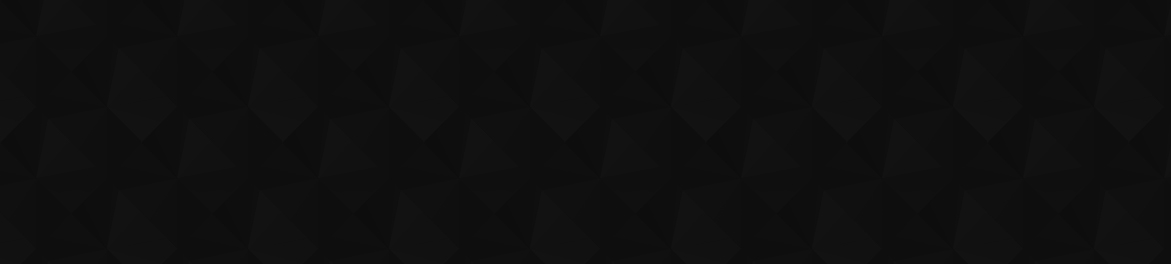
- 26
- 199 859
Forge Product Development LLC
United States
Registrace 23. 02. 2021
How to Align Empty Mesh Files in SolidWorks
Learn how to orient empty geometry files (graphics bodies, scans, .obj, .stl, .3mf) to the base coordinate system within SolidWorks. These workarounds help solve the "...geometry is not valid for this type of save operation" error some subscribers were getting following our previous "Perfectly Aligned .stl's" video.
If you found this video helpful, please Like and Subscribe to help support our channel!
Check out the original alignment video here: czcams.com/video/d-3O_Vie-Sk/video.html
-
Thanks for watching!
Find us on you preferred platform:
Our Website: forgeproductdevelopment.com/
LinkedIn: www.linkedin.com/company/28881244
CZcams: czcams.com/channels/3k2BrjNyNgPqKRWS_2Q0hQ.html
Twitch: www.twitch.tv/forgepd
Facebook: ForgeProductDevelopment
Instagram: forgeproductdevelopment
Twitter: ForgePD
-
If you are interested in being on our show, either with a question or as an industry expert, contact Forge Product Development LLC via email at info@forgepd.com.
If you found this video helpful, please Like and Subscribe to help support our channel!
Check out the original alignment video here: czcams.com/video/d-3O_Vie-Sk/video.html
-
Thanks for watching!
Find us on you preferred platform:
Our Website: forgeproductdevelopment.com/
LinkedIn: www.linkedin.com/company/28881244
CZcams: czcams.com/channels/3k2BrjNyNgPqKRWS_2Q0hQ.html
Twitch: www.twitch.tv/forgepd
Facebook: ForgeProductDevelopment
Instagram: forgeproductdevelopment
Twitter: ForgePD
-
If you are interested in being on our show, either with a question or as an industry expert, contact Forge Product Development LLC via email at info@forgepd.com.
zhlédnutí: 1 615
Video
How To Use SolidWork's Split Feature to Easily Separate a Solid Body Within a Part File
zhlédnutí 8KPřed rokem
In this tutorial, we will show you how to use the split command in SolidWorks to separate a single solid body into multiple bodies. This powerful tool allows you to divide a complex shape into smaller, more manageable parts, making it easier to work with and edit. By the end, you will have a good understanding of how to use the split command to effectively divide your models. If you found this ...
How to Align .STL Files in SolidWorks
zhlédnutí 14KPřed rokem
Today we tackle the most asked question from our previous "working with .stls" video, and that is "How do you orient new .stl files within Solidworks?" If you found this video helpful, please Like and Subscribe to help support our channel! - Thanks for watching! Find us on you preferred platform: Our Website: forgeproductdevelopment.com/ LinkedIn: www.linkedin.com/company/28881244 CZcams: czcam...
Top Down Modeling With Skeleton Sketches in Solidworks
zhlédnutí 12KPřed 2 lety
Skeleton sketch top down modeling is a very robust and light weight method when trying to design complex components within SolidWorks. Today we walk through the basics of this technique and talk about some of the benefits and tips for its use. Monday through Friday we are live on our social media platforms helping people from around the world answer tricky engineering questions. We cover topics...
Weird Faces: A beginner's guide to surface modeling in SolidWorks
zhlédnutí 27KPřed 2 lety
Todays video is inspired by a redditor's struggle with "weird faces". Watch how we work through a basic surface model within SolidWorks. Monday through Friday we are live on our social media platforms helping people from around the world answer tricky engineering questions. We cover topics that include CAD, design for manufacturing, project management, sourcing and supply chain optimization, 3D...
