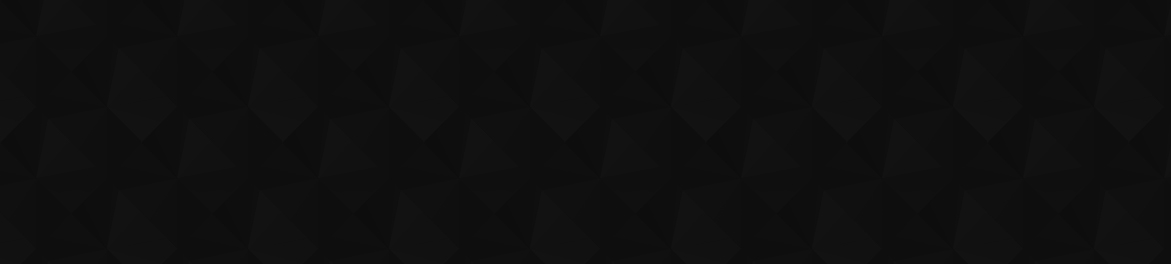
- 27
- 405 494
Meccano Kinematics
Netherlands
Registrace 8. 11. 2011
This channel is about modular building systems in tablescale format. In the 20th century more than 1300 of such modular systems saw the daylight, with different succes. Two of the most succesfull systems are described in this channel: Meccano and the more sophisticated FAC system.
Receiving my first Meccano kit at age 7, I became a lifetime enthousiast until present, but only developed more serious projects starting from the late 90's. At the beginning of this millennium I fell in love with another modular system, the socalled FAC system. The FAC system is in my opinion the most sophisticated construction system the industry has ever developed for tablescale prototyping.
Receiving my first Meccano kit at age 7, I became a lifetime enthousiast until present, but only developed more serious projects starting from the late 90's. At the beginning of this millennium I fell in love with another modular system, the socalled FAC system. The FAC system is in my opinion the most sophisticated construction system the industry has ever developed for tablescale prototyping.
Meccano Orthocyclic Coil Winding Machine
This Meccano coil winding machine has been designed and constructed by Gjalt van Slooten (1927-1992). Gjalt van Slooten lived in Drachtstercompagnie and was a well known member of the Meccano Guild Netherlands (MGN). The prototyping of the machine started in 1985 and took 2 years to finish. A Virtualmec file can be downloaded via virtualmec.com
Orthocyclic winding is a method for obtaining coils whose turns are stacked in the most compact fashion possible. Such coils have certain particularly good properties including good heat conduction, even distribution of electric field strenghts and the highest possible space factor.
The Meccano orthocyclic coil winding machine in the vision of Gjalt van Slooten is capable of making such coils. It's not perfect, partly due to a wrongly attached copperwire, but the result is quite impressive. The model has entirely been made with Meccano except for the motor, magnets and small analog electronics. These are all available online.
More info about the orthocyclic coil winding machine can soon be found on my website meccanokinematics.net
Orthocyclic winding is a method for obtaining coils whose turns are stacked in the most compact fashion possible. Such coils have certain particularly good properties including good heat conduction, even distribution of electric field strenghts and the highest possible space factor.
The Meccano orthocyclic coil winding machine in the vision of Gjalt van Slooten is capable of making such coils. It's not perfect, partly due to a wrongly attached copperwire, but the result is quite impressive. The model has entirely been made with Meccano except for the motor, magnets and small analog electronics. These are all available online.
More info about the orthocyclic coil winding machine can soon be found on my website meccanokinematics.net
zhlédnutí: 2 172
Video
Balancing the Mars orbital system
zhlédnutí 986Před 5 měsíci
Just a small note about balancing the moonarms of the Mars orbital system. During the making of the afore mentioned system I noticed some unwanted wobbling effect of the Mars arm due to an unbalance of the moonarms. To eliminate this effect I balanced each moonarm in a way, that the gravitational middlepoint is exactly centered. The final model of this Mars orbital system has been incorporated ...
Rubik cube solving machine: a tribute to Ernő Rubik
zhlédnutí 456Před rokem
Back in September 2016 I demonstrated my Meccano Rubik cube solver (also called Rubik's Shrine) to a gentleman who was a guest in one of my Airbnb accommodations. The difference between this vid and the original vid is, that the ratio of the drive to rotate the satellite of the gripper has been reduced from 1:5 to 1:2. With this modification we could optimize the speed. NEMA 14 stepper motors w...
