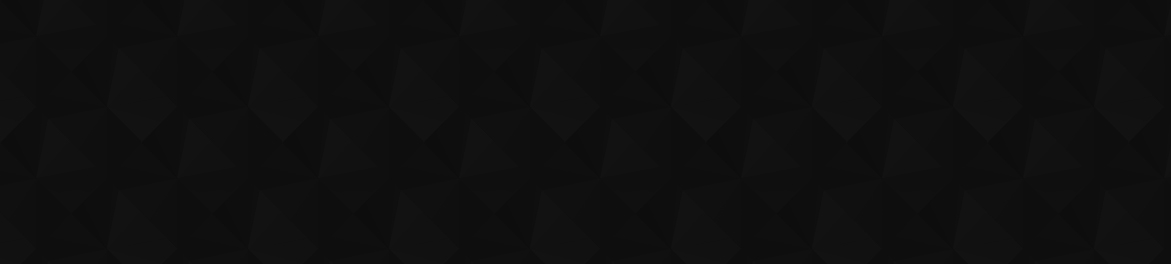
- 8
- 185 115
Caspar Baczynski
Registrace 1. 05. 2013
Hydrophobic Water Maze - just add water to play
Etsy: www.etsy.com/ca/TheSmallestWorkshop/listing/639874737/
zhlédnutí: 952
Video
Custom clear guitar pick box with spring loaded/return lid
zhlédnutí 474Před 6 lety
Not a how-to but demonstration only. A clear case to show-off/display your custom/specialty picks. Comfortably holds six 1.2mm 'heavy' picks. Lid: 1/4" nominal cast acrylic Rod: 0.253" OD extruded acrylic Base: 1/2" nominal cast acrylic Pocket/cavity depth: 0.31" Retaining ring: 0.063" thick brass washer over-sized to 0.250" Compression spring: zinc music wire 6.9lb/in (0.16" preload 0.1" lid l...
Sixteen leaf mechanical iris box disassembly
zhlédnutí 67KPřed 6 lety
Assembled height: 3-1/4" Assembled diameter: 9-1/2" Opening diameter: 5-3/4" Compartment diameter: 8" Smallest aperture diameter: 3/8" Leaves: 16x 0.008" 304 stainless. 130 degree arc Leaf compartment height: 1/4" Dowels: 16x 1/4" 16x 3/8" birch Gear material: yellowheart wood Top/bottom material: padauk wood
Great Value Cola
zhlédnutí 332Před 10 lety
Song: Weezer - Troublemaker Compilation of 9 group rides spanning the summers of 2013/2014
DIY Semi-automatic Motorcycle Gear Shifter (SV650)
zhlédnutí 62KPřed 10 lety
Automatic Economy: system calculates instantaneous cruising fuel consumption and switches into the most economical gear. Manual: user assigns a custom RPM range within which the system will attempt to maintain. Automatic Aggressive: the system records the engines power band and switches gears to maximize acceleration. This is a graduating year PROOF OF CONCEPT project completed by Patrick Kowal...
Word Clock - overview, recommendations, picture build process
zhlédnutí 53KPřed 10 lety
Incomplete notes on building the new clock: imgur.com/a/Cj8c1 Build process photos: (invalid link removed) - 30x30cm x 3/4" MDF - 5mm glass - 2mil colour 3mil blackout vinyl - 3M Fasara Interior Design Film - black and white paint - white wood trim Electrical components: - DS3231N (real time clock) - PIC18F2525 (microcontroller) - 28 serial to parallel shift registers (STPIC6D595, avoid for rel...
Southwestern Cedar Roofing - August 2013
zhlédnutí 386Před 11 lety
Southwestern Cedar Roofing - August 2013
Cześć. Mam kilka pytań co do twojego urządzenia. Scigam się na 1/4 mili i chcę zainstalować takie urządzenie.
?
I need this 😩
great .. can you please send me code and schematics .. I'm trying to create a word clock.. but your code is awesome .. I don't think I can do that much ..
Any email i can contact?
If you crawl in a traffic in 1st gear, do you still pressing the clutch to keep it from stall?
wow
click photographic
spiiiiiiiiiiiiiiiiiiiiin
What brand is that shift solenoid that bolts to the shifter?
Dobry, pomysł 👍 Czy autor mógłby się odezwać na priv? mam kilka pytań, bo akurat jestem w trakcie tworzenia podobnego rozwiązania, dla osób niepełnosprawnych.
Hello! I wrote you an email. I want you to help me make this watch! Thanks
How do you calculate the shape of the blades?
Bro what actuator is that called can I know
👏💪😉
Nice video, Its a pity the indiegogo campaign did not go through . I am home for the next 6 months due ato a heavy cancer operation/.treatment.i wonder whether you could share the schematics of the electronics. time opr me is tht most precious asset and wanted to spend the time as i am home to build a similar one.
