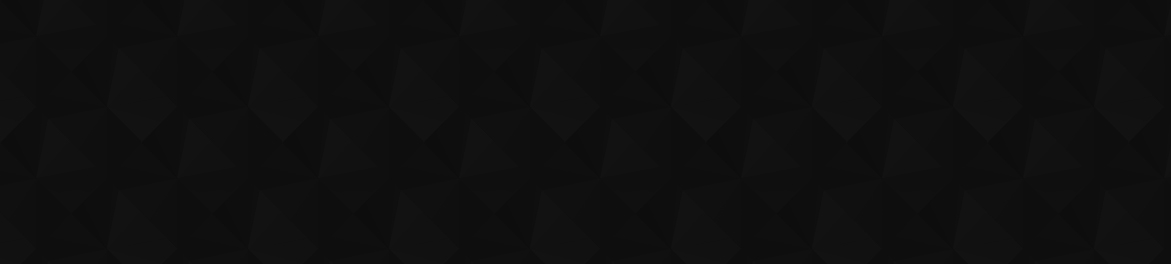
- 158
- 271 310
Alan's Home Workshop
Australia
Registrace 29. 04. 2020
A channel dedicated to amateurs who tackle all sorts of projects in their home workshops.
Building the Lynx15 - Part 9
I resume my Lynx15 journey by facing up to the challenge of machining my first properly profiled camshaft with inlet and exhaust lobes. It took two goes, but I did manage to make a good camshaft and learnt a lot in the process.
NB: There is a sound glitch for a few seconds starting at 13:45 - my apologies.
Links to camshaft machining resources:
* CamCalc modelenginenews.org/design/CamTable.html#opera
- supercedes to: cdn.imagearchive.com/homemodelenginemachinist/data/attach/88/88658-cam-with-draw.xls
* CamCalc documentation: cdn.imagearchive.com/homemodelenginemachinist/data/attach/88/88659-cam-lobes.pdf
* George Britnell Camshaft machining video: czcams.com/video/ysuUhHU6MvA/video.htmlsi=6xHQd6JESWclxRTY
Thanks to Greg @gregsmachineshop for his advice and support for my project
Website - gregsmachineshop.com/
Link to Building the Lynx 15 playlist:
czcams.com/play/PLQ5iH19hiQ0qAyApQVhqf0bhwk9C_kYN4.html
NB: There is a sound glitch for a few seconds starting at 13:45 - my apologies.
Links to camshaft machining resources:
* CamCalc modelenginenews.org/design/CamTable.html#opera
- supercedes to: cdn.imagearchive.com/homemodelenginemachinist/data/attach/88/88658-cam-with-draw.xls
* CamCalc documentation: cdn.imagearchive.com/homemodelenginemachinist/data/attach/88/88659-cam-lobes.pdf
* George Britnell Camshaft machining video: czcams.com/video/ysuUhHU6MvA/video.htmlsi=6xHQd6JESWclxRTY
Thanks to Greg @gregsmachineshop for his advice and support for my project
Website - gregsmachineshop.com/
Link to Building the Lynx 15 playlist:
czcams.com/play/PLQ5iH19hiQ0qAyApQVhqf0bhwk9C_kYN4.html
zhlédnutí: 624
Video
Tool setter for the milling table
zhlédnutí 677Před 21 dnem
I have found it useful to have a way of holding milling adapters in an inverted orientation out of the machine. For example when changing inserts or mounting a slitting saw on an arbor. This is just easier to do when the adapter can be securely held upside down. In this video, I make such a mounting as an attachment to the milling table.
Machining scrap hydraulic piston rod to make a forcing screw
zhlédnutí 1,1KPřed měsícem
High strength steels such as 4140 are expensive to buy as new material. However hydraulic piston rods are made from this sort of steel and I have found that scrapped rods can be scrounged at little to no cost. This video shows how I made a forcing screw from a 25mm ɸ and a 60mmɸ rod.
