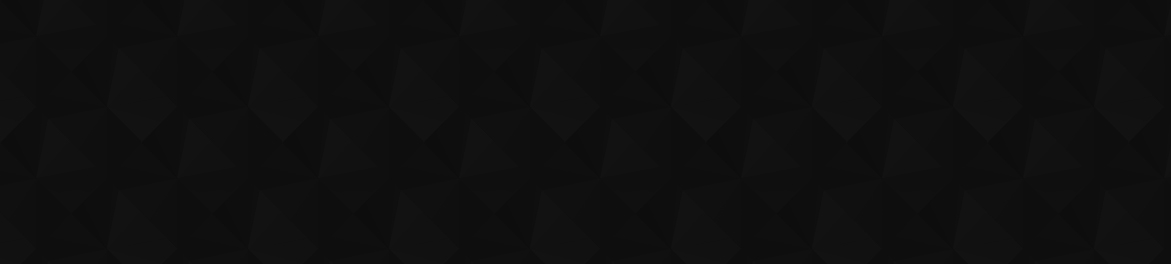
- 106
- 1 344 162
Advanced Thermal Solutions, Inc.
United States
Registrace 18. 05. 2010
Innovations in thermal management and electronics cooling are the focus of ATS, a leading-edge Massachusetts based engineering/manufacturing company. Our industry leading heat sinks, heat pipes, chillers, coolers, instruments and consulting make us an ideal partner for any thermal management application. As an industry leader, ATS values the importance of further developing the electronics cooling industry and offers short courses, tutorial programs, free monthly webinars, and publishes the free online magazine, Qpedia. Our youtube channel gives you an exclusive look inside the Thermal Characterization Laboratory, producing the latest innovations and product releases, instrument demonstrations, and fundamental educational engineering videos for all levels of engineers, from students to industry leaders.
Have a question on a video? email us at ats-hq@qats.com and we'll send you an answer.
Have a question on a video? email us at ats-hq@qats.com and we'll send you an answer.
LQHS - Liquid Qooled Heat Sink
For cooling high heat components, LQHS heat sinks combine an active fan mounted to a heat spreading base with internal channels of flowing coolant. With the liquid assist, LQHS heat sinks provide thermal performance at least three times higher than fan-assisted heats sinks without liquid loops.
LQHS heat sinks are combined with pumps and coolant reservoirs to provide continuous, high-level cooling of hot CPUs, GPUs, FPGAs, and AI processors, along with IFBT, MOSFETs and DC-DC converters. For even higher cooling levels, a heat exchanger can be added to the liquid-cooling configuration. ATS provides recommendations for (non-included) fans per user application.
More information - www.qats.com/Products/Liquid-Cooling/Liquid-Cooled-Heat-Sinks
----------------------------------------------------------------------------------------
www.qats.com
Advanced Thermal Solutions, Inc.
A leading-edge engineering and manufacturing company focused on the thermal management of electronics.
Service, Products and Training
• Cooling Solutions - From Chip to System
• Mechanical Packaging and Design
• Design Services
• Air and Liquid Cooling Solutions
• Rapid Prototyping
• Custom Heat Sink Design
• Research Grade Thermal Instruments
• Engineering Training
• State-of-the-art Experimental Laboratories
• Qpedia Thermal eMagazine
LQHS heat sinks are combined with pumps and coolant reservoirs to provide continuous, high-level cooling of hot CPUs, GPUs, FPGAs, and AI processors, along with IFBT, MOSFETs and DC-DC converters. For even higher cooling levels, a heat exchanger can be added to the liquid-cooling configuration. ATS provides recommendations for (non-included) fans per user application.
More information - www.qats.com/Products/Liquid-Cooling/Liquid-Cooled-Heat-Sinks
----------------------------------------------------------------------------------------
www.qats.com
Advanced Thermal Solutions, Inc.
A leading-edge engineering and manufacturing company focused on the thermal management of electronics.
