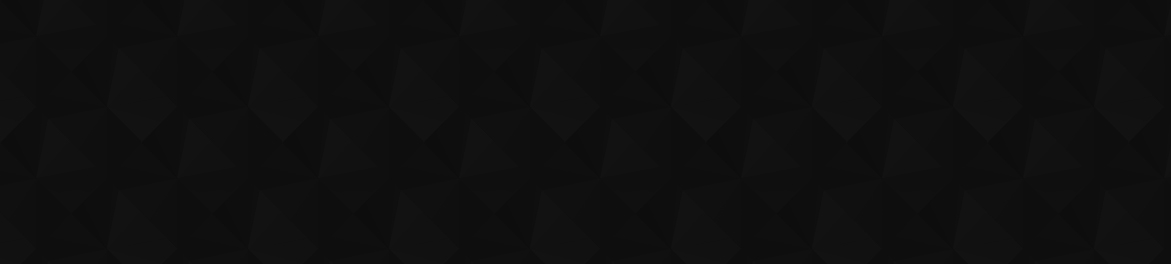
- 232
- 334 339
Tom Mentink
Netherlands
Registrace 10. 01. 2014
This channel is all about continuous improvement in an industrial setting. So you can expect lot's of performance excellence topics, including TPM, Lean and SixSigma tools. What sets it apart from other CI channels is that I really want to give a 'working within industry' spin on it.
There will also be lots of practical stuff for CI specialists to use during your work, like business games, practical implementations of CI tools and some personal productivity ideas that work within most large industrial organisations.
There will also be lots of practical stuff for CI specialists to use during your work, like business games, practical implementations of CI tools and some personal productivity ideas that work within most large industrial organisations.
Engineering Maintenance roles and their link to Performance Excellence
Maintenance and Engineering are very important to machine performance, so it comes as no surprise that engineers are deeply involved with Continuous Improvement.
In this video, we'll go over the basic structure of a Maintenance department (function titles vary a lot from company to company, but the jobs stay roughly the same), how they interact and what their link is to Performance Excellence teams and program.
The involvement of Engineering depends more on your company setup - if they're already really involved with day-to-day machine performance, they'll have a big role from the start of any CI program; if Engineering is mostly concerned with Capex projects, they'll come into the picture more when your organisation is ready to use deeper FMEA's and design for Six Sigma.
#continuousimprovement #maintenance #engineering
czcams.com/video/E3KfW_DuVWA/video.html
00:00 Introduction
01:36 Engineering vs. Maintenance
02:18 Maintenance Technician Roles
07:56 Shift Technicians and Team Leads
11:29 Storekeeper Role
13:52 Reliability Engineer Role
18:19 Engineering Projects and Handovers
In this video, we'll go over the basic structure of a Maintenance department (function titles vary a lot from company to company, but the jobs stay roughly the same), how they interact and what their link is to Performance Excellence teams and program.
The involvement of Engineering depends more on your company setup - if they're already really involved with day-to-day machine performance, they'll have a big role from the start of any CI program; if Engineering is mostly concerned with Capex projects, they'll come into the picture more when your organisation is ready to use deeper FMEA's and design for Six Sigma.
#continuousimprovement #maintenance #engineering
czcams.com/video/E3KfW_DuVWA/video.html
00:00 Introduction
01:36 Engineering vs. Maintenance
02:18 Maintenance Technician Roles
07:56 Shift Technicians and Team Leads
11:29 Storekeeper Role
13:52 Reliability Engineer Role
18:19 Engineering Projects and Handovers
zhlédnutí: 79
Video
How high should Cpk be? Why 1,3 - 1,67 is the sweet spot and 2 is too high.
zhlédnutí 84Před dnem
There is a school of thought that suggest you should have a Cpk of 2.0 - that is, in fact, very much in line with Six Sigma: having 6 standard deviations of process variance between the process mean and a specification limit will yield a Cpk of 2. But I would argue that this is too high for most companies and industries. In this video, we'll cover some rules of thumb for how high your Cmk, Cpk ...
4 roles of the Quality Function in Performance Excellence and Continuous Improvement programs
zhlédnutí 178Před 14 dny
A big part of Performance Excellence is gathering good Process Knowledge and ensuring strong Process Control. This is the role of the Quality function within Continuous Improvement (like the Quality pillar in TPM or Quality workstream in other programs). Regardless of the specific route you use to develop the Quality function, these are the 4 areas you need them to control and improve: 1) Claim...
