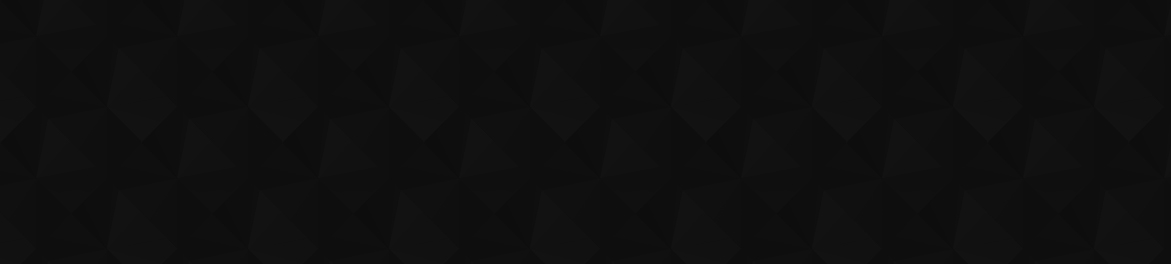
- 37
- 22 793
Strata Art Studios
Canada
Registrace 23. 08. 2015
A couple of creatives, living and making on Canada’s East Coast.
37. Acorn & Oak Leaf
Here's a short clip of a wax carving in preparation for lost wax casting. These will be cast in sterling silver and oxidized to bring out the detail.
Filmed with iPad and edited in iMovies
Music is "Simple" from iMovies Soundtracks
Filmed with iPad and edited in iMovies
Music is "Simple" from iMovies Soundtracks
zhlédnutí: 147
Video
36. Custom Silver Anniversary Rings
zhlédnutí 79Před rokem
We were approached by a couple wishing to celebrate their 25th wedding anniversary with custom rings featuring the place they love. Bear River, Nova Scotia is where they met, fell in love, and ultimately raised their family. The outline of the river runs through the centre of each silver ring, connected to a Nova Scotian amethyst cut and polished in a teardrop shape. This video shows the journe...
35. Custom birthstone ring
zhlédnutí 72Před 2 lety
This is a process/build video for a custom birthstone ring that starts with sketching designs and follows through to the finished ring. The design incorporates three bands to represent three daughters and their Mom's May birthstone. If you have any questions or comments, please feel free to add them below. This video was completely shot and edited using an iPad. Video was edited in iMovies app....
34. Custom White Opal Sterling Silver Ring
zhlédnutí 33Před 2 lety
This is a process/build video for a recent custom ring that starts with sketching designs and follows through to the finished ring. This video was completely shot and edited using an iPad. Video was edited in iMovies app. Music: 'Simple" from iMovies theme music.
33. Carving a wooden dachshund sweater pin
zhlédnutí 227Před 2 lety
Here is something a little different from my normal jewellery build videos. I was asked to create a sweater pin that look like a dachshund. So accepting the challenge, I looked through some speciality wood pieces in my stash and decided on mahogany. This is a build process video that follows the progression, from sketch created using Procreate, cutting out, sanding and finishing this little dog.
32. For the love of sunflowers
zhlédnutí 53Před 2 lety
I was asked to create a custom pendant using a client's ring. Her yellow gold ring was cast as the sunflower and the diamond was set in its centre. This was added to a silver heart pendant base. This is a build video following most of the processes used to create it.
31. Reproducing a hollow form object
zhlédnutí 282Před 2 lety
This is a build process video showing some of the construction of the original model as well as some of the work done in wax before it's cast in sterling silver. It's an example of how with a little design forethought, you can make life easier for yourself when it comes time for reproduction. This hollow form casting worked because there were lots of points throughout the design to allow and ho...
30. Not Another David Attenborough Nature Documentary
zhlédnutí 53Před 3 lety
In this time-lapse video, watch a snapping turtle mama make a nest at the end of our driveway. Snapping turtles are on the Species at Risk list here in Nova Scotia, Canada. (Apologies to David Attenborough.)
