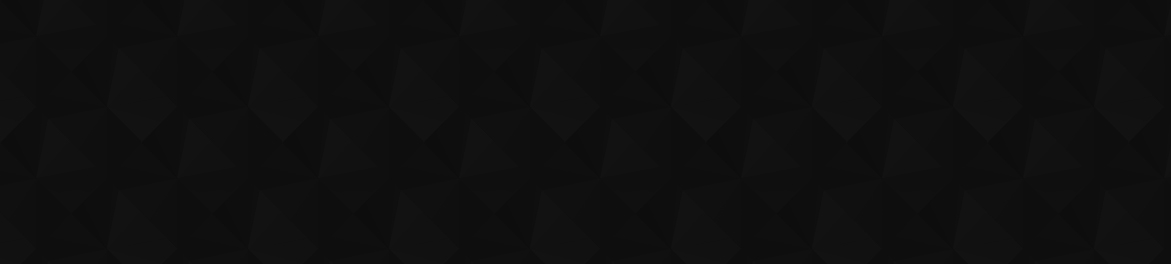
- 40
- 130 806
PolyLabrobot
Canada
Registrace 7. 04. 2013
Video channel presenting the activities of the Robotics and Adaptive Mechatronics Laboratory at Polytechnique Montreal, Canada. This channel is managed by Prof. Lionel Birglen.
Comparison of Soft Robotic Fingers for Industrial Applications
This video demonstrates how important proper soft robotic finger design is for the grasp capability in practical industrial applications. Of the three designs shown here only the newly introduced PacomeFlex finger can grasp all objects without issue. The unique asymmetrical design of the PacomeFlex finger as well as its integrated stopper allows for an optimal distribution of grasp forces as well as strong precision (pinch) grasps.
See the following paper for more details including a prediction of the grasp forces with neural networks:
Shan, X., and Birglen, L. "Bistable Stopper Design and Force Prediction for Precision and Power Grasps of Soft Robotic Fingers for Industrial Manipulation." ASME. Journal of Mechanical Design. doi: doi.org/10.1115/1.4063763
asmedigitalcollection.asme.org/mechanicaldesign/article/doi/10.1115/1.4063763/
See the following paper for more details including a prediction of the grasp forces with neural networks:
Shan, X., and Birglen, L. "Bistable Stopper Design and Force Prediction for Precision and Power Grasps of Soft Robotic Fingers for Industrial Manipulation." ASME. Journal of Mechanical Design. doi: doi.org/10.1115/1.4063763
asmedigitalcollection.asme.org/mechanicaldesign/article/doi/10.1115/1.4063763/
zhlédnutí: 164
Video
Variable Stiffness Soft Robotic Fingers using Snap-Fit Kinematic Reconfiguration
zhlédnutí 287Před rokem
A new design of soft fingers with embedded snap-fit is shown in this video. The snap-fit is used to switch from a low- to a high-stiffness configuration and vice-versa. These purely mechanical fingers can be attached to any standard gripper and do not need any electronics or actuators outside from their gripper. The switch between stiffness modes requires no supplementary actuation and can be c...