Building the Lynx 15 - Part 8
zhlédnutí 352Před měsícem
Lots of milling, boring and drilling here - with more mistakes :( Fortunately I was able to recover from them and only needed to make the cambox once :) Thanks to Greg @gregsmachineshop for his advice and support for my project Website - gregsmachineshop.com/ Link to Building the Lynx 15 playlist: czcams.com/play/PLQ5iH19hiQ0qAyApQVhqf0bhwk9C_kYN4.html
Building the Lynx15 - Part 7
zhlédnutí 978Před 2 měsíci
Time to start on the valve train, and the lathe gets a workout with a number of very small pieces. In this episode I make the valves, valve guides, valve retainers and tappets. Thanks to Greg @gregsmachineshop for his advice and support for my project Website - gregsmachineshop.com/ Link to Building the Lynx 15 playlist: czcams.com/play/PLQ5iH19hiQ0qAyApQVhqf0bhwk9C_kYN4.html
Building the Lynx15 - Part 6
zhlédnutí 601Před 2 měsíci
In this video I start work on the cylinder head. There is a lot of machining and many interesting setups so I hope you find it interesting. Please feel free to comment on how you would have done the machining - I'm always open to suggestions for a better way to do things. Thanks to Greg @gregsmachineshop for his advice and support for my project Website - gregsmachineshop.com/ Link to Building ...
Building the Lynx 15 - Part 5
zhlédnutí 520Před 3 měsíci
Back into it after a short caravan break. In this video I finish and install the cylinder liner then make the piston with its gudgeon/wrist pin. This completes the moving parts in the bottom end of the engine. Thanks to Greg @gregsmachineshop for his advice and support for my project Website - gregsmachineshop.com/ Link to Building the Lynx 15 playlist: czcams.com/play/PLQ5iH19hiQ0qAyApQVhqf0bh...
Building the Lynx15 - Part 4
zhlédnutí 2,3KPřed 4 měsíci
Making another crankshaft (- getting it right this time) and making the connecting rod. There was a lot of work in those 2 pieces and this is a longer video that explains the operations and challenging setups that I used. Thanks to Greg @gregsmachineshop for his advice and support for my project Website - gregsmachineshop.com/ Link to Building the Lynx 15 playlist: czcams.com/play/PLQ5iH19hiQ0q...
#Shorts Morse Taper Wedges
zhlédnutí 548Před 4 měsíci
My rotary table has an MT3 socket with no extraction method for tool shanks except beating them from the backside of the table. In this short video I show how I made a pair of extractor wedges similar to the wedges used for releasing a drill chuck from a Jacobs taper.
Building the Lynx15 - Part 3
zhlédnutí 476Před 4 měsíci
I tackled the crankshaft in this episode and it was going really well - until disaster struck. Thanks to Greg @gregsmachineshop for his advice and support for my project Website - gregsmachineshop.com/ Link to Building the Lynx 15 playlist: czcams.com/play/PLQ5iH19hiQ0qAyApQVhqf0bhwk9C_kYN4.html
Building the Lynx15 - Part 2
zhlédnutí 742Před 5 měsíci
Major piece in this episode is the cylinder and there is a lot of lathe work in it. Thankfully I didn't make any mistakes with this piece :) Anyway, the engine is really taking shape now and looking good. Link to Building the Lynx 15 playlist: czcams.com/play/PLQ5iH19hiQ0qAyApQVhqf0bhwk9C_kYN4.html
Building the Lynx15 - Part 1
zhlédnutí 1,2KPřed 5 měsíci
Following the successful conclusion of my Webster engine build, I decided to make another engine. This one is 15cc with a belt driven overhead camshaft and an enclosed crankcase. Plans obtained from Greg's Machine Shop (links below). In this video, I get started on the crankcase. Greg's Machine Shop: CZcams - @gregsmachineshop Website - gregsmachineshop.com/ Picture of engine by Kevin Woods: cz...
Webster Engine - Final
zhlédnutí 491Před 6 měsíci
In this video I finish tidying up and detailing my Webster engine. (NB: This video replaces a previous post which unwittingly included some copyright music.) Link to Webster Engine playlist: czcams.com/play/PLQ5iH19hiQ0p8G3R0aBK53sVKrV5CB8lx.html&si=076MzlXBC-uwaVQS
Webster Engine - Exhaust Back Pressure
zhlédnutí 378Před 6 měsíci
I was fiddling around with my new Webster engine this morning and noticed that performance seems to be improved by a slight restriction in the exhaust pipe. This is counterintuitive to me as I've always believed that 4 stroke engines run best with the least exhaust restriction. I would welcome an explanation of the observed effect and I'd also appreciate any advice on optimising the exhaust pip...
