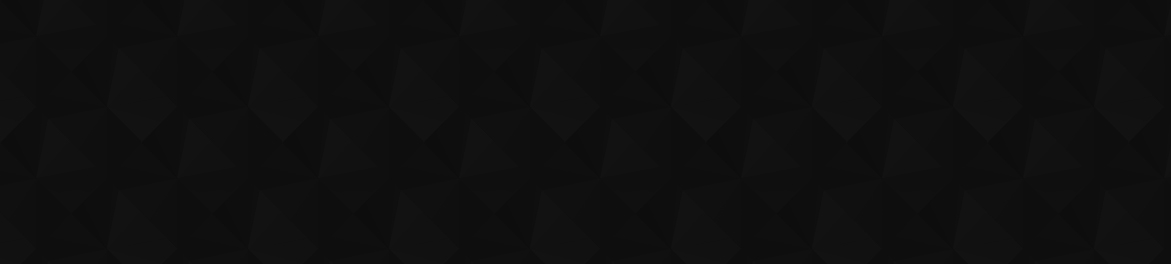
- 15
- 1 665 817
Byham Knives
United Kingdom
Registrace 25. 02. 2018
Small UK knife maker
Check out my website where my knives are for sale - shop.byham.co.uk/
Check out my Instagram - byhamknives
Check out my website where my knives are for sale - shop.byham.co.uk/
Check out my Instagram - byhamknives
Making a DAGGER from Scrap Steel
In this video, I take a scrap peice of steel and turn it into an ornate stiletto dagger, with reletively basic tools. I learnt alot of new techniques whilst making this, and had alot of fun!
If you enjoy my content, you can help out by subscribing for more!
Check out my website where my knives are for sale - shop.byham.co.uk/
Check out my Instagram - byhamknives
If you enjoy my content, you can help out by subscribing for more!
Check out my website where my knives are for sale - shop.byham.co.uk/
Check out my Instagram - byhamknives
zhlédnutí: 1 735
Video
Forging Simple Chip Carving Tools | One Day Build
zhlédnutí 3,7KPřed 3 lety
In this video, I forge a pair of chip carving and Kolrosing tools, designed for carving intricate details in wood. The steel was a 6mm bar of O1 tool steel which has great edge retention and is very forgiving in heat treat. The handle woods are peices of London Plane which has a very unique and interesting grain. Ive never forged such small tools before so this was a fun DIY challenge and im ve...
Handmade Puukko Knife From A Broken Sawblade
zhlédnutí 25KPřed 3 lety
In this video, I take an old broken sawblade and turn it into a Finnish inspired Puukko knife. This knife had my most complicated, decorated handle yet and I am super pleased with how it turned out. I hope you enjoy, if you do, consider leaving a like or subscribing for more content, it helps alot! Check out my website where my knives are for sale - shop.byham.co.uk/ Check out my Instagram - in...
Restoring A Vintage 1950s Blowtorch
zhlédnutí 478Před 3 lety
In this video I try my hand at something a little different. This 65 year old, British made BURMOS blowtorch has been sitting in my workshop for a while and I've finally gotten round to restoring it. This was a really fun challenge and I hope you enjoy watching me figure out how it works. If you do, consider subscribing to catch future videos. Check out my website where my knives are for sale -...
How I Make Custom Mosaic Pins
zhlédnutí 9KPřed 3 lety
In this video, I show the process of how I make my custom mosaic pins from scratch. I've been doing this for as long as I've been knifemaking and I beleive that it adds alot to finish off the handle. Consider subscribing and turning on notifications if you enjoy and want more. ENJOY! Check out my website where my knives are for sale - shop.byham.co.uk/ Check out my Instagram - byh...
Finishing the Forged Carving Knife and Fork!! Part 3
zhlédnutí 978Před 3 lety
In this video, I finish my work from the previous parts, in completing the Carbon steel carving knife and fork. In previous episodes, I forged and then ground the tools to shape and in this video I make and finish the maple and brass handles on the meat carving utensils. Check out @lamproknives Check out my website where my knives are for sale - shop.byham.co.uk/ Check out my Instagram - instag...