Service, Products and Training
• Cooling Solutions - From Chip to System
• Mechanical Packaging and Design
• Design Services
• Air and Liquid Cooling Solutions
• Rapid Prototyping
• Custom Heat Sink Design
• Research Grade Thermal Instruments
• Engineering Training
• State-of-the-art Experimental Laboratories
• Qpedia Thermal eMagazine
zhlédnutí: 1 436
Video
POLARVrTX™ - High-Capacity Air Cooling
zhlédnutí 302Před 5 měsíci
ATS POLARVrTX™ family provides high-capacity active cooling that outperforms liquid cooling options, making them a cost-effective thermal solution. When deployed in high power systems that would normally be cooled with water, POLARVrTX™ provides the thermal resistance of water using air. Added benefits of air cooling versus liquid cooling include low maintenance, uniform cooling, and ease of in...
TEChill Heater and Chiller Family Overview
zhlédnutí 172Před 9 měsíci
TEChill chiller and heater systems are based on Thermoelectric devices (Peltier, TEC) that provide precision heating and cooling of the fluid medium. TECs are semiconductor refrigerators and heaters that have no moving parts. This eliminates the kinds of failures associated with vapor compression for refrigeration. TEChill is capable of 1.4kW or 2.1kW. Learn more - www.qats.com/Products/Liquid-...
ATS picoHEX Compact Heat Exchangers
zhlédnutí 395Před 10 měsíci
ATS picoHEX™ heat exchangers add high performance cooling to small form factor applications where traditional size exchangers will not fit. Their compact design is built on the ATS family of UltraCool CPU coolers, and their cooling properties are consistent with ATS’ wide line of exchangers. picoHEX™ heat exchangers can be used for cooling CPUs, GPUs, FPGAs and other high power components. The ...
ATS Slant Fin Heat Sinks
zhlédnutí 325Před rokem
ATS offers a wide variety of ultra-performance extruded heat sinks with high aspect ratio for applications where there is adequate airflow to take optimum advantage from these designs. Slant heat sink solutions are available for component sizes 10x10mm to 60x60mm. Heat sink height ranges from 2-25mm with 1mm increments. The Slant Fin design offers additional surface area, therefore, higher perf...
ATS Straight Fin Heat Sinks
zhlédnutí 602Před rokem
ATS Straight Fin extruded aluminum heat sinks are available for component sizes 10x10mm to 60x60mm. Heat sink heights range from 2-25mm in 1mm increments. Their high aspect ratio means there is a greater density of fins in a given footprint than more common heat sinks. The Straight Fin design offers an excellent cooling solution for spatially constrained PCB layouts. The ratio of tall, straight...
ATS Pin Fin Heat Sinks
zhlédnutí 1,6KPřed rokem
ATS Pin Fin design offers an excellent cooling solution for spatially constrained PCB layouts when the direction of the airflow in the vicinity of the device is ambiguous. Learn more here - www.qats.com/eShop.aspx?productGroup=0&subGroup=2&q=Pin Fin&pid=1 www.qats.com Advanced Thermal Solutions, Inc. A leading-edge engineering and manufacturing company focused on the thermal management of elect...
ATS Stainless Steel Tubed Cold Plates
zhlédnutí 1,2KPřed rokem
ATS stainless steel tubed cold plates are a cost-effective thermal management solution for component cooling with a low to moderate heat load. Made from SS 304/316 and feature tubing secured between two plates, they are the right choice for cooling high-powered electronics, wind turbines, motor devices, automotive components, medical equipment, and any application where air cooling will not be ...
CLWT-067-PCIe™ - Closed Loop Wind Tunnel for PCIe Characterization
zhlédnutí 601Před 2 lety
The CLWT-067-PCIe™, is a unique closed loop wind tunnel for thermal characterization of components, boards and heat sinks. The unit is made of Aluminum, sheet metal and LEXAN™ and produces flows up to 1400 ft/min (7 m/s) and temperature up to 85°C. The CLWT-067-PCIe™ uses the proven technology of the CLWT-067 and adds a new m test section specially designed for the thermal testing and character...
ATS Vapor Chambers - Aluminum, Titanium & Copper
zhlédnutí 6KPřed 2 lety
The ATS family of aluminum vapor chambers are the largest and broadest set of off-the-shelf vapor chambers available today. From 25x25mm (1x1in) to 250x250mm (9.8x9.8in). Made in the USA, the vapor chambers are also available in Copper and Titanium. The Role of Vapor Chamber (VC) Substrate-level thermal transport whether metallic or synthetic diamond substrates that have been used for their sup...
