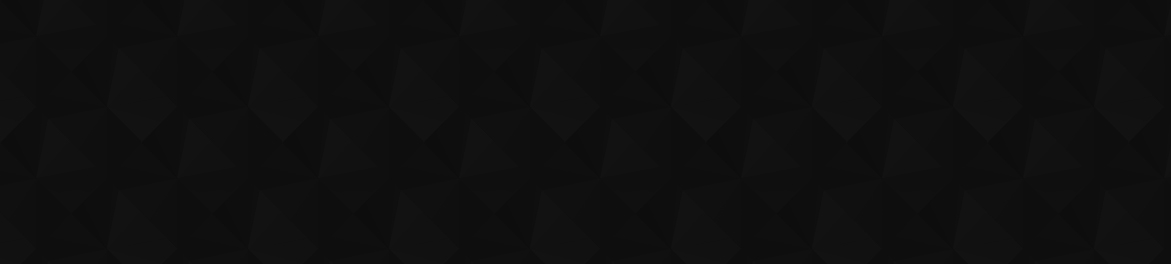
- 36
- 576 115
Alan Reiner
United States
Registrace 18. 09. 2013
Obsessive adventures in AI, engineering, 3D printing, and more!
Creality Falcon 2 Pro - FULL REVIEW (22W laser cutter & engraver)
This is a really solid laser cutting machine for just over $1,000, but also has its fair share of issues. In this video I go over all the good, the bad, and the ugly of it. I also share a design I made to fix one of its biggest flaws.
CORRECTION: I said in the video that camera calibration was pretty bad. I have since redone calibration with a properly aligned honeycomb bed on top of the slats, and kept the calibration pattern within the 400x400 square (instead of to the edge of the machine). The calibration is nearly perfect now!
I reviewed the 22W version, but you can also get a 40W + 1.6W version, and pre-orders are open now for a 60W + 1.6W version.
* store.creality.com/products/falcon2-pro-enclosed-laser-engraver-cutter?aid=zbkol01
Use discount code: FNPALL10
* Creality Honeycomb Bed: store.creality.com/products/honeycomb-workbench-for-laser-engraver-500mm-500mm
* Link to my printable/cuttable slat stabilizers: www.printables.com/model/872184-falcon2-pro-slat-stabilizers-printable-or-laser-cu
==TIMELINE==
00:00 Intro
00:51 Creality & Device Overview
03:58 Unboxing & Build
06:10 Product Tour
07:36 Camera & Lens Calibration
10:12 Cutting & Engraving Showcase
19:31 Final Thoughts
CORRECTION: I said in the video that camera calibration was pretty bad. I have since redone calibration with a properly aligned honeycomb bed on top of the slats, and kept the calibration pattern within the 400x400 square (instead of to the edge of the machine). The calibration is nearly perfect now!
I reviewed the 22W version, but you can also get a 40W + 1.6W version, and pre-orders are open now for a 60W + 1.6W version.
* store.creality.com/products/falcon2-pro-enclosed-laser-engraver-cutter?aid=zbkol01
Use discount code: FNPALL10
* Creality Honeycomb Bed: store.creality.com/products/honeycomb-workbench-for-laser-engraver-500mm-500mm
* Link to my printable/cuttable slat stabilizers: www.printables.com/model/872184-falcon2-pro-slat-stabilizers-printable-or-laser-cu
==TIMELINE==
00:00 Intro
00:51 Creality & Device Overview
03:58 Unboxing & Build
06:10 Product Tour
07:36 Camera & Lens Calibration
10:12 Cutting & Engraving Showcase
19:31 Final Thoughts
zhlédnutí: 1 658
Video
Boss-level upgrades to my CNC machine #mpcnc #hackaday
zhlédnutí 12KPřed 3 měsíci
This video made it onto hackaday! hackaday.com/2024/05/07/mostly-printed-cnc-gets-a-few-upgrades/ The MPCNC is a cool DIY CNC router. But I wanted to use it for more than it was designed for cutting aluminum. Weeks of design and assembly made that dream a reality. See how I did it and enjoy the twists and turns of improv CNC engineering! The original build was about $600 including all the elect...