Process Control: check Inputs and Output || How SPC differs from Process Audits
zhlédnutí 117Před 21 dnem
Processes have inputs and outputs - both can (and should) be controlled with Process Control techniques, but the methods and their goals are very different from input checks vs output controls. The main message is that you want to target for set-POINT inputs and output RANGES; so only 1 target for an input, no "free choice within a range" instructions to operators, but outputs should have a pre...
Coordinate improvement teams across the organisation
zhlédnutí 172Před měsícem
When your Improvement Program is picking up steam, you'll notice that there are way more teams, small and large projects and all kinds of Problem Solving efforts than you will be able to coordinate from a central level. Luckily, you won't have to: coordinate the direction, then train and trust your managers to specialists to manage improvement efforts on their level. This is sort of a part two ...
Managing Improvement efforts with the Infinite Loops of Performance
zhlédnutí 185Před měsícem
If you want to unlock Continuous Improvement and Shopfloor potential, then Performance Management cycles of Controlling, Improving and Visioning should be implemented on each management layer. This is video discusses the need to align KPI's (and Performance Control in general) to the different layers of management - you'll want to control direct process performance on a shift or daily level, wh...
Kaizen Events - When and How to use them
zhlédnutí 677Před měsícem
Kaizen Events are a great tool - they can motivate teams, bring people together across departments and create quick and lasting improvement. So when should you use them and how do they work? Kaizen Events are high-intensity, short-duration improvement efforts: within a couple of days, or at least not more than 1-2 weeks, you go through a full Process Improvement project. This, of course, doesn'...
OEE improvement value
zhlédnutí 229Před 2 měsíci
Most managers want to improve OEE on all manufacturing lines, but why? OEE is not an end goal, it doesn’t bring you any money, at least not directly. It’s just a measuring tool for efficiency losses. Yet every manager seems obsessed by it. So let’s dive into how you can put a value to OEE improvements. How to determine what to do with the created machine time. When OEE improvement projects are ...
How to pick Six Sigma and other Improvement projects
zhlédnutí 159Před 2 měsíci
There's so much potential to improve an any business, so how do you pick the best next projects for your organisation? First off, know that improvement is about moving the proven standard, not just getting back to previous performance (that's root cause problem solving). So we're going to look deeply into our processes and finding ways to make things easier, more efficient and/or more stable th...
Improvement Teams need 2 KPI's to track their results and contribution
zhlédnutí 163Před 2 měsíci
Have you ever seen an improvement team that fully reached their goal but the overall KPI needle didn't seem to have moved? When selecting Improvement teams properly, you will narrow down their focus to a single Failure Mode, or at most one very specific process characteristic. This is the correct way to set the team up for success, but it does open a little pit you might fall into later - you'v...
DMAIC Control phase
zhlédnutí 154Před 2 měsíci
The last, but certainly not the least, step of Six Sigma's DMAIC is the Control phase. Here we make sure that our improvements can be scaled to daily use over all shifts and teams. This means validating that all new standards work for everybody, supported by good training and follow-up. There are many lessons from Change Management that are super useful in the Control phase: * Make sure to use ...
DMAIC Improve phase
zhlédnutí 137Před 2 měsíci
This is where the magic happens - the Improve phase of Six Sigma's DMAIC. Just like with 'real' magic, much of the heavy lifting has already been done in the previous preparatory phases, but the Improve phase is where we come up with and test countermeasures to problems and/or set the most stable process parameters. All to ensure maximal performance and stable production. There are not too many...
DMAIC Analyse phase explained
zhlédnutí 168Před 2 měsíci
In the Analyse phase of Six Sigma's DMAIC, we take a deep look at the inner workings of your process: we've measured what exactly happens, now we must find out how that happened - which factors of the process lead to problems, or alternatively give the most optimal or stable process conditions. We will be exploring the physics of our process. Tools like the Cause and Effect diagram, Design of E...
DMAIC Measure phase explained
zhlédnutí 366Před 3 měsíci
The Measure phase of Six Sigma's DMAIC is all about understanding how your process behaves: How do problems present? What variation is there in your products? Can we see significant differences between shifts? And similar questions should be answered in this phase. We want to know what the process produces (we'll get to the how's later in the Analyse phase), and we'll want to go detailed. Yes/n...
