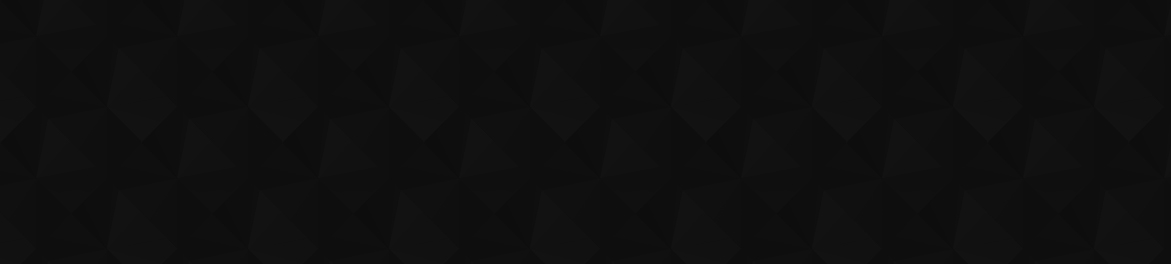
- 12
- 151 351
Engineer Bo
Registrace 1. 09. 2012
Finding the Best NEMA17 Stepper Motor: LDO Motors, STEPPERONLINE and more tested with a dynamometer
NEMA17 motors are ubiquitous, and sometimes they even look identical. How do we know which motors will perform the best, and is there even a best motor for every application?
In this video, we test five NEMA17 stepper motors with a dynamometer and examine their speed-torque curves to find which motor performs the best.
Components used (affiliate links):
LDO Motors 42STH48-2504AC - SPEEDY POWER (s.click.aliexpress.com/e/_DF685C7)
LDO Motors 42STH48-2804AC - SUPER POWER (s.click.aliexpress.com/e/_DEzcLhd)
STEPPERONLINE 17HE19-2004S (s.click.aliexpress.com/e/_DCFVJhl)
Usongshine 17HS8401 (s.click.aliexpress.com/e/_DeOzaT5)
JKONGMOTOR JK42HS48-1684-08AF (s.click.aliexpress.com/e/_DlQnGCB)
TMC2209 Stepper Motor Driver (s.click.aliexpress.com/e/_DlutPRv)
TB6600 Stepper Motor Driver (s.click.aliexpress.com/e/_De5W0JN)
TMC5160 Stepper Motor Driver (s.click.aliexpress.com/e/_DE19ASx)
KORAD Bench Power Supply (s.click.aliexpress.com/e/_DmDEXhH)
HX711 Load Cell Amplifier Module (s.click.aliexpress.com/e/_DD9QFPD)
Optical Encoder (s.click.aliexpress.com/e/_DevICZD)
Chapters:
00:00 Introduction
01:32 Specifications
02:56 What is Torque
04:21 Dynamometer
05:54 Data Processing
06:57 Results
10:41 TMC2209 at 24V
10:58 TB6600
12:42 24V, Finally
13:45 One Last Thing
14:53 Preliminary Conclusions
17:24 More to Come
In this video, we test five NEMA17 stepper motors with a dynamometer and examine their speed-torque curves to find which motor performs the best.
Components used (affiliate links):
LDO Motors 42STH48-2504AC - SPEEDY POWER (s.click.aliexpress.com/e/_DF685C7)
LDO Motors 42STH48-2804AC - SUPER POWER (s.click.aliexpress.com/e/_DEzcLhd)
STEPPERONLINE 17HE19-2004S (s.click.aliexpress.com/e/_DCFVJhl)
Usongshine 17HS8401 (s.click.aliexpress.com/e/_DeOzaT5)
JKONGMOTOR JK42HS48-1684-08AF (s.click.aliexpress.com/e/_DlQnGCB)
TMC2209 Stepper Motor Driver (s.click.aliexpress.com/e/_DlutPRv)
TB6600 Stepper Motor Driver (s.click.aliexpress.com/e/_De5W0JN)
TMC5160 Stepper Motor Driver (s.click.aliexpress.com/e/_DE19ASx)
KORAD Bench Power Supply (s.click.aliexpress.com/e/_DmDEXhH)
HX711 Load Cell Amplifier Module (s.click.aliexpress.com/e/_DD9QFPD)
Optical Encoder (s.click.aliexpress.com/e/_DevICZD)
Chapters:
00:00 Introduction
01:32 Specifications
02:56 What is Torque
04:21 Dynamometer
05:54 Data Processing
06:57 Results
10:41 TMC2209 at 24V
10:58 TB6600
12:42 24V, Finally
13:45 One Last Thing
14:53 Preliminary Conclusions
17:24 More to Come
zhlédnutí: 34 682
Video
Building My Ultimate LED Flashlight: Boost Driver Circuit Episode #2
zhlédnutí 923Před 3 měsíci
I'm on a quest to build my own custom flashlight, and my first step is to answer a bunch of questions I had about boost drivers. To do that, I've made myself a dev board. This is episode 2 in the series, picking up where we left off with explaining how the flashlight boost driver works, how it is designed, how component values are calculated, and more. Episode 1 can be found here: czcams.com/vi...