Open-Source Planar Cable-Driven Parallel Robot: Teach Pendant Demo
zhlédnutí 814Před rokem
Video companion (2/2) of the paper: "Design, Control, and Experiments of a Low-Cost Open-Source Planar Cable-Driven Parallel Robot" by Mikael Arslan and Lionel Birglen, 2023 CCToMM M3 Symposium, June 19-20, 2023. See: cctomm.ca/proceedings_en.php All sources to build your own copy of the robot at: github.com/LionelBirglen/OpenSourcePlanarCableRobot
Open-Source Planar Cable-Driven Parallel Robot: Interpolated Trajectory
zhlédnutí 5KPřed rokem
Video companion (1/2) of the paper: "Design, Control, and Experiments of a Low-Cost Open-Source Planar Cable-Driven Parallel Robot" by Mikael Arslan and Lionel Birglen, 2023 CCToMM M3 Symposium, June 19-20, 2023. See: cctomm.ca/proceedings_en.php All sources to build your own copy of the robot at: github.com/LionelBirglen/OpenSourcePlanarCableRobot
[Francais] Mécatronique : magnétomètre en source libre
zhlédnutí 164Před rokem
Tous les fichiers disponibles à : github.com/LionelBirglen/Magnetometer
Demo of a Spherical Compliant Fixture
zhlédnutí 88Před rokem
Original design by Jelle Rommers, Volkert van der Wijk, and Just Herder, see: Rommers, Jelle, Volkert van der Wijk, and Just L. Herder. "A new type of spherical flexure joint based on tetrahedron elements." Precision Engineering 71 (2021): 130-140. www.sciencedirect.com/science/article/pii/S0141635921000726 Model from Thingiverse: www.thingiverse.com/thing:4808398 www.thingiverse.com/thing:4841850
Modeling and Analysis of Soft Robotic Fingers using the Fin Ray Effect
zhlédnutí 2,8KPřed 4 lety
This is the video attachment of the paper "Modeling and Analysis of Soft Robotic Fingers using the Fin Ray Effect" by Xiaowei Shan and Lionel Birglen, International Journal of Robotics Research, 2020, DOI: 10.1177/0278364920913926 journals.sagepub.com/doi/full/10.1177/0278364920913926 This work discusses a detailed mathematical modelling of parallel grippers equipped with soft fingers taking ad...
Mechatronics: Repairing a Defective Optical Encoder
zhlédnutí 3,5KPřed 4 lety
This video shows the inspection and repair of a defective optical encoder, in this case an Enc22 from Maxon. Encoder Circuit Reference: HEDS-9700E50 Technical Specifications: docs.broadcom.com/docs/AV02-0511EN Digikey Link: www.digikey.ca/product-detail/en/broadcom-limited/HEDS-9700-E50/516-3520-ND/2219906
[Francais] Mécatronique : réparation d'un encodeur optique
zhlédnutí 1,9KPřed 4 lety
Cette vidéo montre comment inspecter et réparer un encodeur optique défectueux, dans notre cas un Enc22 de la compagnie Maxon. Référence du circuit de l'encodeur : HEDS-9700E50 Spécifications techniques : docs.broadcom.com/docs/AV02-0511EN Lien Digikey : www.digikey.ca/product-detail/en/broadcom-limited/HEDS-9700-E50/516-3520-ND/2219906
Mechatronics: Filtering a Noisy Encoder Channel
zhlédnutí 4,3KPřed 4 lety
What to do when the signal from your motor's encoder is noisy and corrupts the rotation measurements? In this video we show a simple fix and demonstrate its effectiveness with experiments. A big thank you to the guys at Basic Micro forums for their help: forums.basicmicro.com/
MEC8352 : Mécatronique I - Présentation des robots BEAM Hiver2019
zhlédnutí 434Před 5 lety
MEC8352 : Mécatronique I - Présentation des robots BEAM Hiver2019 Ces robots BEAM (acronyme anglais de Biology-Electronics-Aesthetics-Mechanics) inspirés du fonctionnement des neurones et du comportement des insectes utilisent l'énergie solaire et sont fabriqués avec des pièces de récupération. Chaque étudiant(e) du cours Mécatronique I en fabrique un pendant sa session. Le circuit choisi, la f...
[Francais] Il était une fois les projets intégrateurs de 4e année en mécatronique...
zhlédnutí 175Před 5 lety
Attention la tête ! Toute ressemblance avec des événements présents, passés, ou futurs est faite parfaitement exprès. Source : Il était une fois la révolution de Sergio Leone (1971), un excellent film à voir et revoir !