DMAIC Define phase explained
zhlédnutí 350Před 3 měsíci
The DEFINE phase starts off the DMAIC Improvement framework - it's critical to set the right expectations: you'll want to define 🙋♂️🙋♀️ what the goals of the different stakeholders are; 🎯📈 how that translates into your team's goal; 💵⌚️ and what resources you'll need to achieve it. We'll talk about how to draw out the wishes and expectations of your own organisation, your customers (and yes, i...
What is DMAIC and when to use it | part 1 of 6: DMAIC overview
zhlédnutí 802Před 3 měsíci
What is DMAIC and when to use it | part 1 of 6: DMAIC overview
Project stakeholders typed by animal characters
zhlédnutí 60Před 3 měsíci
Project stakeholders typed by animal characters
5S's important effect on Performance Culture
zhlédnutí 118Před 3 měsíci
5S's important effect on Performance Culture
AM Autonomy: Unlock the Shift-Based Boost to your TPM implementation
zhlédnutí 85Před 4 měsíci
AM Autonomy: Unlock the Shift-Based Boost to your TPM implementation
How to Value Stream Map (VSM) in Low-Volume High-Variation production
zhlédnutí 328Před 4 měsíci
How to Value Stream Map (VSM) in Low-Volume High-Variation production
How to integrate Safety in Continuous Improvement and Operations Management
zhlédnutí 161Před 5 měsíci
How to integrate Safety in Continuous Improvement and Operations Management
Who to teach Root Cause Analysis skills
zhlédnutí 488Před 5 měsíci
Who to teach Root Cause Analysis skills
Percentages can be dangerous in calculations
zhlédnutí 104Před 5 měsíci
Percentages can be dangerous in calculations
Quick Changeover Steps (How to do SMED)
zhlédnutí 1,4KPřed 5 měsíci
Quick Changeover Steps (How to do SMED)
Off-Spec, a Defect that is good enough to sell? (on First Time Quality and the cost of non-Quality)
zhlédnutí 112Před 6 měsíci
Off-Spec, a Defect that is good enough to sell? (on First Time Quality and the cost of non-Quality)
Again, great video as usual. You're giving me a bunch of ideas for my AM initiative.
I like the idea of commissioning an AM team to determine the work needed. Do you think it should be a good mix of operators in terms of experience? Or should it be mostly senior operators?
Hey Tom, what do you think about incoming shift auditing the AM of the outgoing shift?
The new company i work for has multiple lines, but the main challenge in implementing across the lines is that there are multiple different products or value streams across the plant. In a way its more of a cell configuration where each product line is self contained. implementing an AM pilot is the main initiative i have. Your videos are always great resources as a form of reminder. Thanks!
This is excellent content. Keep up the good work!
just wow.. so many people have knoweldge, but not everyone can deliver their knowledge efficiently. i have not seeing someone breaking things down as easy as you are.. new subscriber
Thank you, that's so nice to hear. Hope you'll be enjoying many more of my videos and that they may help you professionally.
Every qualified quality engineer should be following some type of six sigma based problem solving approach. Key word here is “qualified”
For a great mini course on Quality Leadership within Performance Excellence, I recommend checking out BeltCourse: www.beltcourse.com/a/2147862028/6eADKB6z It's a set of nicely curated information on Quality Management, Total Cost of Quality and other concepts that are key learnings for any Quality professional.
great training material! thank you so much.
Hope you enjoy it and that it will help you teach Lean to your colleagues/students
Hi Tom! Thanks for a great video. In our organisation we are also introducting a Sustainability/Environment pillar, a Early product management pillar and a Flow/Lean pillar. Would be very interesting to hear your thoughts on these as well
Hi Karin, how great to hear, I'm guessing your program has had some good early successes, since you're implementing these pillars that are generally launched a bit later in the program. I'll pull my thoughts together and think about how to summarise those pillars into a video - they might be a bit less popular than the main TPM pillars, but they deserve some attention and explanation too 😉
Hello Tom. Greetings from Peru. A couple of weeks ago, I just heard about OLE, since for my thesis, I had planned to apply OEE, but they told me that this was more for machines. I work in the agroindustrial sector, in Peru, and in the activities of selecting and packaging fruit for export (fresh mango), it is done with people, manually.