Centering a 3 jaw chuck on a back plate - short video
zhlédnutí 630Před 8 měsíci
Centering a 3 jaw chuck on a back plate - short video
I watched this another day and I just tested it on my mini 3inch rotary head, it works! I have been tapping the chuck with hammer for hours and it won’t true up until I saw this method. Many thanks!
I found it to be much faster than tapping, and it would have been even easier with a better jack. I'm thinking about making one designed for the job. Thanks for watching.
Outstanding Effort Alan, getting very close now ! I'll pop over soon to see it in the flesh !
Thanks Fergus :)
Nice. Haven't seen that done before.
Thanks Carl. As noted, this was my first "proper" camshaft (Webster just had a single lobe made with two rounded ends and flat flanks). When I asked Greg how he would make it, he referred to a method that requires a cam machining jig. I expect that is a much faster way to machine camshafts - after you have invested in the jig. However, building a single cylinder engine with enclosed crankshaft and overhead camshaft was just an interesting challenge for me and I may not make any more engines. So while milling several hundred thin slices was a bit tedious, I think it was the best option for me. Cheers.
You have given me many ideas for my bandsaw. Thank you.
Some of the improvements were pretty easy to do James, so go for it! Thanks for watching.
well done Alan. I've never made a cam, I'm going to bookmark this just in case😁
Thanks Paul. The maths involved in calculating the tangential machining path are not trivial and I am very grateful to the person who published their solution :) Cheers.
Nice work Alan, I wish I had a dollar for every time I stressed over a part, only to find the solution was a lot simpler than I had imagined. Always nice to solve a dilemma and hope for a simple task to come around again, cheers!
Thank you. Like most things - easy when you are shown how to do it :) Cheers.
Pat yourself on the back for that..well done
Thank you.
Well done Alan.
Thanks Henry.
Great video Alan, I like your calm, analytical approach to problems. Thank you for sharing.
Thank you Stephen.
Great job Alan.
It was a bit of a character test, but ultimately quite rewarding :) Cheers.
Allan if you won't to confuse your self watch some videos on cam grinding and development . Kit from up north
I'm easily confused these days Kit, so I think I'll limit myself to what I need to know about cams :) Cheers and thanks for watching.
really happening now Alan!!! cheers.
Thanks Graedon. I didn't realise how much I didn't know about camshafts until I made this :) Cheers.
New update! Lemme go make some tea.
Hope you enjoy it :) Cheers.
Well impressed with that mod mate , great job 😁👍
Thank you Karl.
Очень хорошая фиксация . Очень хорошее видео .
Спасибо.
Maybe try some lamingtons? Memm Fox advises it
Its that time of year and the possums are trying it on again. But three years on and the tree is noticeably taller; it is getting easier to prune off all the attack vectors :)
I'm glad to hear :) (I was making a joke about Possum Magic hahaha)
Amazing job! The engine sounds sweet! And the look on your face when it started was priceless!
Thank you - it was a special moment that was very rewarding :) Cheers.
Just remember to properly torque the collet nut before you use it. If the tooling moves at all in the collet it can ruin a job instantly and in the worst case your machine or the operator.
Thanks for your feedback Joe. Sadly, I have on several occasions forgotten to tighten cutters held in my quill mounted tool holders :( However, I don''t think using this new fixture will make me any more vulnerable to such lapses - hope not anyway :) Cheers.
I guess you skipped the rounding of the end. Nice work.
Thanks Carl. I rounded the end using a clamping accessory I made for my bandsaw, and removing material with two angled cuts on each corner. This left small amounts which were easy to remove on the belt sander. I didn't show this because the video was already over thirty minutes long and this seems to be the limit that many viewers prefer. Cheers.
Another terrific idea, beautifully executed. It's always a pleasure watching you at work. Best regards from South Gippsland, Victoria Australia
That's very kind of you to say and I'm glad you enjoy my videos. Cheers, Alan.