What is a Vapor Chamber?
zhlédnutí 43KPřed 2 lety
A vapor chamber is a vacuum sealed heat spreader with a wick structure lining its inside walls. The wick is saturated with a working fluid and when heat is applied, the fluid at that location immediately vaporizes and the vapor rushes to fill the vacuum. When the vapor meets a cooler wall surface it condenses, releasing its latent heat. Learn more about how they function and their role in the t...
How to Choose the Right Heat Sink Attachment - ATS Webinar Series
zhlédnutí 1,9KPřed 2 lety
Choosing the right heat sink is part of deploying a good thermal management solution, the other part is the attachment method. Whether clip, push pin, z-clip, or other, the attachment has an important impact on how effective the thermal solution is. This webinar will cover these issues including attachments for rectangular packages increasingly used in SoC and SiP packages. A handy technical re...
superGRIP™ - Attach a Heat Sink in Seconds!
zhlédnutí 1,4KPřed 3 lety
superGRIP™ - Attach a Heat Sink in Seconds!
ATS fanSINK™ Heat Sink Family Overview
zhlédnutí 1,9KPřed 3 lety
ATS fanSINK™ Heat Sink Family Overview
ATS VOSTOK Ultra-Low Temperature Freezers
zhlédnutí 651Před 3 lety
ATS VOSTOK Ultra-Low Temperature Freezers
What is a Thermoelectric Cooler (TEC)?
zhlédnutí 275KPřed 4 lety
What is a Thermoelectric Cooler (TEC)?
Thermal Management Challenges in Medical Equipment - ATS Webinar Series
zhlédnutí 640Před 4 lety
Thermal Management Challenges in Medical Equipment - ATS Webinar Series
iFLOW-200™ - Cold Plate Characterization System
zhlédnutí 1,1KPřed 4 lety
iFLOW-200™ - Cold Plate Characterization System
How to Install ATS Ultra-Cool High-Performance Coolers
zhlédnutí 733Před 4 lety
How to Install ATS Ultra-Cool High-Performance Coolers
ATS Ultra-Cool Active and Passive Coolers for High-Powered Devices
zhlédnutí 1,6KPřed 4 lety
ATS Ultra-Cool Active and Passive Coolers for High-Powered Devices
IoT Thermal Solutions - M2M/Communications Infrastructure
zhlédnutí 200Před 5 lety
IoT Thermal Solutions - M2M/Communications Infrastructure
Selecting and Designing Liquid Cold Plates for Deployment in Electronic Systems - ATS Webinar Series
zhlédnutí 11KPřed 5 lety
Selecting and Designing Liquid Cold Plates for Deployment in Electronic Systems - ATS Webinar Series
Electronics Cooling: Thermal Management Approaches and Principles - ATS Webinar Series
zhlédnutí 13KPřed 5 lety
Electronics Cooling: Thermal Management Approaches and Principles - ATS Webinar Series
Thermal Management of Automotive Battery Packs - ATS Webinar
zhlédnutí 33KPřed 5 lety
Thermal Management of Automotive Battery Packs - ATS Webinar
I have got a project in my college, to build a heat pipe bender, it would be great if you could help me out, starting with what material you used to build it
Hello, when you say that one works only in one direction while the vapor chambers does it in both, does it mean that it acts like a heat diode ? Does it work also to transmit cold ?
I've done a few custom at-home DIY heat pipe heatsink projects. Now in the past I've been using Sn42Bi58 low melt temp solder but have discovered recently that having silver part in the solder will improve it's strength. What solder paste would you recommend for heat pipe heatsink soldering?
The Sn42Bi58 alloy is the most commonly used, because of the low melt temperature of around 138°C. You can use anything that has a similar melt temperature; anything under 150°C would probably work, so that might rule out the use of anything with silver in it. We do not recommend that heat pipes be relied upon for structural strength, and that includes the joints. If there is expected to be any kind of forces applied, then we recommend incorporating some kind of stiffening bracket into the assembly, so the heat pipes don’t take any load.