Building My Ultimate LED Flashlight: Boost Driver Circuit Episode #1
zhlédnutí 897Před 4 měsíci
I'm on a quest to build my own custom flashlight, and my first step is to answer a bunch of questions I had about boost drivers. To do that, I've made myself a dev board. This video series explains how the flashlight boost driver works, how it is designed, how component values are calculated, and more. Get $5 credit for PCBWay's services by using this link (for new users): pcbway.com/g/OkDAel T...
Regenerative braking broke my motion controller. Here’s how to protect yours (with schematics)
zhlédnutí 20KPřed 5 měsíci
Regenerative braking sounds like the futuristic technology that we all need, but it’s not all sunshine and rainbows. Incorrectly configured, regenerative braking can result in devastating voltage spikes that destroy expensive equipment such as motion controllers. In this video, we run a few experiments to demonstrate the effects of regenerative braking, and talk about a protection circuit that ...
MKS SERVO42C Closed-Loop Stepper: Tests vs Servo with Field-Oriented Control and TMC2209 Open-Loop
zhlédnutí 66KPřed 6 měsíci
The MKS SERVO42C closed-loop stepper system can be found at a reasonable price, but how does it stack up against open-loop steppers we know and love, and how does it perform compared against a servo system? In this video, we put all three motion systems to the test. We look at the power and thermal performance, and run stress tests to find the maximum accelerations and speeds in a linear motion...
DIY Nut & Crab Shell Cracker with 10x Mechanical Advantage
zhlédnutí 594Před 7 měsíci
A regular nutcracker’s measly 2x mechanical advantage just doesn’t cut it with the thick shells of mud crabs. In this video, we make a simple compound lever shell cracking tool that makes cracking shells effortless. Chapters: 00:00 Introduction 00:32 CAD 00:42 First cuts 01:44 Annealing and bending 02:39 Finishing touches 04:16 Assembly 04:49 Demonstration
Game-changing Microscope Polarisation Upgrade - With Free 3D Printable STL
zhlédnutí 2,4KPřed 9 měsíci
If you regularly use a microscope for electronics work, this is the perfect modification for you. Using a pair of polarisers, we can eliminate glare, revealing hard-to-see details like chip markings. Amazon Affiliate Links: K&F Concept 52mm Circular Polariser Filter: amzn.to/3u3j2Of Polarised Film Sheets (Adhesive): amzn.to/3HDA60i AliExpress Affiliate Links (remember to select the correct prod...
Fake USB Flash Drives: How to Test and “Fix” with f3fix
zhlédnutí 10KPřed 10 měsíci
Fake flash drives (USB, SD cards etc.) are aplenty. Find out how to check if the flash drive you bought is too good to be true. We'll use the f3probe tool to detect the actual usable capacity of the flash drive, then "fix" it with the f3fix tool. We'll touch on why it's security risk to plug untrusted USB devices into your computer. Finally, we'll talk about a few legitimate storage products to...
Foam Blaster Electronic Target: Teardown and Quiet Mod
zhlédnutí 200Před rokem
We bought this electronic auto-reset target toy for foam blasting, but found the sounds to be excessively loud. In this video, we perform a teardown and modification of the device to disconnect the speaker. Find out how the device detects when the targets have fallen, and how it resets the targets to the correct position. Chapters 0:00 Intro 0:41 Disassembly 1:30 Modification 3:04 How It Works ...
Print-in-Place Cuban Link Chain
zhlédnutí 6KPřed 2 lety
This Cuban link chain is printed in place, no supports or assembly required! cults3d.com/en/3d-model/fashion/print-in-place-cuban-link-chain
GTA VR for Vive: Alpha Gameplay Snippets
zhlédnutí 9KPřed 8 lety
Gameplay snippets of VR mod for GTA V using the HTC Vive. Gravity gun can be disabled.