You may want to make some plastic caps to cover the tool held in the holder, eventually you will swipe your hand across one.
That's a good point - I catch my hand often enough on the tool in the quill while futzing around under it. Cheers.
Nice neat job Alan, I loved the tolerancing !
The Vertex boring head is a very nice bit of kit. It'll consistently remove 0.01mm off a diameter and can be finessed to ~.005 - provided the operator doesn't lose count of the clicks :) Cheers.
Very nicely done!
Thank you
great idea, nicely done! I must make one now..
Thank you.
Nice tool Alan, Gotta make one of those.
Thank you. The design was influenced (as usual) by what was in the scrap bin. My first idea had been to use a short piece of 100mm square tube and just bore a big hole in the top and a small hole in the bottom. However, I didn't have a suitable piece of stock, and a socket with matching taper does locate the adapter very positively. The design also allowed me to round the piece off and avoid nasty corners. Cheers.
Nice job Alan
Thank you.
Alan, honey mustard is much better on a ham sandwich. Than the milling machine. Such a basic tool, but such an excellent job as well, Cheers from America. :)
Yes, that "honey mustard" is nasty stuff and provides no anti-corrosion protection - it will be replaced asap. Thanks for your feedback Stewart.
@@alanshomeworkshop No need to replace, I just thought it was funny, that's all, love your content
Great job Alan.
Thanks Henry.
Job well done Alan, as said on pinning the nut, thank you for sharing, have a great weekend
Thanks Ralfy.
Very nice work sir
Thank you. I share your interest in repair and reuse of things and materials. Cheers, Alan.
Alan, Nice project and good job working with imperfect stock!
Thanks Allen. It's very satisfying to get a silk purse out of a sow's ear :) Cheers, Alan.
Nice work Alan, I made one like that years ago, but I had a block of aluminum and made check valves from bolts and balls. It worked well for light duty, but was a great experience as I did not have a compressor at the time. Enjoyed the video, cheers!
good vid Alan, i have used those rods and you are right, they can be tough!!
Thanks Graedon. My lathe tools cope well with it, presumably because of the constant engagement pressure. But my milling cutters are on the struggle bus - to quote another CZcamsr :)
Great Job
Thank you.
Nice job Alan. You may end up putting a keyway or cross drilling and pinning the bolt head on. I love that material as stock and use wnmg inserts to peel off the hardened layer.... 1.5-2.5mm DOC. I tried annealing it with flame but it bent like a horseshoe.
Thanks - and good to hear from you again. I'm a bit tempted to test the Loctite adhesion to breaking point just to see if it measures up - but I'm not sure how I could measure the yield stress. The hardened layer on the 60mm bar was actually 3mm thick but it did cut cleanly, albeit with a very loud squeal. What feed rate do you use when stripping it off ? Cheers.
Good interesting video. I enjoyed it. I reckon you could have given it a bit more work to do for the test cuts. 0.2mm is a bit light.
The depth of cut is half what you suggest. Good video. Thanks
Thanks for the feedback Mike. You are right about the depth of cut - but I did actually correct myself at 15:00 Cheers, Alan.
Sorry Alan. I didn’t get that far in the video as I had to go out. Looking forward to watching the last part. Cheers 👍👍 Mike
I started my apprenticeship in the late 60s. We were taught that the Unified system was replacing the Whitworth system of threads, the car manufacturers in the US, Canada and Britain were adopting UNS. In the end, the Metric system prevailed. So I'm surprised that you still use NS taps, unless there is more to the American threads than I understand. Not a complaint. But you do some very nice work, Alan.
Thanks for your feedback Bill. When I started working on cars as a teenager in the early 1970's, Unified threads were the norm in locally (Australian) manufactured cars but Whitworth threads were still common in plumbing and general hardware products. Metric threads were common in imported vehicles and starting to became more common in other domains. So I have worked with all three systems and have a good coverage of taps and dies for them. I have also worked with other metric thread systems eg BA, and pre-ISO JIS (they are found in pre-1967 Japanese cars and motorcycles). When no other factors apply, my preference is to work with ISO metric threads especially when using my lathe as it has a metric lead screw. But I also have quite a large range of imperial socket head screws (an auction purchase years ago) and prefer to use them rather than buying new metric items. Cheers, Alan.