❤❤+1
Great introductory video. Thanks. Keep up the good work. Its much appreciated.
Thanks Aniket! Our new webinar series just started and you can register here if interested - www.qats.com/Training/Webinars
@@heatsinks Yes, Of course. But also upload them here for future reference.
You may find the archives of some value for reference, www.qats.com/Training/Webinar-Archive If there is some specific topic you have in mind, we may be able to point you in the right direction.
Do you have some liquid cooled water block for LEDs too
No we do not have liquid cooled water blocks. You may find our new POLARVrTX product provides the same performance but using air, see it here www.qats.com/Products/High-Capacity-Air-Cooling
Would it be more effective in dehumidifiers that are used in winters, when temperatures in the room drop to 5 deg C
Hard to undertand how. It cool
Hi @wazileiyjh, this article may help to explain more. It is a PDF www.qats.com/Qpedia-Article/Qpedia_Apr07_How_Thermoelectric_Coolers_Work
Do you think heat pipes could be 3d printed into complex shapes to achieve more efficient designs? So instead of the fins you'd have a mesh of heatpipes or something like that.
Maybe. The field of additive manufacturing is growing and new developments happen regularly. Perhaps 3D Printing a bent HP would be better than bending one? The wick is pretty fragile so that would might be quite a challenge with today's technology.
How to select heat sink for different modules?? Like how you will know the thermal conductivity and dimensions of heat sink
Hi - Your best bet is our free training on how to choose a heat sink, you may see it for free here vimeopro.com/user9706503/ats-webinar-series-air-cooling-heat-sink-design-and-selection
You spelled rigidity, 'ridigity'.
So what ????? 🙄
Thats cooler
Great Video
Thanks!
How many watts?
@AutodidactEngineer can you please clarify your question for us? How many watts does it cool or how many watts does the blower use?
@@heatsinks Please forgive my earlier self, yes the cooling capacity is what I asked for and would installing a thicker blower fan improve the cooling and noise even further?
May i know how much power can it handle to dissipate heat? for example a power source of 800W-1000W of power? and can maintain Junction temp below 100c? generally liquid cooling systems are very capable of handling Power range from 1000W-1500W
Hi @ShahulHameed-re2nq ~ Yes you may know the power these new products can handle: If: Tambient = 20 C Tj = 125 C ATS-3012-----13 KW ATS-3013------6.2 KW ATS-3014------3.9 KW --------------------------- If: Tambient = 20 C Tj = 85 C ATS-3012-----8.1 KW ATS-3013------3.8 KW ATS-3014------2.4 KW
What maximum and minimum temperature can this achieve? Would it be useful in a car cup holder to keep your drink hot or cold?
been playing with this one at work, it can easily reach <10°C depending on the ambience temperature
How does this clip attaches to the board?
Both maxiGRIP and superGRIP have wedges on the inner side of the clip that hook onto the bottom of the component they're attaching to. Here is an additional video that shows how that works - czcams.com/video/hKO_lnOXccQ/video.htmlsi=uBdsYH4kYSkKizVj
Great info!
Thanks for watching!
Can you please tell me where it is attached ? ( Component name)?
Hi @dineshkrrish8587 superGRIP attaches to the BGA package of the semiconductor.
@dineshkrrish8587 this video helps clarify where the heat sink frame attaches to the BGA czcams.com/video/hKO_lnOXccQ/video.html
can I use a banana plug connector at the other ends?
2023-11-07 ... again, an absolutely excellent presentation ... well done ...
Thanks @douglascoggeshall2490 we're glad you enjoyed it!