29. DIY Jeweller's Tool
zhlédnutí 218Před 3 lety
Have you ever tried to carve something small in wax but found you struggled to hold it steady? Early on I stumbled on a quick and cheap way to hold on to small carvings while you work.
28. How thick is my wax carving?
zhlédnutí 255Před 3 lety
If you ever wondered if there was a quick way to determine the thickness of the wax you are carving? Well, here is one way. Hope this helps someone out!
27. Our first attempt at making maple syrup.
zhlédnutí 29Před 3 lety
We decided to tap our single sugar maple tree this year to make some maple syrup. Chris spent a few springs, as a kid, riding on the tractor with his uncles while they collected sap. The day was then spent in the sugar shack boiling down the sap into syrup and bottling it. This is what we have managed to do so far this spring. We're hoping to get a little more before the weather becomes too war...
26. Building a better set of stairs.
zhlédnutí 28Před 3 lety
Let me start by saying that I am not a contractor. This video is a quick overview of a replacement set of stairs that I built in the garage. The original stairs were narrow, extremely steep, and not well supported. You can watch me remove them in this video: czcams.com/video/6HBRyYjR9TA/video.html The stairs needed to be replaced before we insulated and finished the second storey workshop area ...
25. A Christmas Tradition.
zhlédnutí 25Před 3 lety
Lorna and I started a Christmas tradition the first year we were together. We decided that we would make or purchase at least two ornaments for our Christmas tree every year, to represent something that happened or a memory that we wanted to mark. Thus creating a tree of memories that grows over time. These can be silly like the red glass heart with Jack Skellington and Sally to the clear glass...
24. “Catch of the Day” pendant build
zhlédnutí 55Před 3 lety
It was a warm fall day when Lorna and I found ourselves walking along one of the beautiful beaches here in Nova Scotia. She was taking pictures of brightly coloured little sea creatures, seaweed and objects lying around us and I found myself picking up perfectly shaped pebbles smoothed by Mother Nature in the rolling surf of the Atlantic Ocean. When we got home I laid them out and imagined what...
23. A year in the life of our compost bin.
zhlédnutí 20Před 3 lety
The experts say the best way to build healthy soil is by adding organic material. All year long we collect leaves, lawn clippings and plant trimmings in our compost bin. With some water, the occasional turn and time, it goes from recognizable leaves and such into rich, dark compost that plants love. All it takes is patience and a little sweat to make some wonder stuff for your garden. Worth it!
21. DIY Plumbing Tool - How to remove a tub drain with a branch.
zhlédnutí 52Před 3 lety
21. DIY Plumbing Tool - How to remove a tub drain with a branch.
14. A flurry of activity in the chicken coop!
zhlédnutí 40Před 4 lety
14. A flurry of activity in the chicken coop!
10. Jewellery basics: "How we make our jumprings"
zhlédnutí 178Před 4 lety
10. Jewellery basics: "How we make our jumprings"
9. A Big Thank You & Time Lapse Stair Removal
zhlédnutí 52Před 4 lety
9. A Big Thank You & Time Lapse Stair Removal
Despues de colocar el modelo y antes de cubrirlo con el resto del hule,debemos llevar bricar el hule con tqlco,procurando NO tocar el modelos.Esto vá ayudar abrir las 2 partes del n tener que cortarlo.Una vez vulcanizado el molde,se deja unos 10 mtos mas en la plancha a fin de prevenir un buen vulcanizado.A contnuacion el molde se ahoga en petroleo durante 24 hs.el mold se incha ampliando el grabado asta 500 veces,despues con parafina obtenemos una copia mas grande. Proceso "jonapru"
Creo que es mejor al iniciar el vulcanizado del molde ,la mitad del mismo se cubre con una delgada capa de talco,esto ayuda a que despues devulcanizado el molde se abra sin necesidad de cortarlo. Si elmolde que se vulcaniza es de hule para llantas,este tiene unas propiedades increibles,el molde despues d vulcanizado se ahoga en petroleo durante 24horas,elmismo se incha asta un 500/100,aumentando de tamaño el grabado..despues se le cuela parafina,obteniendo una copia d mayor tamaño. Proceso "jonapru"
👍
Could you please tell us the name of the tool/clamp to help hold the mold so I can google it? Ive been trying to find one for a while but not knowing what those specific tools are called has made it impossible for me to fine one.