Playing Pong with Smart Breadboard
zhlédnutí 1,7KPřed 8 lety
Playing Pong with my DIY smart breadboard. The smart breadboard is configured to drive the OLED display and uses the resistors as capacitive touch inputs, all without wires! The game logic and audio are also handled by the smart breadboard.
Great analysis! Love your dynamometer!! YES please microstepping vs torque! And I would love to see TMC5160 compared to an established closed loop stepper with optical encoder, e.g. Stepperonline CL57T driver.
Thank you! Microstepping vs torque is definitely a video I'll do.
Cool tests. I"m looking for steppers for random projects other than 3D printing so this is helpful
Glad it was helpful!
I tested serve42c vs standard stepped with TMC. I think: serv42c is stronger, and quickly than standard stepper. I don't really understand why the video shows that servo42 is slower. (setup is siliminar: microstep 16)
Did you change any of the servo42c settings? I left everything on default which might not have been the ideal configuration.
@@engineerbo Hi, all settings is default. But, i enable serial connection with 38kbaud.
That's interesting, I don't think the serial connection would have changed anything though. How did you compare the performance between the servo42c and the normal stepper?
This is a great video. I possess all of those motors and have played around with them not to the graphing extent that you have however. Speedy powers didn't last long for me because I'm dyslexic and I accidentally put the decimal point in the wrong area and fried both my speedy powers pretty much instantly. My superpowers however are very nice and they are connected to 5160 pro external Big tree Tech drivers . I was previously using the TV 6600 drivers and I experienced the same result
Thank you!
This is amazing, exactly what I needed! Bless you
Glad you found it useful!
honestly 32gbs for 5 bucks is pretty good
why r u testing 2209 at 12v? It can go up to 24v as well
I blew up the TMC2209s at 24V (mentioned in the video). It could be a problem with not having a capacitor near the drivers. This will be fixed for the next tests.
It’s a good dyno but the use of a padded brake and brake disc is a factor that can lead to bad numbers in the long run due to nature of wear. Maybe using centrifugal force and fixed weight would have less outside influences.
Thanks! The condition of the brake actually shouldn't matter at all, because I'm measuring the actual braking torque. For example, if the test was running, and I decided to oil the braking disc midway, this would cause the braking torque to decrease, and this change will be measured by the load cell. Oiling the disc would only mean the test would take longer, because the brake calliper would need to clamp harder to achieve the same braking torque.
@@engineerbo ok you’re compensating the loss of torque with time. Thanks for the explanation
Hello , thx for great video. I must say for the test purpose i bought 15TB flash drive for about 5 Euro. And as expected same as in your video shows 15,3T. Well your F3 software wasnt working as intended -shows me same error msg as was already mentioned in comments here (f3probe: read_all(): unexpected error code from read(2) = 121 : Remote I/O error) . But as i before tried full format and didnt finish (too slow to fully done) , just to get back to guick format - can be the reason for that error in my case. After that i did try this tool what i can recommend as its super fast and also in Windows can be used : ValiDrive. Where i got the right information : 2 dots from all in graphic view were green - valid. rest shows as red = no storage. in next result window i got information there are ~30GB storage. Next i get inside of the usb key - really simple done by get off aluminium cover and then i needed just push to lock (2 mm in size) and in same time pulling out usb3 part of the disk. Inside i found card in card reader. Card was made in korea, but nothing else was usefull from text there. I put it in card reader and format it (its shows 30GB already), so windows formating tool was enought for this task and becouse of real 30GB to format, now was time aprox. 1h to finish even slow full format. After that i moved card back to usb "key" (card reader) and buala - new 30GB card with good looking card reader in one for free to use ;p . I must say as it was bought from aliexpress and i did my tests fast enought, i reported fake usb and get my money back (seller didnt get money from aliexpress at all). Cheers
Good video, really hoped to see the nema17 motors i personally use in this test. I use the steppermotor 2,1 A, 0,65nm motor. Wouldve been the highest holding force in this test while being not the highest Amp. The serial number is 17HS24-2104S - i am super happy with these motors and i can just recommend them.
Thank you! The motor you specified has a longer body length (60mm vs 48mm), which wouldn't have been great for comparison in this video.
