to explain in a message. If I do another alignment I will try to do a video.
Woow nice Maschine Greetings from Germany Peter
Welcome Peter!
😎@@OtherBrotherDarylSmith
300 win mag works in 1/2" collet. I usually have to do smaller swiss machines. I usually tell people when they buy machines, get a 1/2,3/8,4mm collet on top of what they are going to run
When gathering the blue, only put pressure on one edge of the plate. If you press first one side and then the other you may miss a totally convex surface.
Hi Daryl, can you help me? My UCMB card was damaged. I restarted the system but I don't have the backup of the parameters. I have already been adjusting some. Now I have to adjust the tailstock ones because when I want to turn the spindle it gives me an alarm 1749. I thank you. Help, the lathe is a capitan l370 control OSP E100 L, THANK YOU
My email is on my about page. Send me an email with OSP-P100 in the subject line. Everything should be backed up on windows. I can send you a procedure to reload everything. Daryl
I can't find your email
I send you my email
@victorsalasgavia6610 There is a tab that says "view email address" that you have to click on. It's under channel details.
@@OtherBrotherDarylSmithI can't locate it just your instagram
I tried finidng your email on the about page but I couldn't. Im currently in the process of rebuilding a conquest T42SP no live tooling 12 tool turret. Do you think i can get the parts list for this?
My email is on my "about" page. It says "view email address"
For the collet closer you need one 6mm x 108mm o-ring, four 4.5mm x 61mm o-rings and one 2.5mm x 123mm o-ring. I am guessing that these are for your collet closer as this is what I have extras of.
Can you recommend seals for the collet closer and turret for a Conquest T42SP. I'm in the process of pulling it appart to reseal it because it wont hold pressure.
I have a parts list that I usually order before a turret rebuild. If you run coolant, you will probably need more than just seals. You will probably need new bearings and possibly both halves of the curvic coupler. Email me and I will send you a parts list and the procedure to set the backlash between the worm and ring that drives the turret rotation. Daryl
I will measure the o-rings for the collet closer as well.
Cool and simple 👍🏽
very helpful information - enthusiasm is no substitute for experience.
Hello there, the green parts (motor), is from Metabo same used on their angle grinder, you can easily find some old one (like new) here in europe, just have to reverse rotation of the armature.
Yes, the grinder is a Metabo ST EP 564, but they are hard to find in the US.
@@OtherBrotherDarylSmith i can help to collect some if necessary ;)
Love what your doing! I wish I had more time to give my old machines the love they need
Thank you, Craig. I love that you help Kimber out as much as you do since I am not close enough.
Hello Daryl Previously you helped me with my spindle alignment of Harding t 42sp. Thanks you for guidance. But there's now issue with same machine tailstock it's not working manually with - la and +la switch, but by giving command in mdi m84 it's coming forward but when I use m 85 to retract it doesn't go anywhere stuck at that position. Please help me with this issue...
It sounds like a switch issue, especially if you don't use the tailstock often. There is a Balluff switch block that will have several proximity switches in one block. Try to clean it with electrical contact cleaner and make sure that one of the switches isn't stuck down after the dog pushed it down.
www.balluff.com/en-us/products/areas/A0001/groups/G0113/products/F01302?page=1&perPage=10&availableFirst=true
The above link is what you are looking for. It might even be a broken wire. Best of luck, Daryl
Do you have any electrical drawing for tailstock circuit ?
When I take chuck close valve from solonoid and put it in rapid to speed valve talestock goes backward in feed. And also rapid to speed valve bit 6 is on .
Daryl, you aren't being lazy, you're enhancing your efficiency! That's you doing your 5S part to help the company... Gotta love screw adjustable gibs, make everything so much easier. A number of our machines (Toyoda's come to mind) use ground shims to set the gibs, arrrggghhh PITA to adjust, - and a nice trap for young players...
Thanks for your comment Marc!
Damn I couldn’t really hear that well and I accidentally hit the input when you said not too ! 😮what do I do in this situation
You need to change that parameter back to your original parameter. Let me know what machine model, serial number, and which parameter. I might have a backup.
Don't run the machine if you changed the first parameter. It could crash if you changed it from metric to inches.