Q&A with Met2 Design Competition Students Pt 3
zhlédnutí 342Před 2 lety
I recently had the honor of talking with a group of students competing in the national Met2 Engineering Competition. This is the third and final segment of out talk, and includes a variety of tips for working within SolidWorks. Monday through Friday we are live on our social media platforms helping people from around the world answer tricky engineering questions. We cover topics that include CA...
SolidWorks Simple Surfacing Challenge Tutorial
zhlédnutí 3,6KPřed 2 lety
Today we go in depth on how to plan and execute a model with some surfacing elements. We discussing analyzing a reference image, planning out surfaces, controlling surfaces for fillets, and other great tips. Monday through Friday we are live on our social media platforms helping people from around the world answer tricky engineering questions. We cover topics that include CAD, design for manufa...
Met2 Program Interview Pt 2
zhlédnutí 87Před 2 lety
Here is part two of our recent talk with a group of students competing in the national Met2 Engineering Competition. This segment includes a variety of tips for working within SolidWorks. Monday through Friday we are live on our social media platforms helping people from around the world answer tricky engineering questions. We cover topics that include CAD, design for manufacturing, project man...
Q&A with Met2 Design Competition Students Pt 1
zhlédnutí 459Před 2 lety
I recently had the honor of talking with a group of students competing in the national Met2 Engineering Competition. This is the first segment of out talk, and includes a variety of tips for working within SolidWorks. Monday through Friday we are live on our social media platforms helping people from around the world answer tricky engineering questions. We cover topics that include CAD, design ...
How to Draft Curved Surfaces in Solidworks
zhlédnutí 6KPřed 2 lety
Today we look at a technique for creating curved surfaces, with adequate draft angle, in SolidWorks. Monday through Friday we are live on our social media platforms helping people from around the world answer tricky engineering questions. We cover topics that include CAD, design for manufacturing, project management, sourcing and supply chain optimization, 3D scanning and printing, entrepreneur...
How To: Twisted Ribs in SolidWorks
zhlédnutí 1,9KPřed 2 lety
Learn how to create complex curved support ribs in a SolidWorks. Monday through Friday we are live on our social media platforms helping people from around the world answer tricky engineering questions. We cover topics that include CAD, design for manufacturing, project management, sourcing and supply chain optimization, 3D scanning and printing, entrepreneurship, and much more. If you found th...
How to Reverse Engineer .STL Files in SolidWorks
zhlédnutí 65KPřed 2 lety
How to Reverse Engineer .STL Files in SolidWorks
Find the Perimeter of a Sketch Soldiworks
zhlédnutí 1,4KPřed 2 lety
Find the Perimeter of a Sketch Soldiworks
How to Fix SolidWorks 2021 Graphics Bug
zhlédnutí 30KPřed 2 lety
How to Fix SolidWorks 2021 Graphics Bug
Complex Pin Paths Using Rack and Pinion Mates in SolidWorks
zhlédnutí 916Před 2 lety
Complex Pin Paths Using Rack and Pinion Mates in SolidWorks
Random Act of Engineering Ep.2 : February Speed Model Challenge
zhlédnutí 416Před 3 lety
Random Act of Engineering Ep.2 : February Speed Model Challenge
How about insert part the skeleton into sub-parts vs derived sketches? Maybe more warranted for more complex parts / subassemblies, and too much overhead for lots of simple parts?
Inserting a part vs derived sketches is a questions that gets brought up quite a bit. I have not done enough testing between the two to say one should win outright. At this point I would view them as tools to have in the box. Get familiar with both and then pull each one out when you feel like is has the advantage. At this point I would say both are viable, but I am likely biased towards the SS method due to familiarity.
Great video, thanks! Only thing I would say is I personally would like to see the actual process of making the sketches in the first place. How did you get the dimensions you used for the general shape?
I have a stl file, i want to modify it in solid works. i have tried to bring in as solid, then convert to solid, but still have lots of triangles. im a novice. im not a good designer but i need to make small tweaks to stl files. can you point me in the right direction
thank you a lot , it really helped me to solve that problem .
Thanks for the comment!
Hi! Is it possible to work like that in SW for Makers?
I have not used it, but if it is just a low cost license of the main desktop software, then yes.
Can we make surfaces like this for curved surface so that wr can split it from main body?
@@Mesolas yes, you should be able to use any continuous surface body that completely divides the solid.
Quick shout out to Josh for helping me out with a problem I was having creating an offset after using the "Cavity" function. I was blown away how quickly he came to my aid, whilst being patient with my lack of experience. 11 out of 10.
Yea, easy when you already know what to design. That is the problem with the cad software designers and instructors, They are seeing and approaching problems from a different perspective than a designer - "This is the best way to design this assembly"....... But most creative designers just have a very rough idea in their head when they start. Then the design will grow slowly from blocky parts and grow by adding/removing features/parts hundreds if not thousands of times in the most chaotic order.... Yea, one could redesign everything again and get it clean and optimally structed after this creative phase, But small companies don't have such resources, and the design will be used as it is.