@@engineerbo will there be a Test with 60mm Body lenght? Would be excited to see it. Really liked your test setup. 👍
I have lots of different tests planned, but not one for 60mm motors (I don't have any!). But if there's a large enough demand for this test, I can arrange for it.
I'm confused why you didn't get any hybrid steppers on your lineup?! They put normal steppers to shame in pretty much every single category, except one - price. They're the ones in one piece aluminum round cases, instead of laminated steel sheet bodies. They are insanely powerful compared to a cheap laminated steel stepper
All these motors are hybrid stepper motors. Are you referring to something else?
@@engineerbo Hmm, I know them just as 'hybrid steppers'. They are just normal 4-wire steppers, but they are in round aluminum cans, I got a box of them in an auction years ago (they were buried in a pallet), and I've used them for various projects over the years. The first picture for google images "EHY21512" or "23HY4604" shows the TYPE of stepper I'm talking about. The cases are round aluminum cans, not laminated steel sheets
The dyno design is great, but running stepper drivers on a solderless breadboard is just asking for problems and likely the cause of your 24v failures. When you are switching relatively high currents at high speed you need low impedance supply rails with plenty of decoupling, something that a breadboard just cannot provide. Why not use an existing stepper driver board like the SKR?
It was the first build of the dyno, the breadboard certainly isn't the best. I'll be building a PCB to replace it for the next video. I needed custom functionality for the dyno that perhaps something like an SKR could do, but it seemed more straightforward to implement it myself.
Interesting results. Would be nice to run some resonance test for each of the motors. I have StepperOnline motors on several of my builds and they perform pretty well. In my Voron 0.2 build StepperOnline resonate less than LDO motors which results in better prints quality over all.
Thank you! That's an interesting suggestion. How did you test for resonance in your build?
@@engineerbo I think you could just add simple ADXL sensor to your rp2040 setup, place sensor on the motor itself and run loop changing motor frequency at the same time recording readings from the ADXL, at least I would start from there. On 3Dprinter setup it's much easier as Klipper helps to run such task semi-automatically.
My first guess would be that every motor has its own resonance frequency, and there wouldn't be "more" or "less" resonance, so I'm not sure how I'd design a test for this.
@@engineerbo I would assume a well-made and balanced motor should have fewer frequencies it resonates at. At the same time, I think the higher the vibration level and the wider the spectrum, the harder it is for the algorithm to mitigate those vibrations, and it will end up affecting the print quality. I'd probably make two tests: the first one to see the overall noise and the second to check how high the peaks are getting.
Very nice and detailed video but what makes me curious what about accuracy and repeatability of those motors or maybe it’s not determined by the motors it self I actually don’t know so please let me know/ us know . Keep it up 👍
Thank you! I've started planning to test for position accuracy, so there'll be a video of that in the future.
Would like to see the popular Wantai motors used in high-speed printers.
Simple way to select a "fast" stepper is to look at the inductance (often listed) as it's the thing that will, during running, limit the current rampup and thus also torque.
Nice video! Is it possible to test motor noise for VFA generation video? I am of the mind to use a motor with the least VFA and sacrifice torque for a smooth curve! Do they exist!?!
Thank you! There've been several comments talking about positional accuracy, so I'll look into make a video on this after my speed and torque series.
It’s unclear to me how the load cell is measuring the braking force. I would greatly appreciate if you could elaborate on that please. I love the dynamometer setup!
Thank you! The brake calliper is mounted onto an arm that pivots about the same axis as the disc, and the other end of the arm is attached to the load cell. This makes the measured force "downwards".
@@engineerbo Aah! That makes sense. Fantastic, thank you!
I found the "TB6600" (no such chip on them in the 1/32 microstep version, it's a TB67S109AFTG or similar) drivers to be really nice and reliable with the big heatsink, isolated inputs etc. Those tiny breakout boards can be a pain in the ass, they can get quite hot, can be really sensitive to noise and randomly die on you, just like this one.
Nice setup. It would be interesting to see the actual current waveforms of the different drivers. You have to keep in mind that when comparing smoothness of operation and noise, newer drivers are basically cheating because they don't really do steps anymore, they treat your step input more as a suggestion and generate a sort of sinusoidal waveform, trying to guess what you're doing and what you need.
I also blew up a few btt 2209 drivers on my 24v printer, one of the capacitors failed. i think it was c6 next to the "bottom" label. i soldered a through-hole 100nf in that place and the drivers worked again.