So what about X
Thanks. I bought some thermal tape off Amazon to get a heat sync onto some ICs for a GPU. I had never worked with thermal tape before and I debated going with an epoxy adhesive but then I decided to go with what the OEM used. The strange thing is that they didn't use any screws to mount the fins to the PCB. There's open copper and holes on the PCB and sync but for some reason, they went with just the thermal adhesive tape. I'm into a NVidia GE Force 760 ti OEM and I was surprised to see such a low standard manufacturing practice. My only question is should heat be applied to the surfaces? Because NVidia used ONLY thermal tape, when I went to remount the shroud, the heat sync fell out of position and when I first went to remove the shroud the heat sync literally just fell off. Scary, right? I may post a short video for those that are curious. ✌🏻
This products looks cheap, if you notice the deformed tube with the first bend and then he covers the deformity with his fingers in the second bend, the price they are asking for this thing its not worth it
Thanks for stopping by and commenting @raymondbennett948, we appreciate your taking the time to do that. As for your comment about the tool, the tube wasn't deformed so we are surprised by your comment. The tool works well to provide a precise bend vis-a-vis other heat pipe benders for this kind of heat pipe. There are of course less expensive benders, and engineers should try what works for them in their lab budget. We'd be happy to talk further with you about your insights into our tool, feel free to email us at ats-hq@qats.com or drop your comment here 👍
FWIW the kink in the cable is from when he slides it out as the bend happens around his finger rather than trying to push it straight out from the bottom. The worse part is this response in which they try and gaslight you into not believing your own eyes of the obvious kink in the heat pipe.
I've seen "Introducing Loop LiquidCool Technology"... where they use "tesla valve," to circulate the air around a chamber. This will be great to have a cooler in one dedicated spot, while the whole device is cooled. Is that something you guys feel is a good idea to do also?
What if you soldered the wires to each other and applied heat to the 'hot side,' would the 'cold side' become cooler? I just want to apply heat and get cold, I dont care about electricity. Thanks
Same idea. Depending on the metals it'll just change the temperature differential. This isn't a good idea though since it can heat or cool too much and carry over to the other side; therefore losing efficiency. At this point you'll need a heat sink for the hot or cold side in case one side gets too hot or coId. Best to arrange the metals so that they hit the tempurature you need most efficiently.
Tl;dr edition: The part uses direct current (dc), to make one ceramic plate suck heat from the other ceramic plate
erm..... what IS the critical temperature? for standard (i guess) 6 mm water type (i assume...)? sort of wanna make a chimney water heater, solder some into a copper pipe and sleeve it in a larger pipe... sorta like an inside out hedgehog... bought a bunch of compression fitting with the idea its possibly better to do it that way. hard solder/braze the fittings in and just screw down onto the pipes. i may want to change them for longer ones. got 40mm shorties... shorter than i expected! havent found much on heating the things for soldering... then again, when i think about it... theyre under vacuum. theyre going to have to get pretty hot before they get to a decent pressure, and copper is still good for pressure up til...400C-ish i would assume them to get some oxide colour change well before they explode!
Can this be used in the automotive sector to replace the HVAC system within a vehicle?
It would not be efficient I don't think
Thank you for your introduction of wonderful prdoucts. How can I contact the sales director for business? Your comment would be much appreciated.
Thank you for stopping by our channel @zzahngtrade7139 and leaving a comment. We appreciate that! For sales inquiries you can contact us at ats-hq@qats.com
so the entire heat remains constant inside the system? how could it be possible? or is there new make up hot fluid introduced to the system?
What does N and P indicate? Are those chemical symbols?
Hi Jack, the N and P indicate types of semiconductors. A typical thermoelectric module is manufactured using two thin ceramic wafers with a series of N and P doped bismuth-telluride semiconductor material sandwiched between them. The N type material has excess electrons, while the P type material has a deficit of electrons. One N and one P make up a couple.
@@heatsinks Does N represent negative and P, positive? Are there non rare earth elements which could be used?
This was a goldmine of information. I’m an electronics engineer and I’m looking to use a heat pipe for an industrial product, and this was a fantastic primer. Thank you!
Glad it was helpful!
Amazing video. Really good job Greg!!
Thanks for watching
Isme hi cepecity wala peltier module konsa aata he 24volt dc 50 amp
I came across one from 1965.