Ya lost me at Vertex rotary, the sine plate, and angle plate. As much as i'd like to make a shell mill out of scrap, it'll be far less to buy the 50 buck import! Great video, very informative, thanks for sharing.
There was a bit of head scratching and high school trigonometry :) End result was very pleasing though and I have found the cutter to be a useful addition to my toolkit. Thanks for watching John. Cheers.
Very good
Thank you
Como conseguiste los planos
Greg's Machine Shop: CZcams - @gregsmachineshop Website - gregsmachineshop.com/
@@alanshomeworkshop gracias
really ,, really good mate!!!
Thanks Graedon. I'm certainly getting plenty of practice at fixing mistakes :)
Honda engines are dropping out of F1 i believe they need a machinest and engineer to safe them ! Kit from up north
Thanks Kit.
A great save! 😅
Thank you.
well done. How come I never come across offcuts that long!
Good'ay Paul. There's a steel supply store near me and they have an offcuts "bin" for pieces under a meter. I cruise through from time to time and check it out. My good mate Murphy ensures that I'll never find a good offcut when I need it, so I go looking when I don't :) Thanks for watching.
@@alanshomeworkshop Murphy's always hanging about somewhere, sticking his oar in😁
@@paulrayner4514 Are you familiar with some corollaries to Murphy's Law that are particularly relevant in the workshop ? A dropped object will always land where it can cause the most trouble Where there's a possibility of multiple failures, the most damaging will occur The probability of the loss or breakage of any part is directly proportional to the difficulty of getting a replacement part. Material will be damaged in direct proportion to its value. And one of my favorite aphorisms: - And a voice from the gloom said smile for things could be worse; so I smiled and, yes, things indeed became worse.
@@alanshomeworkshop oh yes, Mr Murphy is quite prolific in my workshop, I'm beginning to wonder if he's using my workshop to train his offspring in the mystical art lately.😁
Great job Alan, well saved.
Thanks Henry.
Lovely job Alan. Very well explained.
Thank you.
Excellent detailed video. Thank you very much. I have a similar hoist with trolley and have mounted the same on a Ibeam which is 4 inches (3.5inches inside area) x 2 inches. The trolley along with the hoist is moving back and forth by hand push but not motorised. Do you think I need a bigger I beam ? What are the dimensions of your I beam. Did you mount the trolley first and then attached the hoist to it ? I have a similar weight problem as my hpist is a 750/1500 hoist and weighs 27 kgs. Very difficult to handle. My mounting height is only 6feet though.
My I-Beam is 6"" deep by 3" wide with tapered flanges (the modern Universal Beam or UB profile has parallel flanges). This was the minimum width recommended for the trolley. If it is fitted to a narrower beam, the wheel flanges cannot be set close enough together to track correctly. I did mount the trolley to the beam first and then bolted the hoist up to it: czcams.com/video/KJXbOYrOMxI/video.html Thanks for comment and I hope the video helps you achieve your project. Cheers, Alan.
Very nice work. I need to invest in a milling machine.
nice work. you will have to get a jewelers loop to see, I keep going to buy one but never do😁
Thanks Paul. I've tried a few different magnification options with varying degrees of success. I currently use a USB microscope (eg for the valve stem photo), and a headband magnifier with 5 lenses for work in the lathe. The microscope is ok and more useful after I made a taller column for it. This is my "go to" tool for metal splinter removal. The headband magnifier was ok but the lens retaining clip is cracked and the lenses are prone to falling out. It also requires me to get up close and personal with the target - not always desirable with the lathe. But I shouldn't keep whining about it, there are people much worse off than me :) Cheers.
@@alanshomeworkshop Somewhere, a mobile phone was used as a magnifier. Not sure, me I do not own one, and never will.😊
@@alanshomeworkshop I know what you mean with the head bands, i've got 4 of them. what appeals to me is I've see Joe pie using a loop and he puts the loop close to the work with his head away. like a normal magnifying glass I suppose.