CNC Transformation Timelapse #mpcnc
zhlédnutí 5KPřed 3 měsíci
Turned my $600 MPCNC into an aluminum-cutting beast with about $500 in upgrades! Full enclosure, HGR15 linear rails, T-track for workholding, cable chains, anti-backlash Z drive, and a Raspberry Pi for CNC.js. * If you're new here, watch the first video showing how I built the original machine for $600: czcams.com/video/VFPeR6i1BvE/video.html * I will publish a discussion video about this build...
3D Scanner Review - CR-Scan Ferret Pro!
zhlédnutí 20KPřed 7 měsíci
The CR-Scan Ferret Pro from Creality (maker of the Ender line of 3D printers) is one of the most affordable 3D scanners to hit the market, and I'm going to walk you through a few projects I did with it including an angle grinder chop saw mount and a really creepy hedgehog! Until Dec 28th, 2023, you can get it for 10% off from the Creality Store store.creality.com/products/cr-scan-ferret-pro-3d-...
I (Mostly) Printed a CNC Machine! #mpcnc #diy
zhlédnutí 12KPřed 7 měsíci
The "Mostly-Printed CNC" machine (MPCNC Primo Edition), is a budget, DIY CNC router, made from 2kg of 3D printed parts and 20 ft of steel tubing/conduit. Initial cost was about $600. Will be spending more on dust collection, cable guides, enclosure, etc. I have NO AFFILIATION with the MPCNC project or V1 Engineering, I was simply intrigued by the strange design and was pleasantly surprised by t...
BREAKING Every Filament | PLA, ABS, PETG, PLA+ and More! #3dprinting #engineering
zhlédnutí 1,8KPřed 11 měsíci
The Ultimate Engineering Filament Series is here to teach you about ALL the different materials available for consumer 3D printers. This video covers the basic filaments, PLA variants, PCTG and ASA. Future videos will cover Nylons, Carbon- and Glass-Fiber filaments, and resin-printed materials. TIMELINE 00:00 Intro 01:01 Backstory 02:21 Flexure Test (PLA & PP) 04:27 Impact Test (PLA & PP) 08:34...
Building a Cyborg Sloth w/ a Folding Electronics Box
zhlédnutí 1,5KPřed rokem
Sloxel is going to be a battery-powered, AI-enabled front-door greeter for our house. See how I did the the 3D design and electronics to make him look beautiful and mobile. Link to the original sloth face: www.thingiverse.com/thing:4553824/files
Most Annoying Computer to Fix
zhlédnutí 1,4KPřed rokem
Electronic wall art is hard to maintain. Have pity on me. NOTE: After discussions in the comments, it is apparent that it is almost never safe to open a power supply unit (PSU). There are high-energy capacitors that can maintain deadly (dis)charge even after the unit has been unplugged for a long time. I was actually aware of this and have a tool called a "capacitor discharge tool" for this pur...