Hi Casper this is great. I need your help because I have a friend that lost his legs and can't ride his motorcycle anymore. I live in Namibia what do I need to make something like this.
Look nice...
Thank you for posting this video. Do you have build instructions ? Open source project link etc ?
are you using a clutch on lh?
Hello Caspar. I just received a package from you water maze. For several reasons I opened, but I don’t think it’s for me. This might be really important for someone, and I want to make sure it gets to the right person. I hope you see this and reply.
¿Por que no se cierra del todo?
Pretty cool are you guys putting these together as kits for other motorcycles ?
Have you perfected this
hi Caspar, I know this is an old video but I really enjoyed watching your build (dismanteling). I really want to give this a try but to be honest there are few thing I don’t understand. Do you have any reference book or any other kind of source that I can read to better understand the iris mechanism? I do understand how the blades move, the dowel forced to move through the gears’ grooves. But I do not understand how the leaves go that far in the center? Was this build totally hand made or did you use a cnc (especially the gear)? Many thanks. cheers
ебать ты молодец
Playing this backwards showed your true strength and agility.
Cześć 😊 mógłbyś mi powiedzieć skąd masz ten siłownik do zmiany biegów? Dzięki 👍 dobra robota 👍
Such an awesome project! Im just wondering how does it unload the transmission when down shifting and no throttle input, like when slowing down? I would expect you can then only down shift by blipping the throttle a little, like down quick shiting. But from what I understand you can only cut power, but not give it some extra power. Or does the actuator just push hard enough to force it in lower gear without unloading the transmission?
Looks great. To me, it's a bit to technical.
Hi Casper, It's brilliant. Would you mind sharing the schematics & the Code? Would appreciate it if you could. Wanna try aking it. Thanks
Nice.
Did you buy or make?
What is the name of solenoid actuator ???
Do you know where you got the actuator?
What are the benefits of this kit? How this works?
Can I get this system ?
You are a goddamn genius
Hey! Best iris project i’ve seen so far. You think it would be possible to make it out of heat resistant materials for use with open flames inside?
Hahahaha I like where my imagination went reading that. Yes, it should be possible. Heat expansion/contraction of joints/parts can be compensated for. Although, if it's important to you and you would like a very tight seal when closed you'll have to get creative (tiny leaks around each overlapping leaf and it's pivot). Keep in mind that the smaller the leaves of your design and the smaller of a space you'd like them to compress/pile in, the more flexible they'll have to be. Each leaf subtly twists when the box is in the closed position.
Thank you for sharing. I've always wondered what the leafs look like.
After going through the process I can affirm there isn't much information out there. Just have to go for it. Took quite a bit of chicken scratch. If there's anything you'd like to know just ask and I'll do my best to answer.
Hey where did you get that actuator from?
still has the project? great video
Thank you! The box was made for and given away as a wedding gift. If I want one now I'll have to make another.
Worth mentioning in regard to some of the comments about people with l/leg mobility problems, that I have been riding without a left leg (above the knee) for 20 years using the Kliktronic unit, which uses an electromagnet actuator controlled by two buttons on the left grip. I'll point out that the actuator on that is on a pivot mount which makes it much less violent than this fixed one.
Appreciate the feedback; thank you. I do quite like Kliktronic's implemention. Certainly worth looking into for others considering.
Hi there Caspar! love this piece you've made, i'm creating a similar iris mechanism however, it will not be a box and i'm using copper for the blades. I have one question though, i am at the final part of assembling the blades within the wooden frame, but am unsure on how to fix the wooden dowel to the copper? can i ask what you used and did the sanding take some time to ensure smoothness of the mechanism? Thanks!
Thank you Tom! Tangent: I had forgotten for a while but seeing your Nottingham footage once again ignites my drone interest (I was eyeing the Mavic Pro before it was available to consumers). Copper or brass were my first choices but ultimately chose stainless for a few key reasons. Copper will patina well and adds good character. If not a box, what is it you plan on making? For the answer to your question I'll refer you to my brief discussion with 'Scott Ismail' below (search the comments for his name).
Hi Caspar, Thanks, I have a fair bit more on my instagram page @tom_flavin the mavic pro is fantastic! I have since made the aperture using copper and used contact adhesive which has worked well! This piece was made to demonstrate a concept, my girlfriend is studying interior architecture and for her final project will be creating a building with a circular. She wanted a roof that would be able to allow different amounts of natural light in. Therefore i built this that she could add to her model to demonstrate the concept. It came out very well! Thanks again for your help, Tom
What tipe of actuator is it.
You'll have to look into my old comments for more details, but it was a 12VDC centre tap (bi-directional / 2-way) solenoid. The [solenoid] coil is tapped at 3 points: both ends (+, +) and the centre (-), thus actuation direction is determined by which of the ends is energized.