If you have a hard copy of your original parameters, just put it back the way it came from the factory. This is why it is important to have a backup of your machines.
😍😍😍😍😍😍niceeeee
My okuma mx 5va showing hydraulik motor load over alarm. Please guide
It's probably an Okuma MC-5VA, not an MX 5VA, and one of the best mills Okuma made. The overload will take a while to cool down. Let it set for a while, then find which overload is tripped and try to push the small reset button. If you have an amp meter, check to see how much current the motor is drawing. Also, unhook all 3 power leads to the motor and use a megohmmeter and check the winding insulation of the motor. Also, change your hydraulic oil and filters at least once a year. Most machines of that era still have the original hydraulic oil in the reservoir. Preventive maintenance is so your machine will not be down when you need it most.
@@OtherBrotherDarylSmith thanks smith yes it is mc5va , we have pushed it but still problem is there it is from last 3 days . my motor contactor in back side mac unit is not even moving . i have checked all continuity ,even separately check contactor outside,it is fine. showing error 112 always. .in india okuma is very less popular machine so no support is available. we have all the drawings. one blown fuse in cpu card we found and replaced it ,but still problem is there . please help
if you can give us mail then i will drop problem photo to also
@aniveshchaturvedi9886 Where do you see the alarm 112? Is the overload even tripped? There might be something else causing the machine to not come out of E-stop. If you go into manual mode, hit the F8 button labeled "Extend", then hit the F5 button "DIAGNOSIS". What do you see on that screen?
@@OtherBrotherDarylSmith sure Smith I will do and share you tomorrow.
My okuma is showing hydraulic motor over load and it is not resting. Please guide
It's amazing how many people think that manufacturers specifications are just suggestions, and that the people who built the machine don't know what they are talking about.
You shared that knowledge with me years ago I really appreciate your sharing on things like this.
Good to hear from you Steve. I hope things are getting better for you. Hang in there buddy.
I think thing are finally turning around. The last few months I tried a different approach to my health problems and believe it is working great. I feel better now than I have in 4-5 years and it is staying that way so far. Lost almost 30lbs as well. @@OtherBrotherDarylSmith
Easy
Yes, it takes less than 5 minutes to adjust all 3 of the x-axis gibs. I was intending to show the complete job, but then I knocked my phone over, lol.
Left hand threads and bolts and someone still wanted to put locktite on it? Thanks for sharing, fluid in that piston chamber looks pretty yuk! Charles
That's why it's important to change the hydraulic oil and part of the reason the seals wore out. Thanks for the reply, as always, Charles.
Like that thank you I have a Hardinge cobra 65 I can't move the Z and X axis I'd like someone to help me with this old lathe
hey not sure about your CNC but on the DMG there is no HOME or referencing in X or Y or Z ; its supposed to know where the mill is whenever you start up. so ,what do i do if i am "0" in APZ "x" and APZ "Y" ( my batteries died i had to replace them) how do i "return" X or Y ?
What machine model and control? I have worked on lot of Mori Seiki machines. Is this a mill or a lathe? I can send you a procedure. Where are you located?
You shut it off after getting the battery alarm. All the batteries do is store the machine's position when power is off.
@@OtherBrotherDarylSmith DMG DMC CNC mill deckel maho i am in london ontario canada thanks
sorry i thought that was a question? i always thought you'd change batteries with the control on that's what i did but the DC0300 alarm messages for Return X and Y wouldn't go away
@@fredrezfield1629 What control? DMG has their own numbers, but I am assuming it's a Fanuc with a DMG number.
How much of an adjustment would you make? Obviously if the screw is loose youre gonna take that up, but whats the "touchy feely" amount of turning past snug? I have to adjust mine. I noticed today the turret was shifting. I checked the spindle side keeper and the was 2 turns loose. I will check the keeper and the positive on the other side tomorrow. But this will be my first time adjusting box way taper gibs on a CNC lathe. How much to snug since i obviously cannot slide the turret back and forth to "feel" the resistance... (1981 takisawa ts-15 thats been reground in the last 500 hours before me)
Is there a screw on each end or one screw with a lock nut? I like the z-axis gibs snug. My suggestion would be to write down the load percentage for that axis. It's probably going to be single digits. I would adjust the gibs one at a time and make sure that the load increases. I like to see around 10 to 13 percent on the load monitor after the z-axis gib adjustment. To bring up the load monitor on a Fanuc, hit the "Position" hard key, right expansion arrow key, and "monitor" soft key on the right side of the screen.