Hi David, that's great to hear - hope you have great fun and learnings from your thesis study. Do note that the OLE calculations I describe here are based of machine OEE x crew size. This is a way to take machine effectiveness a level further and make it way more valuable than the usual manhours/units produced. If you're dealing more with people capacity and the machines are just there to help them (no really bottleneck machines or machine efficiency to deal with), then it's better to look at your Labor Effectiveness in much the same way as your usual OEE - that is, just the one-dimensional scale. Take away off-time first, then planned breaks etc, and then split real stoppages from overall lower speed and constant minor issues. To do this, you will need to have a standardised unit for measuring output per hour - that's a problem for many job shops, but I think it shouldn't be a problem in most agricultural companies, as it's high volumes with very comparable tasks day to day (at least while you're handling the same produce) - just like in most manufacturing.
Hi Tom - I would say look at the taguchi loss function, which says that the better the Cpk the lower the loss to society. It's another point of view on how high should your CPK be? The Batavia gear box plant is a great case study to look at as well....
Hi Paul, thanks for you reply, those are very valid points indeed. For anyone interested in this great video by Paul: czcams.com/video/vH-1deoUIZw/video.htmlsi=f3ZiBfe7v36B2IBp) I agree that continuous reduction of process variability will lower the loss to society (and is almost always beneficial for the producing company too). The issue I have with Process Capability (variation divided by specs) is that this ratio does not inherently benefit society, because the specification limits are more or less arbitrary. For a quality characteristic that applies to the design or direct function of the part (like the size of a nut, the positioning of a label, etc.) it's best to be in the centre, yes. I would still argue that you should consider transferring this decreased process variability downstream by promising tighter specifications (especially if the customer is willing to pay a premium for it - something Ford's competitors did, by the way, and that drove market for Mazda). When we're talking about a quality characteristic that is more like unilateral tolerance (like weight, break strain, etc. that usually have a hard minimum and a maximum that's more to have product categories), I would say it's often wasteful to stay more than 4-5 SD's away from that limit. In fact, especially in filling weights/volumes, you'll often see companies choose to stay much closer to that minimum, reducing the average when they successfully reduce process variation.
Good point about the specs - The loss function ignores the tolerances, as they are as you say arbitary often, when they should include an element of the voice of the customer. Good stuff as always Tom...
@@paulallen5321 and thank you for the challenge - it’s always good to add these extra nuances and the different angle of approach/thought 👍🙏
Tom, you may still use Fishbone. Ideally if there are multiple problem areas, you will have to create that many 5 why's !!!
Yes, of course you may still use the Fishbone, that's also the premise of this video - just try and get that 5 Why part outside of the Fishbone's visual. I would advice limiting how many 5 Why's you do - my general advice is to first check which assumptions in the Fishbone are true and then pick the 1 or 2 your team feels are most impactful to the problem -> start by diving into those with 5 Why before spending a lot of effort on deep diving all those minor causal factors. It's not a hard and fast rule, just advice to keep your Root Cause Analysis efforts more effective in 90+% of the cases.
based on the formula, if z remains unchanged and the SE is large = we get a smaller t value. A smaller t value indicates that the two groups we are comparing have a small difference and has less evidence against null hypothesis. But WHY and HOW does a high SE lead to a smaller t value?? Not on the mathematical aspect but on the theoretical aspect. How does a high SE affect the t value? I do not understand this concept. Would appreciate some guidance.
I am currently a QA Inspector, attending an interview soon for the QA Engineer position. It was a bit confusing at first, but along the explanation, i understand the relation between my current position and QAE. Thank you, sir!
Great video! Loved it. How often do you usually make an order as a client? Just wondering about this and mix of colors in orders. To make the game (1round) attractive and to make the results satisfying after improvements in next rounds. Do you have any tips?
I usually start with a roll every 30 seconds, just one plane ordered of the colour that was rolled. You might want to hint to the teams that they could negotiate with the client about higher or lower sales volumes (which translates to rolling every 20 sec, or every 40 or 45 sec.), but they will have to deliver on that promise of course 😉 Round one will be interesting in any case - they will make a mess of it because everything is new. Do mention that while they're allowed to build up stock, any inventory in the factory will be counted and cost them money 'for keeping raw materials and WIP'. A general bonus tip (if you can handle the extra workload as the game master 😅): ask the team members how they feel after each round, how smooth were things, how's their stress level, etc. At first, you'll likely hear that some stations are super busy and can't handle the load while others are relaxed, almost bored (and probably laughing at those busy colleagues, since it's all a game anyway). If you do rounds with good kanban, and definitely if you do a full silent round, you'll see that stress levels go down a lot (the silent round with kanbans in place is the most productive and relaxed 'factory floor' anyone has ever experienced).