[Francais] Mécatronique : filtrage du signal de sortie d'un encodeur
zhlédnutí 398Před 5 lety
Que faire si le signal fourni par l'encodeur de votre moteur est de mauvaise qualité et rend la mesure de la rotation de ce moteur aléatoire ? Dans cette première vidéo sur la mécatronique nous allons voir une solution simple à ce problème et démontrer son efficacité expérimentalement. Un grand merci aux forums BasicMicro pour leur aide dans la détection du problème : forums.basicmicro.com/
NIST Webinar (archive): Replicating and Experimenting with NIST Grasping Performance Test Bench
zhlédnutí 182Před 5 lety
This is the recording of a webinar we gave organized conjointly between the National Institute of Standards and Technology (NIST) and the IEEE Technical Committee on Robotic Hand Grasping and Manipulation. Presentation by Prof. Lionel Birglen and Dr. Xiaowei Shan, Polytechnique Montreal. 8 November 2018. Download the presentation at: goo.gl/xeckLy *Note:Sorry for the poor audio and video qualit...
Full Rotation Static Balancer Using Differential Noncircular Pulleys
zhlédnutí 16KPřed 5 lety
Full Rotation Static Balancer Using Differential Noncircular Pulleys
Trajectory Guiding of a Suspended Cable Robot
zhlédnutí 5KPřed 5 lety
Trajectory Guiding of a Suspended Cable Robot
Projet Intégrateur IV en mécatronique H2018 : Robot CRISP
zhlédnutí 436Před 6 lety
Projet Intégrateur IV en mécatronique H2018 : Robot CRISP
Suspended Cable Robot Preview/Blooper!
zhlédnutí 288Před 6 lety
Suspended Cable Robot Preview/Blooper!
MEC8352 : Mécatronique I - Présentation des robots BEAM Hiver2018
zhlédnutí 501Před 6 lety
MEC8352 : Mécatronique I - Présentation des robots BEAM Hiver2018
Simulations of Geometries of Self-Adaptive Robotic Legs Optimized to Overcome Obstacles
zhlédnutí 781Před 6 lety
Simulations of Geometries of Self-Adaptive Robotic Legs Optimized to Overcome Obstacles
Stiffness Analysis of Underactuated Fingers and its Application to Proprioceptive Tactile Sensing
zhlédnutí 369Před 6 lety
Stiffness Analysis of Underactuated Fingers and its Application to Proprioceptive Tactile Sensing
Test Bench for Robotic Hands: Slip Resistance and Grasp Strength of the PaCoMe Fingers
zhlédnutí 286Před 6 lety
Test Bench for Robotic Hands: Slip Resistance and Grasp Strength of the PaCoMe Fingers
A Self-Adaptive Hand for the Baxter Robot
zhlédnutí 684Před 7 lety
A Self-Adaptive Hand for the Baxter Robot
Bin Packing with Self-Adaptive Robotic Fingers and Rethink's Baxter Robot
zhlédnutí 983Před 7 lety
Bin Packing with Self-Adaptive Robotic Fingers and Rethink's Baxter Robot
Simulation of a Robot with Self-Adaptive Two Degree-of-Freedom Legs Traversing Terrains
zhlédnutí 430Před 7 lety
Simulation of a Robot with Self-Adaptive Two Degree-of-Freedom Legs Traversing Terrains
Trajectory for Automatic Fiber Placement Simulation on Y-shape Parts using a Fanuc M20i Robot
zhlédnutí 394Před 7 lety
Trajectory for Automatic Fiber Placement Simulation on Y-shape Parts using a Fanuc M20i Robot
Simulations of Automated Fibre Placement on Multi-Axial Revolution Surfaces
zhlédnutí 519Před 7 lety
Simulations of Automated Fibre Placement on Multi-Axial Revolution Surfaces
Self-Adaptive Robotic Leg Overcoming Obstacles (prototype only)
zhlédnutí 12KPřed 7 lety
Self-Adaptive Robotic Leg Overcoming Obstacles (prototype only)
Self-Adaptive Robotic Leg Overcoming Obstacles (with explanations)
zhlédnutí 1,8KPřed 7 lety
Self-Adaptive Robotic Leg Overcoming Obstacles (with explanations)
Impressive!