Ultimate DIY 3D Printer Experience // RatRig V-Core-3.1
zhlédnutí 41KPřed rokem
Ultimate DIY 3D Printer Experience // RatRig V-Core-3.1
3D Printing a Giant Indestructible Trashcan #3dprinting #tpu #ratrig
zhlédnutí 3,5KPřed rokem
3D Printing a Giant Indestructible Trashcan #3dprinting #tpu #ratrig
DIY 3D Printer Build Experience (III) // Joys of Wiring // RatRig V-Core-3
zhlédnutí 15KPřed rokem
DIY 3D Printer Build Experience (III) // Joys of Wiring // RatRig V-Core-3
DIY 3D Printer Build Experience (II) // Mechanics & EVA Printhead // RatRig V-Core-3
zhlédnutí 10KPřed rokem
DIY 3D Printer Build Experience (II) // Mechanics & EVA Printhead // RatRig V-Core-3
RatRig V-Core-3: Printheads, Fasteners and the Amazing EVA
zhlédnutí 11KPřed rokem
RatRig V-Core-3: Printheads, Fasteners and the Amazing EVA
I made it to the 10-minute benchy club! (#speedboatrace)
zhlédnutí 4,6KPřed rokem
I made it to the 10-minute benchy club! (#speedboatrace)
This AI Face Knows Your Halloween Costume
zhlédnutí 742Před rokem
This AI Face Knows Your Halloween Costume
Exotic flexible filaments for 3d printing (Flexibles Pt 2)
zhlédnutí 3,5KPřed rokem
Exotic flexible filaments for 3d printing (Flexibles Pt 2)
DIY 3D Printer Build Experience (I) // Mechanical Assembly // RatRig V-Core-3
zhlédnutí 9KPřed rokem
DIY 3D Printer Build Experience (I) // Mechanical Assembly // RatRig V-Core-3
Ever wonder what goes into a DIY 3D Printer? // RatRig V-core-3 (Part 0)
zhlédnutí 8KPřed rokem
Ever wonder what goes into a DIY 3D Printer? // RatRig V-core-3 (Part 0)
FEEL these flexible filaments through the internet (3D printing TPU edition)
zhlédnutí 16KPřed rokem
FEEL these flexible filaments through the internet (3D printing TPU edition)
Fascinating 3D Printing Design Technique (#ziptiecity)
zhlédnutí 108KPřed 2 lety
Fascinating 3D Printing Design Technique (#ziptiecity)
Washing 3D-Printed Goats for Fun and Education!
zhlédnutí 807Před 2 lety
Washing 3D-Printed Goats for Fun and Education!
Well i'm hooked so much so i went a bought one to play with. Hoping it will help me with designing parts for my trikes i have, it's the little touches that make it worth while. Very impressed with the turntable setup would be interested in it for a couple of smaller pieces i need to do. You said you designed it do you sell the files or can i get them from somewhere. I have a very old turn table like 10 yrs i think but doesn't work properly anymore. any help would be great like i said love your work. .
Great 👍
Thanks for sharing this.
Excellent video concept, more show... and less numbers. In terms of making a cell phone case, what's your final recommendation? My "drops" are usually from about waist height?
I watched to the wireless in use. I do like the video but I need to see how it works with a phone.
what is polypropylene ?
i also fixed the z leadscrew backlash problem with the mpcnc but i approached it differently. i bought a second brass nut , flipped it upside down from the original, spun it backwards till the holes lined up and used longer screws to take out the backlash. same as your method but like a spring pushing the nuts together instead of apart.
Quick Correction: I said in the video that camera calibration was pretty bad. I have since redone calibration with a properly aligned honeycomb bed on top of the slats, and kept the calibration pattern within the 400x400 square (instead of to the edge of the machine which is way bigger). The calibration is nearly perfect now!
What are your opinions. Ratrig vs Voron ?
It's a great job, but let's not forget how we got here - the community behind MPCNC is amazing, and going off on a few imperfections isn't the look. I don't know if I would lean into CNC.js that might, as they have essentially abandoned the project.
They should not archive old versions, many people still use 1 and 1.5 the files should be Always available somewhere. Is a very good project.
hey, are you still using this thing? how is software? better/worse/same? How do you compare this to iPhone
10:50 i stretched that hole
There are screws that drop through the lead scream nut into the top of the core so that the lead screw isnt just free spinning. Did you use longer ones that drop through the entire double lead screw setup? Please advise
Almost! You do need longer screws to get through the bottom printed fixture half and lead screw nut, instead of just through the nut. And you separately need screws to fix the top nut to the top fixture half. Then 4 more to hold them together after tightening. So yeah, it's a lot of M3 screws for this thing...
@@ObsessiveEngineering thanks!