We did a variation reduction kaizen in our plant and these videos helped add more structure and more pointers on that 5 day event. What you're teaching helped our event successful!!!
That is so great to hear - it brings me joy to know that my content helped you directly. Hope you’ll enjoy many more of my videos and wish you the best with your next Kaizen events!
This video is absolutely brilliant!! You nailed the journey and relationship between different activities for Quality Management pillars!
Thanks for those nice words, happy you like the video - feel free to share it far and wide 😉
Again a very well explained vid Tom, many thanks for making and sharing this.... Cheers/Roby.
Good to hear you liked the video, hope you enjoy many more of my videos. If you ever have a question or video request, don’t hesitate to ask.
@@TomMentink , Thanks Tom and from the next view will try and contribute whatever I can for the growth of this channel.
Brilliant explanation Tom, you made this so easy and enjoyable even for a guy who really does not like statistics....Deep respect and love from India/Roby. By the way subbed as well.
Thanks Roby. Statistics is a strange beast: some people just get it immediately, that was not the case for me either. I found that very practical examples were the key to understanding the concepts of statistics for me, and that’s why I always try to explain it in as simple terms as possible - hope that helps others. Glad to hear that it works for you 😃
Hi Tom, Once again a very insightful video. I truly appreciate the knowledge and experience that you are sharing, and as a Mechanical Engineer with a passion for CI I find it invaluable. I have a question: is the implementation of CI different in a power plant compared to any other production plant(for example cars, pens, etc.), since the main activity there is maintenance? And if so, do you have any recommendations on the best implementation approach? Thank you and keep up the good work Tom!
Thanks for the kind feedback, hope you enjoy many more of my videos. Since you’re not really producing a product, quality and product/service specifications will be less important (although I can imagine OTIF is really important and the market expects immediate reactions to demand changes 😅). That means you use the Planned Maintenance side of CI much more: deeply get to know your machinery, how wear and tear affects parts and make preventive maintenance plans accordingly. Many of your larger spare parts are ridiculously expensive, and also have very long leads times when ordered new, so you benefit even more from conditions based maintenance than most other industries. Of course the basics will work for you just as for any other: organise workplaces for optimal efficiency, safety and comfort with proper 5S, control standards on the 4 M’s, foster a Kaizen mindset of making and maintaining small improvements every day.
Thanks for the kind feedback, hope you enjoy many more of my videos. Since you’re not really producing a product, quality and product/service specifications will be less important (although I can imagine OTIF is really important and the market expects immediate reactions to demand changes 😅). That means you use the Planned Maintenance side of CI much more: deeply get to know your machinery, how wear and tear affects parts and make preventive maintenance plans accordingly. Many of your larger spare parts are ridiculously expensive, and also have very long leads times when ordered new, so you benefit even more from conditions based maintenance than most other industries. Of course the basics will work for you just as for any other: organise workplaces for optimal efficiency, safety and comfort with proper 5S, control standards on the 4 M’s, foster a Kaizen mindset of making and maintaining small improvements every day.
Brilliantly explained 😊
Glad you liked it, hope it can also help you explain our field to friends and colleagues 😉
Thank you Tom! very good video and I got a better understanding of these methodology
I'm happy to hear you liked the video and got value from it! If it raises any other CI questions or suggestions for future videos, don't hesitate to ask - I'm happy to make videos 'on demand'
Hi, If I have my main inventory stock and then stock in a 3PL warehouse, how can trigger automatically using Kanban as a resource ? IFS Apps 10 system. Any idea please ?
If they have different items in the 3PL than in your main warehouse, just treat them the same as any other product in your warehouses - determine the replenishment rates and stock levels and set up Kanban from there. If they are a sort of middle warehouse between your suppliers and you, then they will have a much more specific role to play: they will be your buffer between 'shop floor replenishment' and actual ordering from your supplier. Things will depend on what flexibility that 3PL warehouse has; say for example you're having daily freights and have to provide a picking list 16:00 the day prior, any Kanban card or empty box seen during a check round that comes in before 16:00 will be delivered the next day, boxes that are emptied later will have to wait 2 days before they're replaced. So make sure the remaining number of boxes will last you at least 2 days. Also, make the boxes big enough that it's easy to handle for your 3PL (if they only want to send you full pallets, than your 'box size' becomes a fully pallet...).
what happens if bias fails but cgk is good type 1 study
When your measurement system precisely gives you the same bias, you will structurally affect the process or product you’re using that measurement for. If you use it for SPC, you might get away with it, but practically, it’s always better to do a proper calibration to remove or correct for the bias. Gage R&R will not find a bias, unless you’re comparing multiple measurement systems to one another. Therefore make sure you have a calibration process in place next to R&R testing.