Philips Variable Building System (VBS)
zhlédnutí 1,3KPřed rokem
I couldn't find anything on CZcams about the Philips Variable Building System, so I decided to make this video about the afore mentioned system. In 1970 Philips started with the development of a modular system on behalf of the production mechanisation. In the early 70's the system was called Building System and by 1978 the system had grown into it's full potential and was renamed into Philips V...
Mechanical four planet orrery, partly 3D printed
zhlédnutí 9KPřed rokem
Over the years several satellites and probes have been sent to the planet Mars. The Mars 2020 mission by NASA was a new milestone by sending the Perseverance Rover, which will search for signs of ancient microbial life. Strapped to the rover’s belly for the journey to Mars, a helicopter called Ingenuity, has achieved a “Wright Brothers moment “ by testing the first powered flight on the Red Pla...
1:365 ratio in Meccano
zhlédnutí 1,7KPřed 3 lety
A 1:365 ratio can be used in astronomical clocks as the ratio stands for 1 day : 1 year. Bert Love wrote an article in the februari 1970 Meccano Magazine about the usage of the 73t sprocket in combination with a fork piece to achieve a ratio of 1:73. In combination with a 19t/95t gearpair a 1:365 ratio could be achieved. Recently I came across another clever approach by Ariel Verlatsky, based o...
Meccano Mars orrery with Phobos and Deimos
zhlédnutí 2,1KPřed 3 lety
This is a Mars orrery made from Meccano parts and a few 3D printed parts. The geartrain is after a design by Michael Whiting. However, I changed a couple of idlers from the original design to make the whole geartrain fit into a compact setting. This doesn't effect the orbital system as the idlers take no part in the equation. Further I have made the framework as compact as possible, because thi...
Reaming of the inner diameter of a miniature ball bearing
zhlédnutí 1,3KPřed 3 lety
For one of my Meccano projects I needed the use of ball bearings. The diameter of Meccano axle rods is 0.160” or 4.06 mm so a 4-10-4 ball bearing doesn't fit. For this reason I have designed a device to easily ream the inner diameter of a ball bearing. As for the cutting and reaming I have bought a couple of miniature cutting tools. Please note, that I have no relationship with the companies be...
Trix Metal vertical steam plant after a Doll steamplant 359/6
zhlédnutí 563Před 4 lety
This vertical steamplant is inspired by A Doll & Co vertical steam plant nr 359/6. This was the largest DC Vertical steamplant ever made. I have built this model around 2003. More info here: wiswin.nl/Die Trix Metall Dampfmaschine.htm
Lathe adjustable carriage stop
zhlédnutí 3,6KPřed 4 lety
This vid shows an adjustable carriage stop for my Wabeco D4000 lathe. As far as I am concerned a carriage stop for this lathe should have been a standard feature. The device to adjust the rod and the stop device have been made with FAC system parts. FAC system is still for sale. This device is very usefull when making threads. The rotational travel of the switch lever to (dis)engage the lead sc...
Meccano planet geardrive ratio 1 to 8.5
zhlédnutí 4,6KPřed 4 lety
The idea of a planetary geardrive is from an original Heidelberg platen press, but I have seen similar geardrives in Meccano using combinations of 56 and 57 teeth gears. The idea of this type of planetary gearing has probably been published in the well known Meccano Magazine, but I didn't bother to look for it. This vid shows a very compact gear ratio 1:8.5. I didn't have a 20t pinion, otherwis...
Meccano Heidelberg Platen Press
zhlédnutí 14KPřed 4 lety
This Meccano Heidelberg Platen Press is in it's final stadium. The entire machine is driven by one (brushless) motor only. The pump to transport the paper from the papertable into the platen is made from simple materials, but it works great. Problem (and part of the current study) to solve is, that the paper sticks together by itself by nature, so sometimes more than 1 sheet is being transporte...
Meccano Peacock Clock
zhlédnutí 1,7KPřed 6 lety
This is the final version of the Meccano Peacock Clock. More info can be found at meccanokinematics.net. The striking mechanism is of a rack snail type, commonly used in mechanical clocks. The Meccano equivalent is entirely based on gears. An extensive article about this clock can be found in Robin Johnson's magnificient Meccano magazine called Qonstructor Quarterly nr. 120, June 2018.