Not worth a patent
Thanks for visiting our channel @tarunarya1780 and leaving your commentary on our heat sink and the technology it uses. Your comment "Not worth a patent" is very interesting. Do you have some empirical data you can share with us? Or maybe you have used our product and found them not up to the requirements of your project? We would genuinely be interested in your qualified engineering perspective and happy to discuss your findings. You can drop your info here on the channel or email us at ats-hq@qats.com
Firstly, to be clear I have not bought or tested your products and am not saying that they are not good, or what you say they are.I am also not saying it is not good to have spec'd components to ensure that it will work in your use case. I do not think that heat sinks such as maxiflow are that innovative that it should deserve a patent. I think that it is an obvious design and not that hard to test iterative designs. Heat sinks will need to vary according how much power you wish to dissipate, how long it will be on, and your cooling solution. Other than that it is about maximising heat transfer to your "DUMP/Buffer" medium e.g. air and this will be about surface area with your "DUMP/buffer" medium. Having thin versus thick films depends of the balance of conductivity/heat capacity and use case(power and intended duration of use)/cooling solution. Splaying out fins is not innovative or hard to test. Copper will conduct away the heat faster.@@heatsinks I must have been having a bad day to make the comment in such a brief way, but the patent system is in general I feel very abused with minor obvious things getting approval, and stiffling development.
@@tarunarya1780 Thank you for your thoughtful reply @tarunarya1780 The U.S. patent system does allow minor variations to be patented and in some cases that can be problematic and can stifle innovation, we agree with you on that. Regarding maxiFLOW, its a different story. Its not just splayed fin array, there is engineering on the middle fins that acts somewhat like a duct to direct airflow. We had two of our engineer and one of our physicist working on that. Both Phillips and Northeastern University tested maxiFLOW and found it to indeed drive air down to the base of the heat sink, which improved thermal performance 20%. The speaker references those studies from about 2:20-3:05. If you have the time, and would like to, we'd invite you to checkout our video "maxiFLOW Heat Sink Technology Video" at about the 1:34 to 2:32 section where we talk about the work both Northeastern University and Phillips did to verify our tech. Here is a link to that CZcams video that starts at 1:34 czcams.com/video/qn84QO7gMIA/video.htmlsi=VHxnscY4VyLYxPBo&t=94 (sorry about any ads, that is something CZcams does automatically). Thank you very much again for leaving a comment.
Thanks for replying. Your video makes 2 claims - maximun thermal performance for the volume it occupies (~0.11) and highest performance for base area(somewhere), and mentions its affects on adjacent components. If the fins were vertical (whether folded or not) they would naturally form a barrier to airflow from the side.By splaying the fins out, you are "borrowing cooling air flow from adjacent components" and by reducing resistance as the percentage sideways profile occupied by metal will be less. What is clear is that this for items without a fan mounted on top of the item but a sideways fan, such as a large fan blowing air into the case. In your response you said it drives air to the base. I cannot see why you are saying that for the side mounted fan which is the case where it reduces resistance basically because it is borrowing adjacent boards air space for the same number of fins. If the fan is mounted vertically above, air will be naturally funneled to the base of the splayed fins as in your graphics card picture. I am really sorry, but there is nothing that makes me me think that's a surprise or really clever, just that it has been tested and given a patent. I appreciate you had skilled people working on it, but it seems really obvious to me. With your designs the angle of overhang means you have almost twice the airspace vs the area of the base. czcams.com/video/qn84QO7gMIA/video.html I looked at your video because I had wanted to make a remote controlled lawn mower, and thought the controllers were expensive. Thought I'd learn re electronics/motor drivers/controllers and was looking for a cooling solution. @@heatsinks
🙂 🧣
So, from processor heat spreader there's 400w/m2k copper to thermal paste 4-15w/m2k or 76w/m2k for liquid metal, than it transfers to again, aluminum or copper ,200-400w/m2k with a surface and wick that transfer heat to water that is 1w/m2k on all that wick surface of 200-400w/m2k that is linked to the real cooling surface of aluminum fins, not the transfer from processor to the fins, bit the real cooling surface that is 200w/m2k of aluminum fins surface. So even if there's 1000 000w/m2k of transfer of temperature ,what is the surface that is cooled by fans and how well it performs better by weight and by volume of a heatsink with heat pipes? %?
you didnt explain anything really... sheesh...
Thanks for stopping by our channel Locry and for taking the time to leave a comment. I'm not sure what your comment means. Peltier Coolers (TEC) are pretty simple. To that end, I think we've provided a basic understanding of them in our video. However, as an engineer, perhaps you were looking for more application oriented explanation? As engineers we understand that and so here is a white paper that explains the process to choose a TEC. The link goes to a PDF, and the PDF is free and there is no requirement for an email registration: www.qats.com/Qpedia-Article/Qpedia_Sep12_TEC_Selection_in_Thermal_Management
So where can I get that kind of welder?