Hi, Tom, you said, "I don't like Mother Nature that much as a category." You then explained how the category can be useful. I want to share a story about how we once used Mother Nature to our advantage. At a former employer, one of our products failed QC sporadically. The product was known to be sensitive to moisture, so we took care to use dry reagents and solvents and to run and process the reaction under an atmosphere of dry nitrogen. However, we still had sporadic failures. By looking at the weather, we realized that some days were simply so humid (relative humidity/RH) that they overcame our rudimentary engineering and process controls, leading to unwanted reactions within the product and consequent failure of the product in QC. Since the employer was unwilling at that time to spend money on better controls, we decided to run the reaction in wintertime, when RH was generally quite low and our existing engineering and process controls could cope with the atmospheric moisture. We ran the reaction at a large enough scale to meet our supply needs for the upcoming year. This meant we had to order and process larger quantities of raw materials. We got significant discounts on our larger bulk orders of raw materials, which had the beneficial effect of lowering our cost/gram for this compound. I don't think the solution was ideal by any means -- better engineering and process controls would have been preferred -- but by working with the situation we had, we ended up with a lower price-per-gram for the product, so it was a win for us in the end. 🙂
Hi Robert, this is a brilliant example of when Mother Nature can be a very useful category. In this case, it has additional benefits over just considering the Materials category, since the original material is most likely up to specs. The reason why I don't always like the Mother Nature category is because of the larger risk to blame some outside influence and not come up with actionable conclusions. It's certainly not a bad category to consider, just make sure it doesn't become an excuse bucket. If you would have used just the 4 M's, you could have gotten to the same conclusion if checking your storage Methods against the advice from the supplier. But I'll immediately admit that your stating Mother Nature as an explicit category helped that process along.
Really confusing
Hi Tom, thanks for nice summary. I have a question about the results and benefit. What could we expect after succesful implementation of AM? Could we say for example: 25% OEE improvement is possible? How was the result in your case?
That would really depend on the original situation - 25% OEE gain is very big, so in practice such numbers will only come from AM if the original OEE is under 50% and much of the lost time comes from unplanned stops and low speeds. I've seen some lines really blossom after even a small (but intensive) start of AM dealt with a bunch of problems the machine incurred from lack of proper maintenance and attention to the operating standards. In general, I would put expectations at around 25-50% of the current time lost to unplanned stops. That gives a pretty good first estimate of the OEE benefit. Also don't forget that proper 5S and AM have many more benefits than pure OEE numbers - the reliability of the line goes up, but also the reliability for quality, employee happiness and efficiency, detection and prevention of problems.
Please be careful with you language as you explain these statistics. ppk 1 is not "horrible".. its likes a 0.1% scrap rate which depending on the situation can be EXCELLENT... you also generalize long term short term as "today" vs the "whole year". This can lead to misconceptions and conclusions from your audience.
You’re right, there is a lot more nuance with these studies, and I take a couple liberties to get the general concept across. I try to balance precision with easy to understand, which is a balance that will never be right for everyone. On Ppk of 1 being horrible, I agree with you - that was an overstatement: Ppk of 1 to 1,3 is good enough. Thanks for that correction.
What if you want to compare the eficiencia of multiple products at the same time because your trying to eliminate some products.
VSM is not the best tool For such a comparison, but it will help you to first identify bottlenecks in the process and then you can check which products strain those bottlenecks most. When choosing between products to eliminate, I’d start with their profit margin (but do include the real cost for smaller volume products, not just an average of setup times etc.) and look at VSM and capacity to see for which products you should look only at variable costs (for products that you make on machines that are not at full capacity yet) and for which you should compare profit vs alternative products (when production capacity is fully utilised and you need to choose which products to produce).
If this topic of choosing and managing Kaizen Events is interesting to you, you’ll also love the Kaizen Leadership course my friends over at Belt Course have put together: www.beltcourse.com/a/2147833560/6eADKB6z This course starts from the things covered in this video (in fact, this video is the intro to that course 😊) and then goes on to cover all the aspects needed to successfully lead Kaizen Events and keep the gains. And a very nice thing, you simply cannot get from CZcams, is the simulation exercise where you actually practise those skills.
