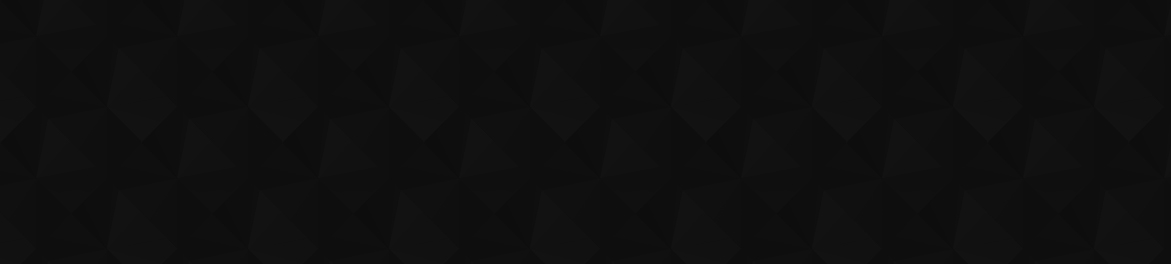
- 60
- 215 231
Lappe Mountain Living
Canada
Registrace 15. 12. 2023
JOIN US IN OUR MACHINE SHOP FOR TOOL AND CUTTER GRINDING, MACHINING, WELDING AND MUCH MORE
Can we sharpen this???
Sharpening a .020" diameter drill bit and drilling a hole with it
zhlédnutí: 1 341
Video
HOW TO SHARPEN THREADING DIES
zhlédnutí 509Před dnem
COMPLETE EXPLANATION OF HOW TO SHARPEN THREADING DIES. START TO FINISH.
SOLID CARBIDE ENDMILL SHANK RELIEF
zhlédnutí 613Před 14 dny
WE'RE USING A DIAMOND WHEEL TO RELIEVE THE SHANK OF A SOLID CARBIDE END MILL SO THAT THE USER CAN CUT DEEPER WITH IT
THREADING TUTORIAL TURNS NIGHTMARE!
zhlédnutí 641Před 14 dny
EVERYTHING THAT COULD GO WRONG DID! AND THEN SOME!
TAPS - DEEP DIVE
zhlédnutí 1,8KPřed 28 dny
How to sharpen taps, (Two methods). Different flute styles. Shank configurations. Rake and clearance angles explained. How to tap a hole. LOTS OF OTHER STUFF TOO
How to modify a grinding wheel AND MORE!
zhlédnutí 2KPřed měsícem
How to modify and dress grinding wheels. In depth discussion on several styles of grinding wheels including different abrasives and different wheel shapes. Some safety tips. Also some wheel setup and speed information.
How to sharpen a dovetail cutter. Full tutorial. All setups explained in detail.
zhlédnutí 6KPřed měsícem
Full tutorial on how to sharpen a dovetail cutter. Three setups, fully explained. Warning! your wife won't like this
Gone fishing! Big thunder storm!
zhlédnutí 224Před měsícem
Join us on our fishing trip. Camp stove broke so had to cook on the fire. Wicked thunder storm, trees down, Had to saw our way out! We had a blast!
Attending our friends annual memorial celebration
zhlédnutí 201Před 2 měsíci
Join us for a fun day out on the bike and hanging out with friends. There'll be motorcycle games and more! Andy got first place in the slow race and Tonya got second place in the axe throw.
How to make fish and brewis. A Newfoundland favorite.
zhlédnutí 73Před 2 měsíci
Fish and brewis has long been a favorite of fishermen and sailors because it can be stored for a very long time.
How to sharpen a roughing end mill
zhlédnutí 4,5KPřed 2 měsíci
Join us in this tutorial as we refurbish a dull and chipped roughing end mill.
How to water glass eggs. 2 year + egg storage
zhlédnutí 340Před 3 měsíci
How to water glass eggs. 2 year egg storage
Making commitment rings for my buddy and his girlfriend
zhlédnutí 1KPřed 3 měsíci
Making commitment rings for my buddy and his girlfriend
Egg noodles made from water glassed eggs
zhlédnutí 92Před 4 měsíci
Egg noodles made from water glassed eggs
modifying a drill bit into a combination clearance drill / countersink
zhlédnutí 709Před 4 měsíci
modifying a drill bit into a combination clearance drill / countersink
We finally got a proper dump of snow!
zhlédnutí 281Před 4 měsíci
We finally got a proper dump of snow!