Me gusta mucho, ese helado.
Very cool
Nice work! I thought about using shaped/cammed pulleys like this to make positioning more precise along entire workspace. So kind of like this idea only the pulleys have brushless servo motors.
Amazing! ❤
do any of the objects you show need the compliant zone? they all seem to be picked quite well with the stiff upper zone
That's a very interesting question! Indeed, most of these objects could be seized with a pinch grasp, namely the distal phalanges. However, the resistance to slipping out is then weak unless the contact forces become huge since you only rely on local friction coefficients which also depends on the object and may vary a lot. Power grasps (compliant) on the other hand are generally better: they spread out the contact forces on a wider surface (thus less chances of damaging fragile objects) and are less prone to slippage. This is the same as with our own hands: for larger objects and a strong grasp we tend to grab with as many fingers and as many phalanges as we can. Pinching is an option when you have small objects (think of a needle) and enveloping is not practical but it is more difficult to maintain a secure grip.
Can you provide gripper 2d draft, I want to make an similler 3d model by 3d printing, need measurements for 3d model.
O
Beau travail, bravo Xiaowei !
Why are the springs getting so extended? Shouldn't your control algorithm be able to adjust for that?
Hi there, sorry for the late reply. The reason why the springs at the top are extending a lot is because: 1. they have a relatively low stiffness but most importantly 2. to produce the small tension required to keep the bottom cables reasonably taut a huge force is necessary in the upper cables. If you look at the projection of the top cables direction along the vertical axis, you get a very small vector component. Thus, to create a small force in this vertical direction a huge magnitude is required and this magnitude reaches values close to the maximally allowable tension. This phenomenon actually defines the limit of workspace of the robot. See the associated paper for more details on the computation of the workspace and numerical values. It is important to understand that this is a physical aspect that is intrinsic to the geometry of the robot, no control algorithm would be able to alleviate this issue. at least in static conditions. If the controller decreases the tension in the upper cables, either the lower cables will become slack or the moving platform will drop.
Excellent demonstration, and great mechanism!
Merci Dmitri!
nice ... job sir FC from thailand
cool!
Am I going crazy or is this an application of a Chinese windlass?
You are not far off... the main difference with the Chinese windlass is that our pulleys (drums in the windlass) are not round but have precisely calculated profiles to transform the linear force from the springs into a torque at the lever arm that balances the payload. But the arrangement with two drums/pulleys connected by a cable is indeed common to our mechanism and the Chinese windlass (and Weston's differential too)
BRAVOOOOOO 👏👏👏👏
Hello sir, what Make and model of actuator u have used in this concept
That's a Schunk KGG 100-80
I'm sorry, but I doubt that this huge noisy spikes related with encoder. Note how cap. changed encoder signal and not changed noise. Consequently, nature of this noise is external, not related to encoder. To me, that looks like either emi, floating/broken oscillosope ground, or you got current loop with stepper PWM, or maybe its a power source problem. Anyway, here huge problem. Fixing this problem with cap. pointless (as we literally see it with our own eyes).
Hi Alex, We agree (mostly): we never said the encoder was defective. The source of the noise is indeed clearly not the encoder itself but the lines. They are long and unshielded which is bad (EMI). Another issue with the lines is that there are wires for motor power (PWM) alongside wires for the encoder. Again, this is not good practice. We built this setup with what we had at hand and very little budget. This is not an issue with grounding (aside the grounding of a potential shield) as we confirmed the noise with both the scope you see in the video and the tuning software of the motor drive. It is also not a power issue, the DC power supply we have is quite good and we have a huge capacitor on it (as per manufacturer recommendation). Where I disagree is that putting the capacitor on the line is pointless. It is not since it fixed our issue... It did not eliminate the spikes but reduced their amplitudes to a point that was good enough for the drive to work properly. Cheers.