Yes there are three capacitors between VM and GND. The caps are rated to 50V though, so they have a better than surviving than the TMC2209 chip.
Let me make this very simple: if you have the right kind of motor driver and are doing field oriented control, all your tests are useless and meaningless and all of the motors will perform similarly. Source: I'm an actual electrical engineer who implements custom motor control systems. If you rely on purely open loop step-based control (like the TMC2209 or similar), then you are entirely at the mercy of winding inductance and resonance. Proper field oriented control with a position encoder (yes, even for hybrid stepper motors) will give you optimum results on any of those motors. Look at the SimpleFOC project for an excellent open source implementation of this. Note: this is NOT the same thing as "closed loop stepper drivers". Those still use a step based driver, not field oriented control.
This is really SOMETHING!
This was a great vid. So you recommend the high torque motors for perhaps the Z motors and the high rpm for the X and Y motors?
The entire flash memory sellers on AliExpress (there are literally hundreds) are selling these fake TF brand labeled cards, Lenovo, Sony, Xiaomi, Sansumg (yes, intentionally spelled this way), SanDian (fake SanDisk), if they are only a few dollars, then they are obviously fake, probably only 8 GB data storage, but faked with high capacity values. Now it's going to be fun fighting off the fakes and somehow shutting these sellers down, which is probably not going to happen, as they just close the store and give it new name, it's so nuts seeing this happening.
Yes! Fake drives are incredibly prevalent in some areas. The sellers have probably decided that non-savvy buyers would purchase a 2TB drive, and end up only using a couple GB.
Love it, finally somebody going deeper into steppers. I'm very deep into cheap servo motors - this territory might be even crazier! But, 14:22 your whole setup is flexing.. not good for reliability of data :(
Thank you! The bracket design is not ideal (I've designed it to make it easier to switch motors out for testing), but I don't think the torque readings will necessarily be unreliable. If the motor is mounted on a flexible, springy bracket, the bracket will flex/deflect depending on the torque applied by the motor. The higher the torque, the greater the deflection. Yet the torque deflecting the bracket is still going to be equal the torque applied to the brake. This is going to be the same for a stiffer material. In reality, there might be a slight power loss by the motor flexing and "de-flexing" the bracket, but I think it's not a major problem.
Id you control Junction resistances on The bread board? At 2 A they might Be significant.
You're right, the breadboard is rated for 2A, so there would have been some power loss there. That would be fixed for the next video!
The best ones are the ones I get free from decomissioned robots from work.
Can't beat unlimited bang per buck.
3:09 I'm guessing the P-Channel didn't work because once you turn it on by lowing the HDR signal, you won't be able to turn it off again because the HDR signal voltage at the gate will never be higher than the Drain.
The gate is pulled up by R7, so it only needs to be left floating for the MOSFET to be switched off. The problem is nHDR, which is connected to the MCU, cannot be pulled up to VPP. The MCU's GPIO protection diodes clamp the pin voltage to between GND and VCC (with a margin of error due to the forward voltage of the diodes). That means nHDR is clamped to ~VCC (and VCC < VPP), stopping the MOSFET from being switched off.
I noticed that some TB6600 driver modules have a circuit connected to the TQ pin of TB6600 chip that chopps the current limit to 30% of its setting, during half step period. May be that is affecting your measurements; i mean, instead of its "brains". You can check by probing pin 3, whether it stays high (5v) or not.
I few thoughts as a scientist: I saw a motor move in your test rig - you need to fix the mounting system. The twist will not be linear, and it ruins your torque test because some of the motors torque is being used to twist the motor in its mount. This is probably not a good place to use a printed part. While including the old school driver was "interesting," it should not be included for comparison since things are obviously not remotely similar. Your driver circuit is not properly designed and your measurements are being infected by back EMF from driving an inductive load. There should be a schematic with some of those motors showing how to deal with it - you will need some capacitors (of the correct type) to manage this. You can measure amperage with a shunt circuit using the RPi. It will not be a good as a dedicated amp meter, but it will be better than nothing. Lastly, you are probably also having issues with your wiring, especially in these low voltage tests where amperage is highest. In particular your breadboard is almost certainly not able to function at high amps. Voltage drop over the circuit can be a major issue, especially if you are using Chinesium connectors. Your circuit needs to be built with a huge margin, something like 80% derating to ensure it is not affecting the experiment. Solder those high amp wires, use genuine western made wire and connectors purchased from a place like Mouser (Not Amazon)
Thank you for the feedback. Could you please elaborate on what you mean by "the twist will not be linear"? I'm guessing there's little "work done" when the motor wiggles in the mount, but yes, it's not perfect. When you say my measurements are affected by the BEMF, do you mean the supply voltage is affected i.e. not perfectly stable at 12V or 24V? For measuring phase currents, I'm reluctant to add additional current shunts. I'm considered this, and may use a hall effect current sensor, though I'd still need to calculate losses. Overall, it might be better to keep things simple. Regarding wiring, yes there're losses involved. The breadboard is only rated to 2A, and the voltage drops could be significant at e.g. 2.5A. These are some things I'll be fixing before I move on to the TMC5160.