Making a new spindle nut for our tool and cutter grinder
zhlédnutí 2,5KPřed 4 měsíci
Making a new spindle nut for our tool and cutter grinder
How to sharpen taps and counter sinks @Lappemountainliving
zhlédnutí 58KPřed 4 měsíci
How to sharpen taps and counter sinks @Lappemountainliving
Smithy lathe mill drill. Make almost anything at home!
zhlédnutí 23KPřed 5 měsíci
Smithy lathe mill drill. Make almost anything at home!
New handle for the radius grinding fixture part 2
zhlédnutí 1,1KPřed 5 měsíci
New handle for the radius grinding fixture part 2
*0,508mm in diameter
Little drill bits like that I've found it doesn't matter if they're sharpened "right". Just so long as they're sharp they'll drill. So what I do is just point them up. I know it isn't right, but it works. I've even drilled through steel after just pointing them up. I don't run them slow either. My micro press doesn't do slow. I think it's 3 speeds, 3,000, 5,000 and 8,000? I just leave it in the middle all the time. So 5K RPM.
Before CNC, it would have just been made with a pattern machine.
I'm going to check that out. Thanks!
Great video. Most micro drill bits I end up using in a pin vice chuck and hand drilling. I once managed to sharpen a tiny drill bit by hand using a lapping stone. Luck more than skill, methinks!
:) Thanks for the comment!
Cannot believe I just watched a craftsman sharpen a #76 drill bit! WOW! I use these tiny bits down to the #80 size, and buy them in packs of 12. The brand is Gyros, sold on Amazon, and they’re available in Carbon Steel or High Speed Steel. I use stricter the HSS ones, and they run just under $13 for a tube containing 12 of the same size. Great video Sir!
Thanks for the info. And for the comment! I'm guessing that the cost of these has come down significantly over the last 3+ decades? Cheers!
I usually buy wire size bits in lots of ten. And that is because I use them to drill circuit boards for feed through components. I even made a drill index plate and LAZERed it for each size hole. Then I take any freed through component lead and see what size bit I need to that component. Works really well for my usage... However, I would never try to sharpen such size bits. Too iffy to do that, so I just buy new ones as needed...pretty cheap to buy them. But interesting video anyway. Thumbs Up!
Thanks for the comment
0.5 mm does not seam that impressive :d
I have always been impressed with these micro drill bits. Like you I am awed by how they are made.
Cheers!
I have iPhone and i use magnifier app and you can also use flashlight lens that has broadening and zooming on your camera or typical magnifying glass lmao😂 and with a steady hand you can actually see something like that .0200” drill bit as a 11/16” drill bit. I use a drimell tool with a diamond disc for my small carbide twist drills from 1/8” down to micro drills i purchase from harbor freight I believe smallest is around 10 thou.
Thanks for the comment! I've decided to go old school magnifying glass
I was hoping to see how you would grind the secondary relief on that drill bit and the web thinning :D Just kidding, thanks for the amazing knowledge you're sharing for us!
LOL... Thank you for your comment!
excellent! Interesting and enjoyable. Thanks for sharing
Many thanks!
I would suggest to add text overlays to your video, translating the imperial measurements you are talking about in your video to metric. easy to do in the edit, and it helps you gaining views from the rest of the world who has no idea what a 1/16-1/32 is going to look like
Great idea!
First off even the Empire doesn't use Imperial measurements today. No one does. We use the International Industrial Standard Inch. But you can just call it Standard for short. The Standard inch is the inch that's precisely 2.54 centimeters long. Imperial was two millionths shorter than that. So that's how you can tell them apart.
Totally agree, it hurts my brain constantly trying to convert these fractions to mm
@@khalilbahlawan4439 then get a drill chart. There's one on my Google docs page if you can figure out how to access that. It's a copy of a metal supplier handout. In one column are all of the number, letter and fractional sizes then there's the decimal equivalents and then the metric conversions. It is the Rosetta stone for measuring.