@@PolyLabrobot The issue is not resolved. A lot of noise is clearly still on the line as shown on the scope and you've only just about managed to keep the noise within the thresholds. In industry, the cable is shielded and they use differential signalling. This capacitor 'fix' is a bodge - change the parameters of the system and the 'fix' completely stops working.
@@Shocker99 The issue *is* resolved since the motor is working correctly now. You can never completely and perfectly remove noise from any real signal. Filtering only allows you to reduce the magnitudes of unwanted harmonics and as you said keep it within thresholds.That is the point. We agree that using shielded cables and differential signals would be a great solution but in this case we are aiming at a quick and easy fix at the lowest possible cost, not industry standard compliance. This is prototyping, not production. Cheers!
Thank you so much Sir
Kreatìv ès nagyon fontos fejlesztès
the compliant flexure gripper definitely wins over this multi-part mechanical design
Very often yes and I do love compliant mechanisms a lot! However, there are situations where you do need a rigid link gripper: e.g. in some industries the tools are getting seriously abused and/or work in harsh (corrosive) environments and in that case, steel or stainless steel with lots of material is a must. Cheers!
You should make this mechanism non planar it's important since the terrain is never 2D
Would be great if you could adjust the compesation torque on the fly e.g. dynamic loading.
It's possible quite easily by moving the attachment point of the spring (lower right) with an actuated slider or arm. That's beyond the simple mechanism we intended to demonstrate here though.
Why not just use 2 winches and get full X/Y control seen from the side? Or, naturally 3 winches and a fully x,y,z control within a practical area.
Well the "truest" answer is we did it this way because we found it fun and interesting! In the lab we explore how to do complex stuff with the minimal number of actuators and relying as much as possible on mechanical intelligence rather than electronics. See our other works about adaptive gripper design for example. Now in this particular example, if you have numerous winches you need to control them synchronously to get the right trajectory. It's not very difficult but still, more work than for us: this particular mechanism does not rely on controllers or sensors at all. There is just a simple DC motor to which we bring a voltage, no feedback or pulse sequencing is required. By design the robot *cannot* deviate from the trajectory so there is by definition zero position error. Cheers!
Industry generally wants products to be as cheap as possible. Why spend money on two axes when only one will do? Furthermore, it's an additional axis will require more maintenance and there are more things to go wrong. If a product is only doing the same operation then why build in flexibility that will never be used? There are many machines in manufacturing that use a similar motion that repeat 100+ times a minute and they will do that exact same motion for the entirety of the machine's life. I like this different take to perform this motion with only a single motor. Normally, i see it with a cam and a 4-bar linkage.
@@Shocker99 I only meant that he should mount the meter in different orientations on his shaker to test if it is more susceptible to vibrations in some axis than others.
Lovely video. Good presentation. Thankyou.
Thank you!
Hey Lionel. Have you seen the underactuated 5 bar linkage gripper (2F-85) sold by Robotiq? What are some of the trade-offs between the 2 different designs?
I do know this product very well as I am the original inventor of its kinematic structure. If you're curious enough, you can find my name in the "patents" section of the 2F-85 and 2F-140 user manual. Robotiq licensed my patent on this kinematics. The Pacome fingers are an evolution and improvement of this previous patent. These fingers are entirely passive whereas the 2F-XX grippers need an actuator to rotate their lower link and close. The Pacome fingers can be attached to pretty much any gripper you have (hydraulic, pneumatic, electric, whatever) and they use the motion of this gripper as the actuator. They are simpler (=cheaper) and more versatile. There are also some more subtle advantages with the Pacome fingers but it would get quite long and technical to explain that here. Cheers!