Hand Forged Carving Knife and Fork!! Part 2
zhlédnutí 1,1KPřed 4 lety
In this video, I continue the work on the high carbon meat carving knife and fork, the fork was forged in the previous episode and in part 2 I grind and file the knife and fork to shape. Consider subscribing and turning on notifications if you enjoy and want more. ENJOY! Check out my website where my knives are for sale - shop.byham.co.uk/ Check out my Instagram - byhamknives I m...
Forging a Carving Knife and Fork!! Part 1
zhlédnutí 1,4KPřed 4 lety
Find out how I forge a carving knife and fork. This is my first attempt at forging a fork and so far i'm pleased! Consider subscribing and turning on notifications for the next part if you want more!! ENJOY!! Check out my website where my knives are for sale - shop.byham.co.uk/ Check out my Instagram - byhamknives
How I Make My Bushcraft Knife Sheaths
zhlédnutí 3,1KPřed 4 lety
A film documenting the process of how I custom make leather bushcraft knife sheaths by hand. Consider subscribing and turning on notifications if you enjoy and want more. Enjoy! Check out my website where my knives are for sale - shop.byham.co.uk/ Check out my Instagram - byhamknives
How to Carve A Spoon With Hand Forged Knives (Feat - Andrew Byham Woodcraft)
zhlédnutí 1,7KPřed 4 lety
Start to finish of carving a spoon out of beech, using hand forged carving tools, as seen in this film - czcams.com/video/ilBtXMw0j8c/video.html featuring Andrew Byham Woodcraft - andrewbyham Check out my website where my knives are for sale - shop.byham.co.uk/ Check out my Instagram - byhamknives
Forging Spoon Carving Knives In 1 DAY!!!
zhlédnutí 13KPřed 4 lety
The process of hand forging a wood carving knife and Bowl hook, used for carving wooden spoons. 01 tool steel blades and London Plane handles. Enjoy! Check out my website where my knives are for sale - shop.byham.co.uk/ Check out my Instagram - byhamknives
Matching DAMASCUS Steak Knives
zhlédnutí 13KPřed 4 lety
How I made these 2 twin damascus utility/ kitchen knives. The steel is 1095/ 15n20 with Ovangkol scales and mosaic pins. Check out my website where my knives are for sale - shop.byham.co.uk/ Check out my Instagram - byhamknives
Handmade Japanese Style Mini Kitchen Knife
zhlédnutí 7KPřed 4 lety
A short film showing the handmade process to create a Japanese style kitchen knife. The blade is made from 01 tool steel with an Oak and Quilted Chechin handle. Thankyou for watching, Stay safe. Check out my website where my knives are for sale - shop.byham.co.uk/ Check out my Instagram - byhamknives
Knife Making | DAMASCUS Hunting/ Camp Knife
zhlédnutí 34KPřed 4 lety
The creation process of a 1095/15n20 damascus hunting knife. Enjoy and Thanks for Watching! Check out my website where my knives are for sale - shop.byham.co.uk/ Check out my Instagram - byhamknives
Making a Bushcraft Knife From Scratch
zhlédnutí 1,6MPřed 6 lety
Video of the making process of of a bushcraft knife. This knife is made out of 01 tool steel with stabilized London plane scales and a matching ferro rod. Enjoy! Check out my website where my knives are for sale - shop.byham.co.uk/ Check out my Instagram - byhamknives
Scratch?
90min in oven but how many degrees?
Great video. Where you taking knife templates frome ?