Thank you very helpful!
Happy to hear you liked the video, thanks for sharing that.
Hi Tom! Great video as always. I think what makes Kaizen Events work is having a structure to bring all the SMEs involved in the same room and look at the issue / problem at a high level and being able to zoom in with the SMEs.
Yes, that is a big factor. It is especially important for solving (often cross departmental) organisational issues - hence the usefulness of Kaizen Events for such cases. But it even seems easier in practice to free up key players (like the Subject Matter Experts you mention) totally for a few days than to get a couple hours from them for 3 months 🤷♂️
thank you, this was very helpful!
Glad to see you liked the video and got value from it. Thanks for sharing that. If it raised any questions, or you just have a future video request, don’t hesitate to share that too 😉
@@TomMentink yes sir, thank you! I appreciate you!
You need a better microphone 😊
Thanks for the feedback. I agree, the sound isn't pleasant enough to listen to and the sound of the marker is way to screechy in these older videos (it was already much better in this one than videos of about a year before)- so I got myself a new microphone about 9 months ago. What I also learned is that the microphone itself is really not the whole story, they're actually quite finicky to set completely right, there's a lot to learn about positioning, interference, post-editing corrections, etc. Do you like the sound quality in my more recent videos better?
It's not really the mic. I think it's mostly the mixing. If you are able to manage to do small mixing progress it will definitely be better
@@dyyleokid4634 I'll dive into that some more (sound and video are not my main expertise, but I'm always learning in that field to make better future videos 👨🎓)
Your videos are underrated. You explain things clearly and you deserve more views.
Hahaha, I couldn't agree more 🤣 I'm happy to hear that you like my videos and get value from them - thanks for sharing that. And that's probably also the best way to help me: feel free to share my videos with whomever you think might benefit from them too.
I agree! I've been a watching his videos for over a year now and im always getting great value from his videos!
Thanks
My pleasure! I’m glad you liked the video.
Loved this! I'm currently starting training to become an Associate Quality Engineer, (currently in a QA role) this was a great explanatoin of the differences in roles.
Thanks for sharing that - I'm glad you liked the video and hope it will help you along in your journey! If you every run into CI or QM related questions or just have a suggestion for future videos - don't hesitate to ask, a good question makes a much more useful video (and at least one person will be looking forward to it 😅)
If you want to be considered qualified and competent you should hold a formal six sigma certificate of green belt or higher
@@NoBubbles I would say the need for a formal (usually external) certification depends on region and culture, but yes - Quality professionals should be proficient in root cause analysis, process thinking and conditions management. A Six Sigma certification is a good way to learn these skills and prove that you have them.
Always a good discussion. Amazing to see that we still use Availability - Performance - Quality indicators. Who started this? These categories are not understood, not actionable, owned by a diverse group of functions ... useless in every way. Good categories link losses to one owner, who uses one dedicated tool, who owns the loss intelligence.
Hi Jasper, totally agree - I don't like the A-P-Q split for OEE either, but it's one that's used a lot 🤷♂ One of the things I advise people to always take into account is to define which time losses are planned vs not planned - and these aren't even categories, it's a simple matter of what does your planning department explicitly define vs what just happens at more or less random moments: czcams.com/video/vruTx66L78U/video.htmlsi=O3x54aE0eY97Jie8 And there's a whole set of more detailed OEE categories (as you know well, I know that much😉). This video (czcams.com/video/lDEd5muY7cU/video.htmlsi=PuCY4CtbiFD2SkTF) goes into my reasons for wanting to split out OEE categories - having dedicated owners and tools per category is an important reason, as is the time scale at which I think you should be looking at these categories (e.g. speed losses are something operators can act on on an hourly basis, while setup standard times are something you'd probably want to reduce with organised teams working off a quarterly or yearly improvement roadmap). Hope those two videos give a more nuanced view and they might be a better starting point for a discussion that will truly benefit the community with your experience and insights 😃
Hi Tom! Ive been meaning to leave a comment when you released this video. Main purpose of the value stream map initiative is to drive TAT reduction and improve OTD. We did a quantity-profit analysis to figure out which products to focus on. Using historical data, we found out that we had a handful of processes that has a high idle time, which drove the TAT. 12:13 we do have furnaces and heat treat process and you're absolutely right that it's one of our bottlenecks due to high run time and high change over time.