This is a great comment, as I can understand your frustration and am sure others have felt this way as well. I have felt the same way watching people do surfacing Tutorials for SW too. The truth is, you are right, CAD is a terrible iteration and ideation tool. It takes way too long to create even the simplest of geometry, let alone build proper file structure and dependent relationships. However, even though that is true, the solution is not to throw those things out. That would be an excuse for poor CAD practices. Rather, it is to use other, more effective tools for the ideation and conceptualization phase. Moving to CAD only when you can leverage what it does best, relationships and structure. Imagine you are trying to design a new house by building walls and pouring concrete, then half way through you realize the layout isn’t right. It would feel really clunky to have to rip all that out to change the design. In fact, that frustration may cause you to build lighter weight walls, or to try to move the concrete around while it’s still wet. The need for flexibility would create bad practices with those tools because they are being used for a job they are not designed for. Same thing here. You are using CAD tool too early in the process to be utilized properly, therefore you are creating bad practices to try and use the tool for something it is not designed for. On a real-world project for a client, it is very rare that I will touch CAD before I have gone through extensive ideation and industrial design with pen and paper or tablet drawing tools. Keep in mind, I am an engineer, not an artist, so these drawings are often very rough and unsightly. Then, once the client has signed of on a design direction based on the 2D sketches, we move towards CAD, then iterate from there. Often times we will design a CAD model and then find a new design direction, but even then, we will go back to 2D sketching and establish direction before trying to capture the idea in a new model. Also, keep in mind you are watching tutorials on how to CAD, not how to design a product from scratch. You only see “cad software designers and instructors” showing you how to draw stuff they already know, because they are trying to show you how to use the tool, not a documentary on their overall process. To make videos showing how to ideate or conceptualize in CAD would be untruthful to their process and bad practice. Hope this helps clarify some things, feel free to reach out if you have any more questions or comments!
@@forgeproductdevelopment no substitute for pen(cil) & paper, highlighters for ideation! That said, I start with some simple reference goemetry in CAD to establish constraints, key datums, and simple sketches. This because we've all sketched something that "made sense" until you put it to scale... Print rudimentary CAD, sketch to ideate, update the sketches, occassionally add more reference features, lather, rinse, repeat. This also creates a breadcrumb trail.
@@raphaelhamm3853 This is an excellent suggestion as well. We have designed products where there are PCBs and motors, attachment points, or other components that are selected based on previous calculations. Sometimes we import those into CAD early on to get a sense of scale, and export out images to draw over the top of when coming up with designs. I think the heart of the matter is "start with what you have and select the best tool to move your forward given the initial conditions'. Whether that be from COTS components, systems you need to integrate with, mathematical calculations, or a completely blank sheet of paper. Each project is unique and part of the fun of engineering is getting to solve and optimize for those challenges along the way.
where are you located?
USA
Fixed my issue and it was one of the first things that popped up when I searched so thanks for this good sir!
Yourr channel is awesome mate! BTW you mentioned CAD scanner in your previous videos, which one are you using? and which one would you recommend?
Glad you are enjoying it! I hope it has been helpful. I don't have a scanner in house, but have sent out parts to have scans generated before. I recently did some testing with photogrammetry, but was unable to produce a model of adequate quality.
Watched it, did it, FIXED it!! Thanks mate!
Cheers!
Good tips, im starting with solidworks and want to do complex modeling rendering for comercial products.
Surfacing in solidworks can be tricky, but once you get the feel for it, it is very rewarding. I would also recommend trying some other programs, such as rhino, zbrush, and blender, as they can be valuable tools in your belt.
I really wish solidworks would implement more "free form modeling" approach or just give you that option. Working with parameters thru really complex geometry is dangerous in SW, it will most likely build out nicely first run, then you hit Cntrl Q and your shit blows up. Working with UG/NX for over 15 years I was able to work without parameters for really fast modeling which also in turn left you with a more "light weight" model in the end (this also has its downfalls as well of course). But, SW is good if your initial approach is really solid. Ive been on SW for last 5 years and I do like it. I like your approach in this video, good tips, thanks!
goood excersice
Great job. Thanks.
You are amazing! thank you!
This is awesome! Thanks for the detailed tutorial!
Thank you so much!!! I went through soo many install and uninstalls!!
thx
Good tut!
Awesome video. Was looking for a way to extrude cut multiple parts in an assembly at the same tiem
Thanks ... preparing for my interview I'm a fresher with no experience n have a interview scheduled Monday.....
Wow, respect. Love your videos
Nice solution!
omfg thank youuuuuuuuuuu
Amazing that this is still helping people
That's great! Thank you. Greetings from Brazil
Greetings! Did it help?