Wow. I could not imagine sharpening anything so tiny.
Thanks for watching! Cheers!
HOW OLD YOU GOOD IDIA.. BEST LIVING☺
Thanks for watching!
Cool, I'll have to have a go myself now. At about what size would you start thinking about setting up a drill grinding attachment? Thanks for the vid. Cheers
Interesting question. I don't have a clear cut answer. My drill grinder claims to be able to handle 1/4" to 3" but I haven't had much luck with drills smaller than 3/4". Thanks for the comment and thanks for watching.
Word on the street is that tiny carbide tooling is ground with lasers. I am willing to guess it's the same with HSS. I can't imagine the bit holding up to some grinding wheel to get those flutes ground . But then again, I've been very wrong before. That being said, if you got more of these needles to sharpen, maybe rig one of them soldering microscopes.
Great idea! Thanks for the comment!
Great Video! I've been looking for videos about end mill sharpening and yours are always great! I'd love to see some test cuts after the sharpening!
Great suggestion! Thanks for watching!
Smithy has a couple of options for motors, maybe you got unlucky and got a weak version. I would contact smithy support and see which motor you have, and if there is an easy upgrade. As I have the same machine, I never really managed to stall the motor, other than I.e. cutoff blade getting stuck
Thanks for the idea. Well worth a try!
I have the same machine... I have adopted the Joe Pie method, putting the tool upside down, and threading away from the head stock.... waaaaaayyyyy less stressful. (I also have a solid tool post, so I just do simple straight in threading)
Self defence and self defence of your property is illegal ?. Wow, nearly as bad as here in the UK. Accuracy on these at close range is brilliant, have loads of damaged bolts to prove it as well.
Thanks for your comment!
I am with you sir. I am building mine and my welding sucks. Although getting the heck of it.
Yes nothing like a big welding project for learning how to weld
Awesome work Andy ! This was a learning experience for us all !! Great filming , you do know your trade !
Many thanks!
It’s good to know how to make sharp cutters, next best is knowing the guy who knows 😂
Good one!
Another excellent video! Enjoyable, and I learned.. I wondered how these got sharpened.. thanks for sharing
We appreciate your comment! Cheers!
Your grouping from the standing unsupported position is excellent
Many thanks!
This reminds me of when I was a kid working with my granddad THANKYOU so much
Glad you enjoyed. Thanks for watching!
good thing you share when things goes wrong, because there's quite a bit to be learned from recovering from those. I have a small lathe and have had the same (weakness on low rpm) problem. I could not finish the thread at all, no matter how small of a cut I was trying.
Thanks for the comment. Thanks for watching!
awesome work 👍
Thank you! Cheers!
Question: What SFM do you think you were using? I just ground some carbide endmills yesterday on my HARIG @ 3450 RPM. I never considered checking the wheel diameter to see how much I lost......
I believe I was around 550 surface feet per minute. Thanks for watching!
Nice job!
Many thanks!
Thanks! Cheers!
Nicely done.. I was wondering what the random clunk was as you were grinding, then I saw the chunk missing from the diamond wheel. :) Really enjoying your T&C grinder videos! Thanks for taking the time to share this with us..
Yes I accidentally ran into it with one of my fixtures one time and blew a chunk out of it,,,oops Thanks for watching!
Yummmmmmmmm................................I'll do a copy, sort of. Davo from Australia Luv to you both
Hope you enjoy
Nice Job! Get a 5" CBN Cup Wheel at about 150 Grit and it would last a lomg time.
Thanks for the comment and the tip!