Meccano Rubik's Shrine
zhlédnutí 52KPřed 8 lety
This cube solver has been assembled with parts from the well known Meccano system. More info at meccanokinematics.net/meccano-rubiks-shrine/ The model is a tribute to Ernő Rubik, inventor of the cube. The appearance of the model with the cube as an iconographical centrepiece looks like a shrine, hence the models name: Rubik's Shrine. This machine is derived from the FAC solver (see the channel ...
Arduino accelstepper vs standard code library
zhlédnutí 7KPřed 8 lety
Arduino accelstepper vs standard code library
Part of the mechanism of a Meccano Cyclograph
zhlédnutí 2,1KPřed 9 lety
Part of the mechanism of a Meccano Cyclograph
Clock Striking Mechanism (part 1 of 2)
zhlédnutí 6KPřed 10 lety
Clock Striking Mechanism (part 1 of 2)
Clock Striking Mechanism (Part 2 of 2)
zhlédnutí 5KPřed 10 lety
Clock Striking Mechanism (Part 2 of 2)
fully automated mechanical spirograph (Super Meccanograph)
zhlédnutí 8KPřed 10 lety
fully automated mechanical spirograph (Super Meccanograph)
FAC system orthocyclic coilwinding machine
zhlédnutí 3,7KPřed 12 lety
FAC system orthocyclic coilwinding machine
acceleration and deceleration mechanism
zhlédnutí 5KPřed 12 lety
acceleration and deceleration mechanism
Woww so elegant
Mesmerising indeed … 😊 I guess the Sun should have been really larger ? 😬
That's correct. If one takes the planet as a reference, the sun would be approx 5.5m in diameter. Further, the Mars moons would be smaller than the diameter of the pin they are mounted on.
@@Meccanokinematics yes. 1.2 million km vs 12000 ! 😀👍🏻 Whatever, you sir built a true masterpiece !
Oooh this is fast
This is pure mechanical genius
I was impressed by this machine as well. A few simple modifications could be made to improve it's performance.
@@Meccanokinematics Yes. The fact that it works today, 39 years later, is a testament to A) quality design and construction (despite the limitations of Meccano) and B) there are people who still appreciate its value. Very few one-off creations stand the test of time. I hope this ends up in a museum some day and is valued for generations, along with the memory of its creator.
after a bit of hair tearing out i got mine to work love it!
That's great. Did you have a look at my website meccanokinematics.net/meccano/models/19-special-meccano-gear-ratios/#designing-an-136525-ratio as well to see how you can add an extra differential to define a leap year?
@@Meccanokinematics a guy up north here in new zealand is making meccano gears an yes a 76tooth!! Makes almost all sizes too
@@grantwells2470 Good to know. I received a pricelist from him. Very reasonable prices.
That has to be the best use of a Meccano model I've ever seen! Very cool.
That is a very nice unit. I'm tempted to make one but its obviously a lot of work and I really only have one coil type I need to do and only a few required. Its out of a Smiths synchronous clock motor and it has 15,750 turns of 0.06mm wire, this unit would be perfect for the job so I might try a cut down version without the versatility of yours. Thank you for posting
This is actually a threading stop as well as carriage stop.
That's correct, I use it for both operations.
I worked on these in the late 1970s, I would love to buy one of these.
The Meccano model is probably more expensive than a well used original...
Фантастика!
I would like to build this, can I get the 3D parts from you or can I use all meccano parts?
I will send a PM to you.
👏👏👏👏👏👏👏
I want to build your small orrary can I build it with standard Meccano gears or do I need your nylon ones and the bearings?
If you mean the 3 planet orrery, that one can be built with standard Meccano gears, but you need also a 20t, 11t , 12 t and 13 pinion. Do you need a Virtualmec drawing? The orrery in this vid is a Mars orrery only. That one needs a few non standard parts, like the 65t gears. I did print the 65t gears and the 20t pinions as I didn't have them. The 65t gear is pretty expensive as well... The bearings are optional, but the system works much better with these bearings.
awsume an how many teeth does the largest gear have?