I have spent a few days looking for something commercial with no success. You can use a bench vice, but try to only grab your rubber mold on the ends away from your model so as not to crush the model. I have seen people use vice grip pliers to grab molds as they cut. These have been modified to be attached solidly to your desk top so you can pull the mold. If you have a bench vice that is bolted down you could clamp the vice grips into it.
@strataartstudios3826 Thank uou for trying to help. ❤️ I finally found one on Amazon. Others looking can do a search for 'RETRACTOR 2X3 PRONG BLUNT/BLUNT 4 1/2 INCHES'.
1) Best video yet. Liked the use of different angle shots 2) Video was around 11 minutes. About how long did it take in real time? 3) Did you or they come up with the use of the landscape in the ring? 4) Do you design the ring, have an idea of amount of time to create and then give a quote, or give a rough estimate and then a final price after you have done the work? 5) Your fingers were awfully close to that blade! 6) The iPad more then seems adequate for your videos 7) Do you have many more tools that we have not seen so far in your videos?. My first time seeing that blade thingy, that multiple drum sander, and the pivoting clamp thingy. It was cool seeing them. Should show them all more often 8) By this time in your career have you reached the point where you already know how to build a design, or is there still the occasional one come up you have to sit and figure it out?
1. Thank you. I am trying to improve. Every change of angle means moving the iPad around to new location. So it means work, stop, shift iPad, work, stop, repeat. 2. I worked on these rings over several days. 3. When meeting with the client and getting the all different inspirational, the area where they live was very important to them, so that is where I got the idea to do the river. 4. I always design first. You need to know as much about what you’re going to build to give an accurate quote. 5. Do you mean when I am cutting the stone? If so it is a diamond blade, no teeth. So it will cut you but it would take a bit. It slowly grinds through the stone. 6. I asked a videographer once what would be the best to use and his response was the best you can afford or whatever you have on hand. Just shoot your videos. So the iPad is what I have and it seems to do a decent job. Some day I might get something better so that I can do better closeups and other things. 7. Equipment usage is completely dependant on the design being created. When I do more stone work in the future, the lapidary saw and grinder will most definitely make a reappearance. 8. There are always new techniques to learn and things to figure out. But typically when I am designing something it is done with the skills I already have, so the build process is worked out in my mind as I design.
Your video making skills have come along way from when you started making them. Were the different sketches made as choices for the family?
Thanks, I am happy to hear that. Yes, when I do sketches for a client I will riff on a theme. Gives choice as well as narrows down the final design until you find the right one.
Super cutting. Can I cut a big piece like 1.5x2.5 inches laxmi murti.
I don’t see why not. I have cut thicker molds in this manner before. Just keep in mind that the thicker the rubber the more resistance it gives as you try to bend it.
remembering i'm on old guy now just clicked what your logo is composed of
It is S A S graphically overlapped. Design-wise it has hints of several cultures, sort of Norse or Celtic knot work (without the over and under), and Asian seal or chop (which is a carved stamp, usually used as the artists mark on paintings or calligraphy).
how late in the process would you not of been able to make the correction?
There are a number of ways that the pendant could have been rebalanced. The bail could have been moved off center to achieve a level heart. More decoration could have been added to offset the weight. The only thing that would add risk to alterations would have been if the stone had already been set, although there are ways to protect the stone from the heat of the torch while soldering. But if you were worried about that the added design could be riveted in place.