I dont need this information. I probably will never need this information, but i now know this knowledge
You never know. Someone might ask you some day, lol. Thanks for the comment.
Pretty neat problem, thanks for sharing. Charles
Hey Daryl would you come to the UP michigan for a cnc repair job? We are in the soo.
I have probably been there 10 years ago when I worked for Gosiger. I put a Prex spindle back together that someone else tore apart. It was on a LB4000EX I believe. Do you work for R&B Electronics? I am pretty much slowing down right now since I don't have a good service vehicle after rolling it. It was a total loss. I would be glad to assist your maintenance department over the phone. What problems are you experiencing and what machines?
Yes I am with R&B. We don’t have anything broken at the moment lol. I found your videos because we have a few Harding t42s and there aren’t many people doing videos like yours(keep it going!). We also have an okuma lb3000ex. Maybe that’s the one you worked on. It did have a spindle issue when it was in warranty. Do you know Robbie Keel?
@@AllieRogers-mq1kf Yes, I rebuilt the spindle on the LB3000 you have. Robby was fairly new at Gosiger when I retired back in 2017.
Please contact me if you have any tools for sale for a Hardinge ESA turret tool plate.
God bless you Daryl for these videos!❤
good explanation of the process, doing thins in the wrong order can cause a lot of headaches. Charles
Nice
Great info, Daryl. So to adjust the gibs, you're just tightening till you feel snug. I assume this is a very touchy feely sort of adjustment. I've torn my whole takisawa ts-15 down to nuts and bolts before, but I've never readjusted the gibs. I recently discovered some slop in the X slide and not sure if it's gibs or ball screws. But feel gibs should be the first thing to address. I am assuming when I get in there, I won't find much in the way of "snugging room", so how should I determine how much to tighten the gib screws? And which ones? All of them? Keepers and positive?
We've got an old Takasawa at work, I think it's a TS series, been a really good machine for the past 30 years or so. Unfortunately, I've never had to deal with adjusting the gibs on it, so I can't provide any specifics. Be aware that not all gibs are screw adjustable, some use shims that have to be ground down or other methods. You have to keep in mind that the ways tend to be a lot more worn close to the spindle/centerline where it spends most of it's time. If you adjust the gibs in the worn area, it will start to bind as you get closer to reference position (assuming that's set with the axis' at their positive end of travel). Depending on the amount of wear you may not be able to get all the slop out of it without binding at the ends. Most controls have some way of monitoring the load on any given axis. When I'm adjusting gibs on clapped-out machines I watch the load monitor and tighten them up as tight as I can go without causing too much load with the machine referenced. You don't want the axis sitting with a 90% load when you home out the machine, you just have to compromise the best you can, or learn how to scrape ways back in!
Tight spaces, I see a lot of walking around the machine just to get to them. Thanks for sharing. Charles
I like to tighten all of the gibs. It is a feel thing, but if you have a load monitor on the controller, you can use that. Write down the loads in both directions and check it after adjusting the gibs. The reason I don't back the z-axis gibs out a 1/4 turn on this machine is because they are pushing a 2-1/2" x 14" long drill. The x-axis gib, I snug them then back them off a 1/4 turn. To access the load monitor on a Fanuc 16 or newer, hit the position hard key, then the right expansion arrow, and you will see a "monitor" soft key on the left hand side. Okuma states to not exceed 35% load, but I like to see about 10 to 12 percent load after a gib adjustment. X-axis will be different load going up as opposed to going down due to lifting the weight of the turret and no counter-ballance. I like to see 10% going down and 30/40 going up on x-axis.
@@OtherBrotherDarylSmith Awesome idea.