Do you have plans or a link for the cutoff wheel? Is that 3d printed? TIA
Thanks Alan! I cant wait to give TPU a go!
abominedgehog 🤣
Freaking Boss level 💯
Amazing vid 🎉 Delrin benchy is boss 😮 you Jammed your PP in the extruder and it was soooooo long lol How did it fit in here 😅
Hah! Of all the filming I've done for videos on this channel, that clip is probably my favorite. I captured my genuine astonishment at just how badly Polypropylene can jam your extruder! Thanks for watching!
@@ObsessiveEngineering same here that was incredible. The extruder basically respooled the filament lol
Hi, I recently bought a Lenovo Yoga Book 9i with dual screens, and since there isn't a case available for it, I'd like to design a unique case. Before diving into an ambitious design, I want to start with a simple protective case. I need some advice on measuring the dimensions of my laptop accurately. I tried scanning an image of the laptop, then cropping and resizing the image to convert it from PNG to OBJ, but it didn't go as planned. What is the best way to measure my laptop for this purpose? Additionally, I am planning to 3D print the case using SainSmart TPU 95A. Can you provide guidance on how to proceed with the measurements and 3D printing?
Hello,it s a voronkiller ?
Thanks. Nice job. And thanks for the stabilizers too. I'm cutting them now. Maybe you are the guy that could come up with a push style clamp for the warped boards???
This is one of the greatest reviews I've seen. Thank you! Also I'll appreciate if you could give me a couple of recommendations for mesh mixer tutorials or channels to follow. Thanks again
I think that chemical adhesion has its limits for parts sticking to beds and can be annoyingly temperamental. I'm surprised that more mechanical solutions haven't been explored -- ie. special base layer that can be clipped, or fastened to a surface for a perfect, heat-free "adhesion" to the build plate.
Like you said -Ditch those slats and use a honeycomb bed. The blade slats were a “cool” idea but in reality the honeycomb provides the much needed stability. I’m still dialing in my settings for deep relief 3D greyscale engravings and almost there :) I’m still very happy and impressed with the Falcon 2 Pro and its capabilities. Cheers
its actually the most impressive of all the filaments i had no idea it was this flexible and strong
Marking spray has silica in it. You are basically putting a ceramic coating in when it heats it. The stuff is permanent and lasts travel to space. NASA uses it. If you can rub it off or remove it chemically you didn't get it hot enough. I've worked with cermark a lot it's great when used right. Just dial in the settings. Tempra paint and glass let's you do engraving in clear glass. I made a video on it a few years back. These machines are coming along but I'm still convinced co2 is the only way to go. Thanks for a great review.
Good to know! I rubbed it pretty hard and you can see that there was still quite a bit of unaltered squares left in the lower right corner where the most laser energy went into the markings. I assumed that it would come off eventually too, but maybe not. I will add this knowledge to my toolbox: cermark + aluminum + diode can work! I haven't spent that much time with lasers, most of my time has been 3D printing and CNC machining. If I were to get another one, I would definitely want to go CO2 so I can do acrylics. But for the price, I can live with the limitations of this machine, and the diode laser still achieves plenty of accuracy and reliability on things it does cut/engrave. Thanks for watching!
@@ObsessiveEngineering Yeah, for the price really can't beat it. Few issues but as you pointed out easy to get around.
You can’t measure a 3d print to see the accuracy of a 3d scanner. 3d printing has around 0.2mm tolerance and the material will shrink depending on the geometry too.
You're right that there is additional error introduced by the printing process, on top of model error. It's possible that the error in the model was actually slightly more or slightly less than what I measured. However, I have calibrated that printer pretty rigorously, and I know it prints approx within 0.1-0.2mm of what I design. Even at max printing error, I think that the results I measured are still very favorable for this budget 3d scanner. I also know to scale up to 100.5% when printing with ABS, but I generally don't need model scaling with PLA or PETG. So, you're not wrong, I'm just on top of that, because I built that printer myself and gone to great lengths to figure out it's tolerances. Thanks for watching!