@@engineerbo For the mount, there are two things going on, fist is the natural hysteresis as the entire drivetrain comes under tension. every part in the drive train will have a different rate, the mount, the belt, the wheel, etc. These all sum together. Second is the way the mount itself winds up as it comes under load. First it compresses around the screws, then the plastic compresses, then it twists 90 degrees to the axis of the motor. once the rest of the drive train overcomes all the sticktion in the system, the mount will actually unwind, and then oscillate (over damped system with non-constant acceleration). All this happens at the beginning of the test where torque is at it's highest. yes, the back EMF as one winding is released is helping to power the next winding that is being powered. Each motor or driver should have a capacitor of a specific type and rating to absorb and drain the BAMF. The other issue is that BEMF can cause real havoc to the control board unless properly managed. Bigtree stuff seems to be pretty solid in general, but I would still take the time to make sure it is not a problem. The nice thing about shunts is that you measure voltage and calculate amperage, which is something that the RPi is happy to do. On the other hand, they need to be accurately characterized if you want true values. There are probably cheap inductive meters for the RPi available. Last time I dealt with it, I ended up just using a shunt tho since I did not trust any of the cheap boards I could find. It is a common enough problem that people want easy solutions to. I have both cheap and very "high quality" bread boards, and have found they all are pretty bad at gripping anything after they have been used. IC boards can be really bad about stretching them out. I think your overall approach is fairly solid.
Thanks for elaborating. The dyno only measures the speed and torque that gets applied to the shaft, and the brake also only affects the shaft, so if the motor is shifting about in its mount, the torque applied by the motor to the dyno would be lower. For example, of the motor is not mounted at all, the body of the motor will just be spinning freely, and it's not actually applying any torque to anything (except the air), and the dyno's measurements should reflect this. The speed will also read as zero, which wouldn't match the step frequency, so we'll know there's a problem.
I believe with the tmc2209 that it does not face such high current draw during holding torque/no movement situations depending upon settings. Doing UART control with an esp32 I've had it successfully vary in current/power draw between different parts of operation. Just a heads up. This is amazing though and I beyond appreciate such
Yes the TMC2299 can be configured to have different running and holding torques, and that's supported in Klipper too.
I recently had a problem involving this exact setup: a (generic noname) NEMA17 stepper, a TMC2209 driver (used with factory defaults as dir/step only drive) at 1/8 microstep and a 12V supply - low speed torque seemed ok, but the motor literally stalled around 600RPM or so, with no load, no matter what I did. Tried a beefier PSU, tried maxing the current pot as far as I dared, tried different microstep, nothing helped - even with gradually trying to raise the speed, the motor just started shaking and stalled. Really weird, and extremely disappointing - 600RPM a.k.a. a measly ten turns per second is NOT all that fast...
poderia Usar o TMC2160. Excelente driver da trinamic, com capacidade de 4.1A e 36V.
Good test. You will not be disappointed with the 5160. I used 2208 (Creative board), 2130 and 5160 (BTT OCTOPUS) on an Ender 5 PRO and a 5 PLUS modified with linear rail and with StepperOnline like the ones in your test. I have not measured the torque but the reliable maximum speed results are visible: if 2208 are 100%, 2130 are 150% (bit of whine at low speed) and 5160 are 170%. Now with all 5160 the loudest things are the PSU and cooling fans.