Good editing job... flew by. now where it is a custom ring does that mean it was made for someone with ring size already known?
Thank you. Yes, it was made to the requested size.
Really wanted to see how you cast it.. kinda weird watching you carefully manipulate the mold with those mitts of yours
Yes, I really need to start including the casting in the videos. At the very least making one about the casting process. I guess I am just used to fiddly work after all these years. Where there is a will there is a way.
So how long did it take real time to make?
It was completed pretty much in one sitting over an afternoon.
WOW... I never realized how much detail goes into making such a 'masterpiece'. Beautiful work.
Thank you for your kind words.
Не понимая английский. Я всё прекрасно понял. Практично и по существу
Thank you. I am glad it was understandable.
Good advice for sculpting rings!
Hermoso trabajo
Thank you!
Hello my friend Thanks for this nice video I have a problem When injecting wax into the mold Next gets .. First, a deformation of the model Second, the wax came out from everywhere Third, there is incomplete presence of the wax inside the model or half of the figure and is weak ...
There are many things that could be causing this. 1. Are you holding the rubber mold with a metal plate on each side? This means that you can apply an even pressure over the entire surface of your mold. 2. Are you squeezing too tightly? If you are, this can distort the rubber preventing flow and also possibly opening up an area for it to leak out. 3. Is the pressure of your wax injector too high? Higher pressure may cause the wax to squirt out. 4. Is the wax in the injector at the right temperature? If too high, it will cause bubbles and sticking to the mold. 5. How long is your injection time? If not long enough then you are not giving enough time to fill. I count to three to give it enough time to fill. 6. Are you cleaning all the wax off the mold between injections? If you leave any wax bits stuck to the mold from one injection to the next, you run the risk of it holding your mold apart and causing the leaking you’re describing. I hope this helps.
Thank you my friend I will do as you adviced By following all the steps in detail And see the result.
I have nothing to say. It does what you set out to do. Instruct
Just trying to help.
@@strataartstudios3826 now do you have control over what key words/hashtags used in a search that will lead to your site?
Yes, when a video is downloaded key words/tags are added.
Thanks for the video! Do you have any suggestions for working with pieces that have been repaired? I find the constancy of the repaired area to be a bit different, and it throws me off.
From what I have seen, a fixed break is always going to be weaker than the original solid wax. So you have to treat these areas with extra care. That being said when you do your repairs the heat of the tool you are using is critical to a decent join. If it is too cold the wax has melted but may not actually bond parts together ie. the puddle of wax just wraps around and hardens to create a socket instead of bonding. If it is too hot you are almost boiling the wax and this adds a lot of bubbles. So it is a matter of finding the happy medium. I hope this helps.
Thank you so much. Great video. I look forward to learning more.
You're welcome. Glad it helped.
More carving projects step by step would be really appreciated as i am a begginer and trying to figure out how measurements and sculpting up your wax model is best done and how to use my tools properly 👌 Great Video Many thanks 👌
I will be doing more wax carving videos in the future. I am glad you liked this one. Thanks so much.
Question. you said you were going to insulate the 2nd floor. Would you not have to close off the steps area somehow or insulate the downstairs for that to work heatwise?
it's been an hour since I posted. Where is my answer?
We do intend to fully insulate the entire garage but possibly not all at the same time. So as a stop gap by closing in the stairs and insulating them, we can put an interior door at the bottom and have somewhat of a sealed area. I could styrofoam the undersides of the steps to really close it in but we will see how far I get.
@@strataartstudios3826 so is the area going to be your studio?
Yes that is the plan for the second floor.
Hi Chris, You were right in saying it "is solid". Looking forward to more of this renovation.
Another "step" closer!
What is the name of tool?
I was using a scalpel to cut the mold. You can get them from any jewellery supplier. The other tool I used was an old burnisher to pop out the sprue cone, but you could easily use anything that you have on your desk to do this job. It just happened to be the first thing I grabbed.