I watched a couple of your videos, but only part way through each one. Your setup really could stand quite a lot of improvement. You have your gas forge setup outside and your homemade anvil inside. You are taking no less than half a dozen to a dozen footsteps from your forge to your anvil one way. Your work piece is being exposed to outside air for way too long. As a result your work piece is cooling down below a forging temperature, which is a bright yellow orange to yellow heat. Your homemade anvil is too big for the tiny tools you're making. Although it's good and flat, you don't have a proper way to lay the piece flat for working and reworking. That piece of plate steel was cut with a cutting torch. It shouldn't be too much of a stretch to have it cut again to a narrower profile width. The sides could be ground and the cutting marks removed to give you a good flat surface. Also (and not to put too fine a point on this) your homemade anvil wanders way too much. The result is you don't have as much control over your work-piece as you could have if you had a solidly fixed anvil surface. Your hammer is good. It seems to be a good size 2.5 pound ball peen hammer. But you need a sharp true edge that is slightly rounded on one edge. You also need a good pritchel hole to go with your square hardy hole. I would recommend drilling 4 anchoring holes to the corners of your anvil, but leave the center untouched. Anchoring the anvil plate down at 4 corners will offer good stability and will not allow the anvil to move or wander during use. The wobbly and wandering anvil is also a safety hazard. Do you have any idea how much that amount of steel can do to a foot if it falls on it? How much damage it can do falling down your leg, possibly hitting your kneecap on its way to the floor? Safety first, foremost and always sir. You have a decent enough propane forge. Close off both ends with fire brick, or weld a hinged door on one end with an open vent that's about 2"x2" square. You'll get better heating and heat control. Your steel will heat to a forging or even a welding temperature much faster if one end is closed but vented. The front end can still be closed off with firebrick for heat retention. your forge could further be improved by raising the inner floor deck by about an inch. Move and raise the floor closer to the burner. It will burn more efficiently and use less gas because your steel will heat up faster. you have a good shop, but it needs a lot of tweaking and improvement... move your anvil closer to your fire source so that you take the fewest steps possible. You'll lose less heat and will be able to forge your projects much easier and quicker. Thanks for sharing and good luck!
I’ve watched a lot of knife videos but got to say this was one of the best beautiful result with fairly basic inexpensive tools loved it 👍🏻🇬🇧
Don’t know if you’ve tried this before (it’s been five years so I’m sure you have but it never hurts to say), but if you dip the entire blade in the oil during the quench it’s less likely to warp
Very very nice
I have an idea for a dagger which i like and i would like to make my own dagger but I don’t know how or much about blacksmith stuff except from youtube videos How could i learn and make my own dagger without having to do proper blacksmithing?
Una obra de arte excelente 👍🏻 muy bonito cuchillo
Is grinding steel bad for your lungs even if you wear a respirator?
the brake fluid bleeder idea was brilliant!
Are you still selling these - sent a message requesting info on your website, but no response. Look just what I need.
This is not from scratch how did you make that steel?
Excellent
can I have the pdf file for the knife shape template please?
Nice work
really nice camera work (on top of the carving of course)
What was the glue type or brand? Is it jusr epoxy?
Nothing to say.. this is great
I We'd like to buy one of your knives or a set of your knives. Hunting knives set a 4 and a 6"
on god that knife 4 real
Закалка можно сказать отсутствует, на первичку 1150гр. отпуск только с "бубнами", и только тогда удовлетворительный результат, алмазы действительно не берут. Другого пути в домашних условиях нет.
QUE PEÇA SUPIMPAS.
На сколько работа хороша?, клинок сырой, закаленный клинок из р6м5 данной фрезы алмазы у меня не берут а тут наждачкой шлифует, закалку с данной температуры 850-900гр. эта сталь не возьмёт.
How much would it cost for you to make me a knife with a fero rod just like the one you made in this video
Going to try this! What length are you cutting to with the gauge at 00:50? Thanks.
Thanks! It doesn't really matter the length, but I think I made two 12cm and one 6cm from the lengths of smaller tubing
Excellent work! A meal with these must taste at least twice as good. 🙋🏻♀️Anna
Perfect technic, clear and professional...👍
would have liked to see them in action.
Hi There, I have a video on my channel here: czcams.com/video/yZURgkW6K8c/video.html&ab_channel=ByhamKnives showing them in use. Thanks for watching!
wait a angle grinder came be fitted with a disk for cutting metal?
Absolutely! Much faster than a hacksaw!
So much hand work. Love them
Хорошая работа
I have some sawblades like that. Any idea what kind of steel they are? Ive made a few Ulu knives from them. Very hard to drill holes for handle pins
There's no easy way to find out the type of steel unfortunately, but in saw blades, it's often very hard and very brittle as you find them. You would have to aneal the steel before drilling any holes by heating it up to a cherry red colour, and letting it cool very slowly. That should soften it enough to drill.
Beautiful
Just made a bone knife took inspiration from these videos thanks
Хорошее видео. Отличная работа!