Very interesting! Would be great to also include a rough price of the motors next time
IMO the most interesting results are "hidden" in speed and torque curves - how much (answer: yes, torque varies pretty much between full steps :) ) speed varies when micro stepping. In 3D printers we can see VFA at lower speeds (e.g. Prusa MK3, any Ender 3 clone), more strongly when the printer is designed for high speed (e.g. Creality K1). They can be fixed in various ways (0.9 degree steppers on MK4, smaller steppers and pullies on K1C). Motor design (smooth stepping) and matching torque with moving mass (less torque and micro step judder with more momentum at higher speeds) and belts (spring) might lead to better print quality. Driver current may also affect VFA (not sure if it is tested) and might need to be dynamically adjusted for speed and acceleration of movement? Silencing stepper noise on Bambu Lab printers and Prusa XL probably also provides smoother surfaces with less VFA...
You should also include the fancy stuff, like Nanotec. And compare similarly specked models for this to make any sense.
I'd be more than happy to test the fancy stuff if I could afford them!
There is no such thing as "the best", the best for what purpose? At what current, for what speed, under what load?
Yes you're right, the user's needs are briefly mentioned in the preliminary conclusions. I just couldn't fit it into the title.
I have had success using TMC5160 with Nema 23 motors for driving a peristaltic pump (pulsating load). I used spread cycle mode to get the best results in terms of limiting heat and noise for speeds from 0.1RPM to 500RPM. However, to accomplish this it is necessary to send a new configuration datagram based on selected speed.
I'm trying to figure out why you can't measure torque at zero speed. I'd think the load cell on the dyno wouldn't be the problem. Is the problem with needing to provide steps to the driver? Any insight would be appreciated. I really enjoyed the video. Thanks for all the hard work. I subscribed.
Thanks for subscribing! To measure holding torque, the motor is usually made to hold it's position, and increasing torque is applied to it (from an external source, e.g. weights) until it position holding fails. With my dynamometer, the torque comes from the stepper motor itself, so strictly speaking, it cannot be at zero speed and increasing the torque at the same time.
Might be worth plotting `speed * torque` versus speed. (This is just 'output power' versus speed, give or take a constant factor.) It results in a much flatter graph, which tends to be much easier to read. Also, you can get stall torque with that setup. Just lock the brake on full, then drive the stepper.
You might be right about the stall torque. The reason I've added belts to the dynamometer is so it has a little compliance, which makes it possible to measure the torque when the motor is holding its position. But I don't think it'll actually be able to reach the actual holding torque, because the motor still needs to move, even if just a little bit, to move through its torque range.
@@engineerbo Ah. I thought you meant stall torque not hold torque. Yeah, hold torque is trickier, especially if you want it to test in the same setup. One approach that can work is to replace the brake with a larger motor with a decent controller. In practice, especially if you have a bit of gear/pulley ratio between the two. Still do the actual measurement with the load cell, but replace the gradual application of brake with the gradual application of PWM (instead of open-circuit). You might want a braking resistor, depending.
Yes using an external source of torque would solve the problem. But I'm not sure the actual holding torque is that critical to know, since an extremely slow speed gets me a number somewhat close enough.
@@engineerbo Agreed, at least for this application. Pull-in torque can be substantially different than pull-out torque even at zero speed, but I don't think you care in this case. One other thing that might be nice to measure - although is somewhat terrible to measure to be fair - is the stepper motor resonant frequency and behavior around said resonant frequency. Note this depends on the inertia of your load! Doing a slide test at (near) your resonant frequency is somewhat of an interesting worst case. (Essentially: a stepper motor 'snaps' to the next pole, especially when not microstepping. But in practice it'll oscillate around said next pole somewhat before settling down. Interesting things can happen when you do another step at the quarter/half/three-quarter/whole period of this oscillation.)
Subbed, awesome content! I would be really interested in testing the 5160tpro with the same motor lineup. Things you could include would be how microstepping affects the curves aswell as input voltage. :)
Thank you! The tests will be done in the near future!
wow great test machine
Thank you!
Thank you for taking the time to make this presentation.
Glad you enjoyed it!
The dyno you built is fantastic! What a great idea!
Thank you!
Ah.. should have used a more powerful microcontroller from the start.. next time try 1.5x the maximum amperage
Some people say it's perfectly fine to "overclock" their motors and I totally believe it, but it's also difficult to test whether the motors end up being unreliable.
#Bigtreetech send this guy bunch of drivers and boards
It'd be amazing if they did!
Looking forward to see similar test for 48 and 60V
Nice video, testing motors at same current setting would be better idea