I’d be interested to see data related to thread/fastener strength with and without relief grooves. The older, more skilled folks I’ve worked with have preferred no relief but imo it’s asking for trouble-> with cnc it’s a non issue as retract motion in X will always be identical and synchronized, but manually seems to be asking for trouble. Some passes you’ll retract a tad early, some passes a tad late. Those irregular loads on what are usually the more delicate tools (smallest tnr) just seem to tempt fate for a broken tool on a penultimate finish pass. Case in point @28:45, albeit with extenuating circumstances. Question: on I.D. threads do you go no relief? Ive never seen anyone not cut a relief on a bore thread, but there’s a first time for everything. Incidentally, as others have suggested, inside out threading, from headstock to tailstock, run at much faster rpm means higher surface speed which means lower loads, as higher surface speeds have a greater plasticising effect on workpiece material, and carbide is not as tough as HSS, so more likely to fracture at low rpm / bottom of machine useability envelope conditions which is when things tend to go sideways, at least for me. Consider giving it a shot and trying the reverse method and see if an old dog can learn a new trick, you might like the results.
Thanks for the well thought out comment You could go with no relief on an internal thread but you would have to be very careful to not crash the back side of your boring bar into the threads on the far side as you're pulling out of the cut. assuming there's plenty of room back there it wouldn't be any more difficult than threading with no relief on the OD. There's a few things I don't like about threading from left to right. First off if everything else remains the same and you're threading from left to right then you're cutting a left hand thread. To cut a right hand thread from left to right you would have to run the lathe in reverse with the threading tool upside down. While this is possible it would make inspecting the condition of the threading tool very difficult. The compound rest, cross slide and carriage are all designed to work with a downwards load on them. They will work with a upwards load on them but they won't be as happy. Here's the single biggest reason I wouldn't try threading left to right. When I'm pulling out at the end of a pass (quite close to the chuck) It doesn't matter how much I crank it out or what setting I end up at as long as I bring it out far enough. In the case of 8tpi .094" is enough. To come swooping in a the beginning of the cut and landing at an exact graduation on my cross feed handwheel, I think would be impossible. Also, consider that I was threading at 80 RPM. My whole pull out happens within approximately 1/4 of a revolution so 60seconds/80 revolutions/4 1/4 of a revolution = .187 so I would only have .187 of a second to advance my tool inward and land on a exact graduation. I am confident that I could not do that. The reason it works for me going the other way is I am simply cranking it out as fast as I can when I get to the zero on my dial and it makes no difference what graduation I end up on. This normally works pretty well for me. Lastly there would be no forgiveness in the engaging of the split nut. In a fraction of a second you would have to engage your split nut and set your depth of cut. Again impossible at least for me. Threading right to left you can start as far away as you like, Your depth of cut can be set in advance of engaging the split nut and you have plenty of time to get your wits about you before the actual cutting begins. Hope this helps Cheers!
You sure know what you are doing, but that machine doesn't want to do what it should be doing. Perhaps with that machine you need to thread from left to right at those settings, or take lighter cuts.. Thanks for sharing, I enjoy your videos, and I learn!
Thanks for commenting!
From an absolute nobody, I've never touched a machine my whole life, and it's probably hundreds of reasons to not do it or even not possible. But is it not possible to have the threading ending outside the stock? What I mean is, start the threading on the tricky part where you "swoop out" and let the thread end in empty air outside the stock. That would remove most of the muscle memory magic. I also guess this means flipping the insert upside down and running in reverse. Maybe that is a reason to not do it that way? "Swooping in" at a known zero mark might not be a thing.. I'm just thinking out loud at this point. Thanks for the great video!👍🏼 Sorry in advance!
Not a thing but I appreciate your comment. Thanks for watching!
No thread relief, sure not a thing, but cut a relief, add a radius, and get to it, shouldn’t be a problem. Thinking about it for a couple more seconds, the acceleration rate required to start in the relief groove may overwhelm the clutch. Alternatively you could do what most mags have done and swap out the excessive clutch with a shear pin arrangement. The clutch *seems* like a good idea but it’s probably better suited for the feed shaft, not the lead screw.
Actually ... it IS a thing, tool inverted and reversed spindle... I've done it myself... 👏😏
Right you are, I've done it myself but not 1/4" from the chuck and I was also able to set my depth of cut before engaging my split nut when I did it. I fail to see how I could engage the split nut and advance to tool to it's cutting depth all in 1/4 revolution. Under the circumstances in my example I would argue it's not a thing
I agree. I think I will disable the clutch for threading and re-enable it for turning.