Привет из России! Ножи супер у тебя!!!
bro.. next time making hidden knife from old file.. keep healthy and stay creative..
bout time you got yourself a propper anvil IMO
Hey what's the name of the thing your dad's using to hold the spoon secure whilst carving?
It's actually his own design of a "spoon mule". There's a huge range of different methods for clamping the spoon and this is his.
@@byhamknives4708 great stuff and thanks, hope you're all staying safe, when this is all over I hope to see you at some events again :)
great job.. setiap orang memiliki ide briliant untuk menjadikan barang yang tidak berguna menjadi berguna kembali.. keep spirit and stay creative..
Thank you!
Hey , you made an awesome knife. I have some suggestions. Try not to cover the piece that you work on with your hands or body when you film and if it was a bit brighter it would be nicer. Also your antler piece was not the best size for your handle so you reached the porous part . Anyways keep it up :)
Thanks for the advice! I often find myself in the moment while working and forget I'm filming. Only realise the footage isn't amazing when I come to edit. And yes, it was my first time working with antler like this so I have alot to learn.
That's a beautiful knife but unfortunately way too brittle.. The steel you're using is super HSS. It's made to cut steel, and is super hard. Tempering doesn't work on it, it doesn't get any softer before reaching 500°C.. So even a high temper wouldn't make it strong enough to make a good knife. I've done a knife or 2 with this kind of steel, and it's basically like ceramic knives. No shock, no hard use, no flex, or it'll break... So I'm afraid it's not a great choice for a pukko. Heating the steel to make it softer is called annealing, not normalizing 😉 Normalizing is another part of the heat treat process. Overall it's a beautiful knife but bad steel choice, too bad but that's part of the learning process 🙂
It's actually very flexible. I too was cautious when I started the knife, as I was able to break pieces of the saw blade easily but after the heat treat and temper I stuck it in a vice and put all my weight on it. Supprisingly it bent to at least a 45 digree angle and then sprung back up to straight. Not entirely sure what I did but it worked.
@@byhamknives4708 oh then it's fine, I'm suprised. My bad, it's probably not super HSS as I assumed, anyway it's a great knife !
Well; it's a beautifull knife, and the steel choice is OK; but when I saw you dunk it in the oil, I expected it to shatter. It didn't, so I rewatched the video and probably have an answer :-) the steel used in these is commonly M42 HSS or 1.3247 (you can find a datasheeth here: ucpcdn.thyssenkrupp.com/_legacy/UCPthyssenkruppBAMXAustria/assets.files/download/werkzeugstahl_schnellarbeitsstahl_datenblatt_tk_3247_de.pdf). This is an air hardening high steep steel used for metal cutting. This steel is very highly alloyed, and requires ridiculous temps to harden throughout.... literally 1160 to 1190 degrees C (almost 2150 degrees F). This is very light coloured yellow. When you "annealed" the blade; you actually just tempered it back to HRC 50 to 55. I betcha it didn't like to grind even annealed (and you can hear this in the screetching of the needle file). Suprisingly, it isn't very wear-resistant at that hardness. When you hardened it in oil; you didn't really hardened it completely, as you didn't reach the required temp nor kept it long enough, as this steel requires a long soak. So coupled with decarburization - this steel really likes to decarb- you probably end up with a good knife. And now you also know why few knifemakers use this steel, even tough it can make good knives.
I dig it, prolly would have done some sort of spacer so the handle materials don’t clash so much. But it’s very pretty, I like the natural material aesthetics.
Beautiful knife. What finish did you use on the wood?
I just use a coat of linseed but things like walnut oil work well too
@@byhamknives4708 thank you. I’ve had an order from a restaurant for some steak knives and I’m trying to find the best finish that will last the longest for them.
what is the width of the blade
The blade was around 3cm wide and about 3mm thick
@@byhamknives4708 thankyou 🙏🏿
holy shit production good. I agree zoom could be bit less
I've seen custom belt buckles made of a plurality of pipes fitted in a bigger pipe... though those were bigger. And welded together on the back, rather than epoxied together, if I recall correctly. Certainly the belt buckle hook and loop that engage the leather of the belt were welded (or brazed) on.
ахуенно
👍👍👍