@@ObsessiveEngineering you can use tools like cloud compare to measure a distance on a cloud point.
I mean, I bought a 40w K40 for $400. And it can cut/engrave far better than this thing. I spent another $300 putting it into a frame that ended up giving me a 16"x12" volume to work with, and I'm still cheaper and more capable than this.
Unfortunately, I don't have a ton of experience with consumer laser engravers, so I may not be the best person to debate this with you. I will say I'm surprised to see so many inexpensive 40W CO2 lasers out there. But it sounds like you ultimately ended up with a DIY laser machine build, which of course is going to lean cheaper. The Falcon2 required some assembly, but it's a complete machine. I wouldn't call it a DIY machine. It looks like the key differences are (at least compared to the OMTECH k40-based machine): * Falcon2's 22W can cut up to 10mm wood (20mm for 40W). K40 claims only 3mm cutting depth (probably really short depth of focus). I'm not 100% on this point thought * Integrated overhead camera in the Falcon2. * You say you put your laser into a frame, does it include the eye-safe panels? Is it "really" safe & sealed? Is it "really" enclosed so it's easy to vent? * There's a lot of safety features on the Falcon2 Pro -- particularly the door sensor that turns off the laser and pauses it when opened. Also, the e-stop button on the front, and the fire and lens obstruction detection directly on the laser module. * The volume on the Falcon2 is a bit more generous. I'm not trying to bash your system by any means, just pointing out that I believe there is an actual value proposition behind the Falcon2, as a mid-range laser option. You might be right to argue that it's still too expensive, but I'd argue it's not excessively overpriced. I also see plenty of CO2-based machines that cost way more.
top class video, much appreciated. Building a CNC myself right now but I am using the approach which u see in onefinity. I use 4 pcs 1100 mm 40 mm solid rod linear rods for Y axis and 1700 mm of the same for the gantry. Not sure about the Z axis at the moment but it's pretty straightforward. I'll add a laser as well and possibly some other attachments but not sure. It will run on rootCNC, a grbl based solution and the motors for all all axes with encoders, to make it more reliable I hope. The movement is done with 2 x 16/10 ballscrews on Y and 1 x 16/10 on the X axis. The base and gantry will prob be printed for the beginnig or made of some plywood but when I'm confident it works it will be replaced with solid steel and/or some epoxygranite cast parts. We'll see. Have some fun time on that beast you built man!
Any update?
Printing gears in TPU is an INCREDIBLE idea. Well done. In fact, the flexibility may outlive ridged gears in environments where sand and dust can work themselves into the mechanism: it may be possible to leave them exposed (provided no fingers or large objects can reach), reducing the need for enclosure. And modifying thickness may be an effective strategy at increasing load capacity. Cleverly integrated capillaries may even make these self oiling as well! Silent, durable, and flexible (eg. sand/dust pass through teeth).
What is that alternative lead screw coupler you switched to?
I believe it's called a "flexible jaw coupling". Here's one listing on Amazon amzn.to/3UZYM9H
definitely not enough credits for the science you're doing there. I'm looking forward to build my mpcnc and will include your upgrades for sure!
Did you end up adding the second extruder ? How did that work out, second extruder for soluble material support definitely worth adding.
I never did. This printer ended up being my workhorse, and I never wanted to put it out of commission long enough to try that. It also was kind of an experimental upgrade in the community. At this point, if I'll probably just build a V-core-4 which has a native IDEX option. I plan to use it primarily for support materials, but also for duplicating/mirroring to print multiple parts at once.
Nice upgrades! What Kobalt router model are you using? Reason why I ask is because I have a Kobalt router and was hoping to commandeer it for my build, but always thought it was too heavy. Would be cool to know if it’s the same as yours.