I think that machine is not heavy enough to cut an 8 thread.
Modified infeed perhaps. Straight infeed taps out machines earliest, then a 29°/30°, then modified infeed, also known as alternating infeed. As in setting compound to 0° and using alternating passes of compound at 0.000”, then say +/-.005” to widen the thread, then reset compound back to 0.000”, infeed cross slide, etc until wires or thread mic reads ok. Surface finish might leave something to be desired though.
That's new one for me. Kinda stuck in my ways but thanks for the comment and thanks for watching.
Haven't heard of that before. I'm kinda set in my ways but thanks for watching and commenting
There may be an error when using a Papago translator. First of all, thank you for the good information. I'm a 29-year-old man who marches end mill and drill in Korea. Since I'm a beginner, I think there is a formula for calculating the tip angle according to RPM, but I even watched an overseas video while looking for it. It's a question that has nothing to do with the video, but after re-marinating the drill, the lifespan of the drill has been reduced. In this case, should the tip angle be reduced or raised? Is there a formula?
Thank you for the comment. I'm not 100% sure I understand your question but I will attempt to answer. Drill bits normally have a cutting angle of 118 or 135 degrees and the angle should be maintained regardless of how many times its been sharpened. I am not aware of any correlation between RPM and tip angle. Tap lead in angles are usually described as taper, plug and bottoming. The angle does not need to be changed as the tap is sharpened over and over again. Hope this answers your question.
@@Lappemountainliving Thank you for your answer. If you don't mind, could you also upload the video of the entire process of the end mill, the end gash of drill re-grinding, the end rellef angle, and the end secondary angle. I would like to learn.
You are very welcome. Please check out my tool and cutter grinding playlist. There are a couple of videos in there about end mill sharpening
Great info again, thanks! Newbie question, what’s your preferred method for getting the center height. My TOS tool and cutter grinder has a wheel head that can be raised and lowered so not a fixed height so I’m not sure a center height gauge is the right tool for the job in my case.. Any thoughts? Thanks from Scotland!
Thanks for the comment! My go to for finding center (or any other height) is a dial height gauge. Say you want to match the height of a fixture you can measure a diameter on your fixture that is concentric to the axis with say a caliper. zero your height gauge on your table. then touch your height gauge off on the top of the diameter you measured. Subtract 1/2 the diameter and there's your center. Record that measurement and then adjust your spindle height using your caliper and height gauge as you see fit. Hope this helps Cheers!
@@LappemountainlivingGreat stuff, thanks very much, that makes so much sense. Better get me a dial height gauge!
A class machine and a very skilled user. Great video.
Many thanks!
I just got this exact same machine a couple days ago. I am new to welding and I'm fortunate to get a machine this nice for my first - but so far I am really loving it. I have only mig welded with it so far and welds look better than I would have expected. Glad I went with this unit.
Very cool!
Harbor freight sells the exact same set for $80US. I love them and beat the heck out of them. I’d probably sharpen them if I had the sweet grinder you have, though! Thanks for the informative videos! Keep them coming!
Thanks for watching!
Nice, I need one!!!
Yes you do. Everyone does
Master, thank you for your work. Wish You talk a lot, save the listener's time and money. The Internet is a luxury for many
You are very welcome
Christmas in July! Merry Chirstmas, man!
Thanks!
congrats!
Thanks!
Love your sharpening videos, thanks so much.
Much appreciated! Thanks for watching!
Nothin but NICE!
Kind words. Thank you! And thanks for watching!
Thank you so much for taking the time to explain how to use a cutter grinder as very few do I am learning so much your knowledge is amazing Thank you rgds nick
We appreciate your kind words! Thanks for watching! Lots more grinding and machining to come.
Good morning I really like your content. I have a Cincinnati number two cutter grinder with a lot of attachments. I was wondering if you could go through your attachments and show each one how they work that would Great thank you and I enjoy your content very much. I’ve learned a lot already.
Good day to you sir. Thank you for the kind words! If you look back through our videos you will find we have already done vids on a number of different attachments/fixtures. I will make up a playlist that features T&C grinding exclusively so keep an eye out for it. More to come. Cheers!