Why dont you use all the pink rubber in the mold? Wich benefit the gold has?
The Castaldo gold is less expensive than the pink. So it is just a cost effective method if you’re making a lot of molds.
@@strataartstudios3826 thanks for answerme. If both cost the same, would you always wear pink? Is much better?
The “no-shrink” pink is slightly more expensive than the gold. It saves me say 50 cents a mold to pair it with the gold. That can add up if you are doing a lot of molds. I like the “no-shrink” pink because if you can accurately get your temperatures right when vulcanizing there is less shrinkage loss from your original model than other rubber types. There are so many different types of rubber on the market these days that all have different properties. Try some out and see what works best for how you work.
@@strataartstudios3826 thank you very much! And sorry for my poor english, im from uruguay 😊
No problem at all. Happy to help.
nice carving
Thanks!
Impressive!
Thank you.
Chris down by the creek! watch out for nymphs
Ya it’s a nice place to relax for me and my nymph.
I have to give that film 3 stars due to the lack of character development for the frogs
Well, first, they are toads not frogs. Second, you should support these small independent creatures. With this, their first ever acting gig, they are simply striving to get recognized as true thespians and get a tiny flipper hold in the gigantic world of cinematography.
I have no quip to make about this one. So other then improvements in materials, how old would this method be?
Examples of primitive casting date back to somewhere near 4000 BC. The first signs of lost wax casting is in about 2500 BC. The use of rubber molds, I am really not sure of the dates. I will do some research and let you know.
Benny Hill tribute video? Also how deep are the beds? Deep enough for root vegetables?
Haha! I'm sure that might be a copyright infringement. Soil is 7-8" deep, so not for root veggies but deep enough for everything else we're growing.
@@strataartstudios3826 So why not till the ground instead of those beds?
@@indobson The ground in that area tends to puddle when it rains. We're also using the "no dig" method of growing (add a new layer of compost each year).
What will you plant in them? Too shallow for root vegetables are they not?
Yes, root veg needs about 6 to ten inches of soil depending on type. We are planning on lettuces and leafy greens. Should be fine for them. We will see.
Certainly gives an enthusiastic 'thumbs-up' to the concept of recycling. Great job!
Is it possible to hold your breath for nearly 6 minutes? I watched your demonstration quite intently and surely expected something to go wrong ...the only thing wrong was my estimation of your skill! Well done.
I am glad I kept you on the edge of your seat and thank you.
It would be cool to see how you cast it as well
I will be doing casting related videos.
So does this mean you are The Lord of the Rings?
No, just his jeweller.
Wow! .. great progress on this project.
Thanks! Tackling it a little at a time!
Where is the chickens?
They flew the coop! ;)
Knitting needles!!! Very clever!!
Thank you. I have always tried to find things that work. Knitting needles are measured and size labeled already.
Loved watching your process , beautiful piece !
Thank you.
Good easy to follow video of your process. How much real time did it take to make the piece?
Approximately 5 hours.
But there is no spoon............
Or is it there was always a spoon? As Michelangelo said the spoon was always there, you just needed to remove the surrounding material to free it. Or like Shrodinger’s cat, until you look there is an infinite number of possibilities contained inside.
@@strataartstudios3826 So now you have to do a bowl.........
Yes, that is the plan. Also a kuksa ( a drinking cup ). A future project I want to build is a Viking pole lathe. So both carved and turned bowls.
So how close are nearest neighbors?
They are just on the other side of the river.
That is very cool. Maybe in the nearby town you can find some kind of history of the area?
That is a good idea. We do know that there was a large barrel mill just upriver. They produced barrels for shipping salmon, apples and other local produce. It burned down some time in the 1930s.
You realize your property would be perfect for LARPING
Yes it would. Maybe that is a thought process for future projects.
Exciting! Looking forward to hearing more of your progress in your new home.
Thanks so much! We are excited as well with all the possibilities. Keep watching for more updates.