Nice
The labyrinth has got to be flat with zero run-out. If not, the run-out will be visible on the spindle arbor. There is also a collar that preloads the rear taper roller bearing, so the run-out on that collar is also critical. This magnetic table is the perfect for grinding these, and it is easy to use. Thanks for noticing!
The scraping is holding up well! Is that what 50 percent bearing looks like?
I didn't print it, but yes. It is probably 10 points per square inch.
That method is new to me. Is that the method Moore recommends? I have always put the quill in its top position and indicate at top of quill.
Yes, that is the way Moore recommends to zero the taper. I got the instructions from Moore. I have repaired a lot of Moore jig grinders when I worked for the Michigan representative for Moore.
ty. The quill method worked well but finding someplace for the mag base to stick was a PITA. I will try that tomorrow to see if i am off any. No one askes me to grind taper anymore. With carbide die taper is just preformed in. I havent been in a die shop for 17 years though.
Glad you are O.K Brother. I haven't been so lucky. Lost a good mate, last Thursday week. Funeral is Wednesday.
Sorry to hear that Phil. This happened several days after losing my younger brother due to falling off of a golf cart. I know the meaning of "survivor's guilt".
So happy you were not hurt brother. Steve
Glad you are safe.
Thats no way to get a some custom bodywork, or to buy tyres for that matter. Are you ok and has the shock passed yet?
I spent six and a half hours in the hospital ER getting all kinds of tests and x-rays. They said no internal or brain injuries and now broken bones. They asked why I was there during check in and I just pointed at my wife. 😀 She was pretty insistent that I got checked out.
@@OtherBrotherDarylSmith best to check, not all Injuries are obbious. I fell down a flight of steps, they did a full body scan but all i had was a small bruise on my arm, oh and pneumonia the cause of the fall.😉
yikes….tools must been flying….glad u are ok
My tools are a mess. I had them pretty organized in stainless steel tubs, but nothing is in the same box now that they are in my shop. A lot of organizing to do. I went on a call today with minimal tools.
Never had a tire do that, and hope I never do. Thanks to hear you are ok. Charles
Oh crap! You were darn lucky. Glad you are okay. At least it sounds like you are. Man, there doesn't appear to be one sheet of metal that doesn't have a dent of some sort in it.
I was able to get out on my own, a struggle but managed. Not a scratch, which is crazy with all of those tools flying around, It was a hard hit for sure. I was on an express way where the speed limit was 70 MPH. I won't say how fast I was going, lol.
Yeah, I was wondering how you managed with a back end full of stuff going every which way!@@OtherBrotherDarylSmith
@@OtherBrotherDarylSmith Who cares about the car, are the tools okay?
@@duanedickey7043 The tools that were still in the car are fine. Unfortunately I probably lost some tools when the car flipped. I had the windows half way down. There were tool all around the car in the dirt. I should go back with a metal detector, lol.
Thanks a lot for this video and pointing me to Ed Dyjak, I got my used Euro BL-40 cleaned up and brushes changed .
I have a Hardinge 65 cobra with GE Fanuc Series 21-t controller it look's the same as yours looking for some help
I am not sure how I missed this comment. Did you figure it out? Did you email me? I can't remember. Daryl
I,d like your help my Harding cobra 65 is not working if you have WhatsApp on you cellphone I can send you some videos I'll pay you for time. I'm from Asuncion Paraguay
@@OtherBrotherDarylSmithhello
@@abramfriesen9834 Did you figure it out?
No not get I'm thinking it might have to do with are electricity Paraguay has 380V 3 phase 220V single phase 50Hz @@OtherBrotherDarylSmith
With straightedge?using stone on circular sometine not so good
As always, thanks for your comments Fabioth. All of my stones have been ground flat with a diamond wheel, so they will not scratch the surface when stoning. They take down the burrs only. I always tell people to have their own experience, and I only share my experience. This works for me, but I am sure there is always a better way to do things.
@@OtherBrotherDarylSmith its ok.i use a Norton stones,just i see some persons using a stones on circular,but me i never do that because i think is no good do it on a surface.just it
Show it with blue paint
This video couldn't be better. It workt perfectly with the X and Z axis alarm on my Schaublin 125 CCN (Series 20-T). Thanks a lot👍🏻💪🏻