How much is the United to pay
Casper - This is just beautiful - I've recently been bitten by the bug to build one of these Iris' and I've been trying to research them as I understand there are different types. In regards to your build, I was curious - how did you attach the dowels to the leaves? My understanding is they can't penetrate the leaves or else that would interrupt the rotation of the Iris, and yours don't appear to go through the leaves. Did you just epoxy them? Also, I have a home made CNC and it looks like you might have a CNC as well - any chance this was made in Vcarve? Thanks and congrats on an awesome build! -Scott
Thank you Scott. It certainly is a bug as it's easy to over-compliate, but personally gratifying in a way I think only the maker/DIY community can relate. The leaf-to-dowel joint is the weakest link of this revision. I actually found dollar store superglue to be stronger than the two epoxies (don't recall their names, some permatex brand and another) I tried (sanded the contact area of the stainless prior), but even so I wouldn't do it again. I'd strongly prefer more of a mechanical bond, even a low [head] profile pin through the bottom (if you drive the head deeper than the surface of the stainless?). Issue is if you don't put stops at the start/end of rotation like I did (the dowel slot lengths) than any excess force by the user is put on the adhesive joint, and even so, given wood movement, something may momentarily bind. Yellowheart likes to split / move / tear-out, Padauk is beautiful but has its own characteristics. I used fusion 360 to model the box: it allowed me to simulate and find a balance between # of leafs / lid height, minimum eyelet/iris diameter, and outer wall thickness / leaf width). The more leafs the thinner your walls can be. I find Adobe Illustrator and Vectric Aspire significantly easier than Fusion 360 for 2D/SVG creation/manipulation, but Fusion360 wins hands down for 3D/CAM. I personally hated the learning curve for modeling in Fusion 360, went back and forth for almost half a year and it still feels unnatural at times, but I'm glad I did because the pros outweight the cons. My workflow sometimes jumps between the three depending what I'm controlling. Mind you I consider myself a trial-n-error hobbyist. On another note, I really do dig your "Ike's Gamble" upload.
Casper - Thanks very much for your detailed response - it was very helpful! It seems like I keep seeing Fusion 360 pop up recently. I will have to check it out. I think your mechanical bond idea makes a lot more sense as I was worried the stresses on such a small contact point would eventually wear out that chemical bond. In any event, I love the build, and I hope to pull off something that looks just half as nice.....and thanks for the compliment on my rifle case - it's definitely one of my favorite projects so far. On to new challenges - like this iris!
What type of touch sensors are you using?
I've seen people use bananas, but I had some thin copper sheet which I ran a wire to from the dedicated IC (see description). Alternatively many microcontrollers today can be purchased with this functionality built in.
Great design, beautifully made
Thank you Paul. Certainly could have made it easier on myself, but where's the fun in that haha
Hi very nice work! One of the best Iv seen definitely. how did you cut the leaves?
Keeping it simple, knowing my tolerances, and given my tools/workspace: 1) print one leaf to scale on a sheet of paper 2) place clear packing tape on either side of the page to reinforce it 3) cut the leaf out 4) trace the paper leaf on the steel stock with a sharpie 5) repeat 16x 6) rough cut each each leaf from the sheet 7) use an oscillating spindle sander to refine the edges. Total time (from recollection): 5 hours. - I used a pair of snips (Stanley 14-556, available at Home Depot) to rough cut the leaves from the 0.008" thick 304 stainless shim stock (from McMaster-Carr). It was a fair forearm workout and I wouldn't do anything thicker than 0.010" with these snips for curved cuts. Having worked quite a bit outside I didn't wear hand protection, but you'll want to with such sharp thin material. - When using the spindle sander quite a bit of heat would build up in the steel as it's a slow subtractive process by abrasion. You'll notice the steel wears the sanding sleeve significantly quicker if you allow the steel edge to heat up and 'discolour'. Between what I had on hand (50, 120, 240 grit) I used 120 grit 3" diameter sanding sleeves (meant for wood, I don't recall their material but it's the standard red sleeves available 'everywhere') and went through 5 sleeves. The finished edge is still quite sharp (cornered) so gently pass every edge over the spindle sander at an angle to round it over. This is certainly not the best way but as is the DIY way. Safety glasses are a must. - I chose 0.008" as it intuitively had the balance between flexibility and rigidity I thought would work. Doing it again I feel 0.006" would be fine but would have to go through some samples if I wanted to go any thinner. An attractive alternative would be copper 'foil' but I chose stainless as I didn't want anyone's hands to have a metal smell after handling it. If you go with copper/brass/other consider applying a clear coat or film of sorts and compensate with increased thickness for any loss in rigidity from these softer metals.