Hi The SegaHolic - Thank you for stopping by our CZcams Channel. There are two places you can get this kind of welder, there may be others but these two are ones we've used: (1) DDC Corporation sells their thermocouple welders directly. www.dcccorporation.com/index.html (2) Omega Engineering also offers a couple of models. www.omega.com/en-us/accessories/tools/c/welders?view=list
what is the feasibility of using them to produce energy from excess heat? Ie a hot solar panel
What if one wishes to glue the heatsinks to a cover using a thermal glue? Do you advise this, and do you have a glue suggestion?
Hi John - Thanks for your question. It would depend on the application. You could epoxy the heat sink to the cover, though I'm not sure how well that will work if the cover is not in direct contact with the hot device(s). It may not help much. Another alternative is a heatsink enclosure. As the name implies, the enclosure itself acts as the heat sink. There's a very good example of one with cutouts here www.takachi-enclosure.com/products/RPH We also have an article on this approach when using these kinds of cases for edge computing www.qats.com/cms/2020/01/14/edge-computing-and-thermal-management/ As for epoxy types, we tend to use products from Parker-Chomerics, ph.parker.com/us/en/thermal-interface-materials?#facet:409927646082227572669112111120121&productBeginIndex:0&facetLimit:&orderBy:&pageView:list&minPrice:&maxPrice:&pageSize:&loadProductsList:true& Here is the shortened version of the Parker URL that I posted above, this may work beter: tinyurl.com/2we9dtc5
@@heatsinks good links all! I'm 'thinking' of making my big workstation art-building computer into a Steampunk renegade. Part of that is the idea of taking the top of the GPU cover, paining it a copper color and then gluing extravagant heatsinks with lots of thin fins and copper tubes to the GPU cover with a thermal glue such as the epoxies in the page you mentioned. There are thermal pads under the cover and the cover dissipates some heat, but good heatsinks over that spot would really ramp it up and give that 'Mad Scientist' look I am aiming for. I think some heat pipes running from the hot spot to the ends would be good also, but unnecessary really... but it is a 3090, and the memories get a bit warm, but not overly hot due to good airflow and lots of Gel pads. In fact, I suspect there may be a good market for cooling 3090 backplates with all the mining rigs getting sold now.
Is the fluids will finish some day??
No, the vapor chamber is sealed and the fluid permanently enclosed.
How can I trust this age old wisdom? Where is the rumors? The Wive's Tales? The THEORY CRAFTING! WHERE IS THE MARKETING TRICKS? IT CAN'T BE THIS SIMPLE AND I WOULD KNOW. IM A PC TEK! NOTHING EVER WORKS RIGHT! I WAKE UP IN A COLD SWEAR MULTIPLE TIMES A NIGHT AND I'M TRYING TO FIGURE OUT THE PROBLEM. WHAT EVEN IS THE PROBLEM?
Thanks now I know how to use that ☺️
What does thermal grease look and feel like if I just let them dry without pushing on them? For context, I’m looking for stuff to put inside my keycaps to make them heavier and sound thocky.
We're not sure about your application where you "put inside my keycaps to make them heavier and sound thocky". But in thermal management, pushing the heat sink down applies pressure which would enhance the thermal transfer from the hot surface it is being attached to.
Convection never happens in solids. I believe your arrow of convection and radiation should have pointed to the gaps between the walls of heat sink.
I love this person’s voice so much. Serious I would love to hear him explain anything.
6:41 - flush
Why not create a motherboard out of one of these?
HI @TNJedeye thank you for leaving your comment. Your suggestion might be very challenging. Generally, semiconductors need to be connected to one another via a trace, which is often copper. That would be challenging to etch into a cold plate, then securely apply all the semiconductors to the PCB/Cold Plate. We think someone might be able to do it but it would be very costly and clearly a very very specialized approach. The current liquid cooling approaches available today and planned by researchers for the future would probably be more cost effective.