@@PolyLabrobot are you selling this one or licensing the patent to a manufacturer? I'm looking for a good robot end effector for a unique application
@@imeautomation Yes and yes. Reach out to me at lionel.birglen -at- polymtl.ca and I'll give you more info.
it is great content! what kind of FEA software do you use?
The simulations starting @3:09 were made using Ansys. See www.ansys.com/products/structures/ansys-mechanical
@@PolyLabrobot ah thank you, the simulated 3D structure is really impressive anyway!
Thanks ! great video. very clear explanation.
Thank you!
NAGYSZERŰ!
bueno genial
That's amazing!
Be careful when You using only a capacitor, because you drastically increase the current peaks when states changing (you can damage the encoder), I think that best method is to use a RC low-pass filter.
That's a very good point and you are absolutely right. At the rising and falling edges of the signal, that capacitor is essentially shorting the input pin and that could create current surges. I believe it still works out here because I have a very large line resistance due to long wires and multiple connectors along the path which all act as the R of the RC filter you rightfully suggest. What leads me to believe this is that I actually measured approx 2.7V for the square wave at the motor driver input instead of the 5V supply of the encoder. That tells me I actually have a voltage divider where the line resistance (+output impedance of the encoder) is of similar magnitude than the input impedance of the motor driver.
how to contact you guys i need support
.stl files or it didn't happen
Very nice!
very interesting but I don't understand it
Thanks! Having a look at the original paper might help you: asmedigitalcollection.asme.org/mechanismsrobotics/article-abstract/10/6/061001/367087/Differential-Noncircular-Pulleys-for-Cable-Robots If you don't have access to the ASME repository, an open source preprint of that work is available at: publications.polymtl.ca/3544/
Thanks
@@va7795 I haven't read the paper but my intuition is that the shape of the cam stretches the springs to match the gravitational force exerted by the mass, so that the two forces balances out at all angles. Ie. The mass exerts 10N of force downwards, and so the cam stretches the spring so that it also exerts 10N of force but in the opposite direction, therefore the mass doesn't move because the forces are equal. The cam is designed so that the force produced by the springs always matches the force exerted by the mass. The mass will always rise if it smaller than what the cam is designed for and it will always fall when the mass is greater.
Dear CZcamsr, could you kindly share the GitHub or procedure to do this? It is using ROS to run it autonomously?
Hi! Sorry but I do not think we have the program we used to record this demo anymore. What I can tell you is that it was a simple playback of a sequence of prerecorded waypoints. It was indeed run from ROS but the robot is not detecting the objects by itself. The objective of our video was to demonstrate the fingers we designed rather than the robot capabilities to detect objects and compute grasp poses.
Thats perfect
Impressive.
Nice concept, I really like it. Could be really awesome for industrial use if printed as a compliant design out of a springy titanium alloy. I think I'll try to design a nylon version for my FDM printer ^^
Hi Tim. We actually have already built several compliant versions of this design and indeed it works out very well. We did not put anything online yet as we are trying to publish a scientific paper about that first. Hopefully, we could let out more info this year or the next. Good luck with your copy of the design!
I wonder if can be used to draw other shape by using the same pulley? Or need to change pulley design?
Indeed, that is the main limitation of our robot: you cannot change the trajectory of the robot with this design. It is essentially a tradeoff: you only need a single motor and the control is utterly simple (just rotate the axis, the trajectory is mechanically programmed in the shape of the pulleys) but deviating from that trajectory is impossible without updating the mechanism, e.g. changing the pulleys, as you rightfully noticed. Cheers!
PolyLabrobot thank you for the response.. What program do you use for computer simulation?
Matlab.
To the people asking us to share the CAD files of the fingers: thank you for your interest but we cannot do that at this point since we are still actively doing research with them. At one point in the future, we may release STL files and this will be announced here but not right now. Thank you for your understanding.
Please share the cad model of this gripper plsss
great !
Good idea sir how can I get the Cad model of this Gripper ?
Que incrível!!!!!!!