@@forgeproductdevelopment yes, very helpful... l've never worked with surface modeling, so I'm trying to learn it by myself
@@duduposser I found learning surfacing within the solidworks community to be difficult, as there are not a lot of intensive tutorials. Please let me know if you find any good material or find an area where you think a video could be helpful!
@@forgeproductdevelopment I work with rotational molding. Usually the design of most products is not so complex but now I am facing a new project with all these curves
Im trying to reverse engineer an obj file of a kar98k rifle stock which is 3d scanned and sended to me but failing to do so ill use this video as guide thanks
Kar98K! Now you are in my world! Is this for work or fun? Let me know if you want some help on it!
how you calculate 2.5 mm distance between each gear ?
Is you are using off the shelf gears, the distance between gear axis will = (PD1 + PD2) / 2 Where PD is the Pitch Diameter for gear 1 and 2. The pitch diameter should be listed in the specifications for the gear. If not, you can calculate it given other know values of the gear (module, number of teeth, etc.). Does that help?
@@forgeproductdevelopment thx
Good day Sir. Is there a way that we can use mesh models into solidworks assembly?
Absolutely, I would create a part file within the assembly and put the mesh in that file, then use that as a reference for the other part files within that assembly. Try to keep the part file with the mesh at the top of the assembly design tree. Does that help?
@@forgeproductdevelopment Thanks Sir. How about creating an assembly of mesh models? Is that possible Sir?
@@Pathfinder_1314 It should be. Have you tried creating part files, each with its own part of the mesh, and then inserting those part files into an assembly?
@@forgeproductdevelopment yes Sir. I created mesh bodies as part files but the Mate Feature doesn't work on them. Do you have a video reference to this topic Sir?
@@Pathfinder_1314 Ah yes! The mate commands will not work on the mesh. You will need to create some form of geometry within each part file to mate to, either sketches or surfaces will work. This video shows how to create geometry within the part files using the mesh as reference.
Nice
Thanks
I need som ehelp as I cannot import as a graphics body, the option is greyed out
You saved my day, ty
Glad I could help!
Nice. I recently purchased a 3D scanner and plan on using it to build rear and front bumpers. I am still a little lost on how to get started in solid works with the scan. Any help would be much appreciated.
Happy to help! Are you making it out of tube? Do you have the scan yet?
@@forgeproductdevelopment it will be a combination of both tube and plate. I do have a scan already. I have uploaded on to Solidworks but now I don’t know where to go from there 😬.
Is this for work or fun? If you send me the scan I am happy to show you some things. Send it to info@forgepd.com
@@forgeproductdevelopment this would be for my business. Sounds good will do!
muy buen video mi lord master, se me deje de parar........la pantalla nunca vi a un crack como tu solucionando un problema de solid al cual no veia solucion alguna pinche solid 2021 esta bien bug no? jajajajajaa githme head
Gracias pelón, me salvaste. Un beso :)
You are a saviour.
Please play tournament in speed cad modeling too tall toby
I have watched those before! Those guys are very fast (faster than me haha). Do you know if they post recordings? I have thought about doing a previous challenge and then comparing it to the winners recording, to see where I lost time and pick up some tips.
This is top notch 🤌
Thanks!
Nice video, but I have problem with save to stl with new coordinate. When I click save I dont see stl in folder. Maybe you know why?
Is this when you try to "save as" .stl it is not an option, or after you save the file it is not in the location you saved it to?
you just saved my day man. thanks!!!!!!
Overall a very good educational video to reverse engineer a scanned part. But here are my 2 cents to the process shown in the video. The first step should always be to check and fix alignment of the origin aswell as checking the geometry itself if its warped or crooked, ie squareness and parallelism of the main surfaces. In general you should really only use the scanned model as a reference to create an actual parametric model. All the sketches and planes you did should not be actually used for extrusions but used for construction reference. This way you can use them for defining actual real measurements for a fully adjustable part that can be edited like the original part. It takes a little bit more work but its nice to have the fully adjustable features for the whole part. That way you can customize it again and it wont be locked to the scan's dimensions which, in the real world, are always off, have weird decimals and never 100% accurate geometry. (In this example the angles are off and most of the dimensions have weird decimals) FYI if you do it this way the mass of this model is 100% accurate with the provided mass it should be. Thanks for the video!
Большое Спасибо . Быстро и понятно , без лишних слов !
What an awesome instructor you are! I just now stumbled across your channel and subscribed. I have always struggled with reverse engineering STL's. Thank you for making it make sense!
Hello from China! Thank you!
Stl give me.
I couldnt do this. Is it because its a graphic body?. Should i convert to a mesh?
THANK YOU SO MUCH JOSH THIS FIXED IT!
Glad I could help!
teşekkürler P
Блин, хорошая у вас тюрьма, был бы в Теннесси обязательно какой-нибудь закон нарушил, чтобы также в солиде развлекаться