Great to hear your experiences - I'm sure other viewer also love it when you share such things (we're all CI enthusiasts out here, after all). Especially with these low-volume production runs, turnaround time and on time delivery are key indeed. You'll probably have seen that OEE isn't all that useful for making impactful improvements, but flexibility, change-over time, and the like are really important. Great stuff, thanks again for sharing.
@@TomMentinkoh yes, definitely! OEE doesn't make sense when we have equipment that only has 11% utility rate 😂
Thx ❤
My pleasure - hope it helps you in your career and development
This is great! Thanks, Tom!
My pleasure - happy to hear that you liked this one too 😃
Hi Tom. I just want to say thank you for all the valuable content you put out for free, which allows people who are new to the CI profession, such as myself, to hone and develop our CI way of thinking
Thank you for taking the time to share those kind words. That's exactly why I started this channel - I couldn't find a lot of good practical CI advice in video format, so it hit me that instead of feeling down about that, I should contribute my experience learn that way 😇 If you ever want to support the channel, and learn even more in the process, check out my online courses at www.tommentink.com. But you getting value from my content and making yourself and others more productive is the best form of gratitude. Wish you a great personal continuous improvement journey 😉
Good Presentation Tom
Thanks - glad to hear you like the video!
Mooie uitleg!
Dank je. Goed om te horen dat je de uitleg en video kunt waarderen. Mocht je trouwens vragen of suggesties hebben voor volgende video's, schroom niet om een verzoekje achter te laten 😉
Very informative, Thank you.
My pleasure, I'm happy to hear that you liked it.
Tom, excellent content, so glad I found your channel!
Thanks for taking the time to share that praise - makes me happy to hear you like my work. If my videos raise any questions or suggestions for future videos, let me know.
Thank you so much
My pleasure - I'm glad you enjoyed the video. Thanks for taking the time to share that ☺ If you have questions or suggestions for other videos, don't hesitate to ask.
I had Kne'x donated to my classroom. How would I do this for a Simulated Green Belt Project for my high school students?
That is lovely - if anything, Kne'x is even more tricky that Lego (because it can turn to any angle and the connectors have more multiple angles), so the difficulty of building it from a written instruction is also much higher. It will also be a bit more tricky to make the Kne'x shapes in PowerPoint (or other software), but don't forget to focus on the instruction - it doesn't have to look 100% accurate, as long as it's a clear instruction. Don't know if you ever put built an IKEA piece: those instructions also often aren't to scale in the intermediate steps, leave out loads of detail and only focus on the key points for each step - great instructions. Also check what you can build and how many copies you'll want (how many groups at the same time) - this will likely limit the size and complexity of the building. But that's ok - you want a simple construction anyway: they should be able to build it in 1-2 minutes with the clear visual instruction, it'll cost them around 10 min or so with the written instruction. For the classroom, there is another issue: your pupils probably haven't written many instructions, they haven't themselves been taught to make those pretty formal text-based instructions (and you probably don't want to tell them that the Languages faculty is teaching them a wrong way of writing reports 😅). So maybe first ask them to write an instruction for some task they do in the classroom, a game or hobby, a chemistry experiment, or something like that. This way, they have some reference to what their preferred way of writing instructions is. They can then use different example instructions, combined with the learnings from playing this game, when making the instructions coming out of their Green Belt project. Or alternatively, you could ask them to collect/copy a number of instructions as preparation for this game, and even ask them to improve upon one of the instruction they found (especially useful and fun if it is an instruction for something in your school - if it is an improvement, they'll also get the satisfaction of seeing their work taken up as materials for the next group of students). footnote: writing an instruction is only 1 part of the skillset of a Green Belt, and it wouldn't receive much attention in most Green Belt courses since it's a more generic skill. The specifics of Green Belt are good Root Cause Analysis skills and a small set of statistical and data analysis tools - a Green Belt first and foremost has to be able to understand process physics and make the process more stable. But I honestly think that for high school students, learning how to make effective instructions is more important than the typical Green Belt skills: thinking about how the reader will interpret it and how to make it as easy as possible for them, being able to imagine your reader without the knowledge you're trying to impart and thinking from viewpoints and understanding different from your own - those are the competences that build great colleagues in any profession.
Thank you for sharing, greeting from Lima Peru
My pleasure Edmar, glad you liked the video and hope it will bring value for you. If you’ve got VI questions or video suggestions that would help you even more, please don’t hesitate to tell me 😉