I bought this one directly from Lowes. Read the linked article, apparently designed in coordination with the MPCNC guy. Only $100, and I'm m extremely happy with it so far. I've probably done 50 hrs with it. www.v1e.com/blogs/news/kobalt-router-featuring-the-lr3
This is an incredible video that makes everything so clear to understand.
$600 for THAT? You have to be kidding!
Nice! Great job.
Nice. 🙂
do you lose any z-height with the 3d printed backlash thing? do you need a different size leadscrew?
At first I thought I would lose some Z-height but because of the geometry of the machine, the core never has a reason to travel low enough to interfere with it. So it turned out to be a compromise-free upgrade. It's just two TR8 leadscrew nuts instead of one. So nothing changes about the lead screw, though I did switch to a new one (of the same size), simply because i assumed the old one was worn down based on that original backlash. Thanks for watching!
thanks for the details. I’ll give it a try a soon as i have some abs that matches my mpcnc color. did you ever get any feedback from the mpcnc team on this mod? this whole backlash thing seems intentional or an oversight?
Nice breakdown of TPU. Have you tried TPR? Its made for the atomstack cambrian, a rubber filament. Its flexible like TPU but grippy like rubber. I wanted to get one here localy as my first 3d printer and sort of regret it because it came with like 6 rolls of the TRP filament which is expensive, but there wasnt any satisfying reviews on it so i passed it up. I wish we could get a real review on it. You should reach out to atomstack maybe they'll send you one.
Don't run your 5v off of boosted 12v... Each buck/boost you go through requires some heat dissipation. Heat dissipation is stored electricity being thrown away as waste. Run the 5v buck off of your main power bus. What you designed here will work, especially if your loads are low. BUT if you want the most power from your battery, the last thing you want to do is over-process your power. And depebding on your BCM, it might be better for both the 5v and 12v boards connect directly to the battery and not go through the bcm. That depends on if you are going to use more power while on line power, or battery power. Generally speaking, boost is less efficient than buck, but neither are 100%. Efficiency is the inverse measure of how much power you loose to heat, and each loss is added to the other losses. In your battery circuits, if something is getting hot, you are throwing power away. Don't throw power away. If each circuit looses 10%, then going through 3 means almost a third of your power will never make it to the thing you are powering. Batteries lose a third of their capacity, not what you want for batteries already in a used state. And if a power device says 97% efficient, that is usually a weighted lie, it will be 97% in a very specific range of voltages and currents, it can drop to 10% efficiency if you are too far outside of the "sweet spot" it was designed for, thus throwing away 90% of your battery power. And put in some filter caps, as those buck/boost devices produce high frequency artifacts. And they can burn each other up if one units artifacts are destructive to the other device. You need some high frequency caps to absorb some of the noise, and some large high-value caps to store energy. Caps take up a lot of space, the maker of the buck/boost is not going to do it for you because they want small cheap boards. Also keep in mind that each board has a limit to how much power it can handle, so a board moving power for another board is also wasting capacity. AND a buck/boost board is turning on and off at a high frequency to do the power conversion. So if you measure a board at a half amp, what it might actually be doing is switching from 0 amps to 25 amps over and over in a way to average .5 amps. Your volt meter may not see the 25amp spikes, but the upstream electronics WILL if you don't put the right filter capacitors in place. If you want to see the 25 amp spikes, you much learn to measure power with an oscilloscope. I got my oscilloscope training when I was 3, explaining how I could handle 120v mains connections when I was 6. Most people don't get to play with oscilloscopes, but seeing the signals has a lot to do with how much you learn from the doing. II learned to build power supplied when I was 6, in 1968. We didn't have buck/boost boards we could buy inexpensively, back then... but now that I have 56 years experience, inefficient designs kind of jump out at me... While I was critical, my goal is to be helpful.