133
Just tried recreating the differential version in Blender using drivers, and it’s twice what it should be - total ratio start to finish is 1:730 instead of 1:365. I’ve rechecked all of the drivers, and nothing seems off from the example
I think your calculations don't take the differential in consideration.
@@Meccanokinematics I made sure the differential works properly before linking it to the other gears, though I’ll have to double check that everything’s spinning in the right direction Edit: seems to be linked properly, so I may have to halve one of the ratios in the train
@@Meccanokinematicschanging the ratio between the red and green gears to 1:2.5 seems to have worked
@artificer26 using a differential gearing you create 2 outputs. In the equation (token from a 50's handbook about gearing) you must half each geartrain. At the green output I get 73 and this number is multiplied by 5 to get 365. On my website I added an extra differential to get a 365,25 ratio. You can also find the calculations there.
@@Meccanokinematics may have figured out the actual issue here - the red gear is the input on my model. Drivers in Blender only work in one direction, so between two gears only one can influence the other at a time. The differential is set up so that the blue shaft is just the averaged value of the two crown gears, though I’m not sure how I’d reverse that so the crown gears are the outputs
All that construction, and it can't even print!
Well, that is not entirely true. Take a look at following weblink: meccanokinematics.net/meccano/models/16-meccano-heidelberg-platen-press/
what cube model is that?
This is a standard speedcube.
hmmm, yes sovling rubix cube, that's important... but is there anything useful we can solve?
Amazing
That is very very cool my son says
Thanks. This was a very challenging, but awesome project. We have made 2 other solvers: czcams.com/video/C9rCBjLGxJs/video.html and here: meccanokinematics.net/new-rubik-solver/
Fantastic 😂
Bravo
Superbe 👍
There's too many gears!!
I am using tmc 2208 drivers now. The machine is absolutely silent. Speed of the geartrain is not very fast either.
WOW
Great video shame about the audio
EXcellent! I wish you hade made a longer video!
With what type of 3d printer did you print the planets and moons?
See the description. The planets and moons were bought from third parties. The Mars moons have been 3D printed by myself.
@@Meccanokinematics oh ok also what type of printer and brand did you use to make the martian moons
@@four4eight Cubicon style. I used ABS filament.
@@Meccanokinematics did you paint it?
@Four4Eight Yes and the colours are based on pictures found on internet.
Very beautiful in the way that it moves
We showed the Rubiks Shrine at Skegex 2016, but later that year we were able to speed up the machine. In 2022 I substituted the DRV 8825 drivers by tmc silent stepperdrivers. The stepper motors are now completely silent.
@@Meccanokinematics I do remember your previous video. It does seem a bit smoother and quieter. Very nice work :-)
@@Meccanokinematics Some of our greatest creations have the potential to be greater I suppose!
@Meccano Man The machine in this video is faster, but the tmc drivers were only a recent addition from 2022 and this latest configuration has not been filmed yet.
🇫🇷 Bonjour, Magnifique tant la réalisation en Meccano que la vidéo, sur Haydn de surcroît ! Les images sont d’une netteté étourdissante. Ce modèle est vraiment très bien fait et fait plaisir, simplement à le regarder évoluer. Bravo. Cordialement. M.
The latest improvement to this machine is substituting the old drivers by tmc 2226 silent drivers. The result is a very silent running machine without any vibrations.
@@Meccanokinematics 🇫🇷 Bonsoir. Merci pour ces précisions. Bien cordialement. M.
It's a very interesting system. Thanks for the video. I've been looking for it but seems to be difficult to find.
Unfortunately you cannot buy it anymore. I myself have only parts for the 6-10-15mm diameter range.
@@Meccanokinematics Yes, I know it's not any more being made. I have been looking for it in the used market but not much luck so far.
In the US at least most of these building systems have been replaced by the use of 80/20 extruded aluminum and Creform systems. They work for simple fixtures and the like, but they don't have the nice mechanisms like the Philips system you've shown here. Thanks for sharing!
The systems you mention will work as well. I saw various impressive 80/20 constructions . The only disadvantage with the 80/20 system is, that once you have made a setup and you want to add a clamp between 2 other clamps, you need to loosen one of these 2 clamps first, otherwise you cannot insert the sleeve. For a prototyping environment this could be an anoying issue.