Thank you for the electronics lesson (seriously). At the time I made this video, my electronics skills were still pretty elementary, enough to hack this kind of stuff together, in a way that superficially works. Since then, I have created many systems, particularly ones using motor drivers and other voltage regulators, usually using a small and a large capacitor for that high- and low-freq filtering as you mentioned. As for chaining them together, the reason I didn't want to run the 5V directly off the battery was that typically they recommend having 2-3V headroom for the buck'ing. Since the battery runs with a nominal 7.4V, and could drop to 6V at the lower charge levels, I thought it might not be "safe" to run 5V directly from it. Having 12V starting point for the 5V buck would be safer--in theory. But as you've pointed out, there are potential issues with this, which I liken to the way the light dimmer switches interact poorly with LED lights. I avoided that fate here, but I imagine other combinations of voltages, or maybe even brands of regulators might not work out.
its so cool
Where is all my GRBL 5x users at 😂
You should go back and edit any corrections into your videos with a text comment overlay as most good utubbers do.
If you were to do this over today, would you wait for V-Core 4.0?
Based on what I've seen of the V-Core-4 -- absolutely. It looks like it's an improvement all around. Build complexity, kit completeness (incl electronics), a lot more metal components, beacon probe, and has the IDEX (dual-extruders) as a primary build option. I decided if I ever get another printer, it has to be IDEX. I would love to build a V-Core-4 myself, but recently added a CNC router and laser cutter/engraver to our mess here. Wife approval is unlikely unless I promise to get rid of 2 other machines...
@@ObsessiveEngineering Thanks, I'm on the list. I was considering a tool changer rather than IDEX on the off-chance I'd need two materials plus support. What do you think? Do you use an inductive probe (Beacon)? If so, how does it work? I've heard inductive probes have repeatability issues at temp.
@@leroycasterline1122 Re: IDEX vs tool-changer -- Toolchangers come with a whole class of extra complexities. I'm going to guess that's why we don't see many printers using it. IDEX isn't trivial either, but at least for the RR, it appears to be a first-class feature now. I also doubt I would personally use 2 materials + support, but that's just me. If you think you might you could consider ROME, which is a side project in the RR community by Helge Keck, for using two filaments per extruder with an extra motor and Y-shaped feed port. I don't know how mature it is, but it's an option. Re Probe: I switched from SuperPINDA to the Euclid dockable probe, because I try a lot of different build surfaces and I needed something that measures the physical top, not the metallic substrate some mm below it. I've had some issues with it but it generally works. I feel like I had some minor issues with the SuperPINDA at temp, but it's been so long I can't say for sure. Beacon is a different beast though, I'm not sure if you can extrapolate to that. Obvs I'm not the person to ask though :)
@@ObsessiveEngineering Thank you for your expertise! I've filled out the rez form for a V-Core 4 500. I ordered an Octopus Max EZ, I hope I shouldn't have asked you first!
@@ObsessiveEngineering Well, 3 materials isn't something I'd use often. I suppose if I bought the IDEX kit when it's available, I'd be able to repurpose the 2nd tool. I'm not interested in a toolchanger if I'd have to remove it for high quality prints! Perhaps if I find I *need* one, a Prusa XL would be in order?
I didn’t think you could scan reflective objects?
Yeah they claim that you can with this scanner. I don't think I really settled the question in my testing, but it did achieve some level of tracking on that metal 123 block.
bro, where's part 2?
I got distracted with other content. But part 2 is like 70% done, and I have all the footage and data already collected for all 4 parts. I'll get there... eventually. Thanks for watching!
The blobing and stringing at 11:03 is not because of moisture. It is because of retraction settings.
Maybe! I've printed a LOT of TPU over the years and by far the most significant factor is moisture. After this video, I realized I was using PLA settings which may not be aggressive enough to get it dry. I have seen mixed guidance on retraction settings-- most say to disable retraction, and I usually turn retraction off and print slow, but even when I leave it on by accident it usually turns out okay. If it looks like this, it will look 90% better after drying it properly (55C for 6-8 hrs). I didn't think retraction settings are a settled matter, but TPU's moisture absorption is.