@@Meccanokinematics with the wide availability of 3D printers and CNC machines, creating a bracket to insert with separable clamp elements wouldn't be too hard, and then theres the drop in t-nuts which address this limitation. I love the VBC implementation for it's time!
@@nerddub Agreed, although not everybody has a CNC at home. Initially I created a 3D printed inbetween clamp, but later I realized, that using an original clamp would work as well by adding a small 3D printed insert to fill the 2.5mm gap between a 15 and 10mm diameter.
@@Meccanokinematics Absolutely that's where I find 3D printing to be most useful, as a medium between off the shelf hardware and my design constaints.
Looks like the Swedish FAC-system
Indeed. Part of the demo model has been built with FAC system. I love the FAC system. Just have a look at my website www.meccanokinematics.net
Well Ive never seen that before, you are very lucky to get that, its rather like professional Meccano
Initially it was only used by Philips themselves, but soon became available for other industries and for universities. It has been quite popular in the 70's and 80's. As far as I know the system was only for sale for other companies and not sold to privates.
@@Meccanokinematics Such a shame Meccano didnt go down this direction, imagine the things that could be built with meccano with these options and accuracy.
Also kinda like scaffolding, just a tad smaller
Oh Wilbert, fantastisch dit !
Ik heb nog steeds voldoende over om een translatie tafel te maken, dus als je interesse hebt, kom vooral langs.
What a marvel
Is that a 95 tooth gear on the output?
That's correct.
@@Meccanokinematics cool
Small
I feel smol
Heel mooi model met smaakvolle muziek.
en wat vind je van deze: czcams.com/video/7xeS8_ZBKDU/video.html
Is the gear pair on the left at the output 1:1? For those new to this, could you explain how the 19 and 17 tooth gear pair lead to the 1:8.5 ratio?
If you mean the gearpair on the topleft, Than yes. This gearpair was only introduced to maintain the same rotational direction of the output shaft compared to the input shaft. So for every full rotation of the input shaft, the sungear (this is the geararm rotating around the input shaft) rotates one revolution as well, because the number of teeth of the pinion on the input shaft are the same as on the sungear. The left 19t pinion of this sungear engages with a 17t pinion. A full revolution of the sungear means a displacement of 19 teeth. The 17t gear is also displaced with 19 teeth, or 17 + 2. So after 17:2 = 8.5 rotations, the output shaft has made a full revolution whilst the input shaft has made 8.5 revolutions.
@@Meccanokinematics thanks -- so the 17 tooth gear rotates 19/17 rotations for each rotation of the input gear. Or 19 rotations for 17 of the input.. Correct? How does this lead to 2:17? Or am I wrong?
Remember that the sungear is rotating 1:1 compared to the input. So a full revolution of the sungear leads to a full revolution of the gear attached to the sungear as well. Whilst the left gearpair attached to the sungear differ with 2 teeth, the ratio is 2:17. Just study the vid and watch the threaded bolts attached to the input and output shaft.
@@Meccanokinematics I think I understand now -- When the 19-tooth sungear completes a revolution, it pushes the 17-tooth gear to move 2 teeth ahead since the teeth are on the same radius. (If it was a 19 tooth gear as well it would not move at all.). To complete a rotation of the output shaft takes 17/2 revolutions of the sungear i.e. 8.5 to 1.
@Atul Divekar That's indeed correct. It's interesting to mention, that I initially wanted to use a 20t pinion in stead of a 17t pinion. If using a 20t pinion I could have left the gearpair on the top left away to maintain the same rotary direction of the input and output shaft!
Incredibile, very good job. I own a Heidelberg Windmill and i recognoized any single movement!
Waoww that’s super smart ! ⚙️👍🏻
Beautiful. They used to call a similar machine, the windmill press. If you were lucky enough not to have your hand hit, you had a good day, lol. :) EDIT - I don't know if you figured out the double-sheet issue, but the real machines use thin metal strips that gently sit on the leading edge of the stack to help separate the sheets. There are also blowers that blow across the top of the stack to help with the results. Beautiful work regardless. Cheers.
🤤 p͎r͎o͎m͎o͎s͎m͎
Yet another masterpiece
Stellar!
Thsi is beautiful!
Very well done!
Thanks! Really helpful!